- Resume Builder
- Resume Templates
- Resume Formats
- Resume Examples
- Cover Letter Builder
- Cover Letter Templates
- Cover Letter Formats
- Cover Letter Examples
- Career Advice
- Interview Questions
- Resume Skills
- Resume Objectives
- Job Description
- Job Responsibilities
- FAQ’s

Supplier Quality Engineer Resume Examples
If you are looking for a job as a supplier quality engineer, having a well-structured and organized resume is essential. A good resume is the first step in getting noticed by prospective employers. Writing a resume for a Supplier Quality Engineer position requires you to show your technical knowledge and skills, as well as your experience working in the quality assurance field. To help you create an effective resume, this guide will provide helpful tips and an example of a resume for a Supplier Quality Engineer.
If you didn’t find what you were looking for, be sure to check out our complete library of resume examples .
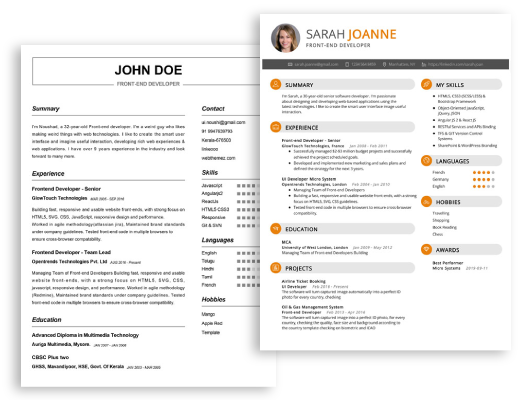
Start building your dream career today!
Create your professional resume in just 5 minutes with our easy-to-use resume builder!
Supplier Quality Engineer
123 Main Street | Anytown, USA 99999 | Phone: (123) 456-7890 | Email: [email protected]
I am a highly- skilled Supplier Quality Engineer with extensive experience in developing, executing and monitoring supplier quality management programs. I have a passion for problem solving and have successfully implemented processes to improve product quality, reduce costs and ensure timely delivery. My core skills include root cause analysis, process and product validation, auditing, and supplier development. I am also experienced in identifying and resolving supplier issues and managing supplier relationships to maintain high standards.
Core Skills :
- Quality Engineering
- Supplier Quality Management
- Root Cause Analysis
- Process & Product Validation
- Supplier Development
- Problem- Solving
- Collaboration
Professional Experience :
- Supplier Quality Engineer at ABC Company – 2016 to Present
- Developed, implemented and monitored effective supplier quality management programs.
- Performed root cause analysis and implemented process improvements to reduce product nonconformances.
- Conducted audits, identified and resolved supplier issues, and maintained supplier relationships.
- Improved product quality and reduced costs through process validation and supplier development.
Education :
- Bachelor of Science in Engineering, ABC College, 2016
Create My Resume
Build a professional resume in just minutes for free.
Supplier Quality Engineer Resume with No Experience
Recent graduate with a degree in Industrial Engineering and a specialization in Quality Control. Highly motivated and eager to learn about Supplier Quality Engineering and develop professional skills. Possesses analytical and problem- solving skills as well as strong communication and interpersonal abilities.
- Excellent written and verbal communication
- Analytical and problem- solving skills
- Excellent organizational and time management skills
- Ability to work independently and within a team
- Strong understanding of quality engineering principles
- Proficient in the use of MS office applications
Responsibilities
- Monitoring the performance of suppliers and their products
- Analyzing supplier quality data to identify trends and areas of improvement
- Developing and executing supplier quality plans
- Performing regular quality audits of supplier processes and products
- Ensuring compliance with quality standards and regulations
- Identifying and resolving supplier quality issues
- Working with suppliers to develop effective corrective action plans
- Collaborating with other departments to ensure customer satisfaction
Experience 0 Years
Level Junior
Education Bachelor’s
Supplier Quality Engineer Resume with 2 Years of Experience
Dedicated and diligent Supplier Quality Engineer with 2 years of experience in the quality assurance field. Proven experience in developing, monitoring, and improving supplier quality standards and procedures. Skilled in managing supplier relationships through quality inspection, auditing, and cost reduction. Adept at maintaining the highest quality standards while identifying opportunities for cost savings and process enhancement.
- Supplier Quality Assurance
- Quality Management Systems
- Quality Auditing
- Defect Reduction
- Continuous Improvement
- Metrics and Reporting
Responsibilities :
- Developed, monitored, and updated supplier quality processes and procedures.
- Planned, organized, and conducted quality audits at the supplier’s facilities and assessed supplier performance.
- Created, implemented, and maintained supplier quality management systems.
- Performed root cause analysis and identified areas for quality improvement.
- Analyzed supplier performance data, identified problem areas and areas for improvement, and developed corrective action plans.
- Performed supplier corrective action management to address quality issues.
- Provided technical support for supplier quality and dispute resolution.
- Conducted supplier reviews and supplier selection processes.
- Identified opportunities for cost savings and process enhancement.
- Ensured compliance to internal and external quality standards.
Experience 2+ Years
Supplier Quality Engineer Resume with 5 Years of Experience
Highly experienced Supplier Quality Engineer with over 5 years in the industry and a track record of successful production of high- quality and reliable products that meet industry standards. Possesses excellent problem solving and critical thinking skills, with an ability to identify issues and create effective corrective action plans. Experienced in quality control, customer and supplier relations, manufacturing process knowledge and cost analysis. Committed to providing a safe and efficient work environment and developing quality control processes that ensure the customer’s satisfaction.
- Quality Control
- Data Analysis
- Project Management
- Quality Assurance
- Problem Solving
- Cost Reduction
- Critical Thinking
- Strong Communication Skills
- Manufacturing Knowledge
- Process Improvement
- Customer Relations
- Supplier Relations
- Safety Management
- Lead and maintain supplier quality programs, policies and procedures
- Conduct supplier performance reviews and audits to assess supplier capabilities
- Develop, review and update quality assurance plans and procedures
- Monitor and control inventory levels to ensure customer satisfaction
- Troubleshoot and investigate supplier related issues and implement corrective actions
- Facilitate and document supplier corrective action process to ensure proper resolution
- Negotiate and influence supplier performance and compliance to quality assurance standards
- Monitor and analyze supplier performance metrics such as quality, delivery, and cost
- Lead new process implementation and ensure suppliers are compliant with new requirements
- Monitor and ensure compliance of regulatory safety standards and practices
- Collaborate with customers and suppliers to ensure customer requirements are met on time
- Establish and maintain good supplier relationships to ensure customer satisfaction and quality standards
Experience 5+ Years
Level Senior
Supplier Quality Engineer Resume with 7 Years of Experience
Highly experienced Supplier Quality Engineer with 7 years of experience in conducting in- process, final, and incoming inspections. Adept in developing, implementing and management of quality systems and processes to ensure supplier products and services meet customer needs. Exceptional problem solving and quality control skills with the ability to provide process and product improvement and guidance to suppliers.
- Quality management systems
- Quality assurance and control
- Auditing and inspection
- Corrective and preventative measures
- Process/product improvement
- Statistical process control
- Non- conformance analysis
- Troubleshooting and problem solving
- Supplier management
- Customer relations
- Performed in- process, final and incoming inspections to ensure manufacturing processes were in compliance with customer needs.
- Developed, implemented and managed quality systems and processes to ensure supplier products and services met customer requirements.
- Conducted root cause analysis and implemented corrective and preventative measures to reduce non- conformance costs.
- Monitored, evaluated and reported on supplier performance, product quality and conformance to customer requirements.
- Used, Statistical Process Control (SPC) to analyze data and identify process improvements.
- Coordinated and managed supplier visits, audits and customer relations.
- Assisted with the development of customer- specific audit plans.
- Conducted supplier reviews and worked collaboratively with the purchasing team to develop strategies for improving supplier quality.
- Ensured timely resolution of all quality related issues.
Experience 7+ Years
Supplier Quality Engineer Resume with 10 Years of Experience
Experienced Supplier Quality Engineer with 10 years of experience in the automotive industry. Possess a strong understanding of the quality assurance process and have a demonstrated track record of success in managing supplier quality and cost reduction. Have a proven ability to develop and manage key supplier relationships, ensure compliance with corporate standards, and reduce supplier- related quality issues. Possess excellent problem- solving and communication skills, as well as strong organizational and analytical skills.
- Supplier Quality Audits
- Cost Reduction Strategies
- Supplier Relationship Management
- Quality System Audits
- Statistical Process Control
- Establish and maintain strong relationships with key suppliers to ensure quality standards are met and delivery requirements are adhered to
- Conduct supplier quality audits in order to monitor quality performance of suppliers and identify areas for improvement
- Develop, implement, and manage effective cost reduction strategies to reduce supplier- related costs
- Develop and maintain quality systems for suppliers to ensure compliance with corporate quality standards
- Analyze data to identify trends and recommend process improvements to reduce supplier- related quality issues
- Assist in the development and implementation of quality plans and instructions for supplier operations
- Monitor production procedures and processes to ensure quality standards are met
- Train and mentor other team members in the development and implementation of quality control and assurance processes
Experience 10+ Years
Level Senior Manager
Education Master’s
Supplier Quality Engineer Resume with 15 Years of Experience
An experienced Supplier Quality Engineer with 15 years of experience in developing and implementing strategies and procedures to ensure that suppliers comply with product specifications and customer requirements. Highly organized and detail- oriented with strong project management, communication, and problem- solving capabilities. Experienced in dealing with vendors, customer service, and customer complaints. Skilled at developing innovative solutions to quality assurance issues and adept at identifying process improvements for maximum performance.
- Vendor Management
- Customer Service
- Regulatory Compliance
- Documentation
- Developed and maintained quality assurance policies and procedures to ensure product specifications and customer requirements are met
- Ensured compliance with all applicable industry regulatory standards
- Collaborated with vendors and suppliers to ensure quality of materials and products
- Negotiated with suppliers to secure the best terms, pricing, and production schedules
- Developed innovative solutions to improve quality assurance processes
- Monitored and reviewed supplier performance to ensure compliance with quality standards
- Investigated customer complaints in order to identify and resolve issues quickly and efficiently
- Prepared accurate and comprehensive quality documentation and reports
Experience 15+ Years
Level Director
In addition to this, be sure to check out our resume templates , resume formats , cover letter examples , job description , and career advice pages for more helpful tips and advice.
What should be included in a Supplier Quality Engineer resume?
A Supplier Quality Engineer resume should highlight key qualifications, such as knowledge of regulatory requirements and quality assurance processes. It should also showcase an individual’s ability to work effectively with suppliers and lead teams in the implementation of quality programs.
Below are some of the key elements that should be included in a Supplier Quality Engineer resume:
- Knowledge and understanding of quality assurance practices and processes, such as Lean Six Sigma, 8D, DOE and FMEA
- Ability to read and interpret engineering drawings, blueprints, and schematics
- Experience with manufacturing process and procedures, including CNC, injection molding, and machining
- Familiarity with various quality audit and inspection techniques, such as ISO 9001 and ASQ/ANSI
- Proficiency with Quality Management Software, such as ProModel, CAPA, and Quality Scorecard
- Excellent communication, problem-solving, and organizational skills
- Ability to lead and motivate teams to effectively implement quality programs
- Bilingual ability in Spanish and English, a plus
- Bachelor’s degree in Mechanical Engineering or related field
What is a good summary for a Supplier Quality Engineer resume?
A successful Supplier Quality Engineer resume should showcase a candidate’s expertise in product quality assurance and regulatory compliance. The resume should emphasize the candidate’s experience working with suppliers to develop and implement quality plans, evaluate supplier performance, and ensure vendor compliance with regulatory standards and industry guidelines. The resume should also demonstrate the candidate’s ability to develop and execute inspection plans, analyze product data, and communicate complex technical information in a clear and concise manner. Additionally, the candidate should highlight any certifications or training relevant to their position, as well as their overall knowledge of industry best practices.
What is a good objective for a Supplier Quality Engineer resume?
A Supplier Quality Engineer plays an important role in ensuring that goods purchased from suppliers meet the quality expectations of the company. Therefore, when writing a resume for this position, it is essential to include an objective that clearly outlines the qualifications and experience that make you the ideal candidate for the job. Here are some good objectives for a Supplier Quality Engineer resume:
- To use my expertise in Quality Assurance and Process Improvement to develop effective supplier quality systems that meet the needs of the organization.
- To leverage my experience in Lean Six Sigma, Statistical Process Control and Design of Experiments to optimize supplier quality performance.
- To utilize my knowledge of international standards (ISO 9001, IATF 16949, etc.) to develop and implement effective quality management systems.
- To apply my technical writing and communication skills to ensure clear and timely communication with suppliers and other stakeholders.
-To employ my training and development skills to enhance supplier capability and performance.
- To use my analytical and problem-solving skills to identify, investigate and resolve supplier quality issues.
How do you list Supplier Quality Engineer skills on a resume?
When crafting a Supplier Quality Engineer resume, it is important to highlight the key skills and experience that make you a viable candidate. The Supplier Quality Engineer role requires extensive knowledge of quality engineering principles and practices, as well as experience in areas such as problem solving, supplier management, and supplier relations. Here is a guide to help you list these skills on your resume:
- Quality Engineering: Demonstrate knowledge of quality engineering principles, including problem solving, process improvement, Continuous Improvement, and root cause analysis.
- Supplier Management: Show experience in assessing suppliers, selecting and evaluating vendors, and developing supplier relationships.
- Risk Management: Detail proficiency in identifying and mitigating risks related to suppliers and their processes.
- Quality Assurance: Illustrate expertise in quality assurance processes and techniques, such as Design of Experiments (DoE), Six Sigma, and Lean.
- Documentation: Prove capability in creating and maintaining comprehensive quality plans, procedures, and reports.
- Regulatory Compliance: Highlight experience with FDA and ISO requirements, audits, and certification procedures.
- Collaboration: Show ability to effectively collaborate with cross-functional teams, as well as external suppliers.
By listing these Supplier Quality Engineer skills on your resume, you can demonstrate to employers that you possess the right qualifications and experience to excel in the role.
What skills should I put on my resume for Supplier Quality Engineer?
If you are looking to apply for the position of a Supplier Quality Engineer, having the right skills on your resume is essential for success. Employers will be looking for applicants who can demonstrate the right knowledge, experience and abilities to excel in this role. Here are a few skills to consider including on your resume when applying for a Supplier Quality Engineer position:
- Quality Assurance/Control: A Supplier Quality Engineer must have a thorough understanding of and experience in quality assurance processes and methods. This includes having knowledge of industry specific quality control systems and standards.
- Communication: A Supplier Quality Engineer must be able to effectively communicate with both internal and external stakeholders. This includes being able to provide clear and concise communication, both verbally and in writing.
- Problem-Solving: A Supplier Quality Engineer should have a natural problem-solving ability and the right problem-solving techniques to identify, troubleshoot and resolve potential quality issues.
- Analytical Skills: A Supplier Quality Engineer should have strong analytical skills to analyze data, draw conclusions, and make recommendations based on their findings. This includes being proficient in using statistical tools, such as Minitab and SPC.
- Organizational Skills: Supplier Quality Engineers must possess strong organizational skills to manage multiple projects and prioritize tasks. This includes having the ability to plan and coordinate activities to meet deadlines and objectives.
- Technical Knowledge: A Supplier Quality Engineer should have a good understanding of technical concepts and processes, as well as experience with quality assurance software applications.
By including these skills on your resume, you can demonstrate to employers that you have the right knowledge, experience and abilities to excel in the role of Supplier Quality Engineer.
Key takeaways for an Supplier Quality Engineer resume
Supplier Quality Engineers are responsible for ensuring the safety and quality of products that are produced by suppliers. A strong Supplier Quality Engineer resume will demonstrate your ability to inspect and analyze supplier processes, develop supplier quality metrics, and maintain relationships with suppliers.
When writing your Supplier Quality Engineer resume, there are several key takeaways that should be included. Below are a few key takeaways for a Supplier Quality Engineer resume:
• Demonstrate your attention to detail: Highlight your experience in inspecting and analyzing supplier processes, and include any certifications or additional training that you have completed.
• Showcase your problem-solving skills: Emphasize your ability to identify and resolve supplier-related problems.
• Focus on communication and collaboration: Showcase your ability to develop strong relationships with suppliers and maintain open communication.
• Highlight your technical abilities: Include any technical abilities, such as software proficiency or knowledge of engineering principles, that you may have.
These key takeaways will help you create an effective Supplier Quality Engineer resume that showcases your skills and experience. With a well-crafted resume, you will be well-positioned to land an exciting career in supplier quality engineering.
Let us help you build your Resume!
Make your resume more organized and attractive with our Resume Builder
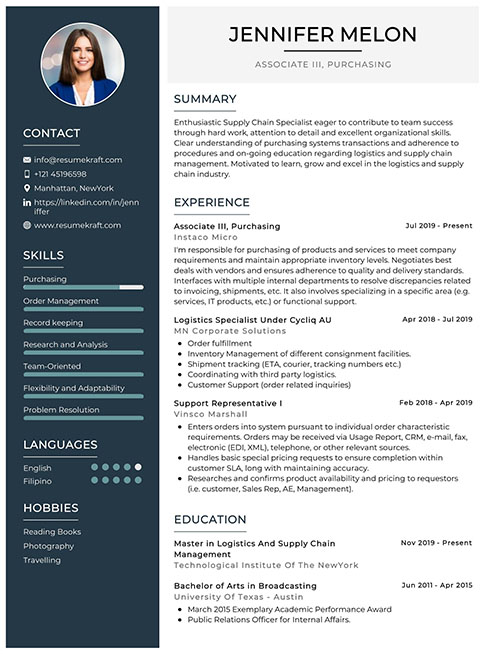
12 Supplier Quality Engineer Resume Examples for 2024
Creating a resume for a supplier quality engineering position must reflect your ability to oversee product and supplier standards. In this guide, we present examples that show effective communication of your skills and experience. We focus on structuring your qualifications to highlight knowledge in process improvement and compliance within the supply chain, ensuring you convey essential capabilities like vendor management, risk assessment, and quality control. This strategic advice refines your resume to showcase your industry expertise to potential employers.

- 02 Nov 2024 - 1 new section (Show leadership and growth) added
- 05 Oct 2024 - 1 new resume template (Supplier Quality Engineer with Renewable Energy Expertise) added
- 25 Aug 2024 - 1 new section (Showcase leadership and growth) added
Next update scheduled for 01 Dec 2024
Here's what we see in standout supplier quality engineer resumes.
Show Impact With Numbers : The best resumes show clear impacts with specific metrics like cost reduction by 15% , process efficiency up 25% , supplier defect rates down 10% , and on-time delivery improved to 95% .
Include Relevant Skills : Include skills on your resume that you have and are in the job description. Some key ones are lean manufacturing , Six Sigma certification , ISO 9001 knowledge , statistical process control , and supplier audit proficiency .
Stay Current With Industry Trends : It's good to show that you're up-to-date with industry standards by mentioning familiar with AIQM and versed in risk management . These indicate you're ready for today's challenges.
use this maybe to have a resume upload button widget 1: yellow Here's a short quick tip / warning for people to include. If your symptoms get worse or do not improve after 1 day, go to a lower altitude if you can. Try to go around 300 to 1,000 metres lower.
widget 2: red / but not serious Here's a short quick tip / warning for people to include. If your symptoms get worse or do not improve after 1 day, go to a lower altitude if you can. Try to go around 300 to 1,000 metres lower.
helpful blue / but not serious Here's a short quick tip / warning for people to include. Here's a short quick tip / warning for people to include. Here's a short quick tip / warning for people to include. Here's a short quick tip / warning for people to include. Here's a short quick tip / warning for people to include. Here's a short quick tip / warning for people to include. Here's a short quick tip / warning for people to include.
Supplier Quality Engineer Resume Sample
Find out how good your resume is.
ummm here it is
Get feedback on your resume
Want to know how your supplier quality engineer resume measures up? Our resume scoring tool gives you instant feedback on your application. It evaluates key criteria that recruiters in quality assurance look for, helping you understand your resume's strengths and areas for improvement.
Upload your resume now for an unbiased assessment. You'll get a clear score and practical tips to make your application stand out in the competitive field of supplier quality engineering.
Detailing relevant coursework
In the education section, list the most pertinent courses you've completed. When you've studied topics like statistical process control or quality systems management, make this clear; these are key areas in supplier quality engineering roles. As you are aiming to provide assurance and continuous improvement in supplier's quality, such studies show direct relevance and should be featured prominently.
Even if your work experience is extensive, showcasing relevant courses can demonstrate a continued focus on critical industry-specific knowledge, complementing your practical experience.
Highlight relevant certifications
Show certifications specific to supplier quality assurance, like ASQ CQE or Six Sigma. This proves you are trained to understand supplier evaluation and can handle complex quality challenges.
Also, evidence of project management skills signals you can lead supplier development projects effectively, this being key in supplier quality engineering.
Lead Supplier Quality Engineer Resume Sample
Ideal resume length.
For a supplier quality engineer, you should aim for a one-page resume if you have less than ten years of related experience. This ensures that you showcase your most relevant skills and experience without overwhelming the reader. Use a layout that helps you make the best use of space. Your goal is to be concise while highlighting your ability to oversee supplier quality processes.
Senior professionals with extensive experience in ensuring product quality from suppliers might need two pages. Focus on streamlining your content to include critical jobs, achievements, and skills. Remember, whether your resume is one or two pages, hiring managers typically scan the first page quickly. Ensure your most impressive qualifications are prominent there. Large text or tiny margins are not suitable substitutes for clear prioritization. It's better to trim your content than to squeeze in too much information.
Supplier Quality Assurance Specialist Resume Sample
Emphasize continuous improvement.
Share examples where you used data to drive quality improvements or cost reductions. Your ability to improve supplier performance is vital.
Include any experience with international suppliers if you have it, as this role often involves global supply chains and shows you can handle diverse quality standards and cultural nuances.
Junior Supplier Quality Technician Resume Sample
Beat the resume bots.
When you apply for a job as a supplier quality engineer, your resume might first be read by resume screeners and Applicant Tracking Systems (ATS) before it reaches a human. To help you get past these, follow these tips:
- Use keywords from the job description. This could be phrases like 'supplier quality management' or 'supplier audit.' The ATS looks for these to decide if your resume is a match.
- Make sure your experience is easy to find. Use clear headings like 'work experience' and list your jobs in reverse chronological order. Focus on your achievements related to supplier quality, such as 'improved vendor defect rate by 20%'.
Keep your resume format simple. ATS can have a hard time reading fancy fonts or layouts. So, use a standard font and avoid images or graphics that can confuse the system.
Supplier Quality Engineer with Aerospace Specialization Resume Sample
Customize your resume wisely.
It's key to show you fit the job like a glove. Focus on the skills and experiences that matter most for a supplier quality engineer role. Make it easy for hiring managers to see your value in this field.
- Emphasize experience with quality management systems, such as ISO 9001 , and the ways you've improved supplier performance.
- For more senior roles, showcase your leadership in cross-functional teams and how you have led supplier audits.
- If you're moving into this field, highlight your background in process optimization or project management, drawing parallels to supplier quality assurance tasks.
Senior Supplier Quality Engineer in the Automotive Industry Resume Sample
Essential skills to include.
When crafting your resume for a supplier quality engineer role, focus on including relevant hard skills. These show your specific abilities and knowledge in the field.
- Quality assurance
- Supplier audits
- Statistical process control (SPC)
- Failure mode and effects analysis (FMEA)
- ISO 9001 standards
- Root cause analysis
- Lean manufacturing
- Data analysis
- Non-conformance reporting
These skills should be listed in a dedicated skills section or highlighted in your experience. This helps applicant tracking systems (ATS) pick them up. Focus on the skills that best match the job you are applying for. Tailoring your resume for each application can improve your chances.
Supplier Quality Control Manager Resume Sample
Show leadership and growth.
As a supplier quality engineer, showing that you've grown in your career is key. You want to make it clear you're ready for more responsibility. Here's how:
- Include any titles that show you've moved up, like 'senior' or 'lead'. If you've been a 'supplier quality engineer' and then became a 'senior supplier quality engineer', list both titles with the dates you held them.
- Detail any projects where you led a team. For example, 'Led a team of 5 in developing a new supplier evaluation process that reduced defects by 20%'.
Think about times you have taken the lead, even if you weren't in charge of people. Maybe you led a training or were the go-to person for a certain type of supplier issue. These are examples of leadership too.
- Use phrases like 'Championed a new inspection protocol' or 'Served as the lead for cross-functional supplier audits'.
- Talk about how you trained new staff or created guidelines that are now used company-wide. Phrases like 'Developed and implemented comprehensive quality control training for new hires' show that you have taken on extra roles that have helped others.
Principal Supplier Quality Engineer Resume Sample
Show impact with numbers.
As a supplier quality engineer, it's crucial you show the tangible impact you've made. Using metrics helps hiring managers see your value quickly. Here's how:
- Consider the percentage of defect rate reduction you achieved in your projects. If you're unsure, estimate based on the before and after quality audits.
- Highlight any cost savings you brought about by negotiating better material prices or streamlining supplier processes. Even rough estimates can be valuable.
Think about the times you improved workflow. Did you increase the efficiency of quality inspections ? Maybe you reduced the cycle time for product verification. Quantify these changes. Reflect on how many supplier audits you conducted and the compliance rate improvements that followed.
- Show the scale of your work by mentioning the number of suppliers you managed or the volume of parts you were responsible for. Talk in terms of supplier count or part quantities .
- Did your work lead to fewer customer complaints? Mention the decrease in customer issues to illustrate your impact on product quality.
Supplier Quality Engineer with Medical Devices Expertise Resume Sample
Showcase leadership and growth.
As a supplier quality engineer, your resume should reflect your ability to lead and your career progression. If you have been promoted or have taken on leadership roles, make sure to highlight these experiences. Employers value candidates who have shown they can take on more responsibility and successfully guide teams and projects.
- List any titles or roles that show you moved up, such as 'senior supplier quality engineer' or 'lead auditor for supplier assessment'.
- Include specific achievements that demonstrate leadership, such as 'Implemented a new inspection protocol that improved supplier defect detection by 20%' or 'Trained and supervised a team of 4 junior engineers in quality control procedures'.
Think about the times you led a project or were recognized for your work. Even if you have not had a formal title change, you can still show leadership. For example, you might have led a cross-functional team to resolve a critical supplier issue or been selected to represent your company at industry conferences. These experiences are valuable and should be included on your resume.
Supplier Quality Engineer with Renewable Energy Expertise Resume Sample
As a hiring manager, I know how important it is to see evidence of leadership and upward mobility in resumes. You should include clear examples if you have them.
- For supplier quality engineers, leadership might look like leading a cross-functional team to improve supplier performance or heading a successful project to streamline supplier assessment processes.
- If you have been promoted, make sure to highlight this. For example, if you started as a quality inspector and moved up to a supplier quality engineer, show the transition in your job titles and the dates you held each position.
Think about the times you have made decisions that affected the outcome of a project or led a team. Even if you're unsure how to label it as leadership, consider situations where you took charge or were recognized for your work.
- Did you train new team members or lead a workshop? Mention it.
- Perhaps you were chosen to represent your department in a supplier negotiation. That counts too.
- Biomedical Engineer Resume Examples
- Sales Engineer Resume Examples
- Electrical Power Engineer Resume Examples
- Production Engineer Resume Examples
- AWS Data Engineer Resume Examples
- Entry-Level DevOps Engineer Resume Examples
- Azure Cloud Engineer Resume Examples
- Structural Engineer Resume Examples
Quick links
Supplier quality engineer, resume sample #1, resume sample #2, resume sample #3, lead supplier quality engineer, resume sample #4, supplier quality assurance specialist, resume sample #5, junior supplier quality technician, resume sample #6, supplier quality engineer with aerospace specialization, resume sample #7, senior supplier quality engineer in the automotive industry, resume sample #8, supplier quality control manager, resume sample #9, principal supplier quality engineer, resume sample #10, supplier quality engineer with medical devices expertise, resume sample #11, supplier quality engineer with renewable energy expertise, resume sample #12, additional resources, questions get in touch.
- • Led cross-functional teams to address and resolve quality issues, improving overall supplier performance by 30%
- • Implemented Lean Manufacturing techniques across 10 supplier networks, reducing waste by 25% and boosting efficiency
- • Drove the improvement of supplier defect rate by 40% through effective quality system auditing and process control strategies
- • Facilitated the development and implementation of a continuous improvement program for suppliers, resulting in a 15% reduction in cycle times
- • Negotiated and integrated quality requirements into supplier contracts, ensuring compliance with Honeywell's stringent standards
- • Spearheaded a project to streamline supply chain processes using Six Sigma methodologies, achieving a $2M cost saving in the first year
- • Conducted thorough gap analysis on supplier quality management systems, identifying critical areas for improvement
- • Collaborated with suppliers to develop corrective action plans, enhancing product quality compliance by 35%
- • Authored and presented impactful quality metrics to senior management, guiding decision-making processes
- • Managed the qualification of new suppliers, ensuring a consistent supply chain for key aerospace components
- • Championed the adoption of error-proofing techniques within the supply base, leading to a reduction in manufacturing errors by 20%
- • Ensured adherence to company and regulatory quality standards, resulting in a 15% improvement in product reliability
- • Managed product inspections and audits, which led to a 10% decrease in customer-reported defects
- • Developed and enhanced QA processes and documentation, improving operational clarity and performance
- • Coordinated with production and engineering teams to identify and resolve quality-related issues promptly
10 Supplier Quality Engineer Resume Examples & Guide for 2025
Supplier quality engineers focus on ensuring that the materials and components supplied meet the required quality standards and specifications. When crafting your resume, highlight your experience in quality control processes, your ability to conduct supplier audits, and your expertise in problem-solving methodologies. Including skills like statistical analysis, root cause analysis, and effective communication can strengthen your application. Mentioning successful cross-functional collaboration on quality improvement projects and quantifiable achievements in reducing defects will demonstrate your impact in previous roles.
All resume examples in this guide
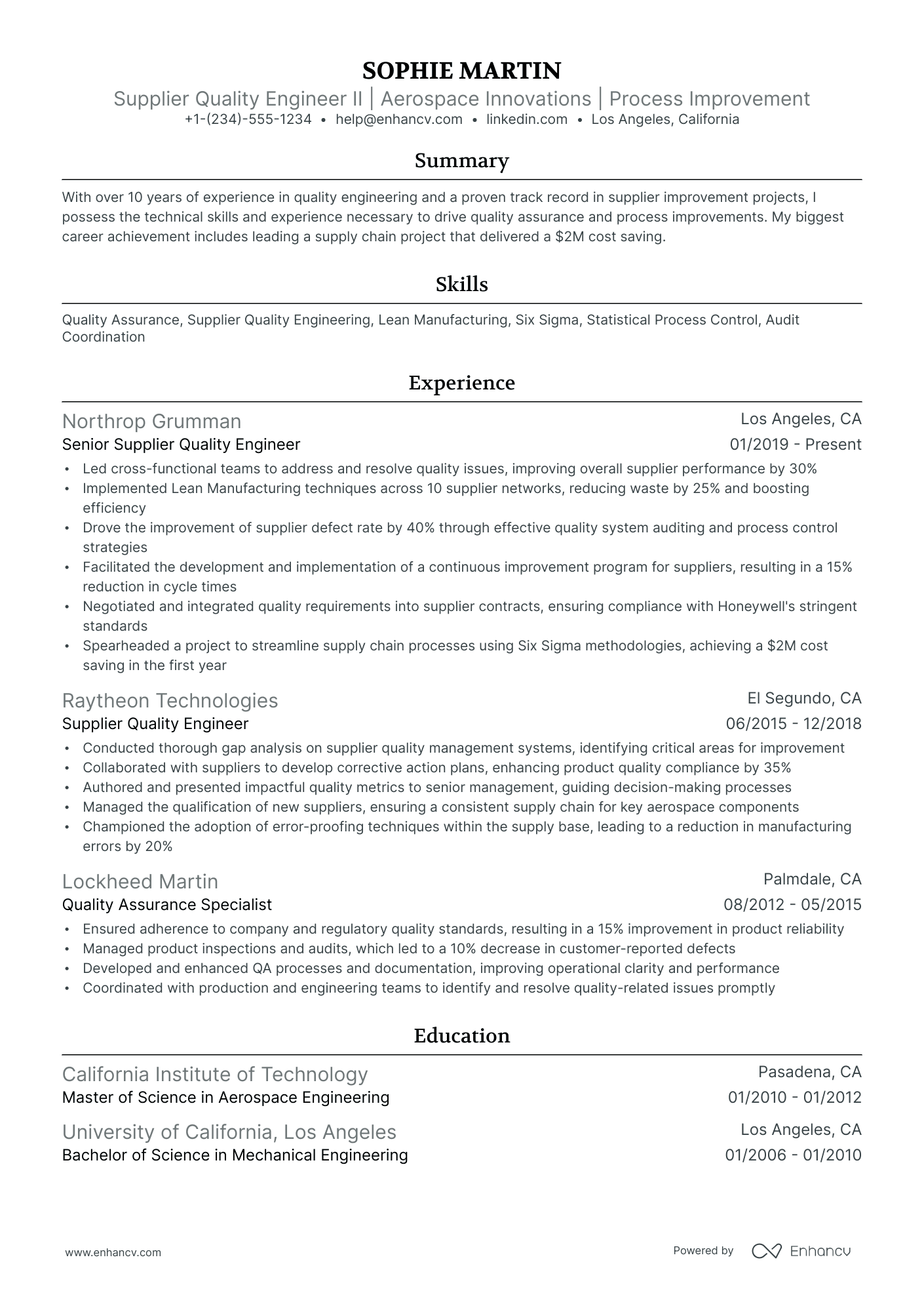
Single Column
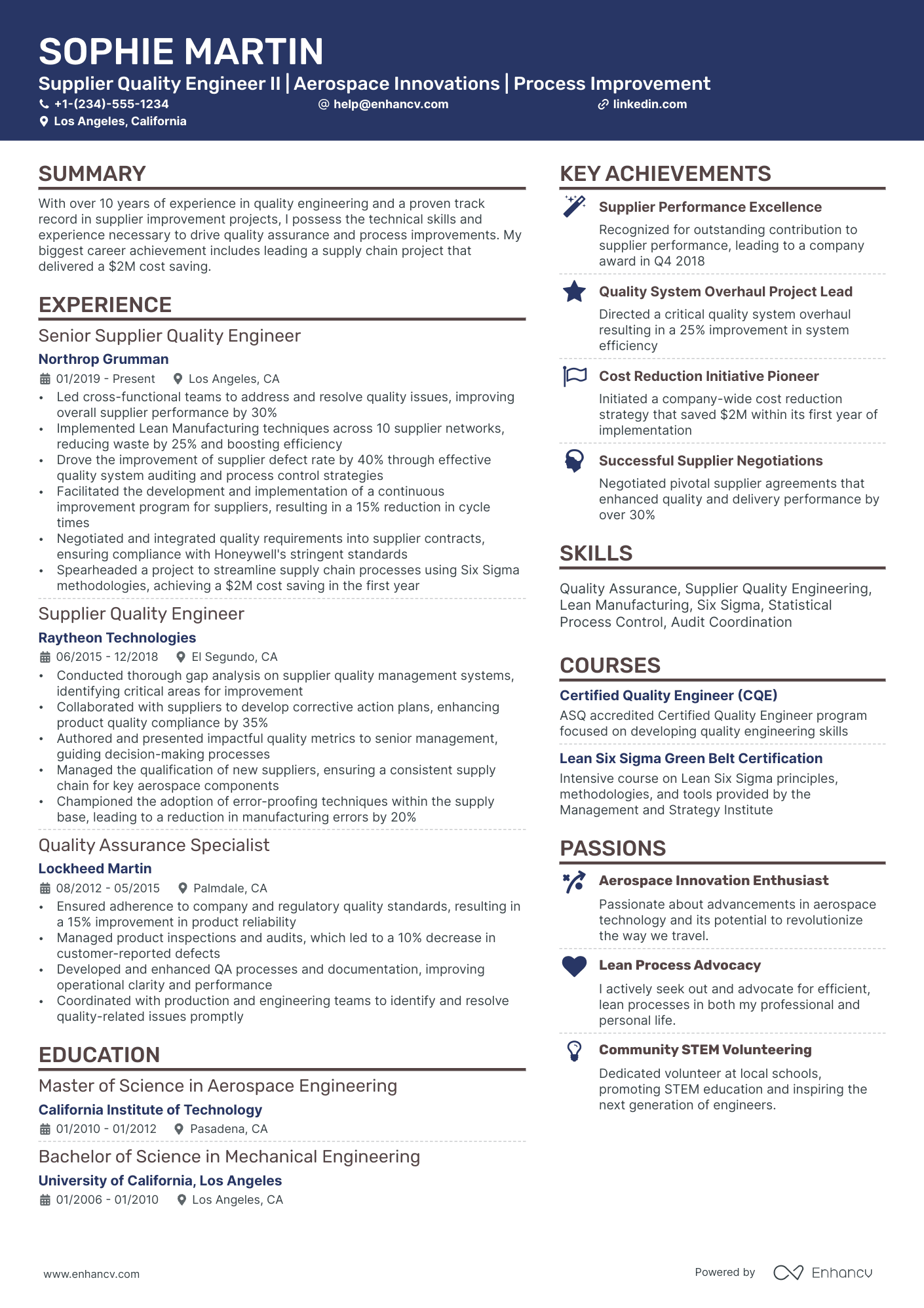
Written by The Enhancv Team
Resume Guide
Resume Format Tips
Resume Experience
Skills on Resume
Education & Certifications
Resume Summary Tips
Additional Resume Sections
Key Takeaways
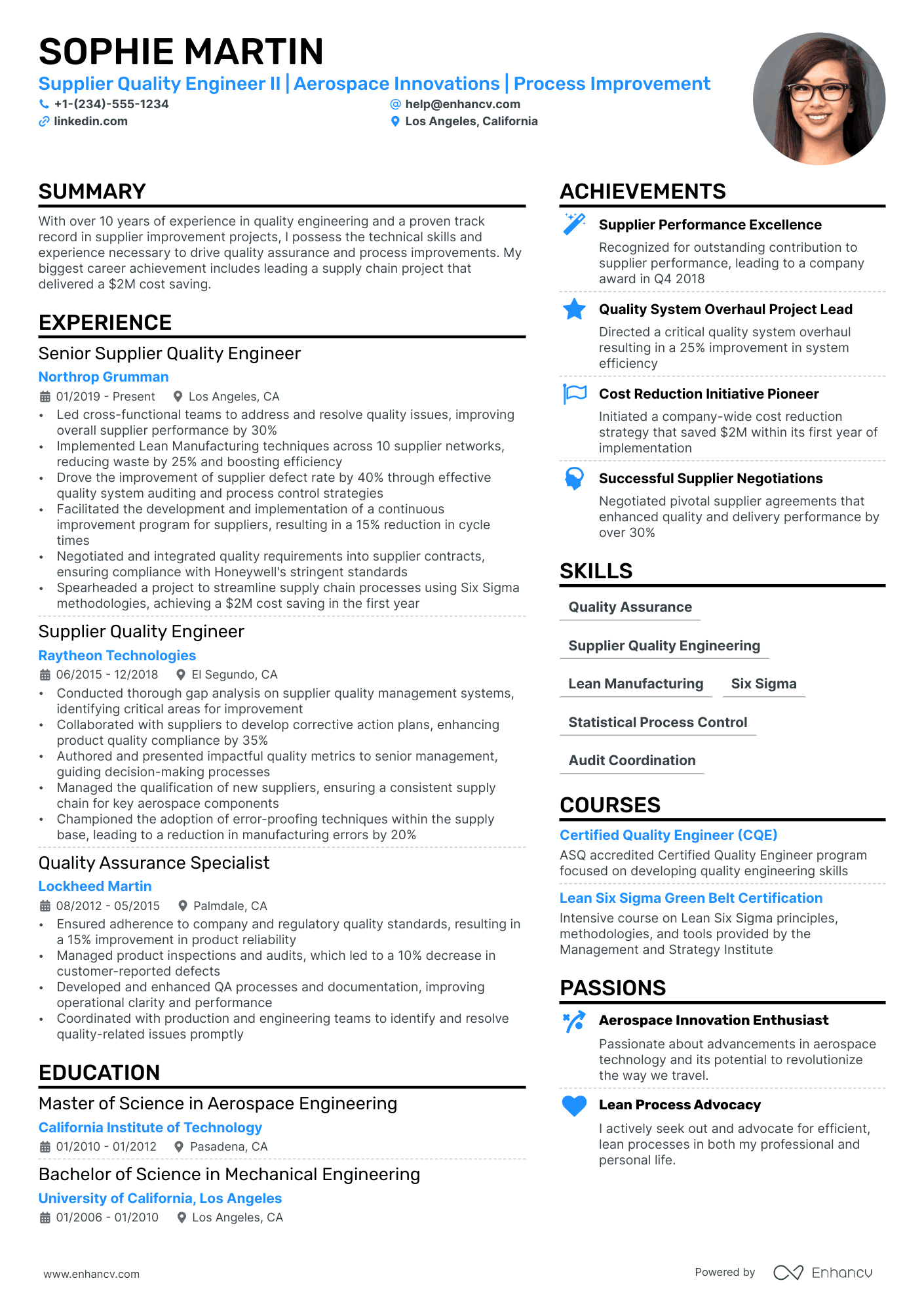
As a supplier quality engineer, articulating your complex collaboration and problem-solving experiences on a resume can be challenging. Our guide offers targeted advice and examples on how to distill these intricate interactions into impactful bullet points that will catch an employer's eye.
- Get inspired from our supplier quality engineer resume samples with industry-leading skills, certifications, and more.
- Show how you can impact the organization with your resume summary and experience.
- Introducing your unique supplier quality engineer expertise with a focus on tangible results and achievements.
If the supplier quality engineer resume isn't the right one for you, take a look at other related guides we have:
- QA Manager Resume Example
- Quality Technician Resume Example
- Quality Assurance Engineer Resume Example
- Quality Control Manager Resume Example
- Quality Assurance Technician Resume Example
- Data Quality Analyst Resume Example
- Quality Control Engineer Resume Example
- Quality Supervisor Resume Example
- Quality Control Technician Resume Example
- Quality Control Inspector Resume Example
Creating the best supplier quality engineer resume format: four simple steps
The most appropriate supplier quality engineer resume format is defined by precision and a systematic approach. What is more, it should reflect upon how your application will be assessed by recruiters. That is why we've gathered four of the most vital elements to keep in mind when designing your resume:
- It's all about presenting how your experience or skills align with the job. Use the reverse-chronological resume format , if your expertise is relevant to the supplier quality engineer role. Otherwise, select the functional skill-based resume format or the hybrid resume format to shift the focus to your skill set.
- Resume header - make sure you've filled out all relevant (and correct) information, like your contact details and link to your portfolio.
- Resume length - unless you've over a decade of applicable expertise in the field, stick with a one-page resume format. If you'd like to present more of your professional experience, go up to two pages.
- Resume file - submit your supplier quality engineer resume in a PDF format to ensure all information stays in the same place.
Upload & Check Your Resume
Drop your resume here or choose a file . PDF & DOCX only. Max 2MB file size.
The more time and effort you've put into obtaining the relevant certificate, the closer to the top it should be listed. This is especially important for more senior roles and if the company you're applying for is more forward-facing.
Essential sections that should make up your supplier quality engineer resume include:
- The header - with your contact details (e.g. email and telephone number), link to your portfolio, and headline
- The summary (or objective) - to spotlight the peaks of your professional career, so far
- The experience section - with up to six bullets per role to detail specific outcomes
- The skills list - to provide a healthy mix between your personal and professional talents
- The education and certification - showing your most relevant degrees and certificates to the supplier quality engineer role
What recruiters want to see on your resume:
- Experience in supplier evaluation, auditing, and qualification processes.
- Knowledge of quality management systems (e.g., ISO 9001) and industry-specific standards.
- Proficiency in root cause analysis and corrective action implementation.
- Familiarity with statistical process control (SPC), Six Sigma, or other quality improvement methodologies.
- Demonstrated history of managing cross-functional teams and projects to improve supplier quality performance.
Experts' advice on writing your supplier quality engineer resume experience
While the excitement and motivation for writing your supplier quality engineer resume was present in the first hour (or so), you now find yourself staring at the blank page.
The resume experience section is the one that allows you to make a memorable impression by matching job requirement with your past jobs and accomplishments.
To help you write this resume section, here are four mistakes you need to avoid:
- Listing every job you have had so far, including the irrelevant ones. Before that, consider each of your past roles based on relevancy to the role. It may be the case that the job you had 15 years ago may have taught you invaluable skills that are appropriate for the role;
- Including irrelevant work experience items . Those are past jobs that aren't linked with the role you're applying for (or so they seem). Consider how your past jobs will serve your professional presentation: will they be filling in a gap in your work history, or just taking up space?
- Focusing on responsibilities instead of accomplishments. Your supplier quality engineer resume shouldn't just be telling recruiters what you did in the past - as it's most often the case that candidates have had similar responsibilities. But, rather, the experience section should showcase the success you've attained in each past role, thanks to your unique skill set;
- Consider listing just your professional experience. Any role you've had in the past - e.g. volunteering, internships, etc. - can make it into your supplier quality engineer resume experience section. Make sure to include it alongside numbers and results.
Two more things you need to remember about your resume experience section.
The first are keywords. Or those specific job requirements that are crucial for the role . Ensure you've integrated them across your experience section to get sorted closer to the ideal candidate profile by the Applicant Tracker System (ATS).
The second are action verbs. Each of your experience bullets should start with a strong action verb , followed by your specific skill and your on the job achievements. Follow this formula to hint to recruiters what your unique value as a professional is.
Still with us? In the next section, we will show you how industry-leading professionals have avoided the four most common mistakes, while integrating keywords and action verbs in their experience section.
- Developed a supplier qualification program resulting in a 25% reduction in part defects and a 15% improvement in overall product quality.
- Managed cross-functional teams to perform on-site supplier audits, assessing compliance with ISO 9001 standards and implementing corrective actions.
- Led a project to transition suppliers to more sustainable materials, achieving a 20% reduction in the environmental impact of products.
- Designed and executed a statistical process control system for critical supplier components, reducing variability and improving consistency by 30%.
- Coordinated with global suppliers to enhance manufacturing processes, elevating our suppliers' capabilities and resulting in a 12% increase in efficiency.
- Implemented quality performance metrics for key suppliers and initiated quarterly reviews, which improved supplier performance by 18%.
- Collaborated with R&D and suppliers on new product launches, ensuring 100% of materials met stringent quality benchmarks before release.
- Conducted process validation assessments for 50+ suppliers, improving process reliability and product life cycle.
- Orchestrated the root cause analysis for product failures, which led to a 40% reduction in warranty claims.
- Oversaw the development and implementation of supplier improvement programs that resulted in a 10% cost reduction while maintaining quality standards.
- Negotiated quality agreements with new suppliers, contributing to an 8% faster time-to-market for new products.
- Pioneered the deployment of quality-focused training for supplier personnel, which decreased defects rate by 22%.
- Executed a comprehensive supplier risk management strategy that minimized disruptions by identifying potential risks early.
- Collaborated closely with procurement to drive supplier integration and lean initiatives, which yielded an annual savings of $3 million.
- Championed a ‘Zero Defect’ program across key suppliers, which cut down the defect ratio by 50% in critical components.
- Developed a supplier scorecard and evaluation system that increased the accountability and performance of suppliers by 15% year-over-year.
- Enhanced supplier selection criteria using comprehensive data analysis, improving on-time delivery by 20% and reducing material shortages.
- Managed the transition of a critical product line to a new supplier, which cut direct costs by 13% while upholding quality standards.
- Facilitated the supplier transition for a high-volume product, preserving product quality and reducing costs by $4.5M annually.
- Cultivated strategic partnerships with suppliers to share best practices, improving the Mean Time Between Failures (MTBF) by 500 hours.
- Drove a continuous quality improvement plan that resulted in a 35% enhancement in part reliability from top-tier suppliers.
- Initiated a supplier development program which optimized supplier deliverables and cut procurement costs by 10%.
- Collaborated on a cross-functional team to map out a supplier consolidation strategy, improving sourcing efficiency by 25%.
- Led the qualification of new suppliers in Asia, expanding the company's supplier base and reducing lead times by 15% for critical components.
The following content includes information from "O*NET OnLine" by the U.S. Department of Labor, Employment and Training Administration (USDOL/ETA). Used under the CC BY 4.0 license. The data represents the top responsibilities present on the task lists for supplier quality engineer professionals.
Top Responsibilities for Supplier Quality Engineer:
- Analyze information to determine, recommend, and plan installation of a new system or modification of an existing system.
- Analyze user needs and software requirements to determine feasibility of design within time and cost constraints.
- Confer with data processing or project managers to obtain information on limitations or capabilities for data processing projects.
- Confer with systems analysts, engineers, programmers and others to design systems and to obtain information on project limitations and capabilities, performance requirements and interfaces.
- Consult with customers or other departments on project status, proposals, or technical issues, such as software system design or maintenance.
- Coordinate installation of software system.
- Design, develop and modify software systems, using scientific analysis and mathematical models to predict and measure outcomes and consequences of design.
- Determine system performance standards.
- Develop or direct software system testing or validation procedures, programming, or documentation.
- Modify existing software to correct errors, adapt it to new hardware, or upgrade interfaces and improve performance.
Quantifying impact on your resume
- Detail the percentage reduction in supplier defect rates year-over-year under your quality management.
- Highlight the number of supplier audits conducted and the subsequent compliance rate improvements.
- Specify the dollar value of cost savings realized through process improvements or negotiation with suppliers.
- Quantify the reduction in product return rates due to enhanced supplier quality controls.
- Include the number of suppliers you have qualified or re-qualified for business to underscore your due diligence.
- State the percentage increase in on-time delivery from suppliers after implementing process enhancements.
- Mention the size of the supplier base you manage to illustrate the scale of your responsibilities.
- List any awards or recognition received for outstanding performance in supplier quality management.
Action verbs for your supplier quality engineer resume
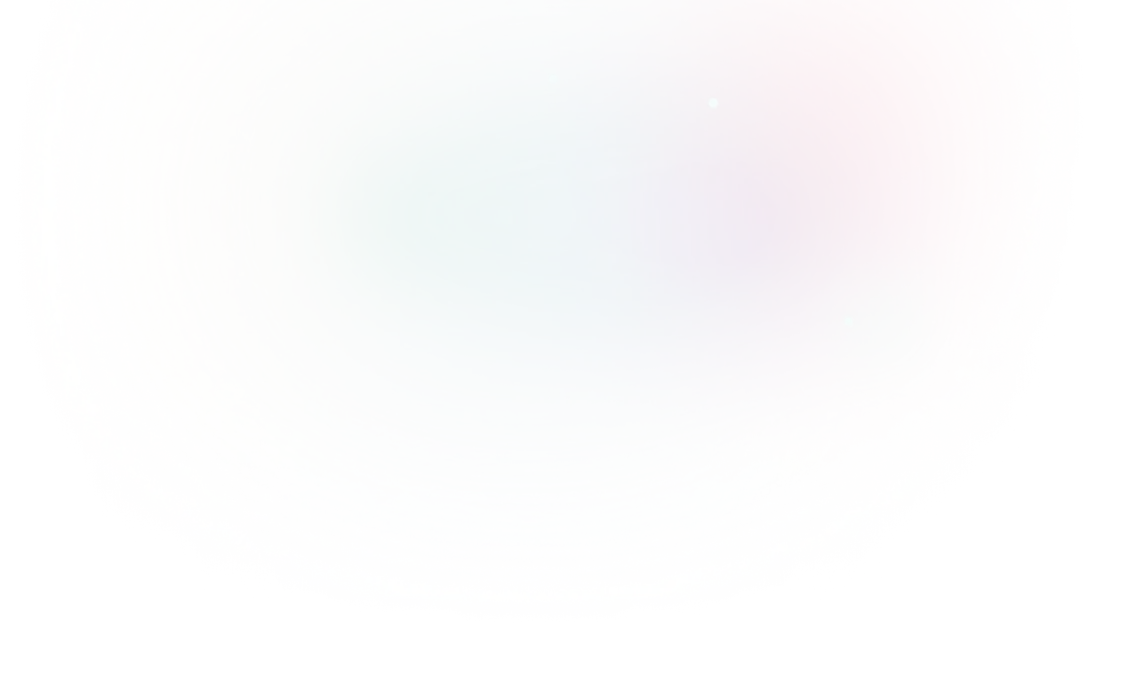
Making the most of your little to none professional experience
If you're hesitant to apply for your dream job due to limited professional experience , remember that recruiters also value the unique contributions you can offer.
Next time you doubt applying, consider this step-by-step approach for your resume's experience section:
- Rather than the standard reverse chronological order, opt for a functional-based format. This shifts the focus from your work history to your achievements and strengths;
- Include relevant internships, volunteer work, or other non-standard experiences in your supplier quality engineer resume's experience section;
- Utilize your education, qualifications, and certifications to bridge gaps in your supplier quality engineer resume experience;
- Emphasize your interpersonal skills and transferable skills from various industries. Often, recruiters seek a personality match, giving you an advantage over other candidates.
Recommended reads:
- When You Should (And Not) Add Dean's List On Your Resume
- Should I Put In An Incomplete Degree On A Resume?
If you happen to have some basic certificates, don't invest too much of your supplier quality engineer resume real estate in them. Instead, list them within the skills section or as part of your relevant experience. This way you'd ensure you meet all job requirements while dedicating your certificates to only the most in-demand certification across the industry.
Featuring your hard skills and soft skills on your supplier quality engineer resume
The skills section of your supplier quality engineer resume needs to your various capabilities that align with the job requirements. List hard skills (or technical skills) to showcase to potential employers that you're perfectly apt at dealing with technological innovations and niche software. Meanwhile, your soft skills need to detail how you'd thrive within your new, potential environment with personal skills (e.g. resilience, negotiation, organization, etc.) Your supplier quality engineer resume skills section needs to include both types of skills to promote how you're both technical and cultural fit. Here's how to create your bespoke supplier quality engineer skills section to help you stand out:
- Focus on skill requirements that are listed toward the top of the job advert.
- Include niche skills that you've worked hard to obtain.
- Select specific soft skills that match the company (or the department) culture.
- Cover some of the basic job requirements by including important skills for the supplier quality engineer role - ones you haven't been able to list through the rest of your resume.
Get inspired with our supplier quality engineer sample skill list to list some of the most prominent hard and soft skills across the field.
Top skills for your supplier quality engineer resume:
Statistical Process Control (SPC)
Failure Mode and Effects Analysis (FMEA)
Root Cause Analysis (RCA)
Quality Management Systems (QMS)
ISO 9001 Standards
Six Sigma methodologies
Supplier Auditing Tools
Measurement System Analysis (MSA)
Control Charts
Quality Improvement Tools
Communication Skills
Problem-Solving
Attention to Detail
Team Collaboration
Analytical Thinking
Negotiation Skills
Time Management
Adaptability
Leadership Skills
Conflict Resolution
Next, you will find information on the top technologies for supplier quality engineer professonals from "O*NET OnLine" by the U.S. Department of Labor, Employment and Training Administration (USDOL/ETA). Used under the CC BY 4.0 license.
Top technologies for Supplier Quality Engineer’s resume:
- Oracle Java 2 Platform Enterprise Edition J2EE
- Oracle SQL Developer
- Blackboard software
- Apache Spark
Mention specific courses or projects that are pertinent to the job you're applying for.
Listing your education and certifications on your supplier quality engineer resume
Don't underestimate the importance of your resume education section . As it may hint at various skills (and experience) that are relevant to the job. When writing your education section:
- Include only higher education degrees with information about the institution and start/end dates
- If you're in the process of obtaining your degree, include your expected graduation date
- Consider leaving off degrees that aren't relevant to the job or industry
- Write a description of your education if it presents you with an opportunity to further showcase your achievements in a more research-focused environment
When describing your certifications on your resume, always consider their relevancy to the role. Use the same format to describe them as you would for your education. If you're wondering what the best certificates out there are for supplier quality engineer roles, check out the list below.
The top 5 certifications for your supplier quality engineer resume:
- Certified Quality Engineer (CQE) - American Society for Quality (ASQ)
- Certified Supplier Quality Professional (CSQP) - American Society for Quality (ASQ)
- Six Sigma Green Belt Certification (SSGB) - Various Institutions
- ISO 9001:2015 Lead Auditor Certification - International Register of Certificated Auditors (IRCA)
- Certified Professional in Supply Management (CPSM) - Institute for Supply Management (ISM)
The content below includes information from "O*NET OnLine" by the U.S. Department of Labor, Employment and Training Administration (USDOL/ETA). Used under the CC BY 4.0 license. The data represents the top associations for supplier quality engineer professionals.
Top US associations for a Supplier Quality Engineer professional
- Association for Computing Machinery
- Association for Information Science and Technology
- Association for Information Systems
- Association for the Advancement of Artificial Intelligence
- Association for Women in Computing
Always remember that your supplier quality engineer certifications can be quantified across different resume sections, like your experience, summary, or objective. For example, you could include concise details within the expertise bullets of how the specific certificate has improved your on-the-job performance.
- How To List Certifications On A Resume (Examples Included)
- Should You Include Eagle Scout On Your Resume?
Practical guide to your supplier quality engineer resume summary or objective
First off, should you include a summary or objective on your supplier quality engineer resume?
We definitely recommend you choose the:
- Resume summary to match job requirements with most noteworthy accomplishments.
- Resume objective as a snapshot of career dreams
Both the resume summary and objective should set expectations for recruiters as to what your career highlights are.
These introductory paragraphs (that are no more than five sentences long) should help you answer why you're the best candidate for the job.
Industry-wide best practices pinpoint that the supplier quality engineer resume summaries and objectives follow the structures of these samples:
Resume summaries for a supplier quality engineer job
- Seasoned supplier quality engineer with 8 years of experience in enhancing the manufacturing processes at a Fortune 500 automotive components producer. Expert in statistical process control, root cause analysis, and corrective action planning. Recognized for developing and implementing quality systems reducing defective rates by 30% within the first year.
- Driven professional transitioning from a successful 10-year career in aerospace engineering to supplier quality engineering, bringing a thorough understanding of material properties and failure mode effects analysis. Adept at cross-functional collaboration and eager to apply problem-solving skills to optimize supply chain integrity and performance.
- Experienced in process improvement and regulation compliance, a former Production Manager with 12 years in food and beverage industry aims to leverage systematic approach and keen eye for detail into supplier quality management, focusing on vendor evaluation and performance metrics to enhance final product excellence.
- Eager to transfer 7 years of project management experience within the renewable energy sector into supplier quality engineering, bringing a track record of successful supplier audits, and risk management initiatives, with deep knowledge of ISO 9001 and lean manufacturing principles.
- As a recent mechanical engineering graduate, eager to specialize in supplier quality engineering, I am committed to applying my academic training in quality control, process optimization, and materials science to ensure the highest standards of supply chain management and vendor satisfaction.
- Seeking to leverage my passion for technology and a strong foundation in industrial engineering education, I aim to embark on a career in supplier quality engineering, dedicated to mastering quality assurance techniques and supplier development to contribute to manufacturing excellence and product integrity.
Average salary info by state in the US for Supplier Quality Engineer professionals
Local salary info for Supplier Quality Engineer.” Source: My Next Move, National Center for O*NET Development. Accessed 10/15/2024
Miscellaneous supplier quality engineer resume sections for a more personalized approach
Your supplier quality engineer resume can reflect even more upon your personality and best qualities - that is if you decide on including a couple of additional resume sections to support your application.
Some of the best-accepted industry-wide choices include the:
- Resume projects - getting into the outcomes of your most important work, so far;
- Languages on your resume - detailing your proficiency level;
- Special recognitions - dedicated to your most prominent industry awards;
- Hobbies and interests - defining how you spend your free time.
Key takeaways
We trust that this Enhancv guide has been informative and useful. To summarize the essential points:
- Opt for a simple and readable format, focusing more on your supplier quality engineer achievements rather than just duties;
- Emphasize your accomplishments in the supplier quality engineer experience section over mere responsibilities;
- If lacking relevant experience, utilize various resume sections like education and volunteering to demonstrate your suitable skill set;
- Never overlook the significance of pertinent higher education, training, and certifications;
- Incorporate diverse sections in your resume to highlight not just your skills expertise but also your personality.
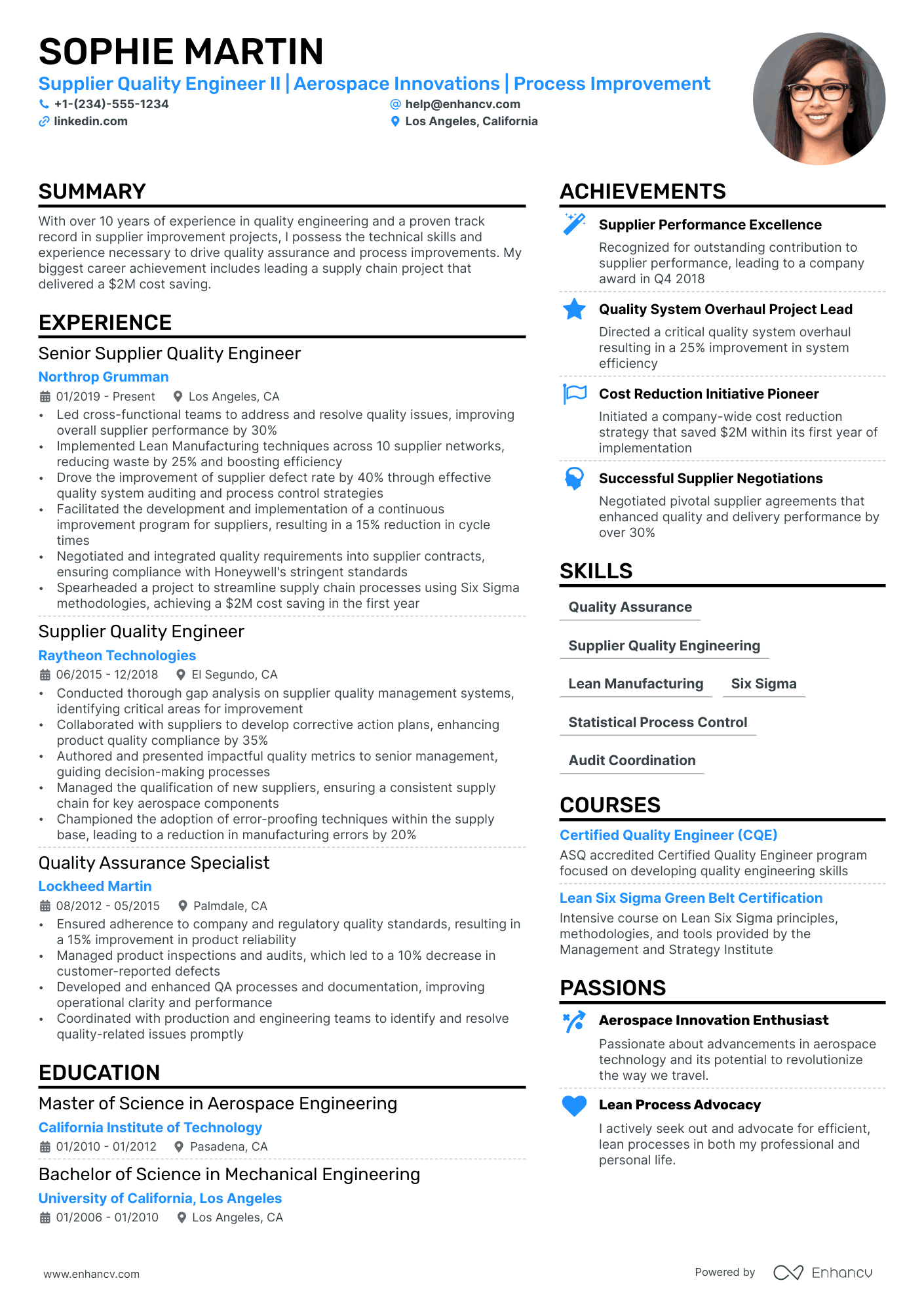
Looking to build your own Supplier Quality Engineer resume?
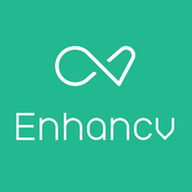
- Resume Examples
How Long Should A CV Be
How to spot toxic work culture at the interview: 17 signs to watch out for, how to edit and proofread your resume professionally to get hired, how to answer the "what are you looking for in a new position" interview question, how to list projects on a resume: a concise approach, quitting your job without another one lined up: pros and cons.
- Create Resume
- Terms of Service
- Privacy Policy
- Cookie Preferences
- Resume Templates
- Resume Builder
- Resume Summary Generator
- Resume Formats
- Resume Checker
- AI Resume Review
- Resume Skills
- How to Write a Resume
- Modern Resume Templates
- Simple Resume Templates
- Cover Letter Builder
- Cover Letter Examples
- Cover Letter Generator
- Cover Letter Templates
- Cover Letter Formats
- How to Write a Cover Letter
- Resume Guides
- Cover Letter Guides
- Job Interview Guides
- Job Interview Questions
- Career Resources
- [email protected]
- English (UK)
- French (FR)
- German (DE)
- Spanish (ES)
- Swedish (SE)
Made with love by people who care.
© 2024 . All rights reserved.
Resume Worded | Proven Resume Examples
- Resume Examples
- Engineering Resumes
- Quality Engineer Resume Guide & Examples
Supplier Quality Engineer Resume Examples: Proven To Get You Hired In 2024
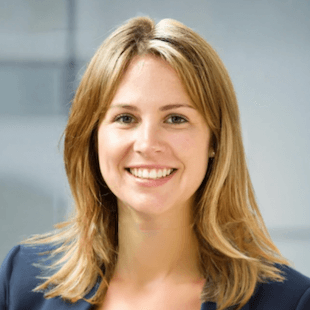
Jump to a template:
- Supplier Quality Engineer
- Quality Assurance Engineer
- Procurement Engineer
- Quality Control Engineer
- Quality Systems Engineer
Get advice on each section of your resume:
Jump to a resource:
- Supplier Quality Engineer Resume Tips
Supplier Quality Engineer Resume Template
Download in google doc, word or pdf for free. designed to pass resume screening software in 2022., supplier quality engineer resume sample.
As a Supplier Quality Engineer, you're the vital connection between a company and its suppliers, ensuring goods meet the company's high standards. It's a role that requires a mix of technical know-how and relationship building skills. There's been a recent shift in this role towards more data-driven decision making. So when you're preparing your resume, you should ensure it demonstrates not only your skills in quality assurance and supplier management, but also your ability to interpret and analyze data. Remember, it's not just about showcasing your technical competence. Highlight your soft skills too. The best Supplier Quality Engineers are communicators, collaborators, and problem-solvers.
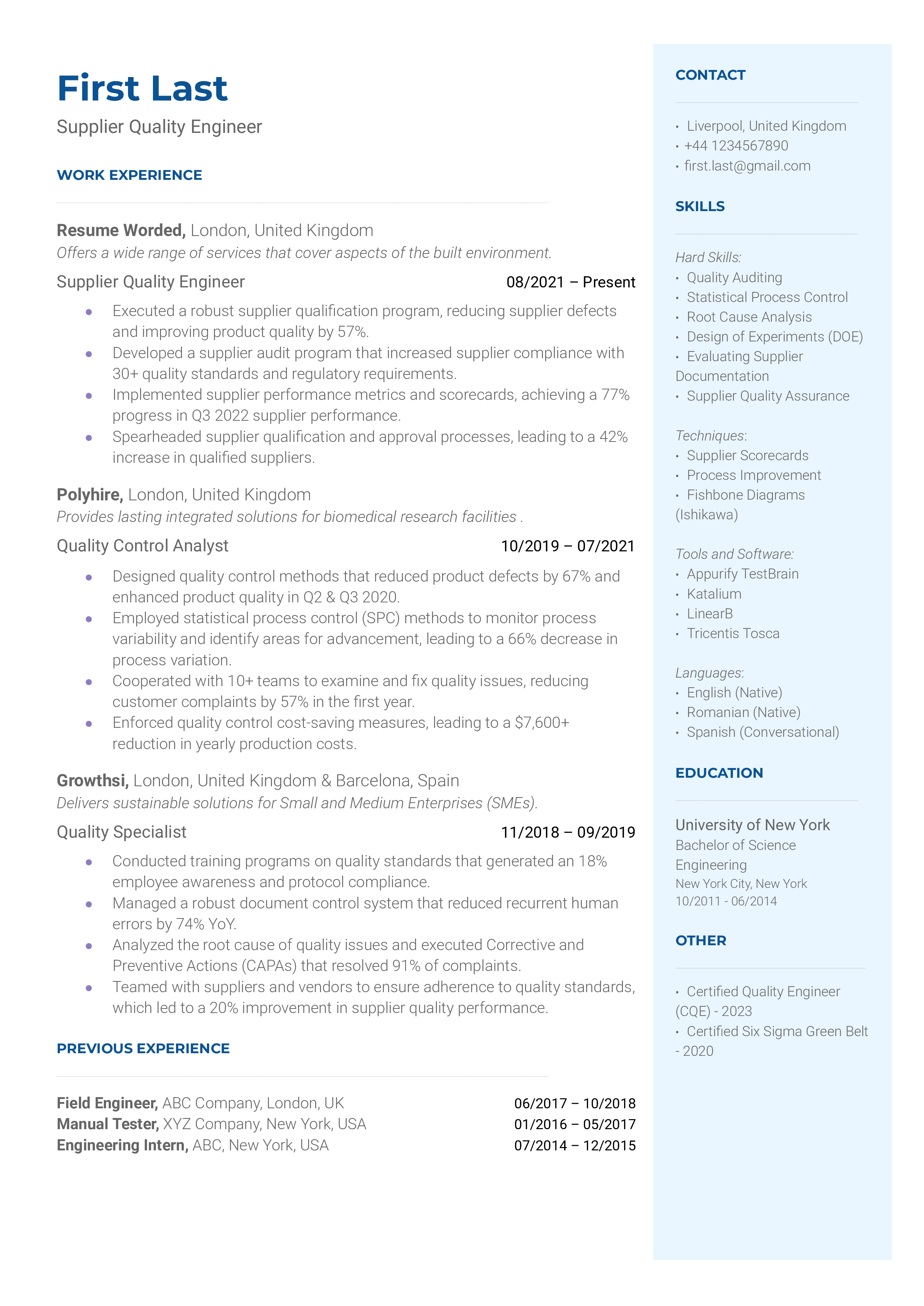
We're just getting the template ready for you, just a second left.
Recruiter Insight: Why this resume works in 2022
Tips to help you write your supplier quality engineer resume in 2024, highlight industry-specific experience.
When you're drafting your resume, don't just list your previous roles. Instead, highlight how this experience is relevant to the industry you're applying within. If you've worked with suppliers from the same or similar sector, make that stand out. It shows you understand the unique challenges and standards of that industry.
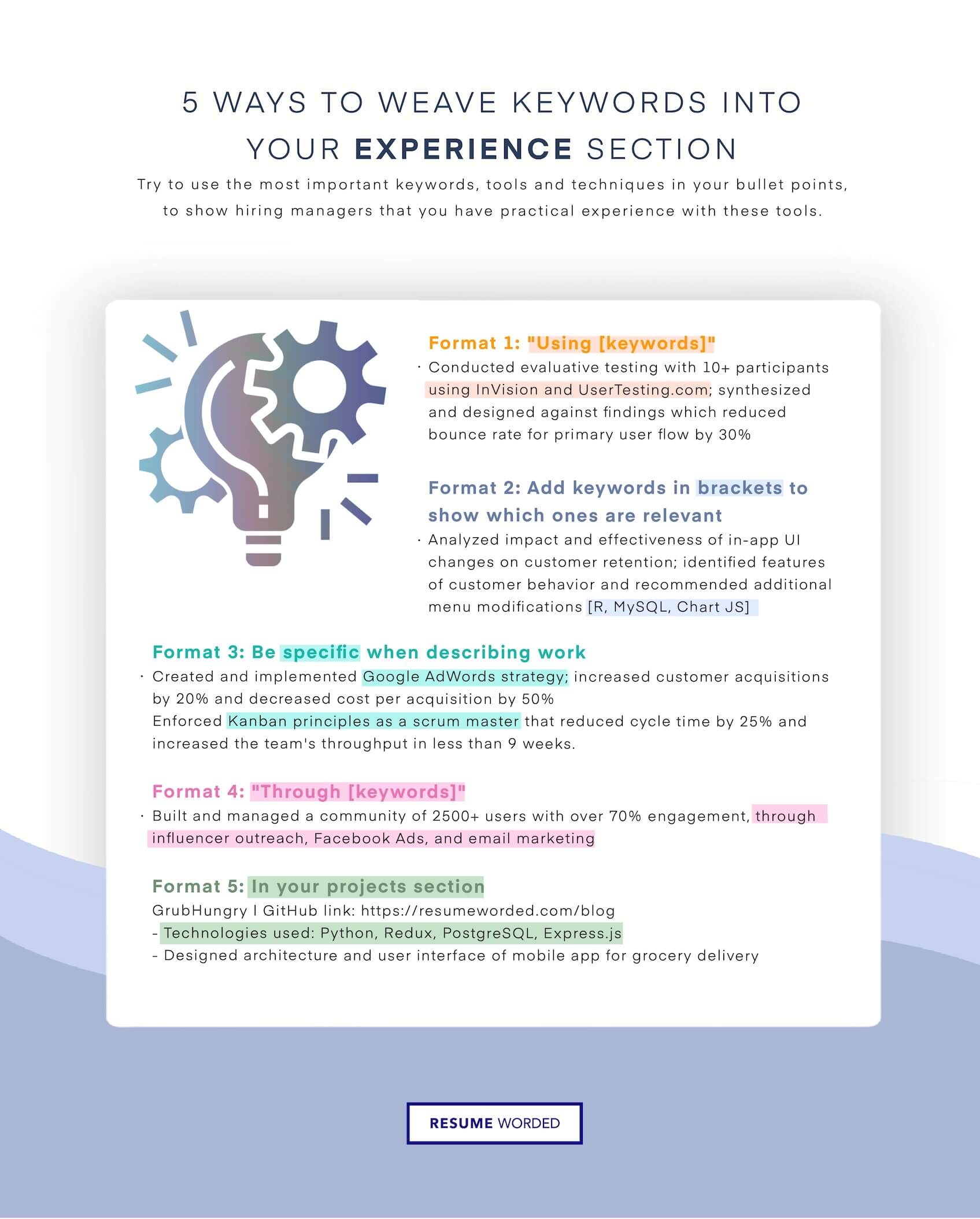
Showcase data analysis skills
The role of a Supplier Quality Engineer is increasingly data-driven. Therefore, make sure your resume clearly demonstrates your ability to interpret and analyze data. This could be through highlighting specific data analysis projects you've led, or relevant certifications you've achieved.
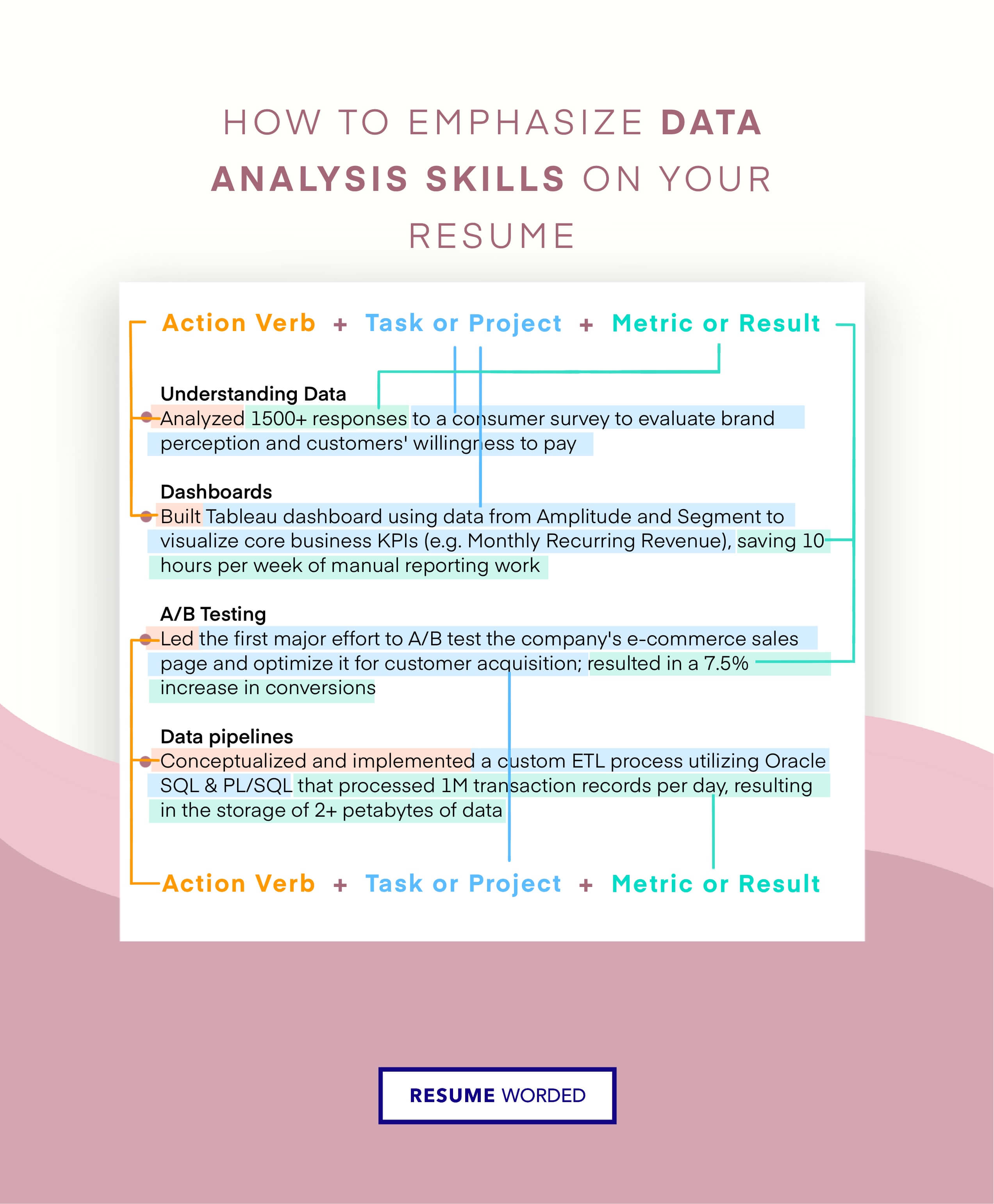
Supplier Quality Engineers work with logistics, supply chain management, and manufacturing. They ensure that all products meet company, industry, and government standards and lack any defects. To advance in this field, it’s important to show your strong technical and analytical skills through previous roles, using numbers and specific examples to quantify your proven results.
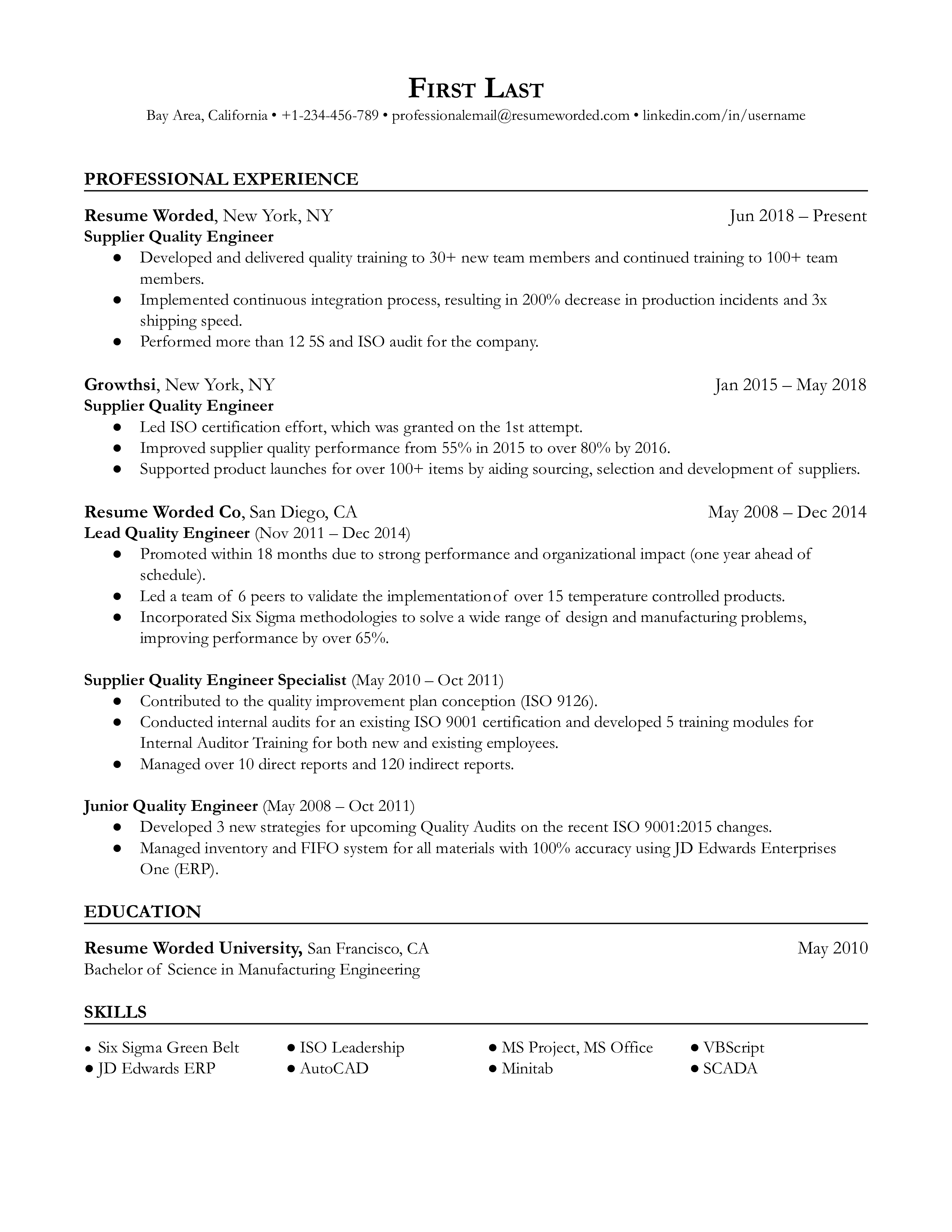
Strong use of skills relating to Supplier Quality Engineer skills
You must have strong technical qualifications to succeed in specialized and technical fields like Quality Engineering. Look at job descriptions and see what programs and software employers will expect you to know. If it’s listed in the description, make sure to include it in your skills section or throughout your bullet points.
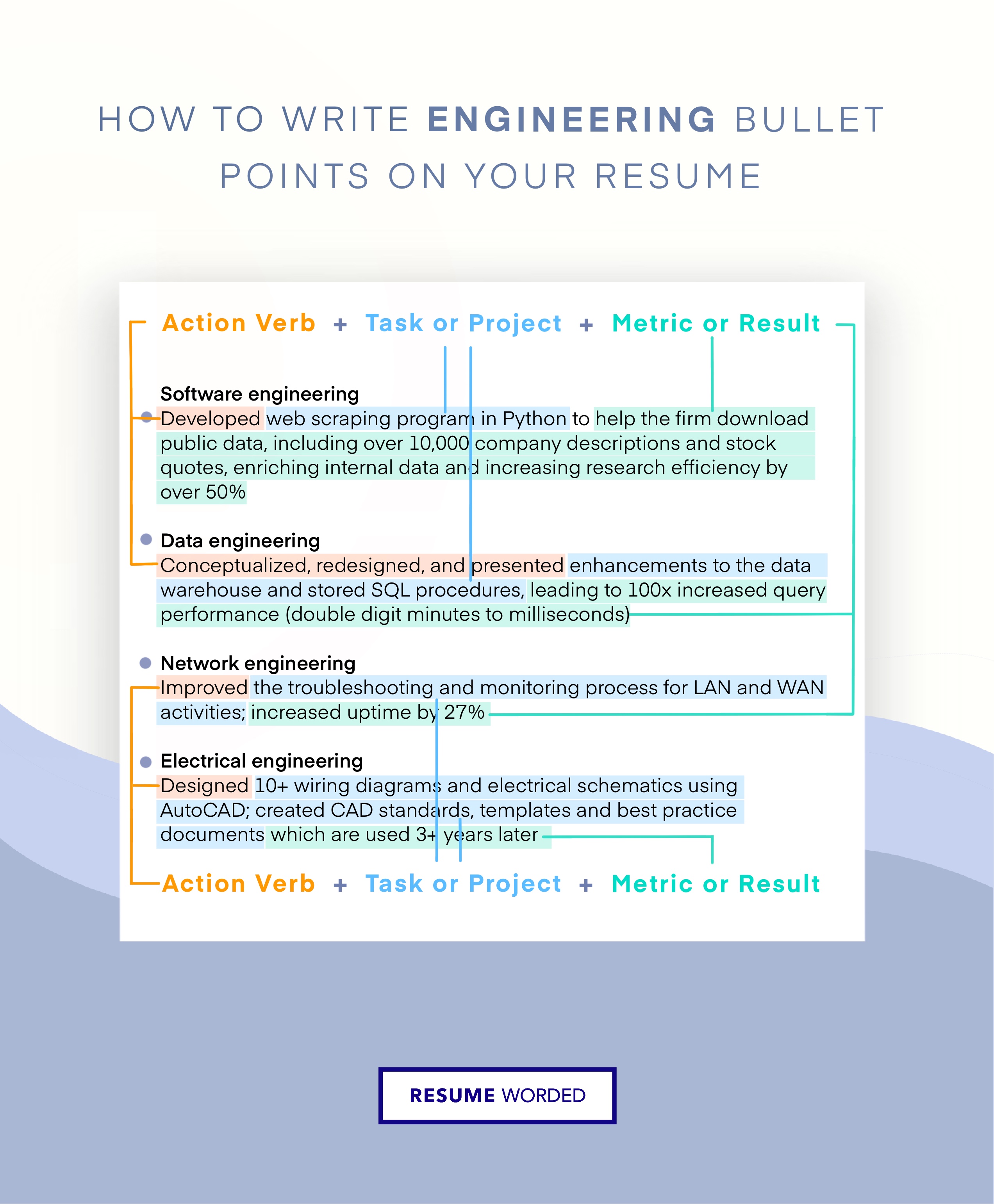
Show substantial experience in Quality Engineering
When you have 10+ years of experience, you’ll want to emphasize examples of leading teams, advancing, and training others. Also, make sure to highlight with metrics how you improved your team, department, or company as a whole. For example, like this resume, “implemented continuous integration process, resulting in 200% decrease in production incidents and 3x shipping speed.”
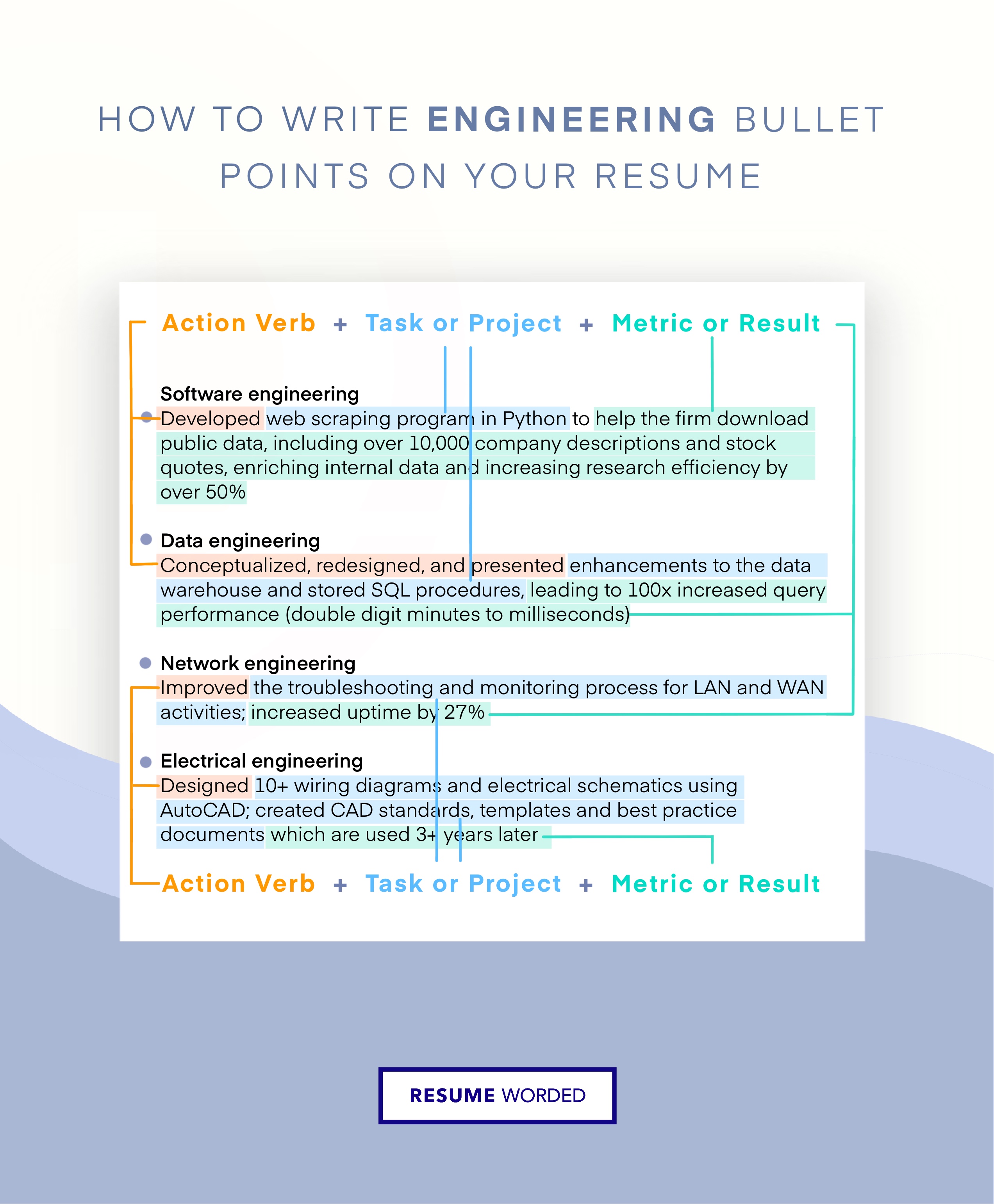
Quality Assurance Engineer Resume Sample
Procurement engineer resume sample, quality control engineer resume sample, quality systems engineer resume sample.
As a hiring manager who has reviewed hundreds of resumes for Supplier Quality Engineer positions at top companies like Boeing, GE, and Lockheed Martin, I have seen firsthand what makes a resume stand out. In this article, we'll cover some key tips that will help your resume get noticed by hiring managers and increase your chances of landing an interview.
Highlight your experience with specific quality standards
Employers want to see that you have experience working with the specific quality standards and certifications that are relevant to their industry, such as:
Be sure to mention any certifications you have earned and provide specific examples of how you have implemented and maintained these standards in your previous roles.
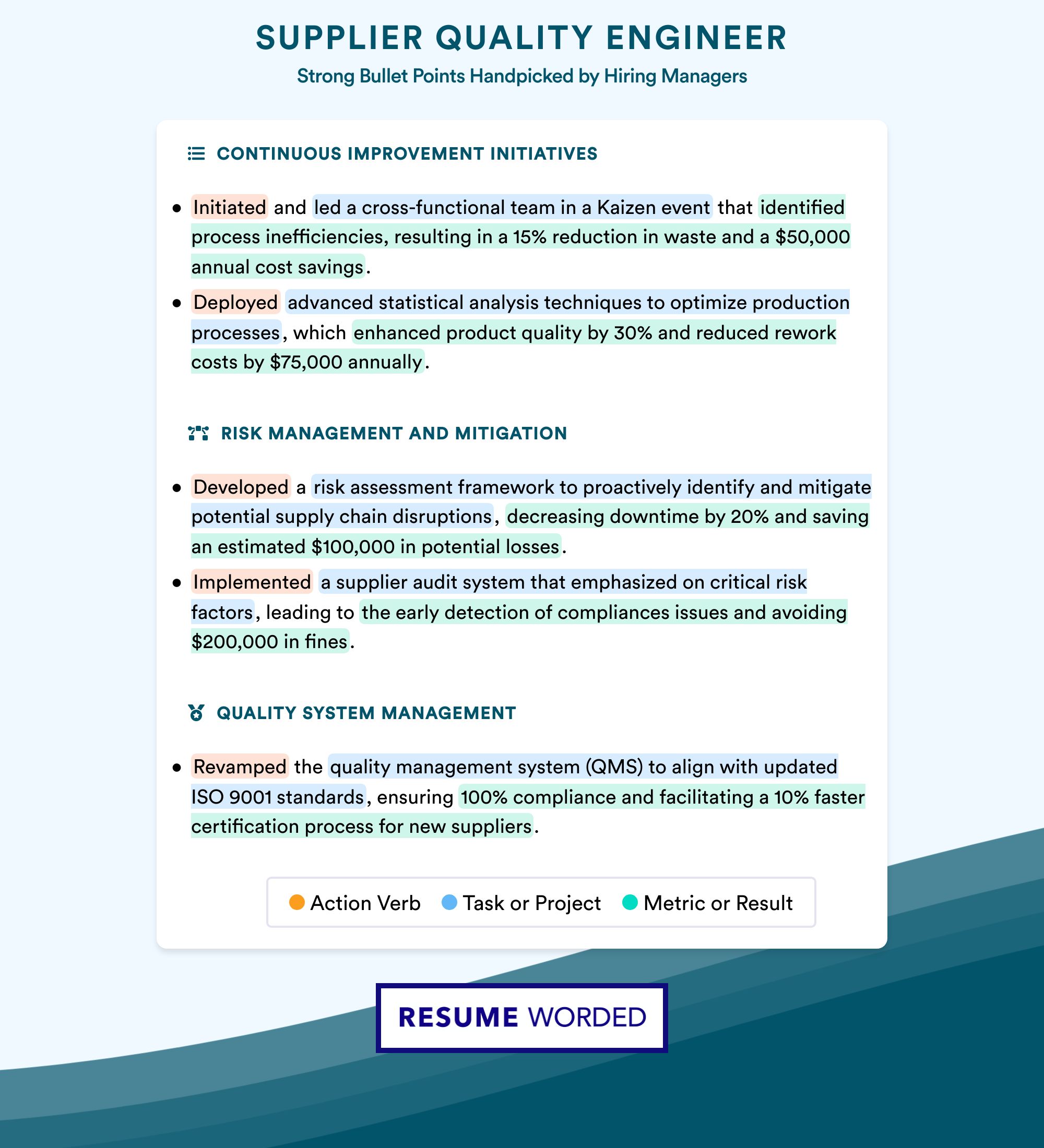
Quantify your impact on quality metrics
Hiring managers want to see concrete evidence of your ability to improve quality metrics. Instead of simply listing your responsibilities, quantify your achievements with specific numbers and percentages.
Compare these two examples:
- Responsible for reducing defect rates and improving supplier quality
- Reduced defect rates by 25% and improved supplier quality scores from 85% to 98% through implementation of new inspection processes and supplier audits
Demonstrate your problem-solving skills
Supplier Quality Engineers are often called upon to troubleshoot complex quality issues and implement corrective actions. Use your resume to showcase your problem-solving abilities with specific examples.
- Led root cause analysis of recurring defect that resulted in $500K in annual scrap costs; implemented corrective actions that reduced scrap by 80% within 6 months
- Developed and implemented new testing protocol that identified potential failure modes early in the production process, preventing $250K in potential warranty claims
Show your expertise in supplier management
Managing relationships with suppliers is a key responsibility for Supplier Quality Engineers. Highlight your experience in supplier selection, auditing, and performance management.
Managed quality performance for 25 key suppliers, conducting regular audits and implementing supplier scorecards that improved overall quality ratings by 20% and on-time delivery by 15%
If you have experience with specific supplier management tools or methodologies, such as supplier risk assessments or supplier corrective action reports (SCARs), be sure to mention those as well.
Tailor your resume to the specific job requirements
While it's important to showcase your overall quality engineering experience, be sure to tailor your resume to the specific requirements of each job you apply for. Review the job posting carefully and emphasize the skills and experiences that are most relevant.
For example, if the job posting mentions experience with a specific quality management system or industry standard, make sure that is prominently featured on your resume.
- Experienced in quality engineering
- 5+ years of experience implementing and maintaining ISO 13485 quality management system in the medical device industry
Include relevant education and certifications
While experience is the most important factor for Supplier Quality Engineer positions, relevant education and certifications can also help you stand out. Include your degree(s) in a relevant field, such as engineering or quality management, and any relevant certifications you have earned.
Some examples of certifications that are highly valued for Supplier Quality Engineers include:
- Certified Quality Engineer (CQE)
- Certified Supplier Quality Professional (CSQP)
- Six Sigma Green Belt or Black Belt
If you have completed any relevant coursework or training programs, such as a course in statistical process control or root cause analysis, you can also mention those in your education section.
Writing Your Supplier Quality Engineer Resume: Section By Section
summary.
A resume summary for a Supplier Quality Engineer is an optional section that can be a powerful addition to your resume when done right. It's a brief overview of your most relevant skills, experiences, and achievements, tailored to the specific job you're applying for. While a resume objective focuses on your career goals, a summary emphasizes what you can bring to the table for the employer.
When writing your Supplier Quality Engineer resume summary, it's crucial to avoid simply repeating information that's already in your resume. Instead, use this space to provide context, highlight your unique value proposition, and showcase your fit for the role. Remember, your summary should be concise, typically no more than a few sentences or a short paragraph.
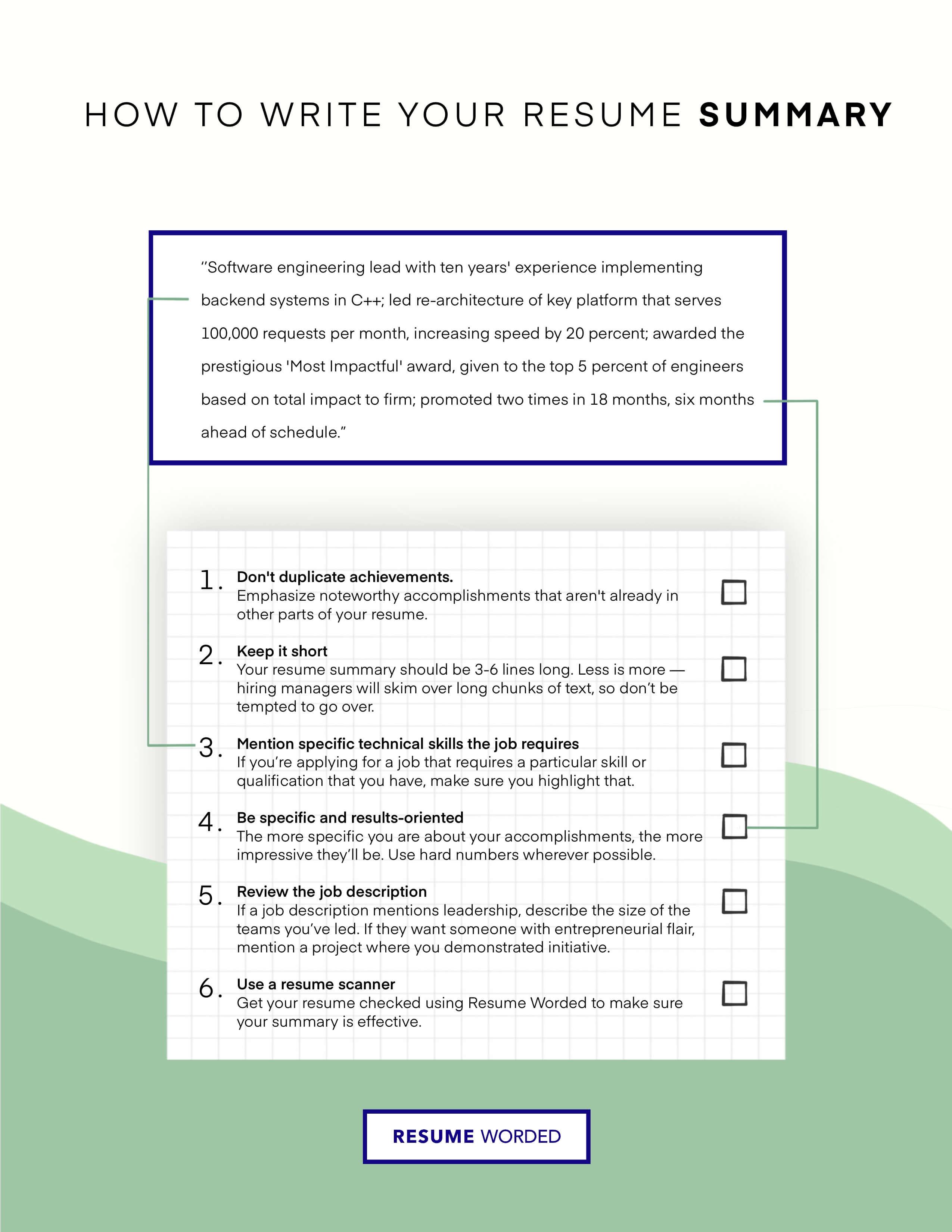
To learn how to write an effective resume summary for your Supplier Quality Engineer resume, or figure out if you need one, please read Supplier Quality Engineer Resume Summary Examples , or Supplier Quality Engineer Resume Objective Examples .
1. Highlight your quality assurance expertise
When crafting your Supplier Quality Engineer resume summary, it's essential to showcase your expertise in quality assurance and your ability to ensure that suppliers meet the company's standards. Consider including specific examples of how you've improved supplier quality in the past.
Here's an example of what to avoid:
- Experienced Supplier Quality Engineer with a proven track record of success.
While this summary mentions the job title and alludes to success, it's too vague and doesn't provide any concrete details. Instead, try something like this:
- Supplier Quality Engineer with 5+ years of experience implementing quality control processes that reduced defect rates by 30% and improved supplier performance.
This summary not only mentions the relevant job title and years of experience but also provides a specific example of how the candidate's expertise led to measurable results.
2. Tailor your summary to the job description
One of the most important things to keep in mind when writing your Supplier Quality Engineer resume summary is to tailor it to the specific job you're applying for. Review the job description carefully and identify the key skills and experiences the employer is looking for.
For example, if the job description emphasizes experience with ISO 9001 standards, you might write a summary like this:
Certified Supplier Quality Engineer with a strong background in ISO 9001 compliance. Skilled in developing and implementing quality management systems that ensure consistent product quality and supplier performance. Proven ability to collaborate with cross-functional teams to drive continuous improvement initiatives.
On the other hand, avoid using a generic summary that could apply to any Supplier Quality Engineer role, like this:
Experienced Supplier Quality Engineer seeking a new opportunity. Skilled in quality assurance, supplier management, and problem-solving. Strong communication and teamwork abilities.
While this summary mentions relevant skills, it doesn't connect them to the specific needs of the employer or provide any context for the candidate's experience.
Experience
The work experience section is the most important part of your supplier quality engineer resume. It's where you show hiring managers how you've applied your skills and knowledge to real-world situations and made an impact in your previous roles. Here are some key tips to keep in mind as you write this section:
1. Highlight relevant supplier quality experience
When writing your work experience section, focus on the responsibilities and achievements that are most relevant to the supplier quality engineer role you're applying for. This might include:
- Collaborating with suppliers to develop and implement quality control processes
- Conducting supplier audits to ensure compliance with quality standards
- Analyzing supplier performance data to identify areas for improvement
- Developing and maintaining supplier quality documentation, such as supplier quality manuals and inspection plans
By highlighting your most relevant experience, you'll show hiring managers that you have the skills and knowledge needed to succeed in the role.
2. Use strong action verbs
When describing your responsibilities and achievements, use strong action verbs to convey the impact you made in your previous roles. For example:
- Implemented a new supplier quality audit program that reduced defects by 25%
- Collaborated with cross-functional teams to develop and implement corrective action plans for underperforming suppliers
- Analyzed supplier performance data using tools like SPC and FMEA to identify areas for improvement
Avoid using weak or passive language that doesn't convey the full extent of your contributions, such as:
- Responsible for supplier quality
- Worked with suppliers
- Helped with data analysis
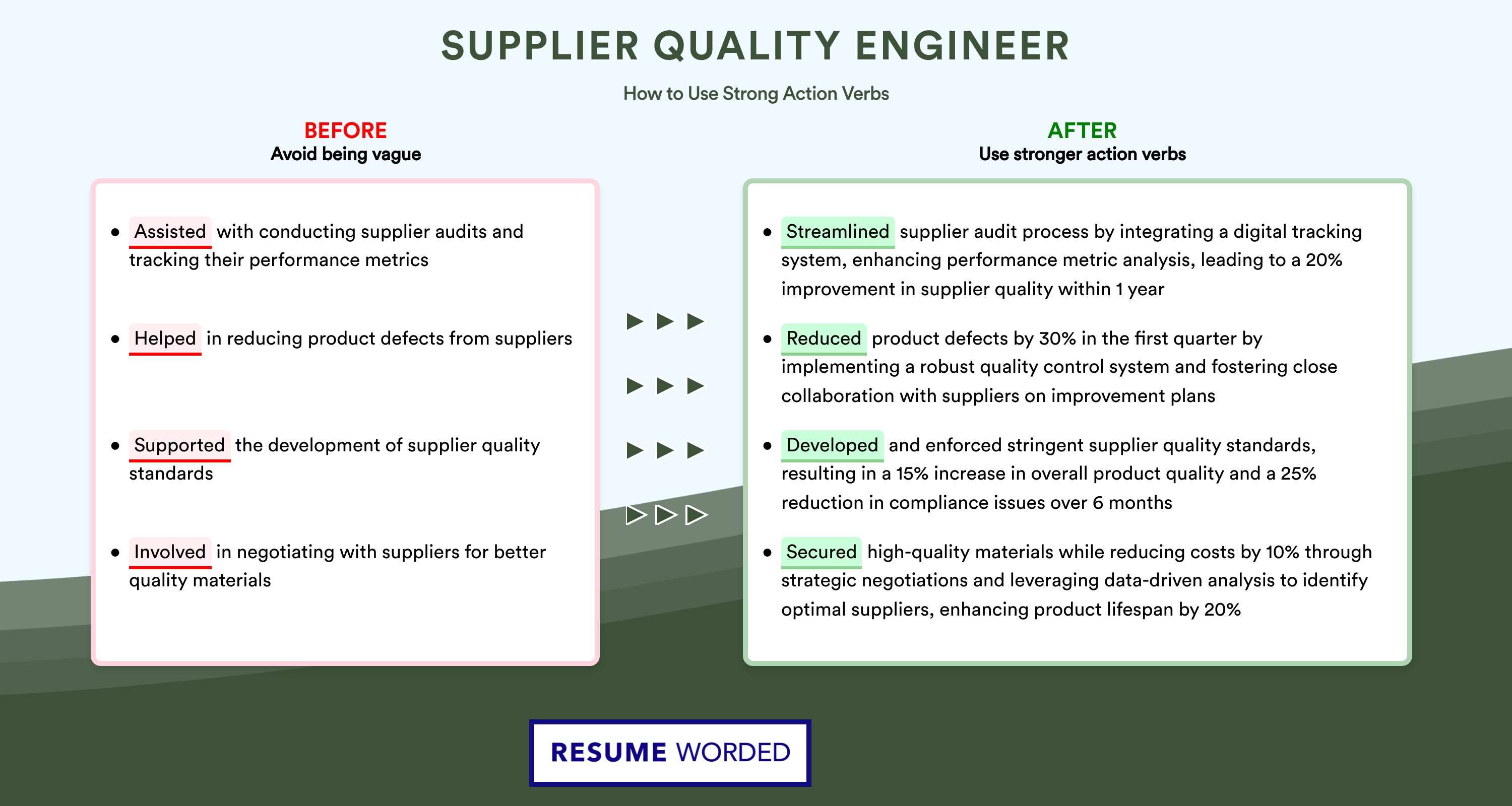
3. Quantify your achievements with metrics
Whenever possible, use specific metrics and numbers to quantify your achievements and show the measurable impact you made in your previous roles. For example:
- Reduced supplier defect rate from 5% to 1.5% within 6 months through implementation of new quality control processes
- Conducted 25+ supplier audits per quarter, resulting in a 20% improvement in overall supplier performance scores
- Developed and implemented a supplier scorecard system that increased on-time delivery rates from 85% to 98%
Achieved $500K in annual cost savings by implementing a supplier quality improvement program that reduced scrap rates by 50% and increased first-pass yield to 99%.
4. Showcase your career growth and promotions
If you've been promoted or taken on increasing levels of responsibility in your previous roles, make sure to highlight that in your work experience section. This shows hiring managers that you've been recognized for your contributions and have the potential to take on more senior roles in the future.
For example:
- Promoted from Supplier Quality Engineer to Senior Supplier Quality Engineer within 2 years based on strong performance and leadership skills
- Assumed leadership of global supplier quality team and successfully implemented a new supplier management system across 5 international sites
By showcasing your career growth and promotions, you'll demonstrate your value as a candidate and make a stronger case for why you should be considered for the role.
Education
The education section of your supplier quality engineer resume should be concise and highlight your relevant degrees and certifications. This section is especially important if you are a recent graduate or if your education is closely related to the position you are applying for.
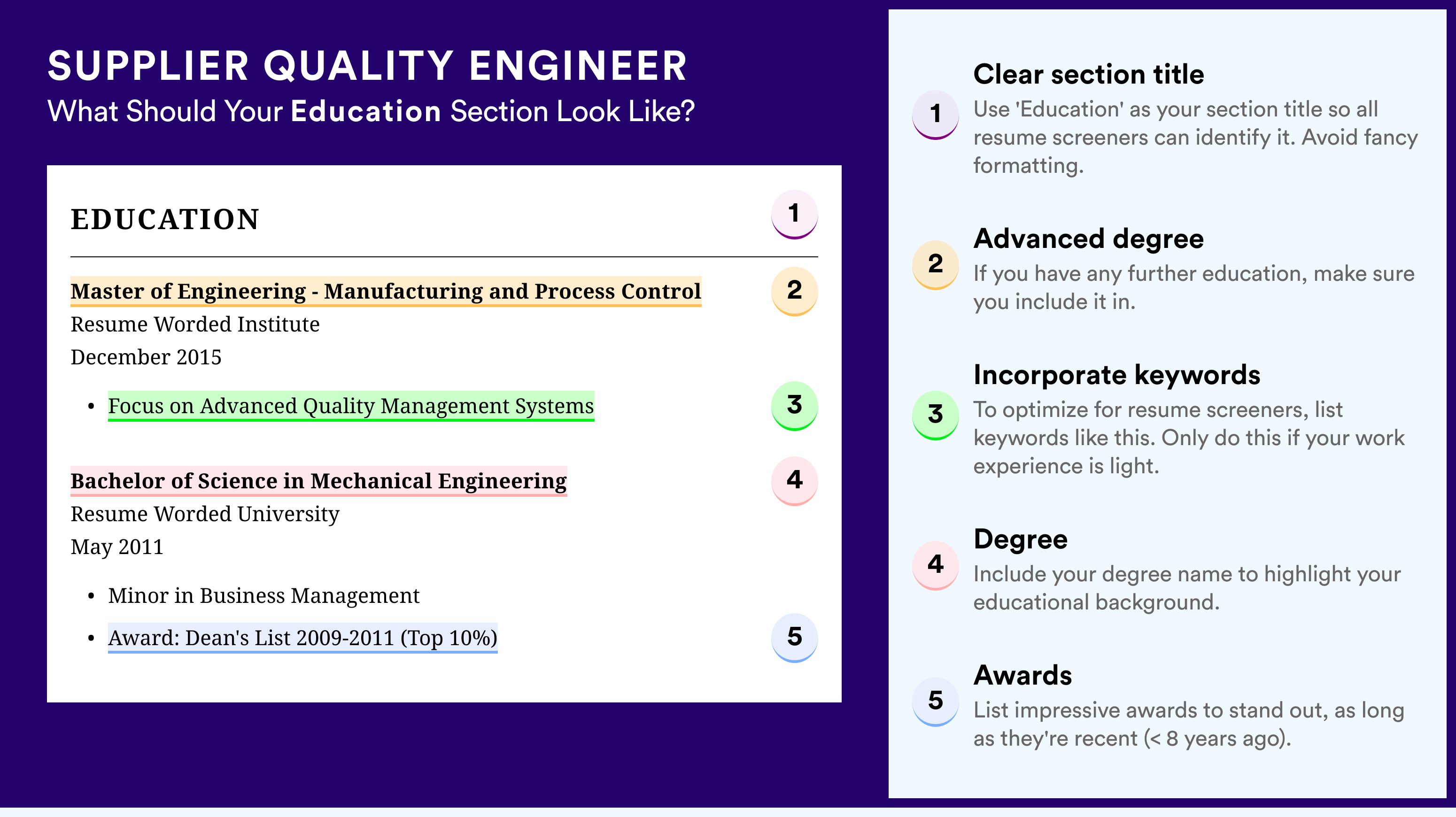
1. List your degrees in reverse chronological order
Start with your most recent degree and work backwards. Include the name of the institution, the degree earned, and the year of graduation.
Master of Science in Quality Engineering, University of Michigan, 2019 Bachelor of Science in Mechanical Engineering, Michigan State University, 2017
If you have multiple degrees, list them separately. Avoid lumping them together like this:
Master of Science in Quality Engineering and Bachelor of Science in Mechanical Engineering, University of Michigan and Michigan State University, 2017-2019
2. Highlight relevant coursework for entry-level positions
If you are a recent graduate or have limited work experience, you can showcase relevant coursework to demonstrate your knowledge and skills. Include a bulleted list of courses that are directly applicable to the supplier quality engineer role.
- Quality Control and Reliability Engineering
- Statistical Process Control
- Supply Chain Management
- Six Sigma Methodologies
Avoid listing general education courses or those not related to the position, such as:
- Introduction to Psychology
- World History
- Creative Writing
3. Include relevant certifications
Certifications demonstrate your expertise and commitment to the field. If you have earned any certifications related to supplier quality engineering, include them in your education section or create a separate section titled "Certifications."
- Certified Quality Engineer (CQE), American Society for Quality (ASQ), 2020
- Lean Six Sigma Green Belt, International Association for Six Sigma Certification (IASSC), 2019
Avoid listing certifications that are not relevant to the position or industry, such as:
- Certified Yoga Instructor
- First Aid and CPR Certification
4. Keep the education section brief for experienced professionals
If you have several years of experience as a supplier quality engineer, your education section should be concise. Include only your highest degree and any relevant certifications.
M.S. in Quality Engineering, Purdue University Certified Quality Engineer (CQE), American Society for Quality (ASQ)
Avoid listing graduation dates, as this can lead to age discrimination. Also, refrain from including details about your education that are no longer relevant, such as:
Bachelor of Science in Mechanical Engineering, University of California, Los Angeles, 1995 Relevant Coursework: Introduction to Thermodynamics, Fluid Mechanics, Heat Transfer GPA: 3.8/4.0
Skills
The skills section of your resume is one of the most important parts, especially for technical roles like Supplier Quality Engineers. Hiring managers and recruiters often scan this section first to quickly assess if you have the right skills and expertise for the job. Here are some key tips to keep in mind when writing your skills section:
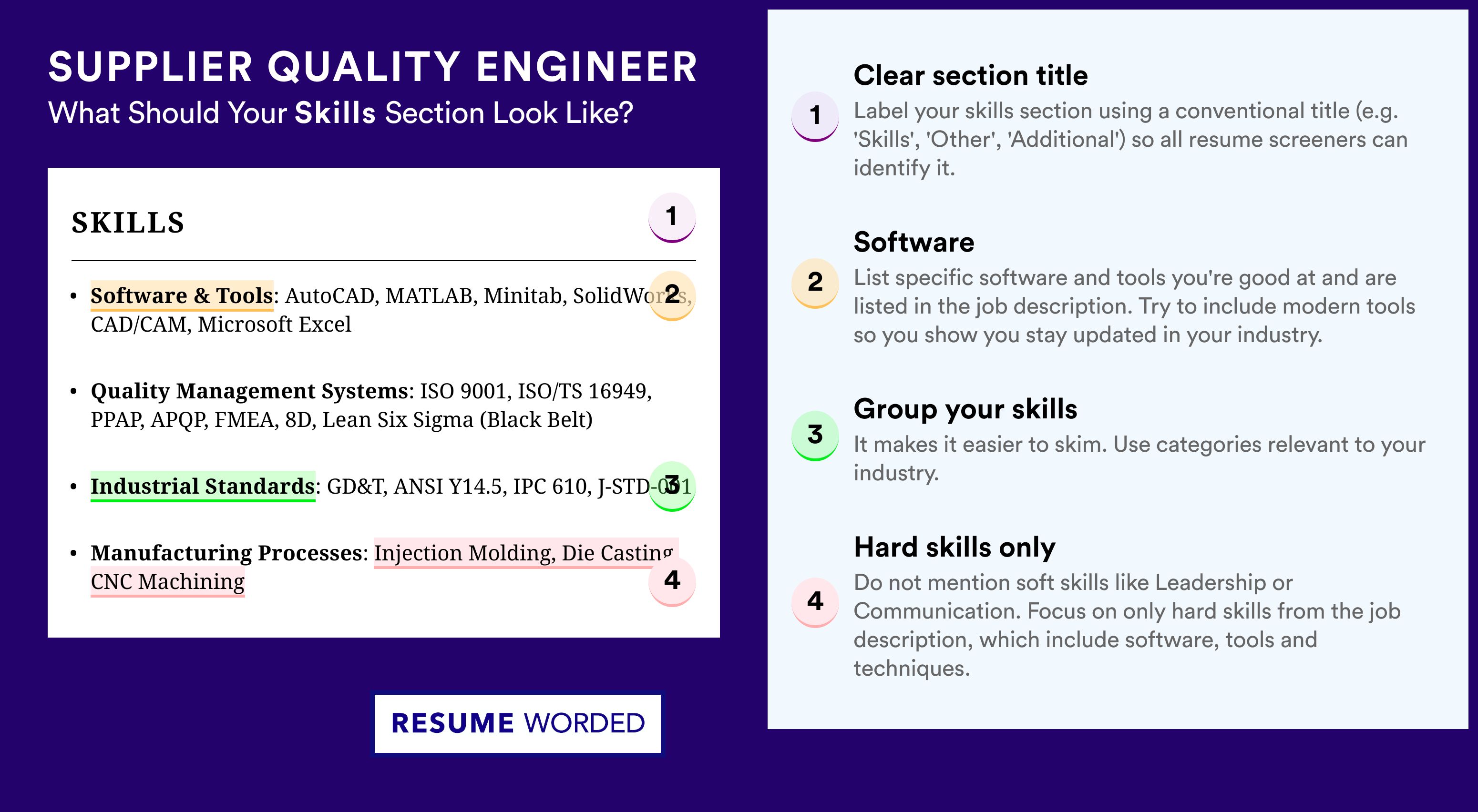

1. Tailor your skills to the job description
Many companies today use Applicant Tracking Systems (ATS) to automatically scan and filter resumes based on the skills and keywords they're looking for. To ensure your resume gets past these filters, carefully review the job description and make sure you include relevant skills and keywords from it in your skills section.
For example, if a Supplier Quality Engineer job description mentions specific skills like ISO 9001, Six Sigma, or APQP, make sure to include them in your skills section (if you have them). This will help demonstrate to both the ATS and the hiring manager that you're a good fit for the role.
2. Focus on hard skills and technical expertise
As a Supplier Quality Engineer, hiring managers will be looking for specific hard skills and technical expertise on your resume, not soft skills. Some examples of key skills to highlight in your skills section include:
- Quality Management Systems : ISO 9001, AS9100, Six Sigma, Lean
- Quality Tools & Techniques : Root Cause Analysis, 8D Problem Solving, Statistical Process Control (SPC), APQP, FMEA
- Regulations & Standards : IATF 16949, OSHA, GMP, FDA 21 CFR
- Software & Tools : Minitab, SAP QM, MS Office
Avoid listing soft skills like "Communication", "Teamwork" or "Leadership". While these are important skills, they are overused and don't distinguish you. Instead, demonstrate these through your bullet points in your work experience section.
3. Organize and format your skills section for easy scanning
Hiring managers and recruiters only spend a few seconds scanning each resume initially. Make sure your skills section is well-organized and easy to read at a glance. Some tips:
- Group related skills into categories like "Quality Management Systems", "Software & Tools", etc.
- Use columns or bullets to list skills, not paragraphs
- Be concise - no need to write full sentences
- Use a simple, professional font and font size
Skills: Problem solving, detail-oriented, ISO 9001, six sigma green belt, 8D, Minitab, FMEA, regulatory compliance, GMP, teamwork, leadership, strong communication, APQP, technical writing, SAP QM, Lean, Kaizen events, stakeholder management
The example above is poorly formatted and contains a mix of hard and soft skills, making it hard to scan and less impactful. Instead, try something like:
SKILLS Quality Management Systems : ISO 9001, Six Sigma Green Belt, IATF 16949, Lean Quality Tools & Techniques : FMEA, SPC, 8D Problem Solving, Root Cause Analysis, APQP Software : Minitab, SAP QM, MS Office Regulations & Standards : GMP, FDA 21 CFR Part 820, OSHA
Skills For Supplier Quality Engineer Resumes
Here are examples of popular skills from Supplier Quality Engineer job descriptions that you can include on your resume.
- Continuous Improvement
- Supplier Quality
- Supplier Evaluation
- Advanced Product Quality Planning (APQP)
- Supplier Audits
- Supplier Development
- Failure Mode and Effects Analysis (FMEA)
- Statistical Process Control (SPC)
- Root Cause Analysis
Skills Word Cloud For Supplier Quality Engineer Resumes
This word cloud highlights the important keywords that appear on Supplier Quality Engineer job descriptions and resumes. The bigger the word, the more frequently it appears on job postings, and the more likely you should include it in your resume.
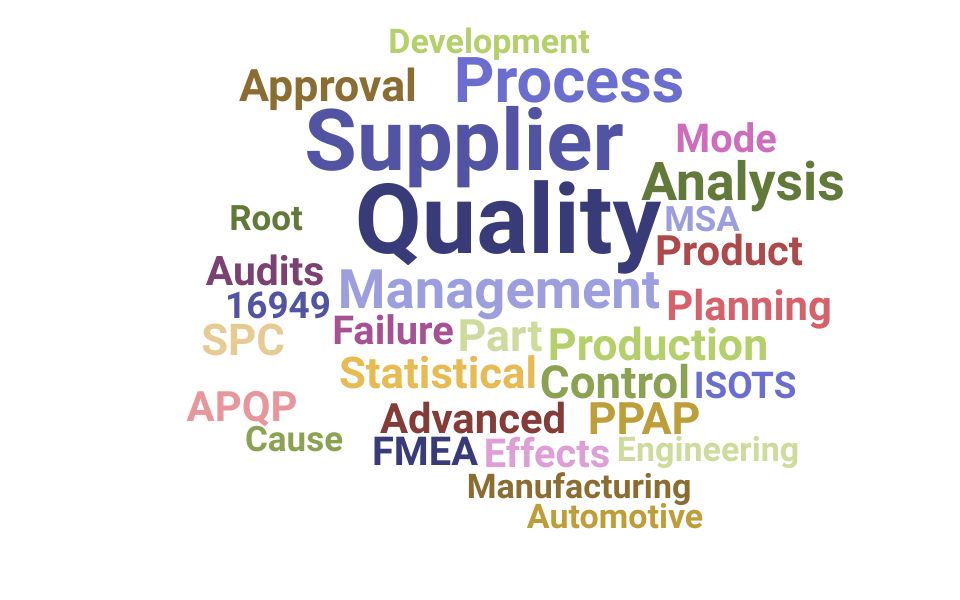
How to use these skills?
Similar resume templates, audio engineer.
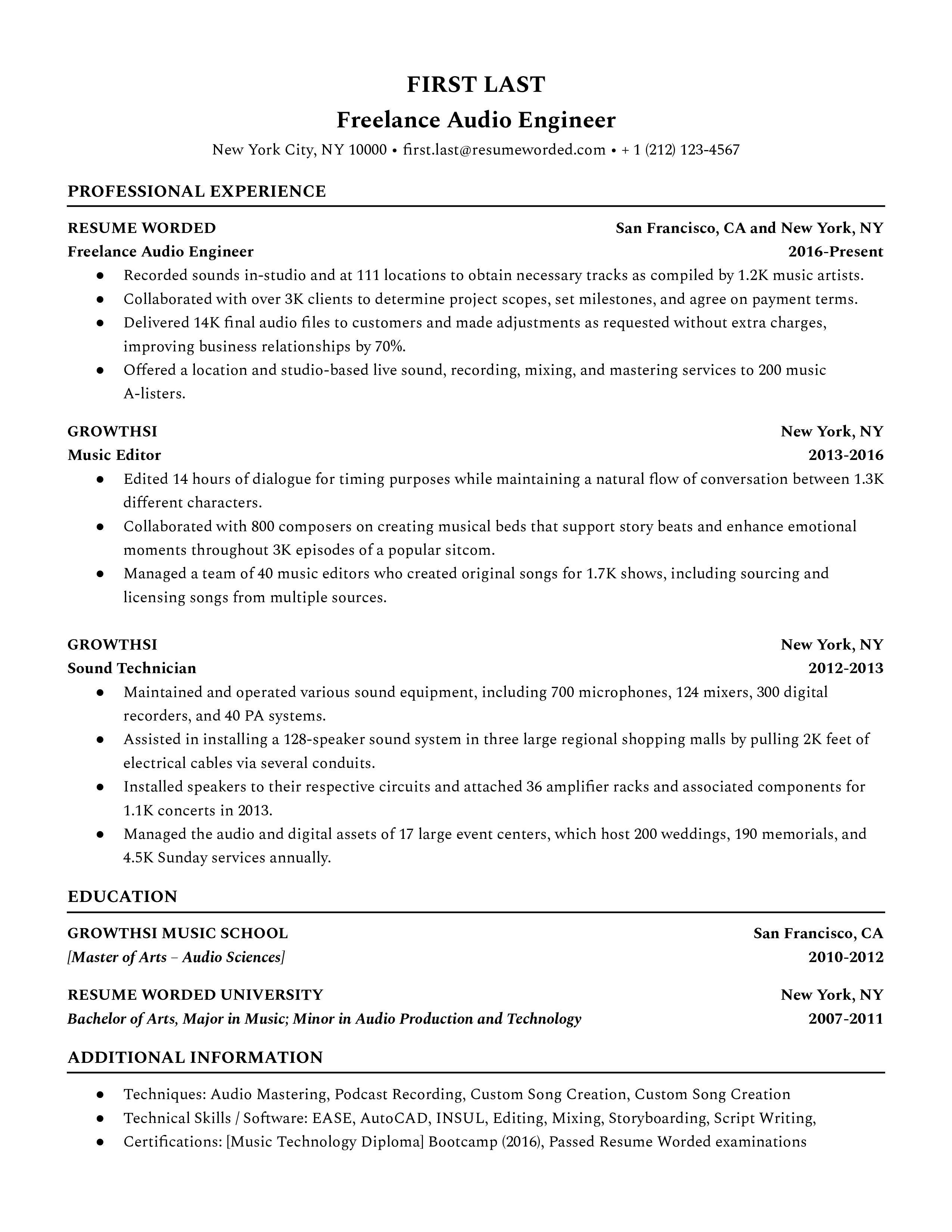
Automation Engineer
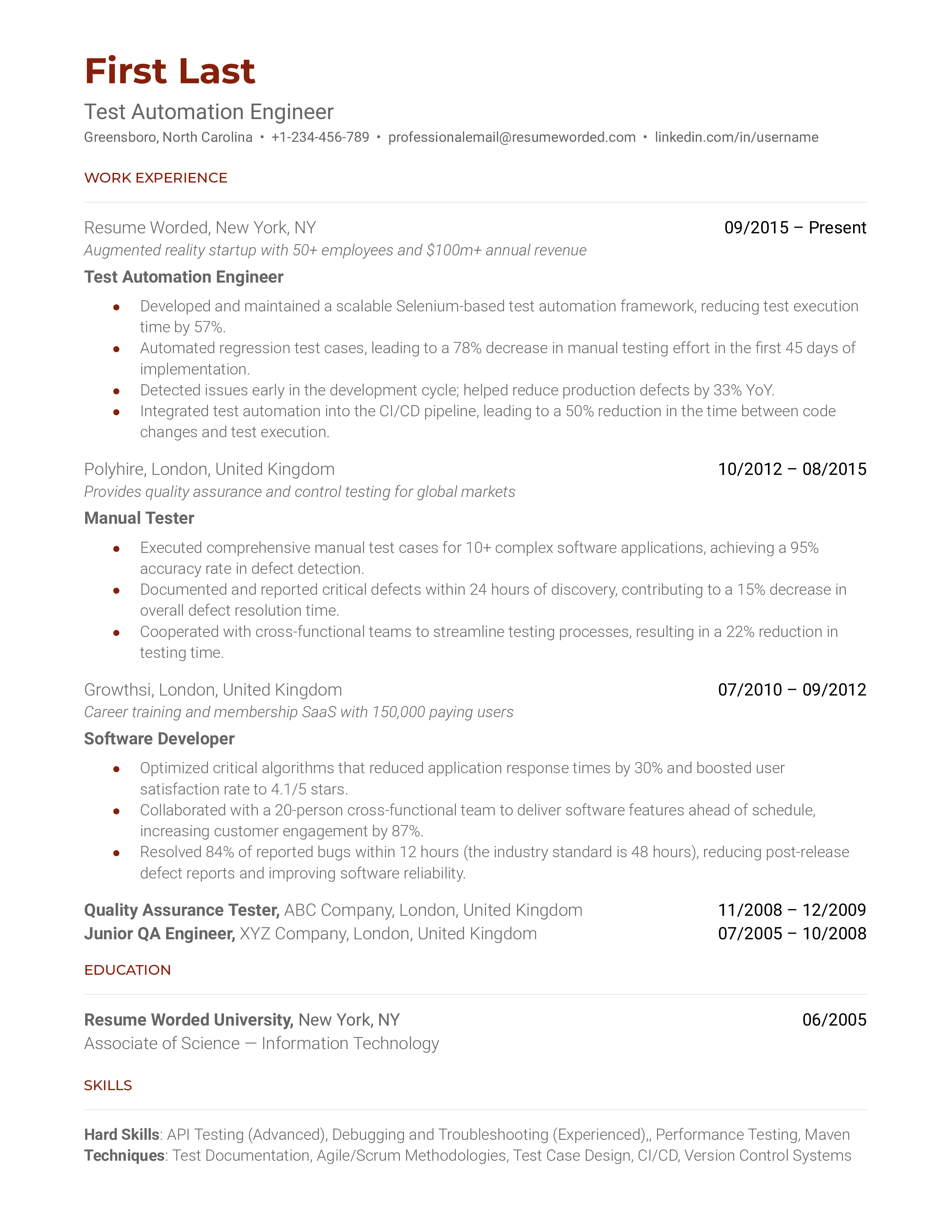
Director of Software Engineering
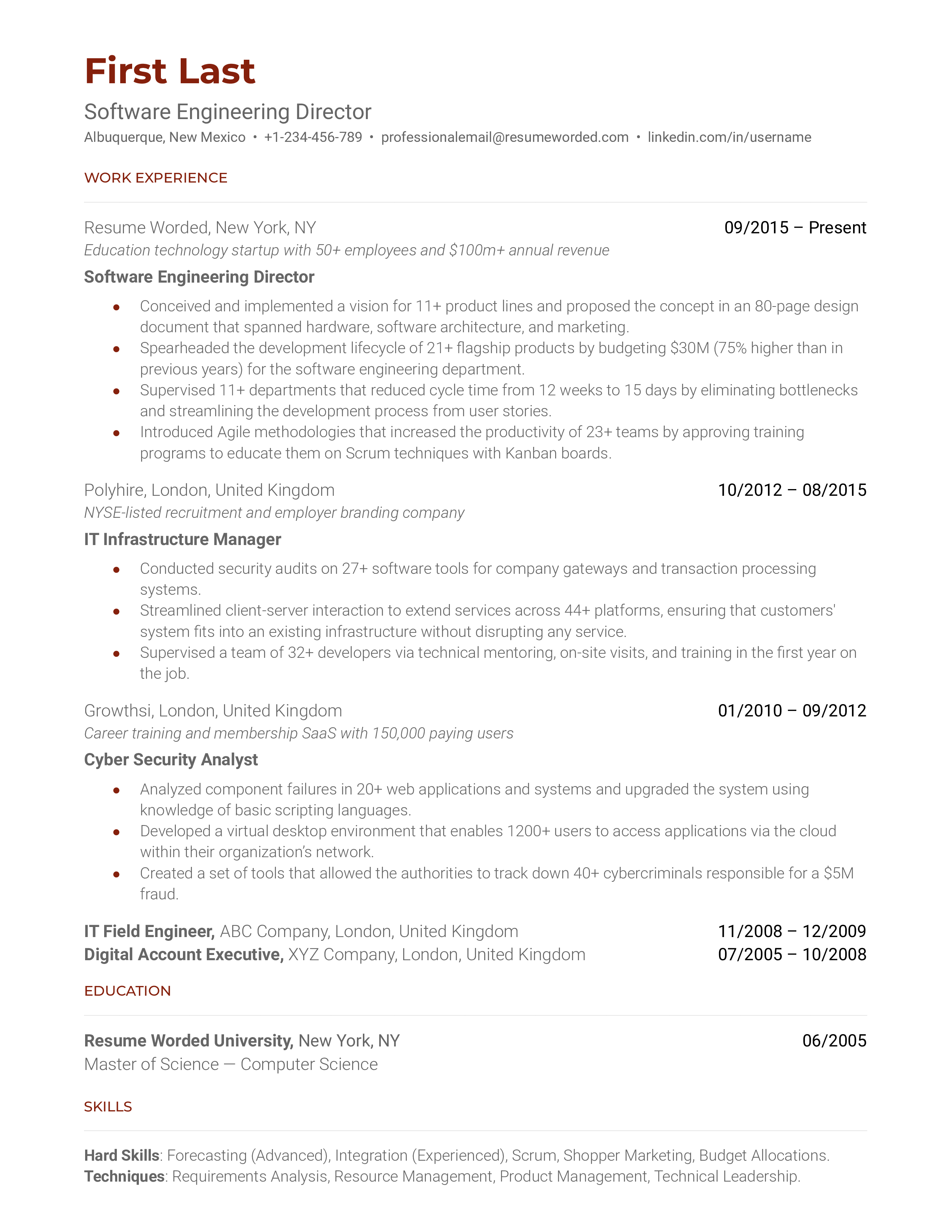
- Director of Information Technology Resume Guide
- Engineering Manager Resume Guide
- Full Stack Developer Resume Guide
- Network Administrator Resume Guide
- SQL Developer Resume Guide
Resume Guide: Detailed Insights From Recruiters
- Quality Engineer Resume Guide & Examples for 2022
Improve your Supplier Quality Engineer resume, instantly.
Use our free resume checker to get expert feedback on your resume. You will:
• Get a resume score compared to other Supplier Quality Engineer resumes in your industry.
• Fix all your resume's mistakes.
• Find the Supplier Quality Engineer skills your resume is missing.
• Get rid of hidden red flags the hiring managers and resume screeners look for.
It's instant, free and trusted by 1+ million job seekers globally. Get a better resume, guaranteed .
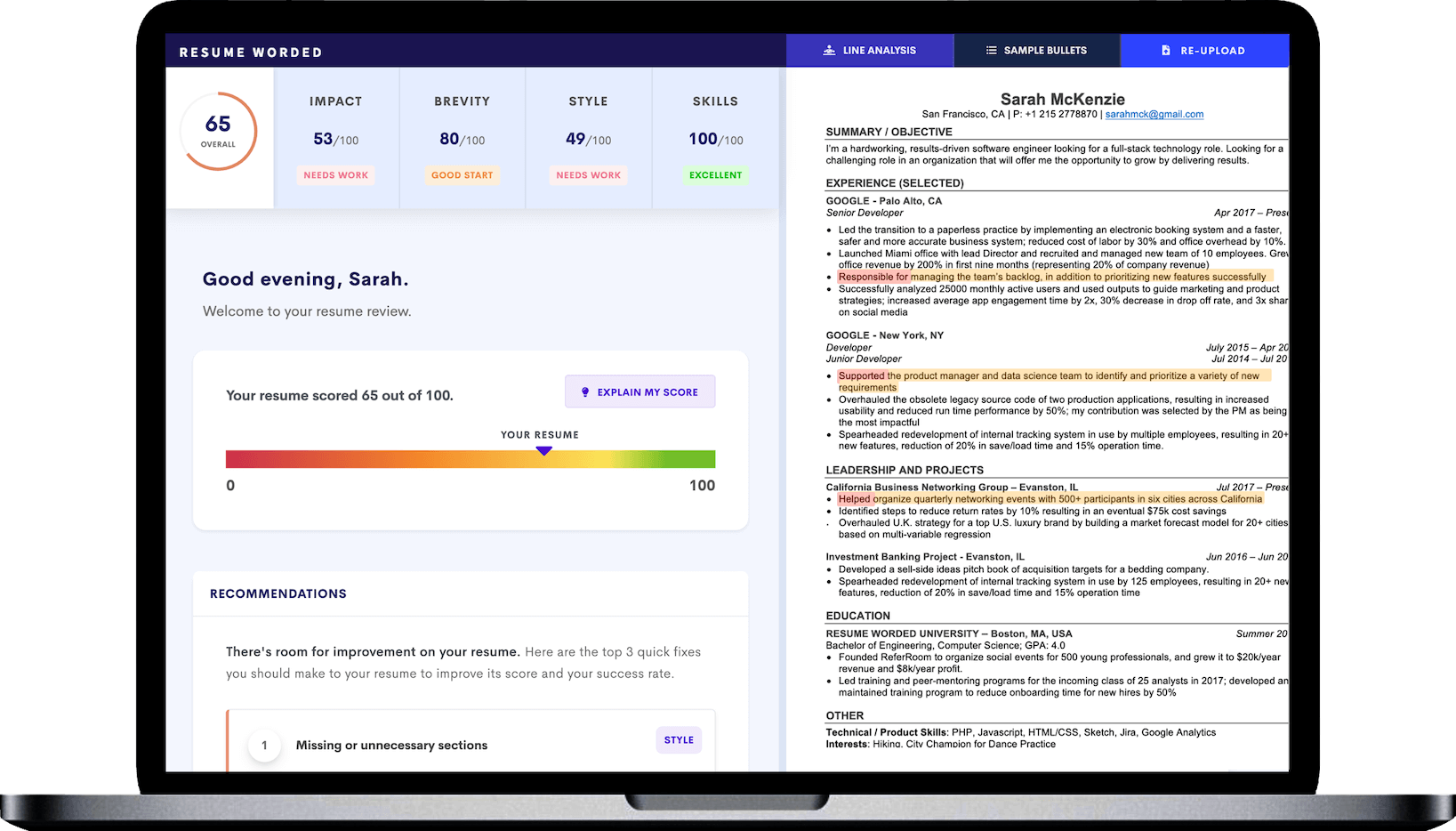
Supplier Quality Engineer Resumes
- Template #1: Supplier Quality Engineer
- Template #2: Supplier Quality Engineer
- Template #3: Supplier Quality Engineer
- Template #4: Quality Assurance Engineer
- Template #5: Procurement Engineer
- Template #6: Quality Control Engineer
- Template #7: Quality Systems Engineer
- Skills for Supplier Quality Engineer Resumes
- Free Supplier Quality Engineer Resume Review
- Other Engineering Resumes
- Supplier Quality Engineer Interview Guide
- Supplier Quality Engineer Sample Cover Letters
- Alternative Careers to a Supplier Quality Engineer
- All Resumes
- Resume Action Verbs
Download this PDF template.
Creating an account is free and takes five seconds. you'll get access to the pdf version of this resume template., choose an option..
- Have an account? Sign in
E-mail Please enter a valid email address This email address hasn't been signed up yet, or it has already been signed up with Facebook or Google login.
Password Show Your password needs to be between 6 and 50 characters long, and must contain at least 1 letter and 1 number. It looks like your password is incorrect.
Remember me
Forgot your password?
Sign up to get access to Resume Worded's Career Coaching platform in less than 2 minutes
Name Please enter your name correctly
E-mail Remember to use a real email address that you have access to. You will need to confirm your email address before you get access to our features, so please enter it correctly. Please enter a valid email address, or another email address to sign up. We unfortunately can't accept that email domain right now. This email address has already been taken, or you've already signed up via Google or Facebook login. We currently are experiencing a very high server load so Email signup is currently disabled for the next 24 hours. Please sign up with Google or Facebook to continue! We apologize for the inconvenience!
Password Show Your password needs to be between 6 and 50 characters long, and must contain at least 1 letter and 1 number.
Receive resume templates, real resume samples, and updates monthly via email
By continuing, you agree to our Terms and Conditions and Privacy Policy .
Lost your password? Please enter the email address you used when you signed up. We'll send you a link to create a new password.
E-mail This email address either hasn't been signed up yet, or you signed up with Facebook or Google. This email address doesn't look valid.
Back to log-in
These professional templates are optimized to beat resume screeners (i.e. the Applicant Tracking System). You can download the templates in Word, Google Docs, or PDF. For free (limited time).
access samples from top resumes, get inspired by real bullet points that helped candidates get into top companies., get a resume score., find out how effective your resume really is. you'll get access to our confidential resume review tool which will tell you how recruiters see your resume..
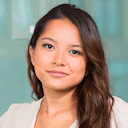
Writing an effective resume has never been easier .
Upgrade to resume worded pro to unlock your full resume review., get this resume template (+ 6 others), plus proven bullet points., for a small one-time fee, you'll get everything you need to write a winning resume in your industry., here's what you'll get:.
- 📄 Get the editable resume template in Google Docs + Word . Plus, you'll also get all 6 other templates .
- ✍️ Get sample bullet points that worked for others in your industry . Copy proven lines and tailor them to your resume.
- 🎯 Optimized to pass all resume screeners (i.e. ATS) . All templates have been professionally designed by recruiters and 100% readable by ATS.
Buy now. Instant delivery via email.
instant access. one-time only., what's your email address.

I had a clear uptick in responses after using your template. I got many compliments on it from senior hiring staff, and my resume scored way higher when I ran it through ATS resume scanners because it was more readable. Thank you!
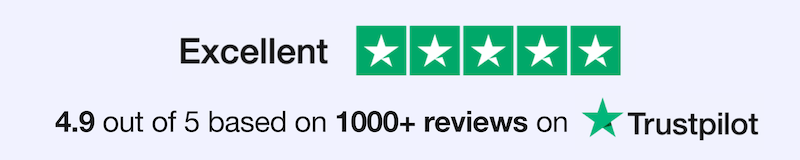
Thank you for the checklist! I realized I was making so many mistakes on my resume that I've now fixed. I'm much more confident in my resume now.
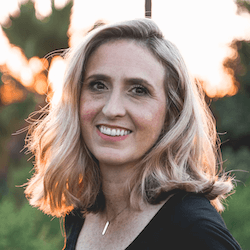
Resume Builder
- Resume Experts
- Search Jobs
- Search for Talent
- Employer Branding
- Outplacement
- Resume Samples
- Supply Chain
Supplier Quality Engineer Resume Samples
The guide to resume tailoring.
Guide the recruiter to the conclusion that you are the best candidate for the supplier quality engineer job. It’s actually very simple. Tailor your resume by picking relevant responsibilities from the examples below and then add your accomplishments. This way, you can position yourself in the best way to get hired.
Craft your perfect resume by picking job responsibilities written by professional recruiters
Pick from the thousands of curated job responsibilities used by the leading companies, tailor your resume & cover letter with wording that best fits for each job you apply.
Create a Resume in Minutes with Professional Resume Templates
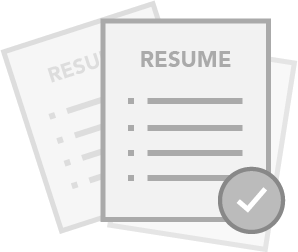
- Supporting and developing suppliers in establishing improvement programs, verifying implementation of quality improvement programs at suppliers
- Work with suppliers to continuously improve performance, implement robust process controls and develop quality assurance plans
- Create, maintain and improve Integrated Management System (IMS) procedures related to supplier improvement programs
- Assist supplier quality manager with supplier improvement process and/or development activities
- Set performance improvement goals with problem/targeted suppliers and work with them to ensure improvement goals are met
- Participates in the Development of Suppliers by means of Training, Consulting and providing Suggestions to improve their Performance
- Assist development and management of Supplier Development/ Supplier Quality Engineering methodology in multiple sites within region
- Manage progress plan with low-performance suppliers, in the development phase, in collaboration with the commodity buyer and supplier development
- Support the Quality Manager to monitor and report on supplier product quality and performance
- Improve, monitor, and report supplier’s performance (cost, quality and timing)
- Manage action plans with suppliers in case of deviations, in the development phase
- Manage progress plan with low-performance suppliers in collaboration with the commodity buyer
- Assist in managing complex and potential high risk supplier situations related to part/process development – Launch
- Manage progress plan with low-performance suppliers in collaboration with the commodity and the program buyer
- Assists in the development of Global SQE improvement initiatives. Helps drive continuous improvement
- Perform and/or participate in source qualification by performing quality management system surveys and special process surveys
- Manages quality conformity of supplies via active monitoring of the supplier performance and driving the incident and complaint resolution
- Collaborate with suppliers in contemporary quality assurance processes and procedures to facilitate continuous improvement of supplier and product performance
- Perform data analysis and issue reports on supplier performance to ensure suppliers meet and maintain expected quality levels
- Assists in developing fabrication/build processes and standards
- Also performs similar work-related duties as assigned
- Good background/knowledge in Quality/Supplier Quality, familiar with APQP/Supplier Quality core process and tools
- Possess strong knowledge of TS16949 quality management system and quality control techniques
- Prior experience as a quality system auditor or SQE highly desired; additional experience in Quality, Purchasing and Manufacturing Operations is desirable
- Knowledge of ISO Quality System Standards and FDA Quality System Regulation is desirable
- Proficient working knowledge of quality systems and tools for supplier interaction (process capability, FMEA, DOE, etc.)
- Demonstrated record of project accomplishments, knowledge of quality management systems, knowledge of organized methods to make systems predictable
- Good data mining skills, strong data driven decision making capability
- Basic AIAG (APQP, PPAP, FMEA, MSA, and SPC) or quality related system knowledge
- Knowledgeable in SAP Quality Management, Oracle Data Warehouse, Mini-Tab, Query tools such as Business Objects, web-based systems, and MS Excel (power user)
- Good Knowledge of industry standard quality tools and processes
15 Supplier Quality Engineer resume templates
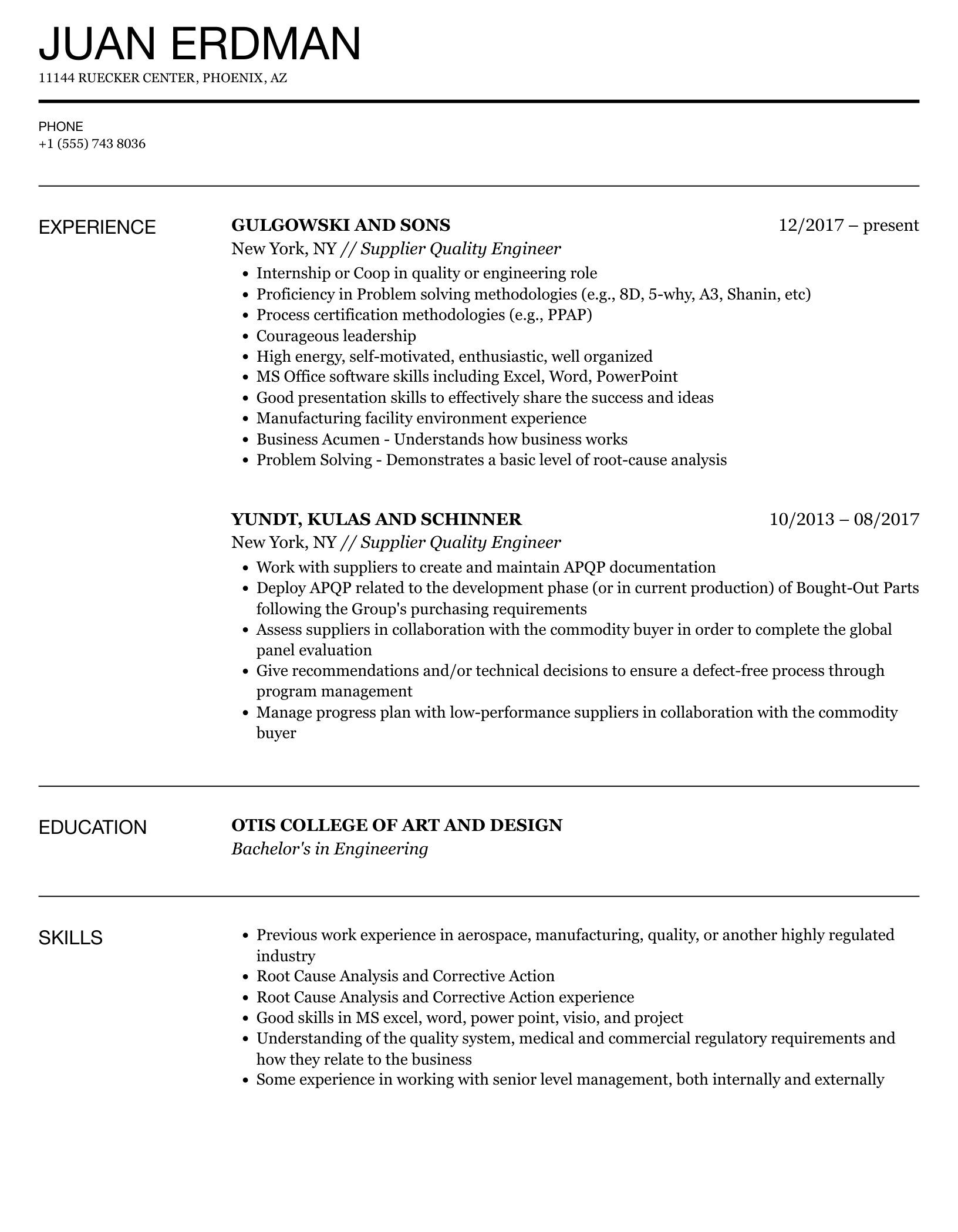
Read our complete resume writing guides
How to tailor your resume, how to make a resume, how to mention achievements, work experience in resume, 50+ skills to put on a resume, how and why put hobbies, top 22 fonts for your resume, 50 best resume tips, 200+ action words to use, internship resume, killer resume summary, write a resume objective, what to put on a resume, how long should a resume be, the best resume format, how to list education, cv vs. resume: the difference, include contact information, resume format pdf vs word, how to write a student resume, supplier quality engineer resume examples & samples.
- Monitor and track supplied product nonconformance trends
- Strive to achieve zero defect via preventive quality initiatives
- Monitor and evaluate supplier quality performance to drive continuous improvement
- Responsible for effective facilitation of the nonconforming product resolution (NCR) process
- Support material review and disposition making decision processes
- Manage, track and trend supplier corrective action processes
- Lead the continuous development of supplier quality process capabilities
Supplier Quality Engineer Specialist Resume Examples & Samples
- Evaluate and authorize manufacturing processes and packaging related to the CKD logistic process, according to the corporate guidelines
- Apply methods like DOE, 6 Sigma, CEP, etc. to analyze the root causes of complaints. Define technical factors to be used in the Warranty Chargeback initiatives
- Influence the development of new projects and technical concepts to achieve the continuous improvement of our product in the market
- 5 -7 years related experience
- Knowledge of inspection techniques and methods (like DOE, 6 Sigma, CEP, etc.)
- Ability to manage resources such as scheduling, travel, report distribution, task completion
- Travel / Supplier visits will exceed 30%
- Some weekend travel depending on scheduling / problem issues
Global Supplier Quality Engineer Resume Examples & Samples
- Provide supplier qualifications, material issue resolution, drive supplier corrective actions
- Establish and maintain acceptable quality standards for raw materials
- Insure consistency of on-going product receipts with original samples/standards from suppliers
- Log and follow-up on quality complaints as reported by customers
- Provide necessary quality reporting for effective supplier selection and product assignments
- Track, analyze, and report on quality performance and trends
- BOM/component validation and maintenance of approved supplier/parts lists
- Drive quality with assigned suppliers and accelerate improvements in supplier quality and delivery of value
- Maintain product specification and performance assurance through conformance testing; including measurements, wash testing, performance testing, etc
- Drive supplier selection through qualification process
- Drive corrective and preventive action program, from initiation to resolution of items; collect and analyze data to track the improvements
- Develop positive relationships and work closely with Purchasing Departments (Domestic and International) to manage and implement supplier engineering changes, and part introductions
- Deliver results as measured by key metrics such as defect rates, total supplier cost and corrective action closure
- Drive improvement through supplier auditing and supplier scorecards
- Understand and drive Lean supply chain internally and with suppliers; ensure that all purchased part documentation and products meet quality system requirements
- Initiate and drive scrap-reduction and cost savings project teams
- Develop and implement plans of action/systems to continually improve the quality of raw and finished goods
- Monitor and communicate as needed all supplier quality data and metrics
- Document and maintain Quality procedures
- Bachelor’s Degree in business or related field or equivalent experience
- 3-5 years supplier quality experience
- Strong data analysis, problem solving and project management skills
- Must be comfortable with rapidly changing priorities
- Experience in a Lean Manufacturing environment is highly desirable
- Must be detail oriented and possess excellent time management and organizational skills
- Excellent interpersonal skills to interact with diverse individuals and groups at all levels
- Must be able to work independently in a fast paced, rapidly changing environment
- Thorough understanding of MS Office applications including Word and Outlook, and strong skills in Excel
- Ability to read product specifications
- Flexible, adaptable with the ability to work under pressure to meet deadlines in a fast paced office environment
- Manufacturing and Office environments – utilizing an office desk and computer – sitting, reading, listening and speaking. Occasional walking, standing, reaching and bending
- Strong sensory skills, such as good eyesight, good hearing, and dexterity
- Ability to operate office equipment, including computers, copiers, fax machines, and phone
- Managing all supplier related quality issues for Caterpillar’s Victoria facility
- Initiating supplier driven containment activity to ensure production schedules are not impacted
- Reviewing and approving 8D Corrective Action Plans
- Maintaining accountability with the suppliers to establish containment plans related to quality discrepancies
- Ensuring supplier develops corrective action plans to enable operations to continue with no disruption
- Working with other purchasing teams to audit 8D corrective actions at a supplier’s site
- Bachelor’s level degree, preferably in a technical field
- Minimum of two years of job related experience
- Engineering or manufacturing background, fabrication experience preferredGood teamwork skills are required in order to develop a cooperative working relationship with others inside and outside of Caterpillar
- Demonstrated ability to manage multiple projects and details all at the same time
- Knowledge of assembly processes and purchasing systems
- Knowledge of steel fabrications
- Knowledge of Caterpillar drawings and specifications
- By addressing these challenges, you’ll impact key quality goals, including
- 8D Corrective Action Process
- Product Production
- Pre-Service or V.E.H.R (0 Hour)
- Warranty accuracy
- Cost savings
- Process quality
- The position requires an engineering or manufacturing background plus familiarity with manufacturing processes used to produce components and assemblies for Caterpillar Products
- Knowledge of shop operations and maintenance procedures is required
- Bachelor’s degree – or equivalent experience, preferably in engineering
- A minimum two years of job-related experience or the equivalent education is required
- Solid ability to use and demonstrate statistical and problem solving tools is required
- Minimum 3-5 years of job-related experience
- Work with suppliers to ensure that robust process controls are in place to preventnonconformities, to continuously monitor supplier’s key manufacturing processes
- Quality management system for improvement opportunities
- Assist suppliers with Advanced Product Quality Planning (APQP) activities to ensure production readiness for New Product Introduction
- Responsible for the supplier’s processes from design concept to the end of product life
- To ensure that suppliers are able to meet corporate and business unit supplier performance requirements
- Ensures all relevant requirements and related changes are thoroughly documented
- Audits process control implementation and effectiveness
- Supports Caterpillar 6 Sigma initiatives with suppliers
- The position manages the completion of their own work assignments and coordinates work with others
- Capable of using and demonstrating statistical and problem solving tools
- Engineering or manufacturing background plus familiarity with manufacturing processes
- Negotiaton level of English
- 3-5 years experience in similar position
- Good interpersonal communication, analytical, leadership and project management
- As a Supplier Development Engineer - Site, you will provide technical expertise and leadership to Product Sourcing Teams for evaluation and development of new and existing suppliers worldwide, while maximizing Quality, Cost, Logistics, Delivery, and Management at the supply base
- To work with suppliers to assure proper process control standards are in place and continuously monitor key manufacturing processes for improvement opportunities
- Ensure suppliers have adequate people, training, tooling, fix Turing, and equipment
- Monitor suppliers’ adherence to Process Change Notification on a timely and cost effective basis as well as to develop the supply base to full fill the total requirements from Caterpillar System implementation
- Evaluate and develop new supplier’s technological capability to meet requirements for Caterpillar Inc. Supplier Excellence Program
- Bachelor’s degree in any engineering field
- Minimum 3 years’ experience in supplier quality or quality assurance in automotive parts industry or related business
- Basic Understanding in Core Tools such as PPAP, APQP, 8D Problem Solving
- Strong in negotiation skills
- Good command in English and proficient in computer
- Managing supplier related quality issues relating to Product Production, Pre-Service or V.E.H.R (0 Hour) and Warranty (Processing and component returns)
- Ensuring supplier is developing corrective action plans to enable operations to continue with minimum disruption
- Engineering or manufacturing background plus familiarity with manufacturing processes used to produce components and assemblies for Caterpillar Products
- Knowledge of shop operations and maintenance procedures
- Caterpillar Production System Black Belt certification
- To support sourcing team to develop suppliers to support American and Europe programs, responsible for the development/assessment and maintenance of the quality system & procedures
- Play a strong liaison role between Chinese/Asian suppliers and American and Europe divisions to ensure program is successfully launched
- Perform New Supplier Assessment base on Magna requirement
- Maintain Flawless Launch Tracking Matrix, Open Issues Tracker to be rolling updated
- Maintain problem solving tracking documents like 8D report, and read across to other projects
- Team player, be supportive and cooperative to other team member
- Periodically audit the existing supplier performance & continue to improve the product quality to drive for continuous improvement in quality/cost savings program
- Working closely with local and global team, communicate and provide technical support to solving the quality issues
- Other assignment by top management
- BS or above of mechanical engineering or any other related technical disciplines
- 8-10 years working experience in automotive industry and at least 5 years experience in supplier quality management
- Familiar related injection molding process
- Familiar second process for surface treatment, like Chrome Plating, Paint Coating
- Comprehensive knowledge of Quality Control management standards and procedures including Total Quality Management, ISO/TS16949 etc
- Proficient in quality tools such as MSA, SPC, FMEA, PPAP, DOE etc
- Good knowledge of Lean Manufacturing or TPS
- Good problem solving skills, familiar 5-why, 8D method
- Self Motivated, result driven /goal oriented with customer focus and sense of urgency
- Strong project management skills, time management skills, influencing and communication skills are required
- Good computer skill, and sound presentation skills at all levels. Be able to read blue print, understand the GD&T and be able to propose measurement method
- Good English skills (oral & writing communications)
- Incorporate customer requirements into Supplier APQP requirements
- Meets with program supply base and rolls out quality expectations, requirements, and timing
- Schedule Supplier APQP meetings to present issues from Supplier APQP document review
- Schedule and participate in Supplier visits to review APQP progress and launch readiness
- Track status in matrix format for each Supplier. Report status to program team
- Assist in preparing and presenting prototype requirements to Suppliers
- Review incoming material and documentation from Suppliers for compliance to specification requirements
- Utilize chargeback database for incoming prototype issues
- Request corrective action from Suppliers related to prototype issues. Follow to closure
- Participate in Special Characteristics Agreement reviews with Supplier. Provide input for requirements
- Review Supplier DVP& R test results for compliance
- Provide pre-production documentation for components received
- Review production PPAP packages and sign for approval
- Schedule and conduct Supplier visits for initial PPAPs
- Schedule and conduct Supplier visits for ongoing Engineering Change PPAP reviews
- Schedule and participate in Appearance Approval Reviews. Collects open issues, documents and tracks resolutions
- Participate in TASP initiation, distribution, and closure
- Provide support for Division by verifying and closing Supplier corrective action issues
- Maintaining good supplier quality records and informs the program team of timely execution
- Use e- business tools (Access, Excel, E-mail, Lotus Notes, Power Point, etc.) to communicate with program team and customers
- Applies academic principles and maintains up to date awareness of PPAP, APQP, GD&T, and statistical based tools
- Utilize supplier auditing methods to assess potential Suppliers
- Ensure incoming purchased components are successfully launched by suppliers and their quality expectations maintained throughout production as to meet or surpass quality levels according to design and customer requirements. (Use APQP process participation and open issues list as tools to document and resolve open issues)
- Utilize/develop a Supplier Quality Manual (SQM) as the key guide with Tier 2 launch and development activities. Maintain and improve the SQM as required
- Communicate to suppliers the SQM and PPAP(Production Part Approval Process) requirements to meet successful supplier launces, and in turn, compliance with the Decostar Control Plan and PPAP requirements of Decostar customers
- Review and approve supplier PPAP’s and trial runs & initiate plans for corrective action as required
- Conduct supplier quality systems surveys to ISO/TS 16949 requirements
- Investigate all assembly component issues, both in receiving or production, and root cause against supplier’s latest PPAP and design documentation. Sort materials as required and implement corrective actions via brainstorming sessions
- Communicate with suppliers and internal customers on product quality concerns and all initiate follow up activities on non-conforming item. Document and recover all cost impacts to Decostar
- Visit supplier’s to address quality spills during production and ensure effective corrective actions are requested and implemented throughout the process flow
- Weekly/monthly tracking, updating, and reporting of the supplier performance reports for each subcomponent suppliers and their summary via the LAN/e-systems. Presents these reports to management as required
- Lead programs and activities to ensure meeting of departmental performance objectives
- Perform job duties within the guidelines of the Decostar Supplier Quality Manual and ISO/TS16949 procedures
- Establish boundary samples/visual aids for all affected departments to help define and maintain consistent supplier quality standards
- Perform other duties as directed
- Minimum Associate’s Degree required (Bachelor’s degree or CQE preferred). Six years work related experience may be substituted in lieu of degree
- Must possess good working knowledge of Microsoft Excel (spreadsheet), Word (word processing), and preference to Access (data basing)
- Knowledge of AIAG core tools such as FMEA, Control Plan, SPC, MSA, etc. is required
- Proficient in problem solving and root cause analysis
- Minimum two years’ experience in quality assurance required with supervisory functions
- Blue print reading and GD&T is required
- Prior internal auditing or lead auditing to TS-16949 experience is required. Exposure to multiple OEM specifications, standards and quality systems is required
- Ability to effectively communicate with all levels of personnel is required
- Must be computer literate in the Windows environment
- Ability to travel within and outside of the U.S. is required
- University degree in a technical subject
- 2 +years experience in Quality or Manufacturing
- Good knowledge of the English language, both verbally and in writing
- Good communication and presentation skills
- Independent, self-confident and well organised with analytical mind
- Set up and maintain supplier quality assurance processes, methods and tools
- Define and develop training path and qualification criteria for quality inspectors
- Provide quality related training to quality inspectors
- Be responsible for the related supplier quality assurance activities in NPI/TPI
- Analyze and solve supplier quality related problems to secure the production and customer deliveries
- Coordinate with related units on disposal of faulty parts reported from incoming inspection and faulty parts reported from production or customer returns that related to supplier quality
- Carry out process review/audit in supplier sites and follow up CAP/PAP
- Monitor quality performance for assigned material and related processes
- Initiate and/or take part in the improvement work
- 2 +years experience in Quality or Manufacturing. Mechanical is preferred
Supplier Quality Engineer Production Specialist Resume Examples & Samples
- Identify part deviations according to specifications
- Prioritize problems and determine immediate actions to protect production line from stoppage
- Immediate problem analysis and problem solving including interaction with Engineering, Purchasing, Logistics or any other organization units that may be needed
- Efficient communication to all affected parties and suppliers to determine root cause and ensure corrective actions at the source (including escalation if needed)
- Reliable data collection for supplier performance tracking and charge back process
- Document information to include in lessons learned for new programs
- Enforce continuous improvement regarding Key Performance Indicators (KPIs), budget, headcount, etc
- Regular reporting to Quality Purchasing management of all KPIs for their area of responsibility
- Root causes analysis, effective problem solving, recurrence prevention (8D)
- Confirm/change quality standards agreed among SQI and 3rd party company regarding containment activities (sorting/rework method, quality standards, priorities, etc.) when needed
- Team work with Supplier Quality Engineer (SQE) to escalate or to agree on next steps when criticality requires it
- Travel to supplier’s site to supervise corrective actions (in agreement with SQE)
- Ensuring proper data collection for debit invoices including activities involved from different VW areas
- Ensuring tracking of supplier performance in VW systems
- Enforcement of 8D and FMEA requirements with suppliers when requested by the SQE
- Attendance of shift and shortage meetings (Audit, Start-of-Shift, End-of-Shift etc.) when necessary
- Give feedback to concern originator
- Bachelor’s Degree Engineering
- 1-3 years of job-related experience
- Product knowledge, either in the Metals, Interior/Exterior, Chassis/Power train or Electrical commodities
- Ability to read & understand engineering / technical drawings & specifications
- Presentation and computer skills
- Credibility and excellent teamwork abilities
- Excellent customer focus
- Capability to design/develop processes to assure process efficiency
- Flexibility to travel on short notice and travel outside of the USA
- Ability to promptly adjust work plans to address urgent tasks
- Available to work outside regular work time in urgent cases
- This position operates within a rotational shift system
- Bachelor’s degree in Engineering from an ABET accredited program required; Mechanical or Industrial Engineering program is preferred
- Co-Op/Internship with manufacturing processes or quality systems
- The ability to travel extensively, up to 70 percent of the time, and on short notice is required
- 2-5 years of experience with manufacturing processes or quality systems
- Understanding of root cause analysis, corrective action, continuous improvement tools, quality systems, statistics, and leadership
- Previous experience in working with the Automotive Industry Action Group’s (AIAG) processes for FMEA, control plans, capability analysis, measurement systems analysis, and PPAP is beneficial
- Managing all supplier related quality issues for Caterpillar’s Victoria facility Initiating supplier containment activity to ensure production schedules are not impacted
- Maintaining accountability with the suppliers to establish containment plans related to quality issues
- Proactively leading quality improvement projects at suppliers
- Good mechanical aptitude
- Clearly understand the technical requirements (dimensional and metallurgical) of the engine components based on the engineering drawings and the technical specifications/standards for MSE
- Referencing the metrological practice at KEC, work with the suppliers to develop the measurement methodologies, validate supplier measurement processes through Measurment System Analysis (MSA) and maintain the repeatability and reproducibility of the measurement equipment
- Develop material test and inspection plans in line with Marine Classification Society (MCS) requirements together with KEC and supplier and witness test execution
- Responsible for collecting all quality data of the engine component suppliers and work with PCEs to improve the quality and the controls
- Perform audits at supplier – and sub supplier (tier 2, tier 3) in regard to MCS requirements
- Utilizes failure analysis techniques to determine cause of failure and relays information to Engineering, Manufacturing and Service Engineering
- Works closely with the product engineering, the purchasing, operations and quality departments to provide advice and expertise for resolution of quality measurements both at suppliers and within Caterpillar
- Develops and maintains the quality inspection database of the main suppliers on the core engine components
- Maintains, calibrates and develops new set-ups and uses for test equipment in the laboratory including the CMM, ultrasonic, magnetic-particle, liquid penetrant, radiographic, weld validation and provide the guidance to the metrology and metallurgical labs
- Responsible for analyzing measurement data and distributing quality reports
- Coordinates service between the metrology laboratory and other departments with the purpose of providing advice and expertise on metallurgical and dimensional testing and works with supplier quality, manufacturing and engineering departments in that capacity
- Reviews and updates test procedures used in the KEC labs and develops new tests and writing procedures as required
- Writes and provides input for Inspection Instruction Sheets that reflect Caterpillar requirements to suppliers
- Writes purchase and work orders, provides support documentation to orders
- College degree in engineering or equivalent experience in areas of product design and manufacturing with an extensive background in engineering design, principles and mechanics
- Good working knowledge of Quality Standards and manufacturing operations along with good communications skills are essential
- Diligent and details personality and disciplined
- Good planning capabilities with priority setting
- Enjoy traveling (>50%) both domestic and internal
- Perform quality systems and special process audits
- Implement, and execute quality initiatives to improve the supply base and reduce risk to the end products
- Non-Conformance management (RCCA determination / reviews / reduction)
- Quality Management System (auditing / assessing / monitoring / analysis)
- Part/Process/System/Supplier Development (evaluation / analysis / recommendations
- Identify potential quality issues based on circumstantial evidence and recommend improvements
- Represent quality organization across entire product life cycle
- Trend and report on critical supply chain quality issues for improvements
- Support continuous improvement process and ACE initiatives
- Drive part and process qualification requirements for product acceptance
- Verify that delivered products meet specification and quality/reliability requirements
- Manage supplier corrective action request and internal quality investigations
- Implement and maintain supplier quality planning through focused audits
- Demonstrate behavior consistent with the company’s Code of Ethics and Conduct
- BS Degree in Engineering or Engineering Technology program
- 3-5 years technical quality experience with engines or similar product
- Experience with Quality improvement projects
- An understanding of small engines, quality systems, and technologies a plus
- Initiating supplier containment activity to ensure production schedules are not impacted
- Minimum of two years of job related experience, preferably in manufacturing, operations, procurement, and/or manufacturing engineering
- Experience in the on-highway truck industry
- Prepare documentation and provide support for new program part launches and process changes at Drive Automotive including PPAP, ISIR Control Plan, FMEA, IPC etc as it relates to supplier quality
- Schedule, coordinate and report to a cross-functional team meeting to address any supplier related concerns internal or external
- Interface with plant quality & manufacturing to ensure all suppliers are adhering to the Drive supplier quality requirements
- Responsible to insure all suppliers adhere to Drive Automotive Industries corrective actions request (on time closures, repeat concerns, root cause, etc)
- Conduct product audit to verify stability of supplied parts from suppliers are met
- Onsite visits to suppliers’ location to address quality issues to insure Drive Automotive Industries satisfaction is met
- Responsible to reduce risk to Drive Automotive Industries through suppliers RPN values in FMEA’s
- Ensure that an investigation takes place on all process failures, such as corrective actions, PDCA as it relates to Supplier Quality
- Perform Supplier TS: 16949 system audits to ensure acceptable quality levels are maintained and properly monitored through Drive SQA managements systems
- Make decisions and advise on an on-going basis to insure Drive Automotive Industries quality requirements are being met
- Coordinate and track progress for interdepartmental studies
- Perform statistical process analyses to verify material quality is being maintained through coupon testing / oil sampling etc…
- Ability to work three shifts as requested
- Able to function effectively using computer software
- Competent understanding of fixture design concepts and ability to use basic metrology equipment
- Able to provide clear direction and training to individual and small groups of employees
- Ensure Supplier counter measures are implemented and effective
- 4 year degree preferred with 5 years work related experience, and/or equivalent combination of education and experience
- Advanced Product Quality Planning (APQP)
- Evaluate supplier performance to ensure the supplier meets all requirements and does impact Magna performance to our customers
- Apply proven problem-solving techniques and cross functional activities to resolve significant problems in electronics and electro-mechanical commodities
- Participate in TS16949:2009 and ISO 14001 activities as determined by Quality Management. Participation with internal audits, layered process audits, and other audits as required
- Evaluate manufacturing, product problems and field complaints for opportunities to improve manufacturing, product performance and field service
- Conduct and/or participate in activities such as Design and Process FMEA's, Design of Experiments, Process/Product Capability Studies, Product Liability requirements, etc
- Participate in the development of Quality Strategic Planning, Defining or Developing - Cost of Quality, Future Role of Quality, Measuring Quality, etc
- Interact directly with suppliers on quality-related topics and assist Quality Management and Purchasing as needed with supplier development
- Monitor and report supplier quality performance, for quality defects, and drive improvement activities by leading 8D problem-solving meetings
- Provide leadership and direction to Quality Engineering Technicians
- Assists with continuous improvement efforts through Magna’s quality systems
- Champion supplier corrective actions for pass through issues to the customer
- Ensure effective closure of supplier CAR by verifying corrective actions at supplier location
- New Supplier assessments, quality systems and/or quality issues
- New program or major revisions ensure effective APQP, PSO and PPAP
- Ensure engineering changes are on time with an approved PPAP
- Review supplier prototype build status and quality of parts
- Participate in reviews with tooling engineering where required
- Supplier performance reporting
- Supplier quality issue investigations and verification of corrective actions
- Develop suppliers quality systems (systemic processes) and use of quality tools; flow charts, PFMEA, Control Plans, SPC, MSA (gages) and discipline problem solving
- Preventative action implementation of supplier lessons learned
- Process Sign off reviews
- On site PPAP approval
- Adhering and implementing the ISO/TS 16949 procedures
- Adhere and implement MAFACT requirements
- Responsible to protect own health and safety by working in compliance with established safe work practices and procedures
- Must comply with all ISO 14001 (Environmental) and OHSAS 18001 (Health and Safety) systems and standards as it pertains to their work
- Abide by all AODA and C-TPAT procedures that apply to their position
- Maintains customer, company and supplier confidentiality
- ASQC Quality Engineer certification or equivalent
- In depth knowledge of quality systems, TS 16949 Auditor
- Blue print reading and GDT knowledge
- A minimum of three years automotive experience
- Must be an assertive team player
- Conduct, as necessary, supplier visits to assess effectiveness of corrective actions
- Track all supplier related costs associated with poor quality and/or service; summarize these costs and communicate to the supplier via the debit memo process
- When applicable, facilitate and supervise all sorting activities (on-site at DexSys or off site) which may include; Sorting of the product by DexSys SQE, sorting of the product by 3rd party containment company, or sorting of the product by the Supplier. Report on these activities via sort report form and sort alert system
- Conduct receiving inspection according to the current sampling plan
- Assist, when necessary, with the training of operators on the use and handling during installation of supplier components
- Communicate lessons learned from manufacturing to Advanced Supplier Quality during new product launch and PPAP
- Blue Print Reading, GD&T
- Knowledge of TS 16949 core tools (FMEA, PPAP, SPC, MSA, APQP)
- Two years experience within an automotive production atmosphere desired
- Working in a team orientated environment
- Demonstrated strong written and oral communication skills a must
- Lead, and support, internal and external supplier quality audits (UTC Q+ and ISO audits)
- Work closely with Engineering to identify Key Product Characteristics required for adequate flow down to our suppliers
- Develop and coordinate the implementation of specific quality methodologies and improvement tools (DFMEA, APQP, PPAP, 8D, SPC, etc.) as they relate to our suppliers
- Compile and Initiate Production Part Approvals (PPAP) in support of Design Engineering and supplier transition efforts. This includes managing cross functional reviews of PPAP packages and assisting in Go/No-Go decision making with suppliers
- Investigate, resolve and reduce supplier non-conformances (SCARs) and escapes by utilizing industry and UTC established investigation tools and practices. This includes assisting suppliers in conducting effective Root Cause analysis and developing Mistake Proof solutions
- Coordinate supplier First Article Inspections (FAIs), certifications and PO Reviews
- Measure, monitor and audit supply base for continuing quality. This includes establishing supplier data collection, developing effective reports and metrics to review with Leadership, and make required recommendations
- Work in Coordination with UTC BIS Division Supplier Gold activities to qualify, audit, approve, train and support a world-class supply base
- Assist in ACE Process Certification training and guidance as it relates to PPAP and the Product Development process
- Provide support of Edwards Quality System, and make recommendations for any required changes
- This role will require between 40-50% travel
- A minimum 2 years of job-related experience or the equivalent education
- Good human relations skills
- Solid ability to use and demonstrate statistical and problem solving tools (fishbone
- Knowledge of APQP/PPAP process
- Metallurgical Basics
- Familiarity with manufacturing processes used to produce components and assemblies for Caterpillar Products
- Preferred experience in the Automotive field
Co-op-supplier Quality Engineer Resume Examples & Samples
- Develop Qualification & Verification Test Plans, Capability Studies and subsequent Control Plans at suppliers for new products
- Help develop PFMEA and Print Process Reviews with suppliers for new/existing products
- Participate in supplier qualification activities, quality system assessments, and process/facility audits and surveys
- Communicate and help facilitate supplier PPAP submissions
- Assist with the selection of qualified suppliers; Match product quality requirements with supplier capability; and Supplier development
- Initiate quality system improvements via application of quality engineering methods and/or supplier quality management principles
- Support internal manufacturing operations via investigation, analysis, and obtaining supplier corrective action for purchased product failures impacting affected Kohler facilities
- Assist with identification of Significant Quality Characteristics – both for internal manufacturing operations and supplied product
- Develop supporting process and product performance data, reports, recommendations, and initiate corrective actions for all listed responsibilities
- Special projects, tasks and activities as assigned
- Schedules and performs subcontractor audits/visits in co-operation with appropriate Presstran team members as per planned schedule for supplier development and continuous improvement in supplier products, processes, services and delivery
- Follows up with subcontractors and verifies successful implementation of corrective and preventive actions as part of development activities
- Reviews subcontractors’ prints and specifications. Designates SC’s and CC’s and issues and/or updates “Subcontractor Quality Requirements” forms
- Initiate, review, approve / reject and follow-up with subcontractors on PPAP submissions for materials, components and fasteners. Develop suppliers in doing PPAP and process reviews as per Presstran / AIAG standards
- Maintain subcontractor PPAP / Corrective Actions and other related documentation submitted to Presstran
- Define, Implement and Maintain Supplier product receiving inspection system and report the findings to QC team for control and tracking for improvements
- Review Supplier NCR on daily basis, monitor material disposition and get supplier product returned
- Develop / report and monitor receiving inspection measurables to improve quality of incoming products
- Contact subcontractors and initiate Subcontractor Corrective Action Reports (SCAR) for suspect or defective products
- Follow up on SCAR’s to verify subcontractor completion of corrective actions and closure of NCR’s
- Work with Presstran personnel on APQP and cross-functional teams to deal with subcontractor component, fastener and material issues
- Reviews internal functions, materials or ES testing on subcontracted components for PPAP submissions
- Revise and maintain Subcontractor Requirements Manual
- Comes to work each day, as scheduled
- Approaches each day and each challenge with a positive attitude
- Conducts themselves in a professional manner when receiving or giving feedback/information, whether it is positive or constructive
- Supports and models the Presstran operational procedures/policies, Employee Handbook and “How We Work Together”, Magna Employee’s Charter, Magna Corporate Constitution
- Follows and complies with all operational procedures/policies as stated in the Employee Handbook, Quality and Environmental programs (eg. TS16949, ISO14001)
- Takes pride in keeping their work area clean and tidy
- Post-Secondary graduate with a technical diploma or degree
- Must be proficient using CAD and Microsoft software: Excel, Word PowerPoint
- Additional Quality certificate / diploma will be an asset
- Excellent interpersonal, organizational, and communication skills are required
- Prior experience implementing TS-16949 procedures, APQP, PPAP submissions, GD&T, Flow Diagrams, FMEA’s, Control Plans, and working independently with tooling and material subcontractors
- Planned and Executed Incoming Inspection Systems and processes
- Internal or lead auditor experience for TS16949 and/or ISO 14001 an asset
- Drive implementation of statistical process controls and quality improvements at key supplier sites
- Conduct quality management system and process audits at suppliers as required
- Provide on-site guidance and coaching to key component suppliers to drive improvements in supplier parts per million (SPPM), on time delivery (OTD) and warranty costs
- Drive warranty recovery efforts with suppliers
- Lead training initiatives on quality tools such as FMEA, Control Plans, Process Auditing, etc. for both supplier and internal resources
- Conduct a quality management systems and process audits at suppliers as required
- Work with potential suppliers to improve / implement robust quality systems prior to becoming suppliers
- Provide on-site guidance and coaching to key component and branded product suppliers to drive improvements in supplier parts per million (SPPM), on time delivery (OTD) and warranty costs
- Lead and/or support new product development programs as needed
- Facilitate change management with suppliers
Electrical Components Supplier Quality Engineer Resume Examples & Samples
- Working with purchasing team on the supplier selection
- Supplier risk assessment and qualification for both product and process
- Quality plan definition, alignment and execution for the suppliers which includes PFMEA, control plan, CTQ processes, outgoing inspection, reliability qualification and monitoring plan, Quality reporting, traceability etc
- Working with engineering team on the DFM for the electrical parts in develop stages
- Process audit for risk assessment and improvement
- Leading for yield improvement
- Proactive quality control system setup for the purchased electrical parts
- A minimum of three years experience as a SQE
- A minimum five years experience in quality engineering, project/program management; or equivalent. Must have thorough and complete knowledge of respective field
- Experience with Paint and Mold Manufacturing
- Managing supplier related quality issues with Facility Management and Suppliers
- Supports SDE in Process Change Notification Management
- Supports Process of Deviation Management
- Bachelor’s degree or Minimum of 3-5 years of Job Related experience
- Extreme sense of urgency and customer focus required for this role
- Certifications: ASQ
- Black Belt Experience
- Perform supplier quality audits and management of the supplier corrective action process. Maintain and update supplier audit schedule when required
- Implement and develop mechanisms to monitor and identify supplier non-conformance trends based on risk
- Track supplier quality performance measurements for suppliers (KPI's) and participate in supplier performance reviews. Completion and approval of supplier evaluations and monitoring when required
- Manage and drive continuous improvement activities focusing on supplier quality
- Review and support Supplier Change Notifications
- Review and approval of raw materials, first part approval and supplier process validations
- Maintaining supplier quality documentation in conjunction with purchasing
- Liaise with Quality Control by providing Quality Engineering support to Incoming Quality Control, In-Process and Final Quality Control for raw material issues
- Provide input and support to the Corrective and Preventive Action program (CAPAs) and the Non-Conforming Product Process
- Support of the Internal Audit, Vendor Audit and Regulatory Audit Programmes
- Completion of risk assessment of suppliers, non-conforming materials and CAPA's
- Provide meaningful Quality measurement while ensuring that in-house or external Quality issues are effectively prioritised and acted upon in a timely manner
- Designee to the Senior Quality Engineer
- Third Level qualification in Science, Engineering or a relevant technical discipline
- Qualification in Quality/Validation/Statistics would be a distinct advantage
- Proven knowledge and experience (min 4 years) of working with ISO13485, ISO14971, the Medical Device Directive and the FDA QSR including 21 CFR Part 820 and 21 CFR Part 11, ideally gained in the medical device industry
- Qualified Lead Auditor, preferably within the Medical Device Industry
- Proven knowledge and experience of all aspects of Validation including Process Validation and design validation
- Strong interpersonal skill with the ability to communicate effectively at all organisational levels
- The ability to challenge thinking/opinion/actions in light of ensuring Quality Systems and Processes are adhered to
- High attention to detail in all aspects of the role
- High self motivation
- Good working knowledge of Microsoft Office
- Communicate with suppliers and internal customers of Norplas on product quality concerns and initiate corrective and/or preventive actions for these concerns
- Participate in continual improvement programs and activities to support the achievement of department KOI and mini goals
- When applicable, facilitate and supervise all sorting activities (on-site at Norplas or off site) which may include; Sorting of the product by Norplas SQE, sorting of the product by 3rd party containment company, or sorting of the product by the Supplier. Report on these activities via sort report from and sort alert system
- Monthly KOI, special status and mini goal tracking and reporting to SQM. Maintain the communication board within the SQE office
- Support manufacturing on all supplier related issues; Report issues and resolution of these issues periodically to management. Communicate to team members all necessary feedback regarding supplier/component related issues
- Act as the liaison between Norplas manufacturing and the supplier for all component related issues
- Bachelors Degree Required
- Effective launch transition to production
- Review component drawings and understand the application requirements for each component
- Engage and support Advanced Team as required during new launch transition phase
- Ensure supplier process controls meet reliability and capability levels
- Certification as a CQE would be an asset
- Able to travel and work flexible hours to accommodate international Suppliers and support Operations needs up to 50% of the time
- Ability to analyze, troubleshoot and follow up on internal & customer supplier quality issues
- Proficiency in learning Business Operating Systems (i.e.TS16949, IMDS, QSI, SupplyWeb, Customer Requirements, Trans4M etc.)
- Strong organizational and prioritizing abilities
- Knowledge of various processes (i.e. moulding, coating, assembly, welding, electronics etc.)
- Strong Presentation skills
Materials Supplier Quality Engineer Resume Examples & Samples
- Complete supplier surveys and associated supplier approvals
- Implement required quality metrics and use that data to address supplier improvement and concerns
- Effectively problem solve production issues as they arrive, related to materials, components, or packaging product
- Travel independently throughout the supply base to address issues and concerns, adjusting to the different work environments at suppliers’ facilities
- Interface with upper management and provide needed feedback for important decisions
- Performs other duties and responsibilities as needed
- Work independently to established quality criteria, plan for implementation, and execute quality plans for all products. Includes inspection planning (PPIP), sample approvals (FAS & LS) and training on the requirements
- Head up efforts for nonconforming material review and corrective action assignment to the suppliers
- Support the Supplier Quality Manager in carrying out higher level requirements and projects
- Work effectively and collaboratively with others
- Bachelor of science or Bachelor of engineering is minimum
- Have solid knowledge of quality management, be familiar with ISO9000 quality system is a must, good understanding of TS16949 quality system is preferred; (Better have ISO internal auditor certification.)
- Have solid knowledge on CM management, have strong sense of influence to leverage other team members to gain success
- Deep understanding on the LCD display and Touch panel manufacturing and quality control
- Knowledge on the plastic injection molding process and quality control, understand the SMT process and quality control and IPC-610 knowledge
- 8+ years working experience at least, working background with world-wide famous ODM/OEM/EMS company (like Foxconn, Flectronics, Celestica, Jabil, Samina…) is preferred
- Good knowledge of 6 Sigma and/or Lean methodology is preferred
- Self-initiation for quick solution for short-term and long-term
- Attitude to influence others, self-management, working for multiple tasks
- Can do attitude and open mind for discussion
- Support plant production by reacting to minimize downtime resulting from supplier escapes
- Issue track and assist with the 8D corrective/preventive action process
- In support of supplied part changes and new part introduction, evaluate supplier PPAP submissions for acceptability
- Assist with coordination of daily activities in the SQA lab
- Conduct Q+ and Process audits at suppliers as required
- Supplier manufacturing quality – assist with the implementation of Pro-Cert / Quality improvements at key RCS suppliers
- Track and report supplier performance in the form of SPPM
- Conduct Q+ System Audits and Process Qualification Audits
- Daily plant manufacturing support
- Investigate and resolve reported supplier-related manufacturing issues, 8Ds, APQP activities, defect resolution, reduces/eliminates warranty issues
- Corrective Action Team project support, addresses field complaints, conducts monthly reporting duties for Carrier Corporate and UTC WHQ
- Provides engineering support for activities related to supplier selection and evaluation, material qualification, supplier performance and receiving inspection
- Contributes to the development, maintenance and improvements of supplier quality policies and procedures
- Reviews and approves all material and component specification drawings
- Assesses supplier capabilities through direct visits, technical discussions and quality system audits
- Bachelor's Degree in Engineering, Science or Quality Assurance, min HETAC level 8
- At minimum 3 years experience in an Engineering / Quality role in a Health Care environment
- Excellent interpersonal and communication skills with good leadership abilities
- Candidates should have a proven track record of working in a fast paced environment
- Work with and support multiple CCS business units to achieve business unit quality goals
- Coordinate cross-functional teams to drive Relentless Root Cause Analysis (RRCA) on assigned quality issues utilizing the Global 8D process
- Support Business Units and WHQ Supply Chain with resolution of customer and supplier quality issues, Support Value Stream Mapping (VSM) and Kaizen events
- Drive, teach, and implement Process Certification and PPAP at assigned suppliers
- Support and drive the increase in Suppliers achieving the performing and gold level in the UTC Supplier Gold program
- Work with the BU sites and WHQ commodity managers in reducing the underperforming suppliers in the supplier gold program
- Coordinate PPAP training and support BU’s / new product teams in executing Passport requirements
- Support development of polices / standard work instructions and maintenance of SQA website
- Become a certified Supplier Health Assessment (SHA) assessor
- Drive, teach and implement Process Certification and PPAP at assigned suppliers
- Coordinate PPAP training and support BU’s/new product teams in executing Passport requirements
- Support development of polices/standard work instructions and maintenance of SQA website
Manager Supplier Quality Engineer Resume Examples & Samples
- Supervise as the Quality engineer in a 3rd party logistics environment
- Manage the receiving inspection process
- Responsible to ensure adherence to the Quality Management Systems
- Responsible identifying root cause and driving corrective action
- Contributes to supplier performance and development as necessary
- Leads and coordinates Achieving Competitive Excellence (ACE) initiatives
- Manages Clinic activities
- Lead and assist with Quality initiatives to continually improve performance and reduce escapes
- Lead, direct, and train Inspection personal
- Maintaining accountability with the suppliers to complete containment plans and corrective actions
- Proactively leading quality improvement projects between suppliers and Cat’s manufacturing teams
- Experience with steel fabrications
- Certified ASQ (American Society of Quality Engineers)
- Work cross-functionally (especially with the broader Production, Supply Chain, Product Development and Engineering teams) to define and execute Supplier Quality Management and Supplier Development strategies, with the goal of reducing variation (and cost) in sourced and manufactured products
- Work with suppliers to ensure all necessary quality activities are rigorously addressed during initial product release and on-going production
- Work with suppliers to quickly address and resolve any quality issues seen during on-going production
- Implement quality tools such as: process mapping, Process FMEA, process control plans, process validation (IQ, OQ, PQ), Measurement System Analysis(MSA/GR&R), Statistical Process Control (SPC); and Design of Experiments(DOE)
- Support advanced product quality planning (APQP) process to ensure successful integration of new products into operations
- Manage injection molding tool qualification for for parts made at our third party manufacturing partners as well as our own production facility in Germany
- Proactively work with the Product Development team and suppliers to improve design for manufacturability and reduce defects and cost
- Ensure supplier test strategy aligns with quality goals & Harry's requirements. Execute supplier audits, CAPA’s and monitor metrics
- Minimum: Bachelor of Engineering
- 3-5 years of experience with 1-2 of them in a manufacturing or production environment
- Exposure to both large (Fortune 1000) multinational companies and smaller, high growth companies
- Exposure to industrial engineering and design for manufacturability is a plus
- Ability to design test equipment and fixturing is a plus
- Exposure to plastics manufacturing is a plus
- Fluency in Mandarin and/or German and significant international work experience are a strong plus
- Attend and actively participate in all PMP and LRR activity to assure coordination of requirements with supply base during the development phase of new products
- Coordinate PPAP request, review of PPAP record and approval for all supplier PPAPs. Coordinate and implement annual validation requirements for all purchased components
- Assure all supplier PPAPs meet print specifications and Magna quality standards
- Provides support by evaluating potential Magna suppliers. Perform audit, report results and follow through on open actions
- Works with corporate purchasing to develop or revise supplier quality policies and procedures
- Monitors quality system status of Holland Mirrors suppliers and tracks quality certifications and necessary assessments
- Develop system for all line accumulations of supplier issues. For customer reject or high volume internal rejects, issues DCARS and follows up with supplier to assure effective corrective action implementation and DCAR closure
- Performs other duties as necessary. May supervise and/or provide work direction to other staff
- Bachelor’s degree in Manufacturing, Quality or Engineering field with understanding of quality engineering practices, principles, processes, etc.; or equivalent
- Demonstrated ability to conceptualize, coordinate, integrate internal data, and clearly articulate concepts, ideas, and other issues relating to quality engineering
- Strong organizational, project management, and leadership skills to prioritize, coordinate projects, manage conflicting needs, and deal with many issues at one time. Must be able to work independently
- Strong computer background with ability to calculate and analyze data, generate reports, present information, etc
- Demonstrated ability to research and recommend new suppliers, products and processes. Must be able to initiate implementation of continuous improvement processes
- Demonstrated ability to thoroughly research, recommend, and oversee implementation of new products, materials, processes, etc. and present information. Must have excellent interpersonal skills to exercise influence at various levels and functions
- Strong leadership skills. Must be able to work independently with considerable latitude for unreviewed action
- Excellent communication/negotiation skills with peers and suppliers in a positive, cooperative way and maintain productive and professional relationships with key functional areas
- Management for all APQP projects via gate review, APQP work book to make sure supplier can meet program requirement
- Continuous communication with PM Manager in order to be deeply involved on program issue and assist on supplier activities to be performed to accomplish launch expectations
- Handle 8D report from supplier Travel to supplier to verify the correction action plan implementation for quality complaint
Supplier Quality Engineer, Mechanical Resume Examples & Samples
- Assess and audit manufacturing processes for major mechanical assemblies by applying knowledge of product design, fabrication, assembly, tooling, and materials
- Define and review mechanical specification requirements for fit, quality and reliability
- Review geometric dimensioning, tolerances, and process capabilities
- Ensure product and process quality by designing quality metrics, testing methods, establishing standards, and confirming manufacturing processes
- Drive on-going improvements in cycle-time, cost, quality, and yield
- Develop and implement quality programs including tracking, analyzing, reporting, and problem solving
- Acquire and analyze data using appropriate standard quantitative methods to facilitate process analysis and quality improvements
- Drive root cause and corrective action for system, rack integrator and in data center failures
- Perform regular audits of manufacturer facilities
- Assist Facebook Sourcing and Hardware teams in vendor selection
- Conduct First Article and Source Inspections reviews on mechanical parts and assemblies
- Carry out Vendor Approval/Surveillance audits to ensure that suppliers are capable of meeting our quality requirements on a continuous basis
- Ensure that "First Articles" are carried out to verify that all parts meet their Dimensional and Functional requirements
- Lead cross functional QIT's to resolve Quality issues at suppliers
- Participate in cross functional teams to review process improvements/ optimizations at suppliers through PFMEA's and control plans
- Complete validations, test reports and protocols
- Represent the Vendor Engineering function on SSI's
- Represent the Vendor Engineering function on NPI's
- Follow all environmental, health & safety rules and procedures and participate in safety and environmental activities in order to improve the workplace for all employees
- A suitable Engineering Degree Manufacturing, Mechanical, plastics/molding etc
- Lead Auditor an advantage
- Excellent "hands-on" technical skills
- Ownership for supplier quality performance and measurement including KPI's and participate in supplier performance reviews. Enable reporting of metrics for monthly reviews
- Participate in External Audits and Internal Audits as needed. Ensure Regulatory compliance in area of responsibility to GMP of all medical devices regulatory agencies (i.e. FDA, IMB, Notified bodies, etc)
- Responsible for accuracy and integrity of supplier data that ensures compliance with documented procedures & processes
- Maintain structured communication channels with strategic sourcing, identifying responsibility by commodity / supplier
- Deliver continuous improvement activities focusing on supplier quality
- Support assessment of supplier changes
- Participate in supplier audit program - planning, execution and closure
- Participate in cross functional projects both locally & globally as required
- Bachelor's Degree in Engineering or Science fields
- Minimum of 2 years experience in manufacturing environment or equivelant
- Good knowledge with GMP, ISO 13485, 21 CFR Part 820 standards
- Good knowledge of FMEA, Validation Programs and SPC processes in a highly regulated environment
- Demonstrated working knowledge to positively influence supplier quality performance
- Participate in the development and review of project documentation. Represent Quality on the Project/Program Core Team
- Provide Quality direction and support for procurement activities, specifically supplier ISO 9001 and UTC Q+ specific audits, qualification and PPAP (requirements flow-down and verification)
- Assessment of systems and processes to identify deficiencies and participate in resolution of issues found
- Assist in development of quality system processes (i.e., records management and document control, control of electronic data, software development and control, etc.)
- Assist in defining/developing Quality Program status indicators, performance measurements and reporting requirements. Includes collection and analysis of product returns data and production yields
- Review and comment on drawings, calculations, specifications and other design inputs/outputs using SIPOC tool
- Provide direction in developing inspection plans, PPAP, In-process and Final Product Inspection, Sampling Plans, inspection and acceptance criteria and Design Validation Testing
- Investigate product quality problems, determine root cause, gather and analyze data and implement corrective actions and mistake proof solutions to reduce or eliminate cause
- Perform process capability studies, or special studies necessary to eliminate waste and reduce variation to improve control and lower cost of poor quality
- Participate in the improvement of manufacturing processes for existing product and assist in development of new processes and associated controls in accordance with UTC Process Certification requirements
- Job related projects as they arise
- Reviews design records and provide feedback to required OEM specifications for Suppliers
- Present supplier APQP requirements during Supplier Day meeting
- Develop Supplier APQP requirements that reflect current PDP system
- Schedule APQP meetings to present issues from Supplier APQP document review
- Prepare and present prototype requirements to Suppliers
- Participate in seat complete testing to acquire information related to Supplier issues
- Review gage design and participate in sign-off approval
- Support in review of Supplier DVP& R proposal for approval, and review test results for compliance
- Schedule and conduct supplier visits for initial and ongoing PPAP reviews
- Participate in TASP initiation, distribution and closure
- Provide support for Division Supplier corrective action issues
- Attend Supplier Partnership Reviews for Suppliers with on-going issues
- Participate in customer program update presentations
- Support Division on-site reviews
- Coordinates Supplier Development requirements for new and existing programs with Division, Program Team, and Craftsmanship utilizing both written and verbal tools through established methods of reporting
- Guides junior quality assurance engineers
- Utilize Supplier auditing methods to assess potential Suppliers
- Minimum 3 years of diversified engineering and/or quality experience with increasing responsibility. Experience to include supplier auditing, problem solving and corrective action development
- Knowledge of statistics and production quality systems
- Demonstrated ability to track improvement process through performance data
- Strong communication skills: verbal, written and technical presentations
- Strong organizational skills and the ability to successfully complete multiple tasks within established and changing deadlines
- Demonstrated successful performance with independent problem solving and presentations
- Proficient with word processing, spreadsheet and database applications
- Responsible for the development, implementation and ongoing maintenance of Quality Management Programs aimed at optimising product quality and processes in the sub-contract manufacturing operations & sub-tier suppliers, including supplier visits as required
- Responsible for the implementation and oversight of Supplier Quality Management Plans/Agreements with suppliers, including supplier review, supplier audits, issue resolution and scorecard based supplier performance management
- Provide technical and quality support to transfer of products and associated technology from Design to sub-contract Electronic Manufacturers, including PQP development, new process qualification/validation and production start-up support / qualification
- Manage product related customer complaints, investigation, root cause / corrective action and customer feedback. Co-ordinate return of defective product and associated investigation with Sales & sub-contract manufacturing operations as required
- Create top level part numbers and develop BOM's in line with internal QMS requirements (ISO 13485 and FDA) and ERP requirements
- Develop Manufacturing instructions for the efficient and effective manufacture of product in production and handling general product queries
- Development and application of the quality system as it relates to process and product controls, including training for compliance to ISO13485 and the FDA Quality System Regulations (QSR)
- Support for DCN, sample, CoC and concession processes pertaining to the supply base as required
- Educated to Degree level, with a preference for Electronic or Electrical Manufacturing background
- Industry type: Medical Device or similar regulated industry preferable. Knowledge of applicable quality system requirements for medical devices
- Experience of electronic manufacturing process with previous supplier auditing experience
Adv Supplier Quality Engineer Resume Examples & Samples
- Own and Lead Supplier 8D’s on all supplier product issues with a targeted closure of 20 days from initiation
- Own and Lead Supplier Quality Business Unit priorities, as identified
- Develop and obtain Supplier approved boundary/PPAP samples and maintenance of the boundary samples throughout the production cycle
- Participate in pre-launch programs with regards to design and specifications required
- Participate and Lead root cause analysis as required in Warranty returns, follow up communications with customers and provide analysis of data as required
- Manage internal line rejections from root cause analysis through to DMN closure analyzing trends and driving corrective actions
- Diploma or Degree required in related filed
- 3 - 5 years’ experience in a manufacturing environment required
- Review and analysis of dimensional data from 1st piece layouts, gauge R&R and capability studies
- Aptitude for working with numbers with a high degree of accuracy
- Able to problem solve effectively
- To analyze, troubleshoot and follow up on internal & customer supplier quality issues
- Proficiency in computer skills. (i.e. word, excel, power point etc.)
- Organization of documentation, records, time, priority setting and deadlines
- Self-Motivated, ability to initiate and follow tasks through to completion
- Must be proficient in learning Business Operating Systems (i.e.TS16949, IMDS, QSI, SupplyWeb, Customer Requirements, Trans4M etc.)
- Knowledge of various processes (i.e. molding, coating, assembly, welding, electronics etc.)
- Represent Autosystems in a professional manner
- Problem solving related to manufacturing
- Focal point for supplier quality related activities and process control for supplier base supporting DS Groby business unit
- Coordinate, direct, and manage supplier quality activities with focus on issue resolution (CA/PA), supplier approval, supplier qualification, supplier development, process control, and quality assurance consistent with Global Sourcing quality initiatives
- Improve quality assurance and drive consistency and adherence to quality procedures and requirements consistent with GE O&G Global Sourcing quality processes and procedures
- Drive continuous improvement of supplier's quality performance through Six Sigma and Lean Six Sigma principles and methodology
- Monitor and drive for Cost of Failure/ Quality (COF / COQ) reduction within the business site
- Manage supplier recovery by working with Sourcing/ Commercial team and supplier to recover all costs associated with rejects/defects
- Monitor suppliers’ non-conformance performance, and identify and drive process improvement, root cause analysis, and corrective action implementation
- Establish programs to monitor and improve suppliers process capabilities for CTQs
- Drive NPI projects at suppliers through Qualifications and Process Capability studies
- Technical focal point for supplier activities directed toward process control and quality assurance of site material and components
- Providing technical guidance to suppliers toward assuring product/process compliance with engineering drawings and specifications
- Work closely with Sourcing COEs, Business Teams, and Engineering to eliminate roadblocks and communication barriers that may affect quality requirements
- Proven experience in Supplier Quality in Engineering / Electronics / Machining/ Fabrication
- Extensive background within Engineering (preferably with an extensive background in Aerospace/ Subsea/ Military/ Commercial)
- Lead Auditor qualified through a recognised accreditation body
- Ability to work in cross functional team environment
- Leadership in communicating business goals and objectives
- Experience in Oil & Gas/ Energy Industry/ Aerospace divisions
- Sound knowledge in ISO 9001 QMS Requirements and applications
- Experience in supplier assessment / audits (lead auditor)
- Good written & verbal communication skills and skills to speak and understand English
- Machining (CNC/ Fabrication/ Plastics) knowledge is preferred
- Working knowledge in MS excel, Mini-tab or basic statistics using excel
- Knowledge in Technology / Metallurgy / Welding
- Hands-on experience in supplier technical development or supplier quality development is preferred
- Green Belt Certified (GE Employees)
- Bachelors Degree in an engineering or technical discipline (or non-technical degree with 5 years of experience in manufacturing, engineering or quality assurance experience, or an Associate’s Degree with 15 years of manufacturing, engineering or quality assurance experience). Key Qualification
- Some experience in manufacturing, engineering design, quality assurance or regulatory assurance
- Proficiency with Microsoft Excel Spreadsheet development and analysis
- Some experience in manufacturing, design, quality assurance or regulatory assurance. ASQ Certified Quality Engineer
- Demonstrated knowledge of Quality Management System tools, continuous improvement methodologies & in-depth understanding of site level products & related processes
- Excellent oral communication & report, business correspondence & procedure-writing skills
- Engineering diploma (mechanical and/or electrical engineer)
- Driving license
- Engineering experience (Technical experience)
- Quality and/or sourcing background (engineering, QMS, QA/QC),
- Excellent Hungarian skills (verbal & written),
- Strong project management skills, ability to prioritizes,
- Ability to deliver results & meet deadlines, ability to learn quickly,
- Process, data & documentation focus,
- Flexible working hours & ability to travel
- Knowledge of EU suppliers (mechanical industry),
- Experience working with integrated operational systems (ERP)
- Act as the technical focal point for supplier activities directed toward process control and quality assurance of business components
- Establish a structured approach for consistency and adherence to quality procedures and requirements
- Work closely with various divisions of Infrastructure businesses to conduct First Piece Qualification (FPQ), quality surveillance, and capacity audits
- Assist in the supplier approval process including manufacturing, technology, and Environmental Health and Safety (EHS) risk analysis
- Track and work on Request For Quotation (RFQ's) and new business opportunities
- Work closely with Sourcing, Manufacturing, and Engineering to eliminate roadblocks and communication barriers that may effect quality and delivery requirements
- Bachelor’s degree from an accredited university or college (or equivalent in knowledge/experience)
- Strong interpersonal and leadership skills
- Six Sigma training is preferred (GE employees only)
- Work closely with GE Industrial businesses Design Engineering, Product Service Engineering, SQE teams, Commodity Leaders, Buyers, business & GGO Sourcing and Project Management teams, Supplier Performance Leaders on all acitivities required to effectively support development of supply base in Russia & CIS and drive identification, qualification & development of RUCIS regional suppliers for forgings, castings and fabrications
- Drive Know Your Supplier (KYS) policy compliance and be responsible for suppliers audits
- Bachelor/Masters Decree in Mechanical Engineering
- Experience in qualification of forgings, castings and fabrications; understanding
- Experience with special manufacturing processes (welding, bending etc.) and NDT processes; ability to assess suppliers’ equipment & technical sufficiency
- Experience with coating and paint systems
- Shop floor experience: quality management (QMS) role with a manufacturing company
- Coordinates and leads supplier process verification activities, ensures engineering design records and specification requirements through PPAP processes, and supplier quality system audits
- Leads process improvement efforts with suppliers using quality system tools and procedures to drive process based quality improvements. Leverage statistical tools for evaluation of process capability of critical-to-quality parameters
- Establishes a close working relationship with suppliers to assure open and honest communication to resolve or anticipate quality concerns
- Interfaces with design engineers and manufacturing engineers to qualify new product/processes, problem solving, buy-in and support of new supplier processes
- Participates as a leader/team member of Lean Manufacturing, 5s, Six Sigma and Kaizen initiatives and develop if needed, projects on multi-disciplinary teams for corrective and preventive action in conjunction with suppliers
- Evaluates and improves supplier process control plans, PFMEAs and statistical process controls and methods to monitor critical-to-quality processes
- Provides training to Electrolux personnel on QSI system usage, GSQA, standardized quality systems audits and PPAP processes
- Works with Purchasing to collect data to support supplier reviews
- Develops supplier quality engineering plans for new product, product/supplier introductions and ensures supplier preparation, readiness and ability to meet engineering design requirements for relevant new business
- Excellent organizational and communication skills with the ability to write reports and procedure manuals, as well as to effectively present information
- Ability to effectively utilize application software, word processing, spreadsheets and specialized application software packages
- Appliance product experience a plus
- Self-starter, ethical and highly motivated
- Willing to travel as required
- Responsible for investigating, analyzing and correcting quality problems generated by purchased parts
- Improve supplier quality performance for the assigned commodity
- Responsible for auditing suppliers processes for compliance to Electrolux EL29002A and EL29002P standards
- Responsible to support the qualification of new parts/components in collaboration with engineering, purchasing and the supplier through PPAP
- Develop positive relationships to work closely with other departments to manage and implement supplier/engineering changes, new product introductions and resourcing
- Proactively generate and support improvement projects working with engineering, purchasing, manufacturing and plant quality to positively affect quality metric such as: SCR, NRFT and PPM
- Lead PPAP and start up training sessions for suppliers when deemed appropriate by the SQ Manager
- Work actively with APO (Asia Pacific Operations) to monitor performance of off shore suppliers
- Work on the generation, follow up and closure of SCARs as a result of quality of a purchased part that affects NRFT, SCR or PPM
- Utilize statistical analysis tools i.e. CP, CPK, Control charts to understand process variances, investigate and identify root cause
- Understands and becomes a Certified EHP Auditor
- Must have knowledge of problem solving tools i.e. 8D, 5 whys, A3 etc
- Support purchasing/Engineering with risk assessment during new supplier selection process
- Excellent statistical analysis skills, 6 sigma tools knowledge (preferred)
- Knowledge of blueprint reading, GD&T
- Experience on a high volume, fast pace, manufacturing environment
- Excellent leadership, communications and negotiation skills
- Communicate clearly and concisely verbally and in writing
- Able and available to travel if required with short notice
- Responsible for Supplier Quality Contracts (for selected suppliers)
- Conduct supplier audits and qualifications
- Identify critical to quality elements and secure in inspection processes
- Drive Item approval process for critical components
- Organize containment activities for defective purchased parts/products
- Determining root cause of supplier quality problems and implement effective quality resolutions ex. with 8D Methodology
- Monitor and Improve supplier quality performance
- Hands on Supplier quality assurance for selected suppliers
- Drive and coordinate supplier quality continuous improvement activities
- Develop methods and processes to improve the quality level of purchased parts/products
- Highlight and communicate quality risks in new product development projects
- Bachelor’s or Master’s degree in Engineering, preferable within electronics and/or Mechanics
- Experience within supply chain with electronics, mechanical and/or box build manufacturing
- Knowledge and interest of product and process Improvement methods— ex. FMEA, LEAN, SixSigma, PPAP, PDCA
- Knowledge of quality standards ex. ISO9001, TS16949
- Ability to define problems, collect data, establish facts, and make an action plan to solve the issue
- Good communication skills on all levels in an organization internal and external
- Knowledge about ERP system use, likely SAP
- Skills in handling data from various systems ex. Excel, SQL, etc
- High level reading, writing, speaking and listening English skills
- Ability to drive and motivate the organization to a better quality level
- Proactive, self-driven and the ability to get things done
- Systematic and methodical with strong analytical skills with attentive to details
- Open minded team player
- Fact based communicator, who communicates the true risks no matter the consequence
- Ability to align resources, seeks the input of key stakeholders, and manages others to achieve results
- A natural authority, courage and will to hold people accountable
- A positive person with a sense of humor
- Participates or leads teams to provide quality input for the development, manufacture, procurement, and acceptance of a variety of products and assemblies
- Develops methods and writes detailed instructions for inspection processes
- Coordinates the design of product acceptance equipment and the ordering of testers, gages, and equipment to support product acceptance
- Provides technical assistance to inspection areas
- Develops and monitors quality metrics, levels, and trends
- Analyzes and makes recommendations regarding product discrepancies
- Evaluates opportunities for defect prevention and implements specific and preventative corrective actions
- Develops test procedures and performs evaluation tests, capability studies, quality audits, data reviews, and other engineering evaluations utilizing Six Sigma methodology
- Interacts with customers, suppliers, designers, and others to assist in resolving design, development, production, and acceptance issues
- Provides technical consultation to management and others, and leads technical project teams
- Conducts activities in a safe and healthy manner and works in accordance with established ES&H requirements to ensure the protection of associates, the public, and the environment
- Takes actions necessary to stop work when an unsafe condition or action is identified. Every associate has the right and responsibility to stop work when unsafe conditions or actions are identified
- Some travel (10-30%) is required
- Must be an U.S. Citizen in order to obtain a DOE “Q” Level security clearance
- Bachelor of Science degree in Mechanical Engineering, Electrical Engineering, Chemical Engineering, Manufacturing Engineering or related engineering discipline from an ABET accredited institution
- DOE Q-Clearance desirable
- Two or more years of experience as a Quality Engineer or Manufacturing Engineer a plus
- Ability to analyze engineering drawings and specifications to develop effective acceptance processes and improve existing processes
- Ability to lead quality improvement projects
- Familiarity with Six Sigma tools and methodology; Six Sigma certification preferred
- Effective verbal, written, and presentation skills
- Ability to work effectively in a team environment and to influence others to accomplish complex tasks and solve complex technical problems
- Ability and willingness to drive change and challenge / improve existing processes
- Demonstrated project management/leadership skills; ability to evaluate situations, determine corrective measures, plan and lead other employees and suppliers to execute plans to meet customer deliverables
- A minimum of a Bachelor's degree is required preferably in engineering, technical, or life science
- A minimum of 4 years of experience in a GMP and/or ISO regulated industry is required
- Experience in the Medical Device/ Pharmaceutical industry is preferred
- Knowledge with FDA CFR Part 820 and ISO 13485 is preferred
- Strong quality engineering skills with a proven track record in design verification/validation, process verification/validation, and effects analyses is strongly preferred
- Blueprint literacy including GD&T is preferred
- Strong in root cause analysis skills are required
- Six Sigma, Lean, or ASQ Certification and trainings are preferred
- This position is located in Raynham, MA and will require up to 20% travel.Quality (Eng)
Junior Supplier Quality Engineer Resume Examples & Samples
- Manage supplier related Non-Conformities (NC and SCAR's) and Corrective and Preventive Actions (internal CAPA's)
- Support Process Validations at suppliers
- Support QE with supplier product PVE's (First Article Inspection, Control Plans, Critical to Quality, Capability studies)
- Contribute to product investigations related to SCAR and internal CAPA
- Support supplier preparation for inspections by authorities / third parties
- Support for Quality Agreement and Change Agreements, supplier assessments and supplier audit process
- Prepare regular report and supplier quality metrics
- A minimum of a Bachelor's Degree in Engineering, Life Science, or related discipline is required
- Supplier quality experience is preferred
- Both, FDA and ISO regulations knowledge is required. FDA CFR Part 820 and/or ISO 13485 knowledge is preferred
- Strong communication, teamwork, and problem solving skills are required. Strong root cause analysis skills are required
- Business fluency in English and German is required
- Pro-active approach to work with hands on ability
- Ability to interpret, communicate, and work from drawings and specifications
- Validation knowledge
- Highly computer literate
- GMP knowledge
- High work standards
- Excellent planning and organisation skills
- A minimum of a Bachelor's Degree is required. A Degree in Engineering, Life Science, or related discipline is preferred
- Minimum 5-6 years’ experience in a Quality or Engineering Function within a Medical Device Company
- Experience in the medical device, biotech and/or pharmaceutical industry is preferred. Both, FDA and ISO (International Organization for Standardization) regulations knowledge is required FDA CFR Part 820 and/or ISO 13485 knowledge is preferred
- Previous experience of product transfers/start up desired
- Auditing background is preferred
- Possess knowledge of statistical analysis tools (Minitab SAS preferred)
- The Supplier Quality Engineer II will conduct audits to good manufacturing practices, international organization for standardization and any other applicable standards
- He/she will provide complex product team support for quality system design and audit, compliance assessment, and for support of steady state manufacturing processes
- This individual will utilize multifaceted industry and process excellence standards on an expert level in daily quality operations, including good manufacturing practices (GMP), equipment engineering system (EES), and international organization for standardization (ISO)
- The Supplier Quality Engineer II will address and correct product and process complaints. He/she will report on contract manufacturer performance metrics and management reviews
- This individual will oversee audits of all quality system categories to assess compliance to process excellence standards
- The Supplier Quality Engineer II will ensure comprehensive measurement systems to monitor effectiveness of quality and reliability systems to identify, bracket, correct and prevent defects, presenting reports to management
- He/she will handle complex technical issues for manufacturing processes that are to be transferred to satellite facilities
- This individual will provide Quality Engineering support to suppliers including audits/assessments, inspection technique support, verification/validation activities, CAPA and change management
- FDA CFR Part 820 and ISO 13485 regulations/standards will be the focus
- Other Duties as assigned
- Bachelor's degree (B. S. in Mechanical Engineering, Chemical Engineering, or related field) from four-year College or university
- Experience including quality control of the battery or electronic devices, quality assurance work is desired
- Management experience particularly required
- Familiar with quality management tools (control chart, FTA, FMEA, etc.) and MS Office (Word, Excel and PowerPoint)
- Experience on laboratory analysis using X-Ray, SEM, ICP similar methods in lab is desired
- Experience including ISO 9001 quality management system auditing is preferred
- Communicates directly with other operational departments as necessary through oral and written presentation to assure resolution of quality related issues
- Evaluates field and internal failures by utilizing problem solving and root cause analysis tools and techniques
- Develops and maintains supplier quality history files
- Maintains up-to-date supplier capability and rating systems. Communicates with suppliers to resolve material problems
- Participates in the development of both the short and long term corrective action plans, and follows-up on corrective action response for rejected materials
- Reviews new design releases or process changes and coordinates adjustments as necessary
- Participates as the quality engineering representative on project teams
- Participates in the development, maintenance and improvement of the in-house ISO QS9000 program
- Participates in the implementation of statistical quality control tools
- Develops inspection instructions and methods to support receiving activities
- Coordinates and establishes classification of defects and critical inspection criteria with management input
- Provides the Layout Technician with prioritized work assignments
- Provides instruction and assistance to Quality Assurance personnel in the proper selection, use and care of gauges and other precision inspection equipment
- Distributes and maintains blueprints, Engineering Change Notices (ECN) and purchase plans to appropriate personnel within the Company
- Years of Experience:5>7 years
- Education Standard: Bachelor’s Degree
- Education Type: Engineering-General
- Ensures theSupplier Qualityfunction operates according to procedures and provides direction to other departments. Is a champion of problem solving and root cause analysis activities with suppliers and customers to eliminate recurrence of non‐conformances
- Review and approves supplier records including but not exclusive to: contracts, quality plans, change requests, SCARs/CAPAs, NCRs, verification and validation protocols and reports. Manages the Material Review Board meetings, Supplier Review Board meetings and other critical decision-making meetings as required to define Suppliers roles, responsibilities and effectiveness
- B.S. Engineering/Operations Management, Biological Sciences or equivalent
- Lead auditor training and certification preferred
- Bachelors Degree in engineering or technical discipline
- Minimum of 3 years experience in manufacturing, design, quality assurance or regulatory assurance
- Proficiency with Microsoft Excel spread sheet development and analysis
- Effective problem solving, root cause analytical skills to lead and influence others to drive change (cross-functionally and globally)
- Willing to travel domestically and internationally up to 25% of the time
- Certified Green Belt (Certified Black Belt preferred)
- Experience with metal fabrication, plastic injection molding, and/or mechanical commodities
- Demonstrated expertise to effectively communicate within all levels of the organization with respect to production and process controls; corrective and preventive action (CAPA), complaints and risk management; product quality improvement using tools such as six sigma, FTA, PFMEA, etc
- Manage supplier control from a Quality Assurance perspective, which includes
- Proficient knowledge of supplier/purchasing control requirements as related to various QMS standards and regulations
- Knowledge of supplier relations from a Quality and/or Sourcing perspective
- Skilled at reporting metrics showing performance and trending; advanced data analysis skills a plus
- Ability to manage numerous priorities and activities in parallel (project management)
- Ability to review current processes and implement productivity and compliance improvements
- Strong “people skills” to be able to deal with various personalities and levels within and outside of the organization
- Excellent verbal and written communication skills; ability to write reports required
- Excellent organizational skills and be detail oriented
- 1) Manage supply network related activities & Ensure zero defect material and services flow for the facility from source to dock and additional required points
- 2) Supplier Quality Performance Reporting
- 3) Zero Line Stoppage
- 4) Supplier & Process Partners Collaboration
- 5) Supplier Process Audit
- 6) PPAP & Packing Adherence
- 7) RCCA & 8D
- 8) Rework Support & COPQ / Warranty
- 9) Supplier Tooling Validation
- 10) CQMS Audit
- 11) ETQ - Transformation - Implementation
Product & Supplier Quality Engineer Zep Solar Resume Examples & Samples
- Devise and implement methods and procedures for inspecting, testing, and evaluating the reliability and performance of products and processes for Zep and SolarCity
- Act as a key member of the HiP team for assigned projects
- Complete and establish Quality Plan requirements as outlined by Quality team in the HiP projects, such as print GD&T review, review/feedback on Critical Dimensions or aspects on prints, Inspection check sheet preparation, Measuring system plan, FAI process instruction and completion, MSA, Pre-production plan, process control plan, Production ramp up plan and sample inspections, Inline critical dimension/aspect checks, self-certification of suppliers
- Create and maintain company quality documentation, such as quality manuals, quality procedures, etc
- Work with TO team members to perform FMEAs and PFMEAs on new products. May lead some projects FMEAs as necessary
- Maintain PLM status for Quality certifications and inspections
- Perform and coordinate quality/inspection activities with Solar City or ZEP suppliers, technology licensees and other 3rd parties
- Evaluate production of modules, Inverters, Module level electronics, BOS, other components, and provide verification of product compliance with specifications
- Develop specifications for any purchased components working together with SC Purchasing. Ensure that contracts include reference to meeting all supplier quality specifications and procedures as condition of doing business
- Write quality specifications for product specific needs as required
- Study product field failures to create pareto of issues, understand root causes, work with suppliers to address and drive issues to zero
- Perform pre-shipment inspections of modules, Inverters, Batteries, Module level electronics, other BOS at supplier locations
- Coordinate with Zep Technical Operations, SolarCity, and suppliers relating to quality performance, trends, and corrective action
- Track supplier performance and optimize Inspection frequency based on dpm outcome
- Verify compliance and effectiveness of supplier quality systems by performing supplier audits and surveys
- Initiate programs to improve supplier performance including supplier survey and supplier corrective action programs
- Implement best practices through training with supplier for enhanced quality systems
- Insure proper certification and testing completion prior to each phase of production
- Responsible for the specification and validation of inspection tools and gages for suppliers
- Handle process improvements at supplier facilities backed up by SPC data (Cp, CpK, P Chart, Xbar, etc.)
- Ensure timely resolution of supplier failure, corrective actions and preventive actions. Drive resolution through weekly meetings with supplier
- Manage suppliers’ performance and conduct audits
- Prepare QA reports on a timely basis
- Degree in Quality/Electrical or Mechanical Engineering or related field
- Knowledge of metrology, GD&T standards, Aesthetics, Finishes
- Knowledge of electrical systems, electronics, and failure modes of electronics
- 3+ years of experience in quality engineering in a related industry
- Analytical skills using Excel, JMP, SPC. Versed in problem solving techniques
- Must be a self-starter and adaptable to a rapidly changing environment
- Candidate should reside in Bay area
- Ability to travel to local and international suppliers, including to China, may be required
- Ability to speak, read or write in Chinese desired, but not required
- Excellent written and verbal communication skills required
- Excellent customer service skills required
- Regular, reliable and predictable attendance required
- Ability to work well with others in a collaborative team environment
- Must be able to successfully pass a pre-employment criminal screen
- Minimum Education level: College degree in science or engineering
- Minimum Years of Experience: 3 years in QA related work
- Required Language Proficiency: English and Korean
- Understand US FDA requirements and Korea FDA requirements
- Good fundamental knowledge on Total Quality Management System
- Understanding of Statistical Process Control and other quality improvement
- Responsible for planning, organizing, and performing all supplier quality related activities delivering on-time PPAP and flawless launch for responsible components
- Lead project teams related to incoming quality issues, CAPA, cost reduction, and quality system excellence driving process and systemic quality improvements
- Drive supplier quality improvement work with supplier and request support from the Supplier Development group in case of major / recurring supplier quality needs
- Assist suppliers in quality assurance processes and procedures to facilitate continuous improvement of supplier and product performance
- Perform and/or participate in source qualification by performing quality and manufacturing system surveys and special process surveys
- Take first action to protect the plant from non-conforming parts from suppliers
- Coordinate containment activities, initiate controls and safeguard replacement deliveries when needed
- Internally, report and follow-up on deviations. Initiate, follow-up and close deviation report requests
- Reduce quality nonconformities, improving quality metrics
- Prepare, distribute and communicate supplier quality data/information to various stakeholders including PPM data for tracking and improvement
- Participate in design reviews of new products
- Serve as the Voice of the Customer within the organization in relating to supplier quality issues
- Bachelor’s degree in mechanical engineering or related discipline
- 6 years of experience in various functions of quality, manufacturing, customer relationship management
- Six Sigma Green belt certification desirable
- Conduct audit for new supplier development, verify the effectiveness of the cross-functional supplier selection process to ensure that the best possible suppliers are selected under consideration of the Total Cost of Ownership approach
- Applies Advanced Quality planning techniques such as SPC, FMEA, Control Plan, and Measurement System Analysis to evaluate supplier’s manufacturing ability to produce products with a stable process
- Works with supply base to assure product is submitted for approval to support new product development and launches (PPAP/FAI process)
- Perform supplier quality role in PROLaunch for new product introduction, work out Supplier Production Control Plans, Supplier Production Part Approval Documentation, Supplier Process Risk Assessment & Mitigation, Supplier Error Proofing Plans
- Deploy Eaton EQS and Supplier Excellence Manual for custom made part and to strategic suppliers
- Supplier DPPM analysis, set up metrics to measure supplier quality performance, drive supplier for continuous quality improvement. Monitor supplier corrective actions
- Drive Close Loop Corrective Action for Material issues
- Provide Supplier Training on SSA, QPA, PFA, FAI, ProLaunch/PPAP, 8D, EQS, and SEM
- Conduct audit for new supplier development and annual audit for existing supplier
- Develop Process Quality Control Plan for components with suppliers; Lead risk assessments and create product quality control plans with suppliers
- New Part Qualification and Improvement
- Conduct Quality Process Audit for supplier continuous improvement
- Perform Focus 5 supplier improvement, conduct QBR meeting with strategic suppliers, focus on establishment of supplier capability and preventive quality system
- Support supplier to develop ITP (inspection test plan) for important parts and ensure supplier follow it with proper inspection gauges and correct inspection method
- Run and track EQS and SEM for critical suppliers, provide supplier management tools training and mentoring to the suppliers for quality awareness, 8D tools, PPAP/FAI, SPC, Lean & six sigma tools, support all suppliers to build Lean and six sigma system, improve suppliers’ process capacity
- Involve in plant EBE, ELSS, EQS assessment and customer and external audit, support across the organization to drive short-term and long term business improvements in supplier management
- Support plant to deploy improvement for agency’s quality management system, select top suppliers to conduct onsite assessment and support supplier build the quality management system
- Must be a Mechanical Engineering degree holder or equivalent. With 5-10 years of related experience
- Knows how to deal, negotiate with customer, supplier and management
- Quality system and Production process audit skill
- Understanding and Implementing MSA and SPC
- Has an awareness of the basic tools of AQP, e.g., FMEA, Control Plan, Process Capability, etc
- Has a basic understanding of the industry / customer specific Advanced Quality Planning processes and product validation and approval requirements
- Technically incline and knows how to interpret drawings / diagrams
- Measures and reports metrics associated with their own work
- Is able to create and manage quality improvement plans at supplier site
- Evaluate the supply base using Supplier Quality Assessment techniques – audit, questionnaire, metrices, etc
- Approve Suppliers by conducting “desktop” and/or on-site audits of the suppliers Quality Management System
- Ensure that Regulatory, Customer and Business requirements are flowed to suppliers and sub-contractors
- Develop and deliver training programs (internal & external)
- Participate in resolving issues with suppliers and sub-contractors relating to manufacture, quality, handling and communications
- Authorise concessions in line with Company & Customer requirements
- Update Supplier Metrices
- Maintain and update supplier or sub-contractor specifications and standards
- Maintain Supplier SPC records
- Maintain Supplier records/approvals on ERP system
- Provide external and internal Auditing with authority to accept or reject proposed suppliers
- Experience in an aerospace manufacturing environment, with a sound working knowledge of aerospace regulatory and quality requirements EASA Part 21 and AS/EN9100
- Sound practical experience with Excel and Word. Ability to learn the use of new business software
- Shall have tack and capacity to meet with Senior Management with understanding of the varying conventions applied
- Qualified Auditor
- Degree/BTEC/HND in engineering related discipline – experience may be taken in lieu of qualification
- Utilize sound Quality engineering background to create, apply, and document supplier improvement forms
- Support receiving inspection team for current quality certification production or new production introduction in terms of process control points, parameters, related FMEA revisions
- Manage supplier related quality issues to apply kaizen activities to eliminate recorded quality failures
- Support and engage on customer claims to improve supplier related issues
- Work within an focus organizational structure that supports the focus High 5 metrics
- Responsible for quality initiatives to improved quality performance of the production
- Has a high focus on quality in his daily work on act as a role model in the team
- Coordinates plant quality initiative within focus organizations
- A Bachelor of Science in Industrial& Mechanical & Chemical Engineering degree or equivalent appropriate experience is required
- Experience in supplier performance improvement
- A thorough technical knowledge of Quality Engineering technics
- The ability to effectively supervise people and motivate subordinates, while maintaining organizational harmony and meeting scheduled deadlines
- To initiate preventive, rather than corrective quality actions
- Strong problem solving and project management skills
- Ability to collaborate with various departments within the plant or global locations
- Ability to work with functions outside of Engineering for the common good of Eaton
- Proficient application of core Quality Engineering tools/ principles, industry best practices and recognition for technical expertise (Ex.: 5Why, fishbone, PDCA, 6 sigma, Lean manufacturing, 5S)
- Update Supplier Metrics
- Sound practical experience with Excel and Word
- Ability to learn the use of new business software
- Independently conducting supplier evaluations and audits
- Utilizing process improvement tools to drive process and product quality
- Monitoring supplier quality levels and perform development activities with strategic suppliers to insure quality performance goals are met
- Process qualification - ensure supplier adherence to Work Instructions, Process Control Plans, Engineering Drawings and Specifications
- Leading supplier Continuous Improvement Teams
- Dimensional and visual final inspection & product release
- Disposition of qualifications, off-standards & discrepant material
- Develop and coordinate the implementation of PPAP, 8D, APQP as it relates to supplier issues
- Compiling and initiating Production Part Approvals (PPAP) in support of Design engineering and supplier transition efforts. This includes managing PPAP packages, reviewing engineering drawings for Critical Characteristics and assisting in Go/No go decisions through the passport process
- The incumbent should have the ability to work independently with minimal supervision
- Lead Supplier Gold Initiative
- Minimum 5+ years of experience in manufacturing/quality/engineering roles in companies embracing Lean or Six Sigma principles
- Proven leadership experience, particularly in quality improvement, manufacturing operations/quality and supplier quality
- Root cause analysis, quality escape/spend reductions and prioritization of potential field issues
- Understanding with implementation of Process-Certification / statistical process control , and ACE
- ASQ Certified Quality Manager or Certified Quality Engineer (preferred)
- Knowledge and implementation of Shainin Red X and Six Sigma methodologies, certifications a plus
- Strong understanding of fabrication equipment, manufacturing, engineering and quality operating systems and how they all inner-relate
- Experience working with suppliers outside of the US a plus
- Ability to lead change initiatives and drive process excellence
- Strong communication skills with a history of influencing multiple levels of the organization and positive interface with customers
- Previous experience with a union environment strongly preferred
- Familiarity / experience in implementing an ISO9001, AS9100, or TS16949 Quality System
- Previous aerospace/aviation industry and Nadcap experience desirable
- PPAP, FMEA and Control Plan experience desirable
- 5+ years of supplier quality/development and/or quality engineering experience and knowledge of AS9100 preferred
- Plans and conducts scheduled assessments of suppliers to assess compliance with Boston Scientific requirements. Includes assessment preparation meetings and scheduling in advance of site visit. Conducts and confirms follow-up actions on Supplier Quality
- Communicates quality issues to suppliers as needed and provides assistance to develop corrective actions
- Reviews, understands, and implements updates related to BSC Policy changes. Includes incorporation of this information into corporate and divisional programs through document reviews, protocol reviews, validation reviews, and training programs
- Participates with Corporate and regional Supplier Quality organization on policy/procedure/ guideline development. Includes generation, review, and implementation of these documents
- Works with global partners to assess and address material quality issues
- Generates Quarterly Supplier Performance Reports
- Tracks and trends supplier performance, taking remedial action as needed
- Supports the development of Supplier Quality infrastructure by working with management on the development and enhancement of critical processes and procedures, as well as training and mentoring less experienced staff
- Support material investigations related to issues identified at incoming inspection, manufacturing, or other feeder systems
- BS degree in Engineering with 2-4 years related experience
- MS degree in Engineering with 0-2 years related experience
- Medical device industry
- Experience with or lead auditor certification to ISO13485, 9001
- Experience with auditing supplier quality systems
- Experience in working with mechanical component fabrication suppliers
- Provides guidance to BSC Purchasing and Engineers in applying supplier quality system requirements
- Reviews and approves all BSIL material and component specification drawings
- Bachelor’s Degree in Engineering, Science or Quality Assurance, min HETAC level 8 essential
Plant Supplier Quality Engineer Resume Examples & Samples
- Ensure the standardized Vehicle Group processes for the supplier quality management system are established, implemented, measured, and maintained within the plant
- Utilize supplier WISPER system and Eaton Supplier Excellence manual guidance within the plant
- Support the Supplier PPAP process by reviewing and approving supplier PPAP submissions, including the coordination of part samples for dimensional reviews and assembly trials
- Manage notifications (DMRs), responsiveness, containment, root cause determination, corrective action, and closure of supplier quality issues. Control scorecard (Supplier DPPM) and lead the Cost of Poor Quality process
- Identification of the most disruptive suppliers and notify divisional SQEs
- Support flow line teams to lead continuous improvement activities
- Receiving and Inspection process owner, which includes monitoring supplier SPC of critical to quality characteristics
- Support correction of supplier receipt errors in WISPER
- Support both internal and external audits
- Support the manufacturing engineering team on continuous improvement projects through the plant
- Other job duties as deemed appropriate
- Minimum of 3 years’ experience working with Quality systems in a manufacturing environment
- Must be legally authorized to work in the United States without company sponsorship is required
- Experience with a large, ISO/TS-16949 certified manufacturing operation
- Experience with various quality processes and systems, to include Production Part Approval Process (PPAP), Advanced Product Quality Planning Process (APQP), Design and Process FMEA, and Statistical Process Control and Capability (SPC)
- Must be proficient with advanced Excel tools and software needed to analyze and report data
- Working knowledge of process auditing techniques to ensure compliance to defined quality requirements
- In-depth knowledge of structured team problem-solving techniques such as 8D or A3
- Ability to read and understand engineering drawings and tolerances, standards, and specifications
- Knowledge and demonstrated ability to use continuous improvement tools and methods
- Effective interpersonal skills to work with and lead cross-functional teams
- Ability to promote and champion change
- Strong communicator - written, verbal, and presentation
- In partnership with Purchasing, revise and maintain the currency of the Supplier Selection and Approval procedure, to include a disqualification process
- Conduct oversight of Supplier Corrective Action (CA) activities, to include ensuring a proper level of effort prior to CA closure
- Develop and implement Supplier Quality rating system in order to support an overall Supplier performance metric inclusive of Delivery and Quality
- Drive trend improvements on the Supplier Quality metric in support of strategic business objectives
- Work collaboratively with Purchasing and Suppliers to reduce Supplier-responsible rejections, particularly in instances of such material found in the production areas
- Develop and maintain close lines of communications with Suppliers in order to foster and promote partnering relationships
- When business interests warrant, conduct Supplier development activities that bring a Supplier to an acceptable level for inclusion on the Approved Supplier List
- Visit supplier facilities/locations when required in order to improve relationships, follow up on corrective action validation and/or due to quality spill
- Develop systems within Mason to establish processes for others to follow which could be based on assigned projects
- Act as a liaison for the production areas on matters related to Supplier-provided material
- Identify, submit, and facilitate technical changes that will make improvements in quality, cost, and delivery
- Develop and deliver public presentations as appropriate for all levels within the organization or at supplier location
- Maintain the highest ethical standards, even when challenged from above
- Understand and live by Esterline’s ethics and business conduct policies
- Perform other duties and tasks as directed by the direct Manager
- Working knowledge of blueprint interpretation in accordance with ANSI/Y-14.5
- Solid command in the use of Microsoft Office Suite (Excel, Power point, Word, Access)
- Proficiency in process control tools (SPC, Process Capability, DOE, etc)
- Working Knowledge of PFMEA (Process Failure Mode and Effect Analysis)
- Working knowledge in systematized approach to corrective action methodologies (8D, RCCA, 7 Step, CAR, etc.)
- Comfortable in making decisions in a rapid paced, forward evolving environment
- Unquestionable commitment to, and ability to facilitate actions in, continuous improvement efforts
- Ability to influence actions at Supplier facilities in support of delivery and quality objectives through strong interpersonal skills
- Proficiency in leading cross-functional teams
- Working knowledge of ISO 9001, AS9102, AS9100 standards
- Proficiency in Minitab
- Knowledge of Lean manufacturing methodologies
- Bachelors degree
- Four to Six years of progressive experience working in a Supplier Quality Engineering capacity within aerospace or automotive environments
- ASQ certifications (CQE, CSSBB, CQA, etc.) desired
- Assist with strategic supplier development and maintenance of an active Risk Management Plan
- Ensure regular reviews for quality with Strategic Suppliers
- Prepare and provide quality presentations for supplier quality conferences and supplier product improvement teams
- Support quality function employees in the above activities
- Typically requires a bachelor's or master's degree in engineering or related discipline and six or more years of related experience with a bachelor's degree or four or more years with a master's degree. May substitute equivalent experience in lieu of education
- Perform Specification Compliance Reviews, First Article Inspections and Source inspections on electrical and electro-mechanical hardware including, PWB/CCAs, RF/Microwave devices and assemblies and cables and connectors
- Initiate Corrective Action Plans and work with suppliers, manufacturing and engineering personnel to identify root cause and ensure robust corrective actions are implemented
- Perform process and product audits alng with capacity assessments to ensure the supplier's processes are robust and capable
- Work with the Technology Domain Teams to manage key suppliers, ensure the supplier's are performing well and their capacity and capability to deliver products on time is acceptable
- Establish positive working relationships with suppliers
- Bachelor's degree in Electrical, Mechanical, or Industrial Engineering
- Six Sigma or Lean certifications
- Knowledge of statistical process control, auditing to ISO 9001 and AS9100 requirements
- Experience in IPC-610/J-STD-001, MIL-STD-883 and Geometric Dimensioning & Tolerancing are highly desirable
Associate Supplier Quality Engineer Resume Examples & Samples
- Monthly reporting & review against global KPI’s / Dashboards / targets. Presentation of date using multiple formats (e.g., pareto, trend charts, bar graphs). Insuring and monitoring of corrective action plans
- Tracking of data and information in ERP databases or spreadsheets. Communicating and presenting data to global stakeholders to drive for resolution of issues
- Leadership and maintainence of Lessons Learned Sharepoints
- Develops Global training programs to support consistent global ERP usage
- Visits Harman facilities and meets with SQA personnel to ensure a full understanding of Customer (internal & external) needs / requirements to identify process and improvement opportunities
- Associate’s or Bachelor's degree
- Minimum 2+ years related experience required
- Expert skills in word processing, spreadsheet and presentation preparation (MS Office Suite)
- Excellent working profiency in ERP systems (SAP preferred)
- Global, multi-location support experience
- Experience with statistical methods, problem solving methodologies and automotive quality management systems
- Training to client, and follow-up on APQP documentation (Control Plan, FMEA, process flow…)
- Conducting supplier assessments to improve the deficiencies found during audits or to help suppliers prepare for an OEM’s audit or a TS16949 audit
- Managing and follow-up on new product launch – APQP activities
- Leading and support of Gap Closure activities to help suppliers close open issues to meet quality system requirements of the customer
- Managing and monitoring supplier quality performance of production to ensure through-put and delivered quantity & date appropriately
- Perform incoming inspection of parts and ensures the continuous flow of quality materials to the manufacturing cells
- Champion problem solving and root cause analysis for all non-conforming parts
- Perform root cause analysis and implements corrective actions
- Report daily supplier quality metrics
- Create SCARs for parts with supplier quality issues
- Converses with suppliers if more detail is needed on part non-conformances
- Ability to set testing procedures up at supplier to ensure incoming parts meets our quality standard
- Review CARs returned from suppliers to ensure through root cause and corrective actions have taken place
- Transact parts accordingly using ERP system
- Test parts before shipping to customers
- Write EC’s and standard work as needed for changes due to supplier changes
- Ensure appropriate containment steps and corrective actions are taken place in a timely manner
- Enter supplier quality information into excel spreadsheet
- Run data analysis on supplier/part trends
- Report supplier quality information at quality council meetings
- Calculate quality scores for supplier scorecards
- Visit suppliers and conduct supplier quality audits
- Work with key suppliers in improving quality of parts
- Responsible for communicating quality issues to various stakeholders throughout the organization
- Ability to communicate complex technical issues clearly and simply. Must have strong interpersonal skills and cooperate well within a team
- Prior experience implementing root cause corrective actions and process improvements
- Proficient utilizing Microsoft Office including Word, Excel, and Access
- Ability to read drawings and electrical schematics
Principal Supplier Quality Engineer Resume Examples & Samples
- Demonstrates intermediate knowledge of quality engineering policies, principles and best practices
- Demonstrates intermediate knowledge of FDA/ISO requirements
- May act as mentor to less experienced team members
- Applies statistical sample size calculations to work for quality determination on projects of intermediate scope/complexity
- Applies intermediate understanding of regulatory requirements (cGMP, FDA, ISO, etc.) to support work with minimal supervision
- Writes test protocol, tests, collects data, and writes reports to validate against plan to ensure product is used as intended
- Applies knowledge and skills to a wide range of standard and non-standard situations
- Works independently with minimal guidance
- Bachelor's degree strongly recommended, advanced degree preferred
- 4-6 years experience
- Experience in respiratory care or with the manufacture of electromechanical devices is desirable
- BS degree or equivalent in Business Management, Engineering, other related field of study,
- Minimum 2 years of experience in QA in Medical Devices, including quality systems, standards, metrics, and tools
- Demonstrated knowledge and expertise in: NPD, supplier development, implementation planning and supplier training
- Ability to build quality system with suppliers from ground up at the supplier
- Mastery of medical device quality systems (specifically ISO13485, CFR Part 820 and Part 211 regulations)and applications is required
- DFSS/DMAIC Six Sigma Black Belt required, Lean Leader preferred
- Certified External Quality Auditor (CQA) certification and experience in auditing suppliers and resolving findings required
- Demonstrated ability to work successfully in emerging markets, leveraging interpersonal, communication, and technical skills to optimize results
- Ability to link customer needs with business
- Strong coaching and facilitation skills
- Mastery of software programs - Microsoft Word, PowerPoint, Excel, Project, Minitab
- BS in Electrical, Mechanical, Chemical Engineering, or related technical field
- 2+ years of experience in an R&D or Manufacturing environment
- 2+ years Supplier Quality management experience
- Strong written and verbal communication skills with the ability to communicate effectively in multi-discipline environment, and across cultures and levels of organizations
- Strong leadership skills with the ability to influence and affect process improvements and facilitate completion of tasks/projects
- Very strong ability to work autononamously and be self-directed
- Strong project management skills and ability to organize and manage multiple priorities
- 50-75% travel required - Domestic and International
- Medical Device industry experience strongly desired
- Certified Lead Auditor (RABQSA, ASQ, or equivalent) with application experience Certified Six Sigma a plus
- (DMAIC) Green Belt desired, Black Belt preferred
Design Supplier Quality Engineer Resume Examples & Samples
- BS in engineering or science. MS desirable
- 3+ years of experience in Quality Engineering in medical device industry
- Experience in related areas, e.g. R&D or Manufacturing may also be applicable if experience includes work responsibilities listed above
- Strong critical thinking, technical writing and documentation review skills
- Ability to read and interpret engineering drawings and specifications
- Experience in application of statistical and analytical methods such as DOE and capability analysis
- Proficient in Design FMECA and Design Verification and Validation activities
- Experience and success working with cross-functional teams
- Proficient in MS Word and Excel, and managing electronic data files to maintain required documentation and write technical reports
- Ability to learn on the job quickly and apply new knowledge immediately
- ASQ certification in Quality Engineering desirable
- Familiarity with applicable standards or regulations such as IEC 60601, ISO 13485, ISO 14971:2012, CFR 820 etc
- Experience with Minitab or other statistical software packages
- Experience in making critical decisions that prioritize patient care/safety and FDA regulations while supporting smart business decisions
- Experience with Class III devices desirable
- Bachelor’s Degree preferably in a scientific or technical field
- Minimum 3 years’ experience in a Supplier Quality, Quality Engineering or Reliability Engineering function
- Demonstrated track record of effectively influencing and negotiating with suppliers and leading effective/successful change initiatives
- Demonstrated knowledge and experience in: supply chain management and supplier development, risk/issue management, implementation planning, training/communication, scope management
- Working knowledge of inspection and test techniques, quality assurance procedures, statistical analysis, product usage and device regulations
- Working knowledge of medical device quality systems and applications
- Demonstrated ability to work successfully in complex and emerging markets, leveraging interpersonal, communication, and technical skills to optimize results
- Strong ethical standards
- Good problem solving skills
- Bachelor’s degree in Engineering or Scientific field and 2+ years of work experience in engineering, quality assurance and/or supplier quality OR a Master’s degree in Engineering or Scientific field and 1+ year of work experience in engineering, quality assurance and/or supplier quality
- Experience working in medical device, biotechnology, automotive, aerospace or pharmaceutical industry
- Experience with Process Validations OR Test Method Validations (examples: IQ, OQ, PQ, and TMV)
- Master’s degree in Engineering or Scientific field with an emphasis in Engineering, Materials, Quality Assurance, or Quality Systems
- 3+ years of work experience in engineering, quality assurance or supplier quality
- ASQ CQE, ASQ CQA, or ISO 13485 Lead Auditor Certification preferred
- Experience with polymers, plastics, electrical, chemcial, mechanical and/or electro-mechanical commodities and injection molding is desirable
- Knowledge with PPAP is also desired
- Knowledge of the Medical Device regulations (21 CFR 820 and ISO 13485)
- Effective verbal and written communication skills in order to effectively communicate with internal customers and suppliers, and to develop and present communication plans and strategies
- Complete audits of new and existing suppliers per Stryker requirements to ensure conformance and compliance
- Identify and issue supplier corrective action requests (SCARs), as required, and drive suppliers to identify, correct, and prevent the root cause
- Drive timely closure of SCARs through the CAPA system
- Provide input to the creation of supplier contracts (e.g. Quality Agreements, Change Control, etc.)
- Participate in and provide feedback to the supplier selection process
- Visit suppliers to resolve issues as needed
- Obtain process performance data from suppliers (e.g. SPC, FPY, fallout, etc.)
- Analyze internally generated supplier performance data and metrics (e.g. DPM, failure modes, trending, etc.)
- Partner with other engineering functions as needed to resolve (non-audit related) supplier non-conformances
- Partner with other engineering functions to execute supplier change requests related to manufacturing, process, or supplier requested changes
- Identify internal requirements and external laws, regulations, guidance’s and standards applicable
- Interpret applicable internal and external requirements and incorporate into requirements for use in Abbott business processes
- Identify areas of potential noncompliance within Abbott
- Review and update the Quality System Manual as needed
- Educate functional areas on quality system requirements
- Participate cross functionally and across business units to standardize Abbott business quality system policies and procedures
- Mediate resolution of interdepartmental and cross business unit process conflicts
- Identify qualified external consultants and experts in government, collaborating with them to insure correct interpretation of requirements
- Collect business process data from different parts of the company for analysis
- Act as an expert resource in specific requirement knowledge for Abbott
- May be responsible for identifying training requirements, programs, and tracking systems
- Manage supplier operation performance
- Jointly work with Commodity Managers / Supplier Relationship Managers to develop and implement commodity strategies
- Provide technical support and qualify supplier process for New Product Introduction
- Bachelor Degree or Master Degree in Mechanical Engineering or the equivalent
- Experience in supplier management, mechanical design and manufacturing process
- Excellent analytical problem solving skills
- Demonstrated the abilities to produce useful engineering solutions for
- Excellent speaking, listening, writing and reading English skill, good reporting and presentation skills
- Demonstrated leadership skills and planning capability skills
- Demonstrated effective interpersonal skills and interfacing with teams that are both located locally and globally
- Lead or provide support to investigations to determine root causes on material quality issues and initiate/ensure corrective and preventive action plans are developed and executed
- Interface with Suppliers/CM (Contract Manufacturer), Engineering/ Manufacturing/ Quality Assurance/ Procurement departments to drive for quality improvements, specifically on incoming rejects, workmanship defects and primitives failures
- Drive Quality review with supplier/CM for improvement to meet quality expectation
- Constantly review quality processes and suggests improvements that can be implemented to improve performances
- Manage Supplier/CM through continuous improvement activities
- Responsible for the qualification processes for suppliers, including new supplier evaluation, audit programs and supplier approval programs
- Work closely with Procurement and Engineering departments to identify new suppliers for evaluation
- May be involved in providing training
- EQOS Health Assessment
- Bachelor's degree in Mechanical, Chemical or Manufacturing Engineering with work experience in supplier quality
- ASQ Certification or equivalent strongly desired
- Ability to work independently having strong organizational skills
- Perform thorough supplier audits and assessments to identify opportunities for process and product improvements
- Monitor and evaluate supplier process for compliance to purchase order and engineering requirements
- Improve product quality by ensuring proper inspection and drawing requirements are communicated, understood and deliverable
- Update supplier records and performance metrics; produce supplier reports
- Provide Manufacturing and Quality with timely investigations into supplier quality issues
- Work with Design, Manufacturing and Quality to define process parameters and criteria to ensure supplier’s process is capable of meeting product requirements
- Promote the use of continuous improvement techniques such as Lean, Six Sigma, Poka-Yoke, Measurement System Analysis and Process Failure Mode and Effects Analysis
- Facilitate root cause analysis and corrective actions of supplier quality issues
- Gather and analyze supplier quality data to identify process improvement opportunities within the supply chain
- Report on key performance indicators
- Conduct benchmarking studies to determine best practices/designs
- Undertake personal continuous training and development
- Master’s degree in Engineering, Mathematics, Applied Statistics or Business
- Knowledge of PPAP
- Six Sigma and/or Lean Manufacturing certified
- Knowledge of mechanical, electrical, pneumatic systems
- Effective listening skills
- Ability to present data effectively
- Self-starter with ability to work independently
- Knowledge of measurement techniques
- Skills: organizational, communication, leadership, personal computing, performance management, continuous improvement and problem solving
- Proven experience of working in a supply chain organization
- Preferably previous experience as a supplier quality engineer or supplier developer within a technology company (ideally mechanical/aerospace)
- Proven experience of driving root cause with Suppliers
- Proven background in Quality Assurance and thorough understanding of Quality tools and techniques
- Understanding of key aerospace Quality Standards such as AS/EN 9100, AS9102 and NADCAP
- Good technical engineering knowledge and ability to read engineering drawings
- Self starter with a desire for problem solving and process improvement
- Professional conduct and good communication skills to influence both internally and externally
- Problem Solving & Creativity
- Business Operations, Systems and Processes
- Managing Projects
- Manage supplier approval processes, identifying, certifying, and auditing suppliers,
- Drive supplier quality management in line with company control procedures, and relevant regulatory standards e.g., AS/EN 9100, AS9102
- Drive prioritized supplier non conformance management and root cause analysis
- Develop suppliers to more effectively support Cobham at lower costs over time
- Ensure Quality Assurance for new and existing suppliers including audits, source inspections, First Article Inspection sign-off and change control process management
- Ensure accurate flow down of Quality requirements to suppliers throughout Product Lifecycle
- Improve supplier Quality Metrics by driving improvement plans with suppliers
- Development of supplier capability via strategic and tactical improvement activities
- Develops, applies, revises and maintains supplier quality standards
- Analyses, tracks and reports discrepancies and corrective actions taken when vendor products are rejected/returned on receipt or fail post acceptance
- Participates in First Article Inspections at suppliers
- Participates in Continuous Improvement Projects
- Co-operate with management to meet the employer’s legal duties and take reasonable care of their own health and safety and that of others who may be affected by their acts or omissions
- Analyze and verify supplier quality system implementation and process methods and procedures for manufacturing, testing and inspecting the quality level of products
- Review supplier manufacturing documentation ensuring the necessary criteria and provisions are incorporated to permit effective inspection, testing and use of materials
- Analyze reports and product to be returned to suppliers; initiate correction action for procedural, product or process deficiencies
- Analyze supplier failure analysis root cause determination and corrective action to assure the action is contributing to supplier process improvement
- Review in-coming inspection rejections of supplier material, parts or products identifying rejection trends observed and communicating these to suppliers
- Interface with buyers resolving supplier procurement quality issues
- Interface with engineers resolving design and manufacturing related issues
- Participate in safety training and actively comply with safety policies and practices
- Improve and maintain 5S in SQA area, make suggestions for improvements
- Participate in Lean/Six Sigma activities in own work area as well as events for other areas to enhance cross-functional problem solving
- Collaborate in team meetings and activities, including SET team support as appropriate
- Issue regular supplier performance reports to key suppliers, visit suppliers as necessary accomplishing supplier process audits and to qualify them as “Approved Suppliers”, participate with suppliers improving supplier process, procedures and product quality
- Accomplish Customer Source Inspection (CSI) at suppliers when required
- Input SAP Material Master data for Quality related fields
- Bachelor’s of Science degree
- Experience with manufacturing processes such as soldering, plating, machining, etc
- IPC-A-610 certified
- LEAN/Six Sigma
Powertrain Supplier Quality Engineer Resume Examples & Samples
- Team up with engineering and supplier to alleviate discrepancies in product specifications and evaluate cost reduction opportunities
- Bachelor of Science in Engineering from an ABET accredited university
- 5+ years of work experience in quality, engineering, or manufacturing
- 3+ years of experience within Powertrain areas
- Audit supplier's quality systems and manufacturing processes, including critical production processes at sub-tiers
- Establish close relationships with assigned suppliers and actively drive continuous improvement activities following the FCA Foundational Principles
- Participation in launch teams for purchased components within the vehicle platforms
- Assist in educating suppliers on FCA systems and requirements
- Bachelor of Science degree in Mechanical Engineering or Electrical Engineering from an ABET accredited university with a minimum 3.0 GPA. A bachelor's degree in Aerospace/Aeronautical, Biomedical/Biomechanical/Bioengineering, Chemical, Materials, Metallurgical, or Mechatronics may also be considered
- Prior Internship experience in Quality, Supplier Quality, Engineering, Manufacturing or a related field
- Creative problem solving ability
VIE Advanced Supplier Quality Engineer Resume Examples & Samples
- Masters degree in engineering with a specialisation in quality management
- Results orientation with strong written and oral communication skills
- International mind set, overseas experience will be a plus
- Bi/multi-lingual (English, German mandatory)
Advanced Supplier Quality Engineer Resume Examples & Samples
- Deploy APQP related to the development phase of Bought-Out Parts and Raw materials following Faurecia’s purchasing requirements and within the programs timing objectives
- As an extended core team member, complete and deliver required evidence detailed in the Faurecia Program Management System on-time per development program training
- Manage the process qualification (trial run at rate & process audit) with plant Supplier Quality Assurance (SQA) Engineer and program quality engineer
- Follow the BOP supplier APQP progress utilizing the ePPAP system and take decision in collaboration with the program team
- Facilitate effective communication between the supply base and FIS program functions (engineering, logistics) to ensure program objectives are met in a timely manner
- Complete monthly reports per departmental requirements
- Manage the process qualification (trial run at rate & process audit) with plant Supplier Quality Assurance (SQA) Engineer and Program Quality Engineer
- Follow the APQP progress with the status report and take decision in collaboration with the program team
- Conduct supplier panel assessments in accordance to the commodity / the process & technology responsibilities
- Masters degree in engineering with a specialisation in Quality
- Experience in a comparable position in an industrial environment
- Results oriented
- Bilingual (English and German required)
- Manage the process qualification(trial run at rate & process audit)with plant Supplier Quality Assurance (SQA) Engineer and program quality engineer
- Minimum 3 years experience as an ASQ in an industrial environment
- Minimum bilingual (German-English)
- Supplier Process &Production Control
- Supplier components and process validation
- Non-conformity cause analysis
- Supplier Quality Control
- Annual supplier audit plan and implement
- Supplier process Audit R@R
- Complain for the non-conformity from suppliers
- Supplier quality issue solution/accidents follow up, solution validation
- Production Quality Cost Control
- Localization under the leading of Project manager
- Participate in the PFC,PFEMA,Control Plan creation and review, and be charge of component control
- Manage the process qualification(trial run at rate&process audit)with plant Supplier Quality Assurance (SQA) Engineer and program quality engineer
- Conduct supplier panel assessments in accordance to the commodity/the process&technology responsibilities
- Bachelor's degree in engineering with a specialisation in Quality
- Master's degree in Engineering with a specialization in Quality
- Minimum 3 years experience in Quality in an industrial environment
- Fluent in English, other languages would be appreciated
- Defines, develops and implements Supply base strategies that drive improvements is supplier selection, development, and leverage across customer programs for quality improvements and cost savings
- Provides regular updates to Quality Engineering Manager on the execution of the strategy
- Provides support for NPI activities by participation in the AQP process as required
- Ensures that all production critical supplier issues are resolved in a timely manner, and corrective actions are implemented
- Defines and develops the appropriate Inspection Plans and Inspection Methods, directs Receiving Inspection Auditors
- Defines and develops the inspection processes via inspection aids and instruction guidelines
- Ensuring ongoing site supplier evaluation is performed. This would be achieved by using site information collected from Receiving Inspection, MRB, Customer Returns, SCAR database and by liaison efforts with customer work cells. Performance will be reported internally, to the supplier, and to the customer where applicable
- Monitors and drives PPM issues with the supply base in addition to helping them achieve “Dock to Stock” certified with Jabil (in accordance to the vendor performance system)
- Reviews all supplier discrepancies. Coordinates and tracks the corrective/preventative action effort
- Proactively communicate information or issues that may impact the product costs or manufacturability to all affected departments
- Provides insight and assistance of implementing and maintaining Process Improvement and Optimization concentrating on proactive methodologies with the supply base
- Leads SCAR – Supplier Corrective/Preventive Action process for problem resolution and continuous improvement, including critical analysis of supplier DOE, CPK, Gauge R&R studies
- Comply and follow all procedures within the company security policy
- Site RoHS subject Matter Expert
- May perform other duties and responsibilities as assigned
- 5-7 Years of experience in Quality or Manufacturing Engineering
- Or an equivalent combination of education, training or experience
- Drive standard process technology and set requirements for supplier
- Support special Process Audit Modules - (Molding / mold tooling / stamping/ etc.)
- Engage in Focus Supplier Program - Rolling top 5 Standard tools & Cross functional
- Lead Continuous Improvement activities of supplier (etc. Scorecard Reviews)
- Create a flexible Lean Manufacturing environment at suppliers
- Get the voice of supplier
- KPI Synchronization
- Gap assessment of missing standard contracts / QAA
- Support enhancing supplier audits for robustness
- Act on New Product Stream (NPS) survey results
- Join projects and partnership for process efficiency improvements
- Assure that suppliers meet TE customer requirements
- Perform process audits
- University degree (engineering preferred)
- 3+ years experience in applying automotive quality tools according TS 16949, AIAG and VDA standards
- Experience with problem solving tools (8D, 5 Why, Ishikawa, PDCA, DEMAIC,…)
- Driving for Execution
- English on business level is a must, bilingual language beneficial
- Five or more years of experience in Quality Engineering; with three or more years of Supplier Quality Engineering experience
- Bachelor’s degree in Engineering, Quality or related technical field
- Demonstrated expertise in quality concepts, practices and procedures
- Knowledge of ISO 13485 and related quality system requirements (i.e. ISO 9000)
- Process control knowledge and implementation experience (SPC, Cpk, Gage R & R, DOE, Control Plans, etc.)
- Knowledge of and experience in problem solving implementation. Proficiency in MS Office and e-mail
- Demonstrated ability to make independent, informed decisions
- Ability to communicate in English language clearly in both written and verbal forms
- Knowledge of RoHS and WEEE requirements beneficial
- Knowledge of ESD requirements preferred
- B.S. Degree in engineering with additional hands on experience in quality engineering; Or 5-7 years’ experience in a quality related capacity
- Hands on experience on 8D, 5Y, FMEA, MSA, SPC
- Experienced in GD&T including being capable of transferring specifications and drawings into control plan/quality inspection plan and work instructions
- ISO9001 or AS9100 or TS16948 experience is essential
- Advanced Product Quality Planning (APQP) experience is preferred
- Lean and Six Sigma knowledge is highly preferred
- ASQ certification and/or a strong fabrication background is preferred but not essential, as is experience with SAP
- Active development and maintenance of QMS at dedicated suppliers
- Improving suppliers’ KPI performance based on SD EMEA strategy and goals
- Mitigate risks of supplier process induced non-quality
- Definition, training, deployment and progress tracking for implementation of continuous improvement activities for dedicated suppliers (TPM, 5S+1,OPL etc)
- Coordinates supplier production process release in liaison with Product, Transfer, and APQP Engineering departments
- Regular quarterly supplier’s performance and scorecard review
- Participation on audits at supplier’s location according to VDA, ISO TS and TE relevant specification
- Communication across departments and locations within TE Automotive
- Direct contact with supplier representatives
- Review production processes at supplier (R@R, SLP)
- Travelling relevant to business needs
- Regular reporting, data collection and analysis
- Under the direction of the Director - Manufacturing and Supplier Quality (Mexico), the Supplier Quality Engineer will provide Quality oversight and support for Elster manufacturing operations in the form of supplier quality audit and standards compliance management efforts in addition to regular line-level manufacturing quality support and oversight responsibilities. Job responsibilities include
- Drives activities for Supplier Qualification and approval. Define and coordinate recording, reporting and evaluation of all supplier quality-related information
- Manages and facilitates the supplier evaluation process. Based on performance results, defines and coordinates measures to deal with deviations between actual results and target performance and to initiate appropriate actions for achieving the defined targets
- Participate in Supplier Escalation Process and serves as a technical / communication interface to Supply Chain and Support Engineering functions
- Uses detailed knowledge of equipment, personnel and processes to advise on content of manufacturing and supplier communications (RNs)
- Works with Commodity Managers to develop preferred supply base. Interprets and clarifies supplier and manufacturing instructions related to inventory controls and management
- Gathers, correlates and interprets SQL data related to yields, failure rates and FIFO component date code management
- Supports new materials, processes and/or equipment introduction (configuration / setup, debug, modification, calibration,…)
- Work with manufacturing and supplier personnel to design / modify manufacturing and inspec-tion equipment
- Reviews Supplier manufacturing processes and collaborate with suppliers on process improvements and value enhancement opportunities. Serve as the SME for Supplier quality and continuous improvement efforts
- Identify and understand key process indicators, develop measurement methods, track, and develop action items
- Works with supply chain on findings and issues related to audits. Collects and maintains supplier performance metrics. Analyzes yields, customer problem reports (CCRP), and RMAs to identify opportunities for improvement
- Work with personnel to design / modify materials and/or component inspection equipment and process
- Serves as auditor and/or lead auditor for manufacturing and supplier audits
- Remains up to date with industry quality standards and regulatory requirements
- Interpret UL, Measurement Canada and CFE regulatory and compliance requirements (assembly, calibration, material / component selection, handling, storage, etc)
- Identify, coordinate and implement changes required to meet new / modified requirements
- Works with auditors to thoroughly understand findings and issues, and develop mutually acceptable solutions
- First line contact for issues identified in Incoming Inspection: evaluation, communication, escalation, work-arounds, etc.Drive activities for Supplier
- Six Sigma or other Continuous Improvement Methodology
- Six Sigma Black Belt Certification is preferred
- Knowledge in project management is desired
- ASQ Certification desired
- Quality tools management
- Certified Lead Auditor for ISO 9000:2008 or ISO/TS 16949
- Bilingual, English and Spanish
- Management personnel
- Experience in manufacturing/quality/engineering roles in companies embracing Lean or Six Sigma principles
- Experience in quality improvement, manufacturing operations/quality and supplier quality
- Understanding with implementation of Process-Certification/statistical process control and ACE
- Strong understanding of fabrication equipment, manufacturing, engineering and quality operating systems, and how they all inner-relate
- Experience working with suppliers outside of the U.S. a plus
- Strong project planning skills
- Adaptable to fast-paced environments with changing circumstances, direction and strategy within a diverse organization
- Familiarity/experience in implementing an ISO9001, AS9100, or TS16949 Quality System
- Processes non-conformance activities and supplier corrective action reports, when necessary, by using analytical skills and driving a 8D problem resolution approach and 5 Why root cause analysis from suppliers
- Support the SG production line and supplier related customer issues by reporting and managing resolution through existing reporting systems (Oracle)
- Reduce quality non-conformances and cost of poor quality, through the use of quality tools (SPC, Root Cause Analysis, 8D, Lean, Six Sigma, and KPI) and validate improvements through defined measurements
- Proactively and effectively work with suppliers to minimize ongoing quality/performance issues by requesting and reviewing SCAR submissions from suppliers to ensure appropriate resolution of issues and by maintaining a regular cadence of supplier quality discussions (governance)
- Conduct weekly & monthly failure & metrics analysis to detect trends and opportunities
- Drives quality improvement efforts internally and externally (supply chain base) and communicates benefits realized to upper management
- Support on-site quality system assessments to evaluate potential new Suppliers, in support of Strategic Procurement and Sourcing in selection of new Suppliers
- Provide New Product Introduction quality support by engaging early in the launch process, driving completion of the Launch Readiness Acceptance Checklist and defining appropriate qualification metrics and post launch quality expectations
- Conduct capability audits at suppliers. Monitor supplier corrective action results and ensure sustainable action plans are in place to resolve non conformances
- Support supplier development projects to enhance supply chain capability in both processes and systemic quality improvements
- Provides quality guidance and support to organizations such as Procurement, Manufacturing, and Engineering including effective use of problem-solving tools / techniques, statistical analysis and inspection equipment and techniques
- Review and make dispositions on supplier production first articles submissions, to ensure they are submitted and approved to organizational requirements
- Travel 10% to 25% of the year (domestic and/or international)
- Requires a Bachelors degree in Engineering (Electrical, Mechanical or similar preferred)
- At least 3 years of experience in supplier or manufacturing quality engineering. Experience working with electrical, electro-mechanical or mechanical assemblies is required
- Good understanding of Statistical methods, quality tools, and methodologies (DFx, SPC, APQP, FMEA, 8D, Poke Yoke, and Control Plans)
- Proficient with statistical analysis tools such as Minitab, and high level skills working with Microsoft Excel, Microsoft Word and Microsoft PowerPoint
- Knowledge of ISO 9001, ISO 13485 or TS 16949 is a plus
- Strong tactical planning and execution, effective time management and organizational skills. Project management skills are a plus
- Strong communication skills and ability to effectively deliver information to upper management levels
- Practical knowledge of Six Sigma principles. Green Belt or Black Belt certification is a plus
- Deploy APQP related to the development phase (or in current production) of Bought-Out Parts following the Group's purchasing requirements
- Monitor the Production Part Approval before the transfer to the plant and hand over to the plant SQA Engineer
- Bachelors degree in engineering with a specialisation in Quality
- Liaisons between the workcell and the supplier regarding issues with material quality Ensures that all production-critical supplier issues are resolved completely and efficiently using corrective actions Serves as the point of contact for inspection plans and inspection methods, and provide guidance to Receiving Inspection Auditors
- Evaluates suppliers on an ongoing basis by analyzing data gathered from multiple sources including receiving inspection, customer returns and MRB and communicates results to the workcell
- Performs supplier audits as necessary in compliance with Jabil and externally recognized standards (e.g ISO 9000, ISO 13485, TS 16949, etc.)
- Reviews supplier part approval submission documentation (PPAP or other) Provides documentation to perform inspection of components per Inspection Plans in SAP
- Monitors and drives PPM issues with the supply base and helps suppliers achieve “Dock to Stock” certification with Jabil
- Drives supplier selection strategies to develop a supply base that can be used across multiple customer programs and yield cost savings
- Proactively communicate information or issues that may impact the product costs of manufacturability to all impacted departments
- Be familiar with textile manufacturing processes, implement effective quality control measures
- Understand product fitness-for-use in conjunction with the Product Specialist Function in order to ensure raw materials meet the needs of our manufacturing and the end user application
- Partner with Process Engineering to understand the impact of process variables on product attributes to drive appropriate improvements with suppliers
- Monitor supplier key quality metrics, partner with vendor to drive continuous improvement
- Work closely with suppliers for trouble shooting any raw material quality issues, and make solid cause & effect analysis and corrective and preventive actions
- Manage changes with suppliers effectively to ensure product performance stability and capability
- Bachelor & above degree in textile qualification
- Minimum 5 years working experience in the textile industry
- Strong analytical thinking and problem solving skills to complex issue, able to develop and implement solutions
- Good knowledge of ISO9001 requirement and extensive auditing experience
- Demonstrated success in working with cross functional teams in a multi-culture environment
- Effective communication in both Mandarin and English
- Project management skill & experience (the ability to initiate, plan and drive projects to completion) is a plus
- Willing to travel in the AP region
- Participating in the selection and qualification of production suppliers through the use of rationalization / scoring techniques, and leading supplier certification activities
- Leading supplier development projects / activities
- Providing updates and presentations to management as necessary
- Chairing the procurement quality board (PQB) meetings each quarter in order to continuously review supplier performance and sustain an acceptable supply base
- Issuing corrective action requests to suppliers to address systemic issues, major non-conformances, etc
- Implementing the necessary elements of program quality plans, ensuring that quality requirements are satisfied throughout the order fulfillment process via receiving, manufacturing and pre-ship activity
- Providing technical support to the receiving inspection function. Implementing inspections for critical characteristics
- Supporting Operations, Engineering, Program Management and other functional groups by providing trend analysis and root cause analysis investigations, as well as corrective action recommendations
- Supporting program execution and new product introduction for suppliers, assuring contractual compliance internally and externally by establishing Program Quality Plans and providing appropriate inputs into Design Reviews and DPM/DFT/DFQ
- Participating in Failure Review Board (FRB) and/or Material Review Board (MRB) in order to identify supplier related yield issues, and work corrective action with suppliers
- Participating in Change Control Board (CCB) activities
- Proactively identify risks and implementing appropriate mitigation plans
- Bachelor’s degree (technical degree preferred) and five to seven years of experience in the quality field; or equivalent combination of education and experience
- Experience in internal auditing and Lean Six Sigma experience (green or black belt) are desired
- Must have experience with IPC standards for circuit card assemblies and PWBs
- Defense contract experience and experience working with RF or SATCOM is preferred. Experience with a stage gate New Product Introduction process is helpful
- Must be a motivated and organized multi-tasker that requires minimal supervision to complete assignments. Must be able to read and interpret documents such as engineering drawings and procedures, quality procedures and work instructions, test procedures, design documentation, contracts, and SOWs as relative to Quality Engineering requirements. Must have exceptional interpersonal skills and be computer literate
- Must understand hardware quality assurance standards, CCA assembly and test processes, as well as performing root cause analysis and corrective action implementation, including failure analyses
Supplier Quality Engineer of Electrical & Electronics Resume Examples & Samples
- Take major responsibilities in the following aspects
- Minimize 8 years’ experience in high or middle voltage product experience, like transformer, generator, control cabinet and other electrical assemblies
- Ability to travel to suppliers frequently
- Manage the launch as well as support the continued development of a global supplier quality system
- Lead on-site audits focusing on both quality systems and technical processes
- Conduct thorough technical reviews at the part level to assess suppliers’ capabilities
- Continuously monitor and improve supplier quality performance (NCR, PPM, RFT, Yield)
- Work with Global Purchasing to ensure supplier performance is regularly reported to suppliers, and that appropriate and timely corrective actions are implemented
- Help suppliers to exceed "Fit, Form, Function" as well as reliability requirements while working with AGCO purchasing, manufacturing and engineering teams
- Champion problem solving and root cause analysis activities with suppliers to avoid repeat failures
- Work with Technical service and supplier recovery team to gather, analyze and action all field issues related to assigned suppliers
- Lead required problem solving efforts to eliminate warranty failures
- 2-7 years of experience in a Supplier Quality Engineering (SQE) role
- Advanced knowledge of Excel
- Bachelor’s degree in Engineering or a related technical field
- 2+ years of experience at a manufacturer of industrial, automotive, heavy machinery, or agricultural equipment
- Experience working with and analyzing data from an ERP system, preferably SAP
- Experience supporting specific commodities
- Driving Improvements in commodity/supplier specific quality issues through CLCA
- Supporting quality planning in suppliers to support continuous improvement in
- Manage non conform material handling (all Rework/RTV/DMC/RMA activity)
- Provide support where necessary to select, audit and approve new suppliers
- Provide emergency Buyer cover when required (in case of line down situation)
- Manage plans, in conjunction with Line Support & Lean team, any packaging
- Preparation & updating the Incoming Inspection plans
- Coordinating the incoming inspection activity
- Monthly Supplier PPM calculation & communication to supplier
- University/college degree in Engineering
- Minimum 2 years of experience in engineering/IQA area
- PC skills on user level
- English on communication level
- Good analytical ability
- Experience in Lean and Six Sigma tools
- Knowledge of Supplier Quality and Process improvements
- Quality control techniques
- Evaluate and approve suppliers for Type Certification and Production use
- Train suppliers in applicable Honda quality requirements and operating systems
- Conduct audits of supplier facilities and manufacturing processes to ensure compliance with all Honda and FAA requirements
- Coordinate and verify supplier root cause and corrective action activities
- Implement supplier improvement plans as necessary in order to ensure suppliers perform at expected quality levels
- Support the continued development of the Supplier Quality Management System and related processes
- Support supplier Production Readiness Activities
- Support cross functional Integrated Project Teams as necessary
- Promote the Honda Philosophies in daily SQA activities
- Willingness to travel up to 50% of the time to supplier sites. (domestic and international)
- Bachelor’s Degree in related Engineering field preferred (mechanical, manufacturing, materials, electrical, industrial, aeronautics)
- Experience working with and auditing to internationally recognized quality systems such as AS9100, TS16949, ISO 9001 preferred
- Experience in the development and oversight of an FAA Part 21 approved Quality System a plus
- Exposure to Six Sigma or Lean Sigma methodologies preferred
- ASQ CQE or CQA certifications a plus
- Working knowledge of various quality tools and processes such as PFMEA, Control Plans, APQP, PDCA, DMAIC, SPC preferred
- Experience managing suppliers of composite structures, major assemblies, valves, actuators, or interiors a plus
- Experience auditing special processes such as heat treat, welding, acid anodizing, plating, chemical conversion coating, composite fabrication, or NDI a plus
- General computer proficiency in Excel, Word, and PowerPoint a must
- Effective communication skills and proficiency in English a must
- Lead resolution of quality related issues on the manufacturing floor including the disposition of non-conforming material as required
- Monitor processes by developing, collecting, analyzing, and reporting quality statistics and metrics to qualify process capability, sustain process control, support problem resolution and promote continuous improvement
- Acquire, develop and provide training in quality disciplines, tools, and techniques
- Support foreign and domestic pressure vessel requirements to include: ASME Section VIII Div. 1, EC-PED, and AS1210
- Participate in design reviews and assist design engineers in identifying product improvements, definition of key product characteristics, necessary process controls and product validation tests
- Lead, facilitate and execute quality planning activities in direct support of new product development programs and quality improvement projects
- Drive customer critical-to-quality requirements down to critical feature control plans supporting expected process capabilities
- Conduct post-launch audits of production lines to ensure all required controls and tests are being properly executed
- Support, maintain and enhance the current/applicable Quality System, assuring organization adherence; promote system improvement via participation in product, process, and Quality System audits
- Work closely with supplier quality engineering to support component qualification (PPAP) efforts such that purchased material is effectively integrated with internal control plans
- Participate in activities around sourced component quality including production part approval, proactive quality problem resolution, assisting supplier evaluation and selection, improvement training, business process development, quality cost recovery and projects to improve supplier quality
- Develop and manage business processes around improving internal and external quality performance as well as other duties as assigned to support business goals and objectives
- Experience in GD&T concepts, CMM and/or FARO Arm techniques helpful
- Bachelor’s degree in engineering required. Bachelor’s degree in quality management or technical related disciplines with ASQ CQE certification and 5+ years of relevant experience will be considered in lieu of an engineering degree
- Minimum 2 years of manufacturing, product/process development, metrology, and/or supply chain experience
- Technical knowledge and expertise in quality and/or assembly, weld/fabrication, or machining process disciplines preferred
- American Society for Quality (ASQ) Certified Quality Engineer (CQE) preferred or must be willing to work toward certification
- Strong work ethic, customer-focused, team oriented and results driven
- Excellent interpersonal, written and verbal communication skills with strong leadership, project management, team building and presentation skills
- Strong PC skills (Microsoft Office, design-related software, statistical-based software)
- Leads Supplier Quality Performance Management for the Group
- Provides functional support for deployment of supplier performance management tools and processes to drive overall improvement in supplier performance with an intense focus on highest impact, poorest performing suppliers
- Works directly with business unit SCM and Quality teams to engage key suppliers (external) to drive improved quality and delivery results using proven EQS methodologies
- Develops and deploys guidelines for issuing DMRs, calculating PPM, and evaluating suppliers’ corrective action responses in order to insure consistency across the organization and eliminate repeating quality defects
- Responsible for Group deployment and refinement of standard processes and tools such as Business Reviews for strategic suppliers, Internal Supplier Partnership Process (ISPP) and Focus Six Process to improve supplier performance including procurement, quality and delivery metrics
- Partners with the Sector Supply Chain teams to develop common sector performance goals (PPM, On Time Performance, Cost Recovery)
- Systematically gathers and reports supplier performance metrics including monitoring, trending, and analysis for the Group so that actionable data is available for sourcing decisions, supplier performance reviews, selection of suppliers for quality development, supplier recognition in order to meet sector business goals. Data will include: monthly ppm defects, supplier escapes & speed of response, cost-of-non-conformance (CONC) and recovery, and On Time Performance (OTP). Evaluates results and oversees the organizational and supplier development of improvement plans to close gaps and goals
- In liaison with the Corporate WISPER/SAP QM teams and the Sector leaders, coordinates projects to effectively implement and deploy WISPER/SAP QM system level improvements and improve the accuracy of the PPM and OTP data maintained in WISPER/SAP for all ES sites including acquisitions
- Develops and deploys group wide Cost Recovery program to recover costs of poor quality from suppliers (Phase I – DMR Administration Fee, Phase II – High Impact Cost Recovery)
- Provides training on Supplier Quality practices and tools for Eaton and Supplier personnel (8D Problem Solving, APQP, PPAP, QSA, WISPER, SAP QM, etc.) and monitors implementation
- Partners with Sector SCM team to conduct periodic reviews of the Supplier Performance Management systems and creates improvement cycles based on performance results
- Ensures that the implementation and improvement of the Quality Management System for suppliers is effectively managed to foster a culture of customer focus and continuous improvement while maintaining compliance with internal and external requirements. Regularly coordinated knowledge and best practice sharing across sites. Utilizes appropriate benchmarking and comparative data, serves as a thought leader for next generation functional requirements and participates in enterprise forums and teams to improve the Quality Systems
- Takes an active leadership role in the PROLaunch process to ensure flawless product and/or process launches with suppliers. Responsible to ensure that supplier quality deliverables are completed according to standard per the pre-gate functional review process
- Minimum 3 years experience in a quality position within a manufacturing organization
- Must live within 50 miles of Ellisville, Pittsburgh, Peachtree City, Cleveland, or Menomonee Falls
- Master's degree from an accredited institution
- Experience with SAP/ERP system, including Quality module
- Fluent in Spanish
- Prior global or multi-plant level of responsibility
- Monitor materials in the manufacturing process to meet the quality expectations
- Follow up KPIs and initiate any necessary corrective actions
- Maintenance of updated LCD documentation, specification
- Analysis of process related LCD problems
- Analysis of LCD scrap, RMA, debate with suppliers
- SRMA process of LCD panels
- Reporting, statistics related to LCD
- Bridging of customer-supplier relation for LCD
- Emphasis in the areas of supplier process capability and product quality, this position will use analytical techniques to make recommendations for continual improvement as well as ensuring conformance to internal and external standards
- Provide direction and disposition of product through the discrepant material area. Coordinate all necessary testing and failure analysis regarding nonconforming components from suppliers
- Coordinate activities with suppliers on rejected components or materials received by Itron and ensure that "bad" product doesn't continue to reach the production lines. Share this information with other Itron production facilities so they may also watch for any discrepant material(s)
- Provides expert analysis, guidance and support to Production/Supplier in Process Improvement activities, including effective use of Problem-Solving tools and techniques, statistical analysis, and thorough inspection equipment/techniques
- Responsible for advanced product quality planning, roadblock remover, and successful launch of supply base components (on time and zero defects)
- Provide technical expertise and leadership to all production value streams enabling effective communication between production and suppliers
- Conduct Supplier Quality Training at supplier’s facilities to meet Itron’s specific quality expectations/requirements
- Participate in development of supplier metrics and monthly gathering/distribution of measurements
- Review and make disposition on Supplier PPAP (Production Part Approval Process) submissions, to ensure they are submitted and approved to organizational requirements
- Troubleshoot problems associated with customer returns, defects from manufacturing related to purchased materials, assist to determine root cause and corrective action
- Work with purchasing, quality, engineering, and all manufacturing support areas to improve cost, quality, and throughput from suppliers
- Management of quality system, graphical analysis, data management and control utilizing centralized databases
- Considered to be a leader within the Supplier Quality Engineering (SQE) group and Subject Matter Expert (SME) regarding SCAR's (Supplier Corrective Action Reports) and PDCA’s (Plan, Do, Check, Act)
Component Supplier Quality Engineer Resume Examples & Samples
- Experience working in semiconductor fabrication ranging from leading edge sub-micron processes to RF specific components
- Detailed understanding of all Fab processes and their dependencies on techniques & equipment
- Experience in Failure Analysis and Quality Control of semiconductor components
- Experience with Root Cause Analysis for Wafer Sort, Parametric, Test Issues and Related Process / Design Improvement DOEs
- Experience with Process and Design FMEA to drive CTQ Wafer Sort and Product Yield issues
- Bachelors' Degree in Mechanical, Electrical or Industrial Engineering from an accredited institution required
- Minimum of 5 years prior mechanical/electrical engineering experience in a electromechanical industry environment
- Exposure to manufacturing enviroment is required
- Must be legally authorized to work in Puerto Rico/United States without company sponsorship
- No relocation benefit is offered
- Proficient in Excel, PowerPoint, Word, Minitab
- Bilingual - Spanish & English - oral & written
- Speak Chinese
- Certified ISO 9001 Auditor
- Overall supplier quality performance to drive quality, delivery, and service improvements. Periodic reporting and tracking of quality performance
- Assure closure on supplier PPAP approvals, deviations, audit findings, corrective actions
- Supplier development through training, audits, selection, etc
- Conduct internal and external training necessary to improve supplier quality
- Assist Purchasing Supervisor and/or Quality and Regulatory Affairs Director in source selection and development, surveys, certification, and tool and component qualification
- Support new product development, programs and platforms from a supplier quality perspective. Supplier selection, qualification, capability, tooling, gauging, measurement consistency/gauge correlation, gauge R&R, print reviews, etc
- 3 years of related experience
- Minimum three (3) years practical, hands-on, quality and lean operations experience
- BS in Business Administration, Mechanical Engineering, Material Science, or Manufacturing Engineering
- Previous experience with quality related systems in a manufacturing environment
- ISO internal lead auditor certification and/or ASQ Certified Quality Auditor
- Proficient in Problem Solving and Corrective / Preventive Action skills - Proactive approach
- Proficient in understanding ISO 9000 and/or AS9100 along with knowledge in Statistical Tools and Techniques, APQP and Measurement System Analysis desired
- Proficient with Microsoft Office, Oracle, Rohbe SAS, IQS CATS software
- Proficient written and verbal communication skills
- Based on education and experience, this may be filled as a job band 25
- Supplier material quality control. Assist to sourcing on supplier process audit
- Abnormal issue disposal of materials Negotiate to supplier on raw MRB materials
- Supplier performance appraisal and quality improvement
- Regular meeting with supplier on quality key indicators
- Assist to sourcing on new supplier development
- Training to incoming inspector on material quality standard
- Creation of material inspection instruction
Mechanical Supplier Quality Engineer Resume Examples & Samples
- Typically requires 5+ years of experience in developing quality plans, designing test methods and gauges, validating test methods and gauges, and driving corrective actions and failure analysis efforts required
- Knowledge of quality and reliability concepts, supplier management, and general manufacturing operations. An area of expertise such as a specific process, material or industry is key to show depth of knowledge base
- Project management experience and a solid understanding of problem solving tools including design of experiments, root cause analysis and statistical process control principles preferred
- Experience with any of the following: mechanical enclosures, castings, plastic parts, injection molding, tooling, jigs, fixtures, or automotive high volume quality manufacturing engineering
Supplier Quality Engineer / Sheet Resume Examples & Samples
- Preferred Bachelor in Engineering, or >5 years of technical experience needed
- (extensive experience and strong performance can substitute for academic degree)
- Experience from supplier quality work within automotive business
- Good knowledge and practice of automotive quality standards and tools, such as ISO/TS 16949, APQP & PPAP
- Preferably, some knowledge about sheet-metal components and associated production process
- Car driving licence
- A minimum of 2 years of experience in a GMP and/or ISO regulated industry is required
- Both, FDA and ISO regulations knowledge is preferred. FDA CFR Part 820 and/or ISO 13485 knowledge is preferred
- Demonstrated expertise with statistics, sampling strategies, design of experiments, and structured problem solving methodologies is preferred
- Strong communication, teamwork, and problem solving skills are required. Prior experience working collaboratively in a highly matrixed organization is preferred. Intermediate knowledge and use of Microsoft office are required
- Experience in auditing is preferred
- An ASQ certification (CQE, CQM, CRE or CQA) is preferred. Six Sigma (Green Belt, Black Belt, etc.) or Process Excellence certification is preferred. Excellent Investigative skills such as analytical problem solving, Fishbone/Ishikawa, root cause analysis, etc. are an asset
- This position will be based in Monument, CO, and will require up to 25% travel
- Perform Specification Compliance Reviews, First Article Inspections and Source inspections on mechanical parts and assemblies, and cables and connectors
- Perform process and product audits along with capacity assessments to ensure the supplier's processes are robust and capable
- Bachelor's degree in Mechanical, Materials, Manufacturing or Industrial Engineering
- Experience in Geometric Dimensioning & Tolerancing and the use of basic inspection tools as well as the ability to use a CMM and laser tracker to measure dimensions
- Understanding of NADCAP certified processes, including painting, plating, finishing, coating, machining, brazing, welding and castings, and NDT methods highly desirable
- Work with Purchasing and TE data system to ensure supplier performance is regularly reported and that appropriate and timely corrective actions are implemented
- Monitor, communicate and improve key supply chain KPI’s, including Supplier past due, DPPM and waste
- Strategically lead supplier performance improvement projects in an effort to increase the supplier capability of consistently meeting TE requirements. Projects may include: process analysis, value stream mapping, process capability and throughput analysis, 6‐Sigma, 5S and Kaizen events
- Assure compliance to all applicable legal requirements pertaining to the environmental aspects and impacts. Work to help achieve the performance goals established in the environmental measurement areas. Offer suggestions that can lead to improved environmental performance whenever possible
- Bachelor’s degree in related discipline; or 4 years related experience and/or training in manufacturing environment; or equivalent combination of education and experience
- Advanced computer skills using Microsoft Office applications
- Solid knowledge of various quality system methodologies 8D, Lean, 5 Why’s, Pareto Analysis, Six Sigma, 8-D, DFMEA, PFEMA, PPAP, etc. preferred
- Must have a strong command of the English language (verbal and written)
- Must be able to travel aborad
- Due to ITAR restrictions, US Citizen or Permanent Legal Resident required
- Manage supplier qualifications for professional services commodity, such as NDT, welding, scaffolding, rigging services
- Conduct surveillance audits to assure that suppliers have effective process control, rigorous product acceptance standards, and robust quality systems
- Manage supplier non-conformance and Supplier Deviation Request (SDR) activities. Owner of process and 1st technical interface with supplier and engineering
- Drive consistency and adherence to quality procedures and specification requirements
- Provide Sourcing Quality input to Engineering, Field Services, Repairs Network during product design reviews
- Conduct 40 supplier on site visits per year. Close all findings identified with supplier with focus on major findings and timeliness of corrective actions
- Bachelor’s Degree (Technical Degree preferred)
- Demonstrated technical aptitude and a passion for quality
- Black Belt certified or equivalent (demonstrated experience). Core competencies of a BB are a must for improving supplier statistical capability, evaluating readiness to serve, including capacity verifications
- ISO Lead auditor certified by 3rd party registrar or accepted internal GE training/certification program
- Certified RCA Leader or other proven expertise with formal problem solving (Kepner Tregoe, 8D, Apollo, etc)
- Experience in metallurgical and/or manufacturing processes
- Bachelor’s Degree in Mechanical or Metallurgical Engineering / Advanced Technical Degree
- Minimum 3 years of experience in Supply Chain, Supplier Quality or Engineering
- Demonstrated proactive approach and issue ownership with process orientation
- Ability and willingness to travel internationally. Travel >50%
- Developing supplier partnerships to ensure quality, service and cost requirements that meet the needs of the United Technologies Aerospace (UTAS) ISR and Space site Operations, Program Management and Engineering teams
- Working with our supplier partners to investigate and correct supplier quality issues and establish a culture of continuous improvement
- Creating a trusting relationship with emphasis on removing waste and variability from processes to assist suppliers in reducing their costs, and improving the suppliers' quality and delivery
- Managing people within commodity and directing activities with their supply and commodity base
- Overseeing corrective preventive action
- Working with both supplier and other site supplier issues
- Must have in-depth background in working with key subcontracts and sub-contract manufacturers
- Must have in depth background and ability to manage the suppliers within various commodities with a main focus in the optical commodity field
- Requires an extensive background in processes and process surveys and thorough understanding of AS9100 and ISO 9001 is required
- Knowledge in lean and lean techniques with an ability to work with suppliers on lean improvement activity with the supply base for both operational and quality improvement is a must
- Self Starter, Highly motivated
- Detailed knowledge of standard AS9100, ISO 9001-2015, Quality Systems and Supplier Management Requirements; and First Article Requirements per AS9102
- Experience with advanced problem solving techniques, 6 sigma tools, corrective action, root cause analysis, CPK, Gage R&R, and Lean Manufacturing-Understand Metrics / First Pass Yield and general process improvements
- Strong experience with Microsoft Office Suite particularity in Outlook, Excel Power Point & Word. SAP experience a real +++
- Utilize multifaceted industry and process excellence standards on a moderately complex level in daily quality operations, including good manufacturing practices (GMP), equipment engineering system (EES), and international organization for standardization (ISO)
- Address or escalates product and process complaints
- Conduct audits of all quality system categories to assess compliance to process excellence standards
- Implement comprehensive measurement systems to monitor effectiveness of quality and reliability systems to identify, bracket, correct and prevent defects, presenting reports to management
- Facilitate technical issues for manufacturing processes that are to be transferred to satellite facilities
- Experience in the medical device and/or pharmaceutical industry is preferred. Operations supplier quality experience is preferred
- Both, FDA and ISO regulations knowledge is required
- Fluency in French and English is required
- This position will be based in Le Locle, Switzerland and requires up to 25% travel, including possible international travel.Quality (Eng)
- Execution of supplier management plans to improve supplier and product performance
- Perform supplier audits & material qualifications
- Investigate and disposition nonconforming materials. Develop plans to prevent reoccurrence
- Act as primary quality representative for root cause and corrective action analysis regarding supplier caused quality issues
- Visit suppliers to resolve product performance concerns
- Education: Bachelor’s degree in engineering field
- Previous supplier quality management experience (i.e. supplier development, material specification development & monitoring, supplier approval & material qualification, ISO stds auditing) is desired
- Self-starter with a demonstrated ability to focus efforts, overcome obstacles and complete key projects
- Project Leadership - Ability to guide the successful completion of low to medium complexity processes and/or projects
- Knowledge of GDT and ability to interpret engineering drawings
- Experience with Word, Excel, Outlook and MS Project
- Knowledge of machining processes
- Experience with sampling plans, process capability analysis and measurement systems analysis desired
Supplier Quality Engineer for Inorganic Surface Treatment Resume Examples & Samples
- To evaluate Surface Treatment (coating) supplier lines and facilities, managing their development plan up to the excellence level required by the Volvo standards
- To support the new part developments, securing the suppliers ability to coat the parts according to the specification on robust manufacturing processes
- To lead the supplier continuous improvements as well as being entitled to steer strong reaction in case of supplier performance deviation
- To contribute to the Surface Treatment Supplier Quality Global Network, working on new standard inputs, continuously improving the assessment tool and permanently monitoring the new technology and their opportunities
- Preferred Bachelor in Engineering, or >5 years of technical experience needed in surface treatment chemistry , inorganic coating area, (extensive experience and strong performance can substitute for academic degree)
- Experience upon the Surface Treatment (coating) application processe and its management within automotive business
- Good knowledge and practice of automotive quality standards and tools, such as ISO/TS 16949, process audit and problem solving
- Understand and promote Magna’s philosophies and Employee Charter
- Key liaison with both internal & external customers
- Utilize the tools of APQP (PPAP, FMEA’s, control plans, capability studies, etc.)
- Participate/Ensure timeliness of corrective and preventive actions for internal and external quality concerns
- Support Continuous Improvement activities and lean manufacturing processes
- Ensure supplier compliance to specifications / approval of Corrective Actions
- Monitor status of key program milestones – PSW dates, Launch Build events, etc…
- Follow all plant safety policies and procedures
- Visit and follow-up with suppliers on Quality / Delivery issues seeking corrective actions
- Maintain and communicate supplier tracking metrics for continual improvement
- Assist Engineering / purchasing in new supplier selection process
- Manage potential supplier profiles and assessments
- Conduct Supplier audits
- Lead supplier development programs and follow-up
- Assist in updating Magna supplier portal
- Quality training, Metrology, AIAG standards
- Computer skills; proficient in Microsoft Office applications
- Minimum of 5 years of Quality experience in the automotive industry
- Must possess in-depth experience with GD&T
- Understand automotive Quality Assurance requirements (e.g. Production Part Approval Program, Process Sign-Off, Part Submission Warrants, etc.)
- Must be proficient in Microsoft applications
- Must have thorough knowledge of the TS16949 Quality System Requirements and Auditing
- Must comply with customer specific requirements
- Must be willing to work extended or flexible hours as needed to meet production requirements
- Willingness to work in various locations within and outside the facility
- Must have experience with launching new programs including the stamping/die buyoff process
- Must have experience in auditing and implementing quality systems to support development of new suppliers
Supplier Quality Engineer, Senior Resume Examples & Samples
- Performs Supplier Audits and resulting documentation
- Maintains documents relative to Supplier Management
- Ownership of projects and technical Competence
- Works independently and is Results Oriented
- Initiates new or revised documentation and tracks through appropriate approval cycles and implementation
- Maintains a professional working relationship with internal & external customer and support staff
- Participates and/or leads cross-functional teams
- Provides technical support on components, material methods, systems and equipment
- Develops physical and functional test requirements to assure specifications & regulations are met
- Writes, reviews and approves protocols, reports and data
- Understands and follows company procedures and regulatory requirements
- Participates in and provides input to training on department & division procedures, and policies
- Analyzes problems in design, process and test development
- Prepares and presents oral and written project updates and technical discussions
- Develops and implements procedures to provide easy to follow instructions
- A Bachelor degree in science or engineering with six (6) years of engineering expereince withign the medical device or equivalent regulated industry, OR
- Masters degree with five (5) years of engineering experience within the medical device or equivalent regulated industry
- Above experience must include 3 (three) years’ proven and effective project management skills
- Demonstrated knowledge of engineering principles through engineering experience within the medical device or equivalent regulated industry
- Ability to make and present engineering decisions
- Specific specialized engineering skills such as
Production Supplier Quality Engineer Resume Examples & Samples
- Engineering degree (mechanical and/or electrical engineer)
- Relevant engineering experience (Technical experience)
- Excellent English skills (verbal & written)
- Good interpersonal, communication & presentation skills,
- Good negotiations skills,
- Taking initiatives & initiating changes,
- GE background is preferred,
- 6Sigma Greenbelt certified
- Basic financial knowledge,
- Quality and/or sourcing background (engineering, ISO, QA/QC),
- Ownership of supplier management process for approx. 50 suppliers, including supplier audit schedule
- Regular reporting on supplier performance and supplier quality metrics
- Guarantor of full regulatory compliance in supplier management process
- Reporting to Supplier Quality Leader in Dowty and dotted line to local site Quality Manager Dowty Propeller
- Responsible for driving quality for assigned suppliers, improving quality performance via Quality Plan implementation
- Provide Quality Engineering expertise requiring advanced/specialized skills and a broad range of quality engineering expertise
- Provide technical expertise to customers/licensees in solving technical problems associated with test facilities
- Drive investigations of quality problems
- Monitor supplier non-conformance performance, and drive root-cause analyses, corrective actions and process improvements to reduce the Number of Defects and Cost of Quality
- Work effectively with commercial, engineering and manufacturing teams to eliminate any barriers that may affect the quality and delivery of sourced components
- Execute the supplier selection process and supplier surveillance process
- Responsibility for Supplier quality on commodity level, responsibility for meeting Dowty requirements and on time deliveries
- Continuous quality improvement – ownership or suppliers QIPs
- Regular reporting on Supplier performance to senior leadership
- Maintenance and execution of supplier oversight
- Liaison with sourcing processes and procurement processes
- Responsibility for regulatory supplier compliance
- Responsibility for supplier rating
- Execution of corrective an improvement actions at suppliers
- Bachelor’s degree from an accredited university/ college or equivalent with experience in Sourcing or Quality improvement role
- Experience in a Sourcing or Quality Improvement role
- Proven years of experience in sourcing, manufacturing quality or product engineering role
- Willingness and ability to travel to Supplier locations
- Ability to lead and manage other members in the organization
- Lead Sourcing in the selection, qualification, and development of suppliers regionally
- Define activities within the commodity management team to improve supplier quality, delivery, and performance for direct material suppliers (Electro Mechanical including electrical, mechanical, and electro-mechanical components, as well as, raw materials and finished goods)
- Direct PPAP – production part approval process - qualification activities associated re-qualify parts as part of supplier transition projects
- Utilize standard Honeywell processes to coordinate the audit and approval of new suppliers
- Be an expert on supplier quality tools - lead the roll out, training and implementation of supplier quality tools for suppliers, including alignment with HOS requirements
- Lead and support efforts to fully realize cost savings opportunities
- Liaise effectively with commodity teams, program managers, operations and engineering leadership, to identify and fully satisfy requirements for supplier quality engineering activities at Brno factory
- Monitor and ensure correct acquisition of PPM metric
- Ensure corrective actions for non-conforming material
- Coordinate 4 blockers for major non-conformances for MOR
- Provide daily leadership to direct reports
- Complete HPD activities for direct reports
- Train SQEs in Brno
- Implement actions and processes for PPM to meet goal
- Attend Quality and OPS Tier meetings
- Attend Quality and OPS staff meetings
- Participate staff meetings for EMEA SQE Team
- Assist procurement in continuous improvement for OTTR
- Lead quality approval process for new suppliers in Brno
- Prioritize and escalate quality issues to Sourcing for site tier 4, 5 and 6
- Bachelor Degree in Electrical/Mechanical/Material Engineering
- Good understanding of English and preferably a second language
- Minimum 3 – 5 years experience in Engineering/Purchasing/Quality and strong knowledge related to the manufacturing, design, and use of Mechanical and/or Electrical components. Knowledge of raw materials/metals/plastics/resins/electronic components preferred as well
- Strong understanding of QS,TS, APQP and PPAP standards, processes and implementation
- High level of fluency using advanced quality tools
- Skilled in Microsoft Office, SAP and Excel
- Lead Supplier qualification & audit processes and maintain supplier QMS system effectiveness
- Work with Production Associates & engineering or sourcing team to resolve quality problems related to methods, processes, tooling, equipment and etc in supplier side
- Participate in new product introductions through SPQP (Supplier Part Quality Plan)
- Ensuring regulatory compliance through Validation & Verification - Plan execution and analysis
- Lead Supplier Change requests handling and ECO’s implementation
- Supplier quality issues follow-up and actions effectiveness checking
- B.S. Degree in Mechanical (Die Casting, Plastics & Machining) or Electronics (PWA) with at least 8 years’ experience (5 +years in mechanical design or processes, 2+years in quality related)
- Understanding ISO9001 requirements
- Good team worker in international teams
- Good English communication skills
- M.S. Degree in Engineering
- Demonstrated ability to identify & implement best practices
- Demonstrated ability to perform with high levels of ambiguity
Supplier Quality Engineer Parts & Projects Resume Examples & Samples
- Conduct process capability statistical analysis to proactively identify issue trends
- Manage supplier non-conformances and Supplier Deviation Request (SDR) activities. Owner of process and 1st technical interface with supplier and engineering
- Perform robust Root Cause Analysis to solve quality issues and prevent reoccurrence
- Be the technical focal point to coordinate Sourcing, Design & Materials Engineering functions while interfacing with suppliers
- Provide technical guidance to suppliers to assure product/process compliance with engineering drawings and specifications
- Work closely with commercial, engineering and manufacturing teams to eliminate any barriers that may affect the quality and delivery of sourced components
- Bachelor’s Degree in Engineering discipline
- Strong background in interpretation of Engineering drawings/specifications, metrology, and manufacturing process planning/evaluation. Must understand GD&T and be able to lead technical design and manufacturing reviews with suppliers
- Certified to lead Supplier Responsibility Guidelines programs for suppliers in “mandatory regions”
- Related Power Generation manufacturing experience
- Ability to work in cross-functional and global team environments
- Bachelor’s degree or higher in an Engineering or Science discipline from an accredited institution
- Experience with evaluating and/or qualifying suppliers (an Internship or Co-op experience is considered qualifying)
- Master’s degree in an Engineering, Science, Business or related discipline from an accredited institution
- Experience in medical device and/or other regulated industry
- Knowledge of International Organization for Standardization (ISO)/ Food and Drug Administration (FDA) quality system requirements
- Background in statistical techniques, data analysis, Six Sigma and/or Lean
- Understanding of process validation, control plans and acceptance activities
- Understanding of risk assessment and the translation to risk proportionate deliverables
- Prior auditing experience
- Manufacturing background/experience
- Ability to read and interpret drawings and design requirements
- Proficient in technical writing, communication, and collaboration
- Proficient with standard computer applications, such as Word, Excel and PowerPoint
- Motivated and a self-starter
- Highly organized and displays a sense of urgency
- Demonstrated ability to teach new concepts and subject matter
- Master's degree in engineering with a specialization in quality management
- Ability to work in a matrixed organization
- Bi/multi-lingual (Fluent in English, Intermediate German)
- 1) Supplier quality management on fab, metal, sheet metal, hardware, heatsink, stamping, machining, enclosures, die casting commodity
- 2) Supplier Auditing, Surveillance Auditing
- 3) Deal with Sporadic problem/resolution issues in supplier site and report to customer
- 4) Monitor supplier quality performance and drive action if out of target
- 5) Support qualification audit for new suppliers with SDE and sourcing team
- 6) Customer drawing and Specification review and problem solving from supplier, IQA, production or customer site
- 7) Responsible to help supplier to increase quality and productivity with SDE
- 8) Other specify request from customer
- 3) ISO9001, ISO13485, QS9000, ISO/TS16949 knowledge
- 4) Familiar with Quality Tools, such as PPAP, FMEA, MSA, SPC, APQP
- 5) Problem solving skill, ability to use 8D/5why analysis tools to resolve the problem
- 6) Ability to read and interpret documents such as safety rules, operating and maintenance instructions and procedure manuals. And to write routine reports and correspondence
- 7) Experience in Drawing reading and review
- 8) Experience in audit skill
- 9) Good English skill both Oral and Written
- 10) Good communication skill and work attitude
- 11) Proactive, Team player, self-motivated & result-oriented
- Relevant education (at least P.E), B.Sc. – An advantage
- Good understanding of statistical methods, quality tools and methodologies (QFD, CtQ breakdown, DfSS, SPC, AQP, FMEA, Control Plan)
- Six Sigma GB/ BB certification preferred
- Highly motivated, action oriented, persistent towards accomplishing tasks and drives for success
- Ability to communicate well, oral and written, in English and Hebrew
- Experience in specific manufacturing processes used for engine components for example: casting, machining, surface treatment or electrical components are desirable
- Good networking capability
- Pro-active, positive attitude and good ability in priority management
- Willingness and ability to work in a global organization
- We highly appreciate a positive attitude, a target oriented approach, and good interpersonal skills
- Frequent travelling expected
- Managing multiple commodity groups for continual performance improvement
- Addressing day to day quality issues to minimize impact to the production environment
- Problem solving using six sigma analytical tools to permanently correct chronic supply base component quality issues
- Work cross-functionally to resolve issues and drive continuous improvement
- Identify and drive warranty reduction activities associated with supplier components/parts
- Utilize quality skills, tools, and talent to continuously drive supplier performance improvements
- Provide guidance and support to the Quality Technicians on all matters related to supplier quality
- Minimum 1 year working experience in Supplier Quality Assurance, Automotive area – is a plus
- Good knowledge and experience working with 8D report, PFMEA, PPAP, Control Plan, SPC etc
- Fluent English Skills (Written, Spoken, Reading)
- Excellent presentation skills, with verbal and written communication abilities
- Well organized, able to prioritize and high capacity to solve problems
- High technical skills, analytical, able to assimilate information and draw conclusions quickly
- Accountable for RMA request and send to Buyer
- To assist PQE for any of quality issue suspected to supplier fault if only required
- Able to demonstrate best method on how to handle components
- Work with supplier and ensure world class Supplier Corrective Action report (SCAR) obtained for each of issue
- Perform analysis on supplier performance and share on quarterly basis
- Review each of new component for NPI activity (Packaging and Handling)
- Establish specific short / long term supplier quality goals Supplier KPI for critical supplier
- Ensuring Pending Q location are well maintain and always at the lower amount
- Support introduction of new products into existing suppliers as required for NPI projects
- Regularly review all open CARs and ensure closure on timely manner
Sqe-supplier Quality Engineer Resume Examples & Samples
- Responsible for all tactical and operational Supply Quality processes
- Member of the global Supply Quality commodity team
- Informs LEAD SQE per commodity about risk and developments with suppliers (escalation)
- Responsible and Performs Supplier Validation, for NPI and Ressourcing the APQP/PPAP process, follow up suppliers for NCR/Claims from project, serial/mass to warranty
- Executes supplier visits / audits and follow up action plan defined
- Conducts the 8D analysis after NCR/ Claim to warranty the elimination of Root Cause
- Assists global tenders, regular audits and supplier evaluations
- Responsibility for everyday communication with suppliers
- Carries out Quality contract management, incl. quality appendix with Cost non quality and performance
- Manages Engineering Change Process in NPI and production phase , according PPAP3
- Troubleshooting (support technical and time-critical ad-hoc requests / requirements)
- Supports commodity and supplier reporting and performance measurement
- Uses up to date standards and templates provided by the Competence Center
- Ensures regular communication with internal and external interfaces
- Technical knowledge of the product commodities
- Good understanding of ISO 9001
- Process audit method
- Use of basic precision measuring tools, workmanship standards, visual inspection and calibration activities
- Problem Solving tools (brainstorming, Cause & effect diagram (“fishbone”) , 5 Why
- Excellent communication and negotiation skill both verbal and written when working with suppliers
- Ability to work with others
- Positive attitude with self motivation
- Master Degree in Mechanical engineering or similar and passion in quality jobs
- Current practice of process auditing
- 5 or more years of Experience in same role within modern and structured manufacturing plants
- Very good pc skills
- Fluent English speaker
- Lead and organize supplier audit and follow up to closure
- Interface to external suppliers for quality assurance from supplier
- Lead purchased part approval activities with internal team and external suppliers
- Drive Supplier Corrective Action Requirement(SCAR) initiation till closure for external suppliers
- Support Quality Notice(QN) handling from production for external supplier issues
- Monitor and improve the quality part inside Global Supplier Rating System(GSRS) and Supplier Performance Monitor (SPM) for external suppliers
- Conduct supplier quality development in audit, Purchase Part Approval (PPA) and Supplier Quality Improvement Plan (SQIP) activities
- Lead regular quality review with priority external suppliers
- Drive the purchasing compliance in Diagnostic Imaging China
- Supplier Quality Management: Ensure the standardized Aerospace processes for the supplier quality management system are established, implemented, measured, and maintained within the organization
- WISPER Plant Champion: Manage Eaton and supplier WISPER system utilization and Eaton Supplier Excellence Manual guidance within the organization
- Supplier APQP: Manage and ensure quality of supplier’s deliverables in non-critical (medium and low risk) sourcing changes
- DMR: Manage notification, responsiveness, containment, root cause determination, corrective action, and closure of supplier quality issues. Report supplier DPPM data
- Production Floor Support: Respond to supplier-induced failures caught on the production floor in support of the High Performance Work Team structure. Manage 3rd party calibration lab located on site
- Bachelor degree in Engineering
- Minimum 3 years of manufacturing experience
- Must live within 50 miles of Bethel, CT
- Knowledge of GD&T
- Knowledge of Engineering blue-print reading
- Knowledge of ISO9000 or AS9100
- Knowledge of 8D structured team problem solving methods
- Knowledge of Continuous improvement tools & methods
- Value-Added Engineering Activity (VEA) to optimize supplier manufacturing process or products
- Material qualification through implementation of PPAP (FAI, Material Certificates, Quality/Process Control Plan, FMEA, MSA, Reliability Test, etc.)
- Hot issue troubleshooting and resolution
- To insure all raw material suppliers are in compliance with all OEM standards as called out by the Customer Specifics
- Responsible to maintain, clean (5-S) and insure all safety precautions are followed in the lab and lab equipment at all times
- Material testing and sampling in-house and outside through a TS: credited lab
- Prepare technical documentation and provide support for new program, EC, part launches and process changes at Drive Automotive including PPAP, ISIR Control Plan, FMEA, E/C etc. as it relates to supplier quality
- Conduct LPA on a scheduled cycle agreed on by the area manager with follow up findings noted to audited supplier on follow-up requirements
- Interface with plant quality & manufacturing to ensure responsible suppliers are adhering to the Drive supplier quality requirements
- Responsible for meeting supplier rating targets, ie. PPM, incident rates, MDR’s as it relates to the KOI’s for Supplier Quality
- Onsite visits to suppliers’ location to address quality issues and to insure Drive Automotive requirements for FTQ is being met
- Responsible to reduce risk to Drive Automotive Industries through suppliers RPN values in FMEA’s, lessons learned activities
- Ensure investigation(s) takes place (LPA) on all process failures, such as corrective actions, PDCA as it relates to Supplier Quality
- Coordinate and track progress any related interdepartmental studies or testing needed
- Take additional training to maintain pace with new technology. Will require some personal time
- Able to function effectively using computer software i.e. word, excel, SAP, PP
- Competent understanding of metering devices which measure and yield data for e-coating processes and or sealer applications
- Able to provide clear feedback to the OEM level when needed
- 4 year degree (Mechanical Engineer with a minor in Metallurgy preferred): and/or work history of 5 to10 years of related work experience in an engineering roll with lab and metal background automotive manufacturing environment
- Statistical Process Control Management
Supplier Quality Engineer Rosemount Europe & MEA Resume Examples & Samples
- Set and reinforce expectations for a safe work environment
- Ensure close cooperation with Global SPE and manufacturing sites in Europe & MEA
- Implement Supplier Performance Engineering Strategy to achieve business objectives for quality, speed, and flexibility
- Auditing of suppliers to ensure they met Rosemount expectations and reduce variation in supplier processes
- Advanced Quality Planning Process/Production Part Approval Process - to deliver guaranteed quality and short lead times for source changes, product transfers and new product information
- Initiate Manufacturing Verification Test for source changes, product transfers and new product information
- Ensure control plans are implemented to sustain performance improvements
- Ongoing Monitoring & Control Process - to deliver early warning, and fast, effective issue response worldwide
- Monitor key performance measures, identify opportunities, and implement project plans to drive improved performance
- Provide regular report outs to functional management, including current status and action plans for improvement
- Conduct Supplier Performance Business Reviews to share expectations, strengthen relationships and charter joint projects to deliver mutual benefits
- Ensure suppliers are trained in Structured Problem Solving, Lean & Six Sigma methodology and that management is committed to the use of these tools
- Lead cross-functional, cross-facility projects to improve supply chain performance VACANCY
- Identify and swiftly eliminate barriers
- Champion world class standards within the organization and supply chain
- Languages – Fluent in German and English
- A good team player with a passion for excellence and driving improvements. Is customer focused and has a sense of urgency to resolve issues timely and effectively
- Available for domestic/international travel as required and ability to work on own or unsupervised
- Perform supplier evaluations including on-site audits to assess supplier capabilities, determine approval status, and verify corrective action
- Conduct component and product Quality testing for purposes of supplier and component qualification and improvement
- Evaluate supplier Quality systems, strategies and regulatory compliance via vendor audits
- Bachelors in Engineering is required
- Effective communication and conflict resolution skills
- Effective problem solving techniques
- Understanding of Manufacturing processes (i.e. Injection Molding, Extrusion, and Machining)
- Understanding of Risk Management principles
- Six Sigma Green or Black Belt/LEAN Manufacturing experience a plus
- Supports on-site/off-site supplier quality development including coordination/management of required internal/external resources. Qualifies sub-processes of suppliers
- Ensures quality conformity of supplies via active monitoring of the supplier performance and take corrective actions (incident and complaint handling)
- Executes the contractual definition and agreement on product and process specifications with the supplier (e.g. PQA / MQS)
- Supports incident related liability recovery (CoNQ)
- Produces and completes Supplier Quality Engineering related activities and documentation under direct supervision
- Qualifies Parts, identification of supplier processes for CtQ's, supplier process control plans to ensure part quality; ensuring that the supplied part meets specifications, and the control limits/tolerances for CtQ (critical to quality) parameters are met
- Qualifies and sustains sub-processes of suppliers, including supplier audits
- Ensures that the components/products at the supplier (including spare parts and services) are released according agreed specification and quality requirements
- Supports SCAR management, effective and timely closure and
- 1) Process qualification
- 1) Drive the supplier qualification/re‐qualification process and ensure the supply base is and remain fully qualified and compliant. Support supplier onboarding
- 2) Plan and conduct, or ensure, required supplier assessments including assessment reporting and non‐conformance reporting. Verify effective closure of assessment non‐conformances, by the supplier
- 3) Ensures each supplier is in compliance with the ABB Supplier Code of Conduct, ethics and corporate governance, ABB standards and applicable regulatory requirements. Ensure every supplier is linked to a GUID and all masterdata up to date
- 2) Product qualification
- 1) Schedule, monitor and approve supplier part, material and project subcontractor service activities, as applicable
- 2) Coordinate with other functions/experts like engineering and where applicable includes PPAP, Production Part Approval process
- 3) Perform required product surveillance at supplier manufacturing site
- 3) Customer Complaint Resolution
- 1) Monitor Customer complaints & effectively close with systematic problem solving approach
- 2) Operationally lead and fast execute upcoming supply issues like quality issues, late deliveries, non‐conforming products or project services
- 2) For any issue with likely root cause supplier, prepare a claims case for the responsible buyer
- 4) Supplier development & Continuous improvement
- 1) Develop and support targeted suppliers to achieve conformance with ABB requirements and continual improvement in quality, e.g. reduction of variation; sustainability, service/delivery performance
- 5) Supplier performance evaluation / monitoring
- 1) Monitor and report supplier performance (KPIs), quality issues, and development actions. Initiate and lead, or support, required Supplier Performance Evaluations
- 6) Process and system development & implementation
- 1) Define & develop with local unit counterparts (Sourcing, Quality, Operations, R&D / Technology) local quality procedures & practices
- 2) Ensure that defined systems and practices are in line with existing Group/Division/ BU instructions and procedures
- 3) Ensure full and appropriate utilization of ProSupply+ according to global ABB procedure including required information for supplier classification by our category teams is available
- 4) Ensure full utilization of local system for reporting, monitoring and disposition of quality and on time delivery (OTD). Ensure supplier quality cost is reported according to ABB procedure
- 7) Interface with other functions
- 1) The role requires close cooperation with category teams, responsible buyers, Q&OPEX, Sustainability/HSE, R&D/Engineering and project tender teams, among others
- 2) Represents the “Voice of Supplier” to ABB, e.g. R&D, Engineering, Supply Chain Management, Quality, and Manufacturing
- Experience in Quality assurance of PCB/ PCBA / Electronic assemblies & sub-assemblies
- Experience in Supplier qualification & audits. Preferred certified IQA auditor (ISO9001) or other equivalent International standards
- Six sigma certification – minimum green belt. Should have handled at least 5 quality & process improvement projects involving Cp/Cpk, Pp/Ppk study & DMAIC process
- Familiarity in the finishing of the interiors (home depot)
- Very good computer skills in the field of MS Office
- Practical knowledge of quality tools used in the process of complaints (8D, 5Y, PDCA and others)
- Practical knowledge of metrology and measurement tools
- Knowledge of the principles of logistics complaint – RMA
- Electronics, electromechanical or mechanical commodity knowledge will be advantage
- Decision-making and problem solving skills
- Understanding of Product manufacturing processes, functionality and test is a must
- Ability to work in fast-moving environment with changing priorities
- Analytical and problem-solving skills and good Interpersonal skills
- Experience/Knowledge in RoHS, RoHS 2, REACH and WEEE initiatives and compliance regulations worldwide
- Demonstrated ability to work and perform in team environments
- Proven ability to resolve issues and participate in process improvement activities
- Experience/Knowledge in Quality Systems (ISO 9000/TS16949), Supplier Quality Management, 8D, FMEA, PPAP is a plus
- Fluent Chinese and English is needed, good reporting skill in Chinese & English
- Bachelors in EE, Mechanical, Industrial, or equivalent technical degree
- Disposition nonconforming material and develop plans to prevent reoccurrence
- Perform root cause analysis and develop corrective action plans for supplier caused nonconformance
- Self-starter with a demonstrated ability to focus efforts, overcome obstacles and complete projects
- Project Leadership - Ability to successfully develop and/or complete low to medium complexity processes and/or projects
- Customer orientation & results driven
- Experience with sampling plans, process capability analysis and measurement systems analysis
- Experience working with suppliers
Supplier Quality Engineer Intern Resume Examples & Samples
- Product Quality Processes
- Production Design Improvements
- New Part Qualifications
- New technology Research
- 6-Sigma experimentation and process development
- Process Documentation
- Currently enrolled in a Mechanical, Materials, Biotech, or similar engineering program
- Teamwork skills and ability to collaborate
- High initiative and self motivation
- Good computer skills including Excel, programming, design, and technical searches
- Desire for a hands-on working environment
- Master Quality system
- Certified auditor or supporting experience
- Engineer (Mechanical, Electrical or associated), or
- Bachelor's degree (B.S.) from four-year College or university in Business, Procurement or Supply Chain Management
- Quality management certificates or supporting experience
- Green Belt is advantageous
- Audit and assessment of suppliers 60%
- Reporting & Follow-up 30%
- Problem solving 10%
- A Bachelors degree in Science Technology Engineering Math (STEM) is strongly preferred
- 7+ years experience as a Supplier Quality Engineer in the Aerospace and Defense sector working independently in a regional based assignment
- Relevant technical experience in Cable Harness, Antenna, RF, PWBs, CCAs, Antenna Systems and/or Electronic Components
- Relevant training or desire to obtain certification/s in Quality, such as CQE, Lead Auditor, IPC-600, IPC-610, IPC-620, Six Sigma, other applicable
- This position requires a blend of technical and analytical ability, strong verbal and written communication skills and a high degree of professional acumen
- Proficiency in MS Office software applications. Experience with SAP a plus but not required
- Ability to perform root cause and corrective action
- Good technical writing, diplomatic, factual, and excellent communication skills
- Ability to develop strong working relationships with the suppliers and internal customers
- Ability to interpret a drawing, SOW and other technical documentation, GD&T, as well as ability to develop an associated inspection plan/compliance matrix
- Ability to interpret data, analytical, SPC, identify trends and develop preventative actions
- Experience with AS9100, ISO:9001 Quality Systems; Supplier quality requirement flow down, FAI and/or FMEA strongly desired
- Ability to travel to suppliers and support short notice trips. Travel will be high within assigned region and will require regular day trips, as well as overnight travel to surrounding area – estimated 75%+
- BS/BA in Engineering, or equivalent combination of education and experience
- Min 8-10 years of relevant experience
- Ability to interface with all internal and external stakeholders
- MS Office experience required
- Technical knowledge of machining and casting processes is desirable
- Lean and/or Six Sigma improvement skills
- Thorough understanding of ISO 9001 standard
- Experience as internal or supplier auditor
- Demonstrates a good grasp of knowledge and principles of Supplier Quality practices and applies through successful completion of assignments
- Successfully applies knowledge of fundamental concepts, practices, and procedures of particular area of specialization
- Successful demonstration of Key Responsibilities and Knowledge as presented above. Advanced degree may be substituted for experience, where applicable
- Must be able to interface with all levels of management and work in a highly integrated, cross-functional manner
- May provide general guidance or train lower level support staff
- Perform product assurance activities associated with a manufacturing environment to ensure that the dimensional, materials and visual characteristics of a product's design, as documented on drawings, specifications and quality standards are consistently produced
- Perform process and system audit of suppliers and maintain a working knowledge of ISO and TS quality systems requirements to support the suppliers
- Review and approve supplier Production Part Approval Process (PPAP) submissions for new items and changes to existing product components
- Monitor quality data within the operating systems to ensure accuracy of data and develop reporting systems to accurately document and record monthly and annual supplier trends and performance data
- Perform periodic reviews and continually monitor quality specifications to ensure supplier compliance
- Facilitate deployment of supplier metrics across supply base
- Supports plants in supplier quality issues and drives corrective actions with the suppliers
- Facilitate supplier quality roadmaps leading to improved supplier performance metrics
- Skill set in tight tolerance complex stamped components and plated materials
- BS Degree in Engineering required, preferably Mechanical or Electrical Engineering
- Master’s Degree preferred
- 0-2 years of relevant experience as Quality Engineer in TS16949 automotive environment (Tier 1 and OEM)
- Experience with International Suppliers
- Experience using 5-Why and 8-D problem solving tools
- Able to work effectively in a team environment
- Proficiency working with Microsoft Excel, Word, SAP and other software products
- Excellent verbal and written communication skills and have project management capabilities
- Must be able to lead and motivate engineering resources within a matrix organization
- Candidate should be self-directed individual possessing managerial courage and business acumen
- Occasional travel within US and Mexico is likely
- Strong skills in auditing and evaluation of new or critical suppliers, conduct audits and Quarterly Business Reviews (QBR) with suppliers to evaluate supplier performance. (Preferred background: automotive or electronic industry.)
- Work with suppliers to resolve issues identified in audits and reviews. Responsible for trouble shooting, root cause analysis and on-site support at suppliers in case of quality or capacity problems
- Train and up skill suppliers on quality standards, quality and LEAN tools, TE requirements, best practices, 8D-Reporting, Control, SPC, FMEA, Control Plan, and APQP. Six Sigma knowledge is an advantage as well as audit skills for tier 2 suppliers
- Negotiate with suppliers on KPIs, supplier performance, QBRs, audit results, corrective action plans, TE standards and requirements
- Collaborate and partner with suppliers to ensure the supplier
- Knowledge and experience in use of Quality tools (6-Sigma, Product compliance, LEAN manufacturing, Quality standards, Project Management skills
- Bachelor’s degree in Engineering (Mechanical engineering, Process engineering, Manufacturing engineering preferred)
- 5 years of professional experience
- Accredited to conduct & demonstrated experience of conducting supplier audits
- Understanding of the market, processes, supplier contractual agreements, competitors
- Technical knowledge and demonstrated experience in engineering assignments: Process manufacturing knowledge, supplier industry knowledge
- Ability to pick up new information and processes quickly
- Proactive and self-starter
- Fluent in English and Spanish
Chassis Supplier Quality Engineer Resume Examples & Samples
- Bachelor's Degree (or equivalent) from an accredited University
- Minimum of 7 years work experience in an automotive environment
- Knowledge of automotive process and components
- Green/Black Belt
- Experience in Manufacturing, Engineering, Quality and Supplier Quality
Electrified Powertrain Supplier Quality Engineer Resume Examples & Samples
- 5+ years of experience in Electronics industry with working knowledge in quality, engineering or manufacturing
- Working knowledge full, partial and mild hybrid vehicle electrical systems including Power Management (High/Low Voltage, batteries, inverters, charging systems) and drive systems a plus
- Computer literacy in Windows, Excel, PowerPoint, Access and Basic understanding of basic statistical methods including SPC
- Ability to lead root cause investigation of electrical and electronic devices at the IC, PCB and module/systems Level
Entry Level Supplier Quality Engineer Resume Examples & Samples
- Working cross functionally with Engineering, Manufacturing, and Purchasing to ensure proper designs, suppliers, and manufacturing processes are selected
- Driving change within both Plant Manufacturing and component suppliers to resolve component issues
- Ensuring component suppliers processes are robust and capable
- Leading problem solving activities with internal and external organizations
- Managing key component quality milestones
- Developing and presenting program status updates and articulating open issues to senior leadership
- Bachelor of Science degree in Mechanical, Electrical, or Chemical Engineering from an ABET accredited program
- Bachelor's degree or higher completed by December 2016 / June 2017
- GPA of 3.0 or higher (based on a 4.0 scale)
- Ability to work in a manufacturing facility
- Previous internship/co-op experience or previous manufacturing, design, or engineering work experience
- Proficient interpersonal skills and the ability to work effectively in a cross-functional team
- Comfortable completing complex technical analysis
- Ability to travel within the NAFTA region
- Bachelor of Science degree in Mechanical Engineering or Electrical Engineering from an ABET accredited university. A bachelor's degree in Aerospace/Aeronautical, Biomedical/Biomechanical/Bioengineering, Chemical, Materials, Metallurgical, or Mechatronics may also be considered
- 2 1/2+ years of work experience in Quality, Supplier Quality, Engineering, Manufacturing or a related field
- Prior Internship Experience within Supplier Quality, Engineering, or a related field
- Bachelor of Science in Electrical or Mechanical (with a strong electrical background) Engineering from an ABET accredited university or related Bachelor's degree with 5 years commensurate experience; Bachelor's degree in Aerospace/Aeronautical, Biomedical/Biomechanical/Bioengineering, Chemical, Materials, Metallurgical, or Mechatronics may also be considered
- Minimum 5 years work experience in quality, engineering, or manufacturing
- Familiar with WCM methodology
- Experience with Wiring, Clusters, Radio 7 Energy Management
- Problem Solving Skills: Green Belt or Black Belt
- Quality Certifications: CQE, CRE
- Proven ability to manage multiple projects and tasks Effective written and verbal communication skills
- Ability to travel within the NAFTA region Comfortable with complex technical analysis
- Works independently to establish quality criteria, plan for implementation, and execute quality plans for all products. Includes inspection planning (PPIP), sample approvals (FAS & LS) and training on requirements
- Completes supplier surveys and associated supplier approvals
- Implements required quality metrics and uses that data to address supplier improvement and concerns
- Effectively problem solves production issues as they arrive, related to materials, components, or packaging product
- Travels independently throughout the supply base to address issues and concerns, adjusting to different work environments at suppliers’ facilities
- Heads up efforts for nonconforming material review and corrective action assignment to the suppliers
- Supports the Supplier Quality Manager in carrying out higher level requirements and projects
- Interfaces with upper management and provides needed feedback for important decisions
- Works effectively and collaboratively with others
- Bachelor's degree in an Material Science or in an Engineering discipline
- 5+ years of experience in Quality Engineering within a plastics manufacturing/processing environment
- Experience with statistical software (e.g. mini-tab, etc.)
- Exhibits a solid product and manufacturing process knowledge base and have growth potential to lead small teams (2-3 people)
- Good problem solver - can work independently to make important decisions
- Able to communicate effectively with a wide range of people
- Strong knowledge of Quality systems, Quality process controls, material performance testing
- General understanding of Advance Quality Planning, e.g. AIAG PPAP’s
- Strong analytical problem solving skills and sound statistical application in areas such as DOE, sampling techniques, regression, reliability, FMEA, hypothesis testing etc
- Experience in Polymer, Paint and Wafers
- Lean Manufacturing or Six Sigma certification
- Minimum 12 years of experience in QA, including quality systems, standards, metrics, and tools
- Demonstrated knowledge and expertise in: NPD, supplier development, risk/issue management, implementation planning and supplier training
- Experience in launching medical device products with software & electronic components for large scale platform or breakthrough projects
- Demonstrated track record of effectively influencing without authority with all levels of an organization and leading effective/successful change initiatives
- DFSS/DMAIC Six Sigma Black Belt preferred
- Certified Quality Engineer (CQE) preferred
- Self-starter, with the ability to work independently under minimal supervision and with all levels of managers, associates, and clients
- Strong analytical and statistical problem solving tools
- Assist quality assurance leadership in the management of select contract manufacturing sites and raw material suppliers engaged in the production of Johnson and Johnson products
- Provide product team support for quality system design and audit, compliance assessment, and for support of steady state manufacturing processes
- Oversee audits of all quality system categories to assess compliance to process excellence standards
- Handle complex technical issues for manufacturing processes that are to be transferred to satellite facilities
- A minimum of 1 year of experience in a GMP and/or ISO regulated industry is required
- Operations supplier quality experience is preferred
- Both, FDA and ISO regulations knowledge is preferred; FDA CFR Part 820 and/or ISO 13485 knowledge is highly preferred
- Six Sigma, Lean, or ASQ Certification and/or trainings are preferred
- This position will be based in Raynham, MA and require up to 25% travel, including possible international travel.Quality (Eng)
- Responsible for partnering with the Business Units and Supplier Development Program Managers to perform Supplier assessment, approval, qualification, and surveillance
- Develop and activate a process for leveraging an existing pool of cross-business technical resources into the supplier development program for South Africa
- Assist in accessing technical guidance in manufacturing and repair processes (e.g., welding, machining and assembly) to a global supplier base to assure product & process compliance with engineering drawings and specifications
- Ensure supplier compliance with regulatory and reputation requirements
- Perform regular audits at supplier sites to ensure conformance to manufacturing control plans
- Develop positive relationships and work closely with Sourcing Managers to manage and implement supplier/engineering changes, New Product Introductions, and transfers
- Evaluate supplier capabilities and develop in partnership with suppliers, capacity expansion plans
- Implement supplier scorecards to improve suppliers cost, quality, service, and inventory
- Drive corrective actions to address quality issues to improve the scorecard
- Assist manufacturing process teams on determining solutions to technical problems
- Drive lean manufacturing initiatives at suppliers to support deflationary goals
- Drive design changes to reduce total product cost & improve manufacturing
- Bachelor's Degree in Technical area from an accredited college or university
- Minimum of 5 years of experience in Supply Chain, Supplier Quality or Engineering
- Demonstrated experience in developing and implementing vendor Qualification
- Experience with cross-functional program management
- Experience in qualification of forgings, castings and fabrications; understanding of related manufacturing processes
- 3+ years of experience in SQE or similar roles
- Strong Project Management experience
- Strong written & communication skills – English & Russian
- Position requires up to 70 % travel
- Shop floor experience: quality management (QMS) role with a manufacturing company (automotive industry)
- Ability to work in broad cross-functional and global business environment
- Demonstrated technical aptitude and passion for quality; Six Sigma training (for GE employees only)
- Demonstrated leadership and organizational skills, inclusiveness
- Work closely with GE Industrial businesses Design Engineering, Product Service Engineering, SQE teams, Commodity Leaders, Buyers, business & GGO Sourcing and Project Management teams, Supplier Performance Leaders on all acitivities required to effectively support development of supply base in Russia & CIS and drive identification, qualification & development of RUCIS regional suppliers for electrical components, electrical machines and engineered systems
- Bachelor/Masters Decree in Electrical Engineering
- Experience in qualification of electrical machines, componens and/or engineered systems; understanding of related manufacturing processes
- Experience with special coating, VMI
- Responsible for improving quality performance via suitable Corrective Action and Quality Improvement Plan (QIP)
- Drive improvements in quality and in delivery rate by working actively with suppliers and on their processes
- Develop positive relationships and work closely with Supplier Quality Managers to handle and implement process/product/engineering changes, New Product
- Introductions, and production transfers
- Interface with Suppliers and Sourcing to drive Quality improvements
- Deliver results as measured by key metrics, such as supplier yield, field defect rate, supplier quality plan engagement/effectiveness, and corrective & preventative actions implementation
- Drive improvements using Supplier Scorecards and plan Supplier audits, ensuring compliance, product integrity and improvement plans introduction
- Apply Six Sigma tools and analysis
- Problem solving and related relevant methodologies knowledge and application
- Provide Quality and Engineering expertise, requiring advanced/specialized skills, to drive the solution of urgent issues
- Specify, develop, and accept advanced technology, quality requirements and test equipment choice
- Collaborate with Incoming Inspection Operators to work as a team in problem solving and Incoming Inspection lean projects
- Specify and develop product acceptance/test procedures that relate to a state of the art product and process
- Lead investigations of supplier quality escapes and major quality issues
- Significant experience in a quality environment or supplier quality
- Knowledge of machining and raw material processing and inspections
- Fluent in English and Italian
- Strong interpersonal and driving skills
- Quality Engineering expertise requiring specialized skills
- Candidates from Avio Aero Global Supply Chain should apply; qualified candidates are encouraged to apply
- Primary interface with suppliers
- Monitoring materials, services & processes (external & internal) to assess new vendor opportunities,
- New vendor screening & selection (participate in cost benefit analysis),
- Cooperation with vendors, designated inspection agency and/or other parties involved in the inspection process,
- Participate in make or buy analysis,
- Qualification process & documentation,
- Qualification budget monitoring,
- Clarifying technical requirements,
- Supporting supplier base in case of new product designs,
- Supporting site sourcing, operations & quality functions,
- Supplier defect monitoring & follow up,
- Supplier charge back negotiations,
- Suppliers approval process participation,
- Reporting & coordination (local & global)
- Active engineering experience (technical experience)
- Strong project management skills, ability to prioritise,
- Ability to work with application software (Microsoft),
- Knowledge of Hungarian suppliers (mechanical industry),
- Experience working with integrated operational systems (Oracle),
- Driving licence
- The ideal candidate will have 5+ years of relevant experience with expertise in optical inspection/metrology, laser triangulation, and defect detection
- Experience with digital imaging, camera system, and image processing is a definite plus
- Experience with 2D/3D triangulation laser system and CCD inspection system such as Keyence, Cognex, and/or Visco
- Familiar with mechanical metrology system qualification process, such as GRR, Correlation, Stability and Reliability
- Expert understanding of geometric dimensioning and tolerancing
- Deep understanding of optical, software filtering and judgment algorithms
- Excellent data analysis, statistics, documentation, communication, project management skills
- Intermediate knowledge of system layout, architecture and cycle time optimization for optical, motion and mechanical systems
- Familiarity with the properties and process used in microelectronics fabrication and PCBA assembly
- Committed to work under high time/deliverable pressure with solid results
- Positive attitude facing complex situations to reach constructive win-win solution
- Collaborate with functional teams and develop vision for Supplier Quality Management that aligns with business needs
- Drive the highest supplier quality standards for all new and existing products by proactively using Advanced Quality Planning tools such as Failure Modes and Effects Analysis, Process Control Plans, Process Capability and Design of Experiments
- Review supplier process flow and validation systems
- Initiate and manage supplier quality initiatives and strategic plans related to both new and sustaining products
- Evaluate prospective suppliers to ensure capabilities and systems align with Nutanix requirements
- Lead supplier audits to ensure conformity to contractual requirements as well as Quality System Compliance
- Utilize the Supplier Corrective Action Request (SCAR) program to ensure suppliers meet performance requirements in quality and service throughout the product life-cycle
- Work closely with suppliers to assure applicable systems are in place for the identification, processing and disposition of non-conforming materials provided by suppliers
- Identify and implement improvements to supplier quality with respect to measurements such as PPM, initial quality, and SCAR response
- Manage daily tactical activities such as first article inspections, quality notifications, and material qualification activities
- Lead supplier quality discussions at both internal business review meetings and supplier QBRs
- Demonstrated use of effective written and oral communication skills
- Ability to mentor new associates and other team members
- Lead a proactive role to continuously improve processes and systems
- Ability to work closely with all Engineering groups, Supply Chain and Suppliers to ensure successful product introduction and life cycle management
- Identify Critical to Quality processes and product metrics and drive sustainable and significant improvement
- Lead cross functional audit, manage any 3rd party audits and train internal auditors
- Ability to balance both Quality goals and Business needs of the organization
- Must be able to adapt to an ever-changing work environment
- Take accountability to execute personal development plan (as defined in conjunction with immediate manager) to grow within the current role and prepare for future roles
- Minimum of 5 years of experience with a Master’s degree or 8 years of experience with Bachelor’s degree or equivalent work experience
- Must have supplier quality/qualification experience in a demanding fast paced environment
- Experience in troubleshooting/problem solving of manufacturing and/or assembly processes is required
- Experience facilitating quality reviews and demonstrated use of quality assurance tools
- A strong knowledge of statistical tools is preferred
- Experience with various manufacturing processes/commodities such as electro-mechanical assemblies, plastic injection molding, printed circuit assemblies and Semiconductor fabrication is preferred
- Experience in Supplier Management and/or Engineering preferred
- Knowledge/experience with risk management throughout the supply chain is preferred
- Ability to mine data for growing trends and driving sustained continual improvement
- Experience with Microsoft Office tools is required
- ASQ certification for Quality or equivalent preferred
- Familiarity with a major PLM tool such as Agile PLM or Arena PLM is preferred
- Evaluates suppliers for suitability to be added to the Approved Supplier List, by following criterion specified in GA-EMS procedures
- Coordinates and conducts onsite supplier quality audits, both planned and unplanned
- Critiques corrective action plans submitted by suppliers and coaches suppliers to satisfactory closure of corrective action requests
- Provides face-to-face, web based, and AT&T Connect Conference type training to suppliers on how to fulfill GA’s quality requirements
- Acts as liaison between GA and suppliers on quality issues
- Develops, interprets, and applies quality standards to meet a myriad of contractual requirements
- Initiates and contributes to continuous improvement of supplier quality management related processes and procedures
- Collects value added metrics
- Typically requires a bachelor's or master's degree in engineering or related discipline and five or more years of related experience with a bachelor's degree or three or more years with a master's degree. May substitute equivalent experience in lieu of education
- Training in ISO 9001 and experience conducting quality system audits of suppliers
- Documented history of strong proficiency with root cause analysis investigations and corrective action implementation
- Demonstrates strong writing, technical, and analytical problem solving skills
- High proficiency understanding and applying the full MS Office Suite
- Must be able to apply solid understanding of inspection methods and have an intermediate level of knowledge related to computer operations and applications
- Must have the analytical ability required to develop creative solutions to routine and non-routine quality issues and demonstrate the skills required to present those solutions to internal and external customers
- A strong understanding of metric collection to accurately prepare statistical reports and technical documents in support of company quality objectives
- Must have good leadership skills to direct staff members and ensure project costs and schedules are maintained
- Able to travel within the CONUS
- Preferred: ASQ Certified Quality Engineer
- Execute and refine techniques for early program engagement during supplier solicitation, pre and post PO award, as well as pre-production phase
- Work with cross-functional team members for Design for Manufacturing/Design for Test, Critical Design Review on new/complex/strategic awards
- Execute Pre Award Review to review the PO and the Technical Data Package (TDP) to ensure that all the requirements are understood, and Key Product Characteristics (KPCs) with their associated processes are identified
- Execute Post Award Review process to review how the Supplier has implemented all the requirements of the PO and TDP, as well as determine what type of process controls have or will be implemented to control KPCs
- Plan and execute supplier process alignment to vetted requirements, Process Failure Mode Effects Analysis (PFMEA)
- Execute Manufacturing Readiness/Test Readiness Reviews (MRR/TRR)
- Review/Approve supplier Compliance Matrix Review (CMR) for technical data package requirements and quality control plan
- Analyze program requirements and derive QA related activities, participate in the development and execution of quality requirements flow down
- Lead supplier risk management plan and appropriate levels of supplier oversight
- Determine the supplier sell off and Inspection Plans
- Provide Lessons Learned to Supplier Development processes and/or Design Engineering
- Utilize and participate in the CAR/CAPA related process, particularly for major or complex Supplier CARs
- Develop standardized and appropriate QA inputs for Statement of Work (SOW) on complex, high value, strategic awards
- Coordinate closely with Engineering, Manufacturing, Supply Chain Management, Program Management and Program Quality to support new strategic awards, awareness of materials critical to quality and internal customer support
- Lead quality and manufacturing process audit teams at suppliers in accordance with industry standards and specific L-3 program initiatives
- Support Lean Manufacturing and Six Sigma initiatives to reduce cost, remove variability, and improve both quality and delivery within supply base
- A Bachelors degree in Science Technology Engineering Math (STEM) is required. A Master’s degree in Engineering or Business preferred
- Experience in all phases of the product lifecycle with emphasis on initial quality planning activities
- Experience with supplier development and continuous improvement activities are preferred
- Project management skills such as identifying required resources, developing project plans, and driving project execution
- Proficient at preparing and presenting clear and concise presentations to suppliers, customers, and management
- Experience with risk management techniques
- Experience identifying key process parameters/characteristics and developing PFMEA
- Ability to perform and council suppliers on root cause analysis and corrective action
- Ability to interpret an engineering drawing, SOW and other technical documentation, as well as ability to develop an associated inspection plan/compliance matrix
- Ability to interpret analytical data, SPC, identify trends and develop preventative actions
- Experience with AS9100, ISO:9001 Quality Systems
- Ability to support travel to suppliers, including short term and unplanned for high visibility/complex quality issues. Travel estimated around 40%
- Engineering Degree in relevant discipline (Industrial, Production or Electronics) or other relevant technical background
- Project Management experience: Driving improvement projects with suppliers and internal stakeholders e.g. QA/QC, Production team, Supply Chain Management and R&D
- Supplier Management skills: Experienced in achieving results on-site at Asian suppliers
- Technical and Analytical
- Manage and meet customers’ requirements
- Secure procurement deliverables (Supply Chain process documents, KPI reports and improvement plans) are according to standards agreed with customers
- Drive supplier performance improvement/recovery action plans primarily with suppliers for Aeronautical products
- Request and manage closing of 8D reports (NCR and delays) where applicable
- Drive analysis of Non-conformance reports
- 1/. Support quality and manufacturing staff across the business on supplier quality related items
- 2/. Development, Monitoring and Reporting of Key Performance Indicators (KPI’s) to ensure objectives are met
- 3/. Collect, evaluate supplier quality data to identify improvement opportunities within the supply chain
- 4/. Development of a supplier audit program and conduct audits to ensure expectations are being maintained
- 5/. Review supplier manufacturing process and collaborate with them on process improvements opportunities
- 6/. Support Procurement with Supplier Qualifications and Disqualification activities
- 7/. Ensure the Production Part Approval Process (PPAP) is being utilized as required
- 8/. Review and approve PPAP submissions prior to introduction into manufacturing
- 1/. Minimum of 5 years experience in a quality engineering role including audits and long term corrective action implementation
- 2/. Ability to resolve complex problems independently and lead teams to implement solutions
- 3/. Broad knowledge of quality systems and approaches including ISO 9001:2008 and ISO 9001:2015
- 4/. Knowledge of process improvement tools and methodologies such as Root Cause Analysis, Six Sigma, Kaizen and Lean principles
- 5/. Good communication skills and familiar with communicating on all levels of an organization
- 6/. Technical background with working knowledge of electrical and mechanical components including the manufacturing process to produce them
- 7/. Competency in Microsoft Office Suite required; SAP Competency preferred
- 8/. Desired Certifications – ISO 9001 Quality Auditor
- 9/. Bachelor of Science or equivalent combination of education and experience
- Participation in supplier qualification in cooperation with Global SQE
- Review and assess supplier compliance to customer specification and other regulatory standards
- Initiate Supplier Quality Complaints when non-compliance is evidenced
- Follow up supplier quality events till closure
- Evaluate supplier quality performance
- Initiate Improvement Plan with supplier in case of under-performance
- Liaise with co departments PCNs
- Create specific work instruction for IQC
- Coordinate rework and selection activities
- A minimum of five years direct experience manufacturing processes and production documentation
- General understanding of CM (contract manufacturing) business is preferred
- Experience with supplier interface and communication
- Demonstrated knowledge and understanding of quality management systems (QMS)
- Creative problem solving ability and very results oriented
- Demonstrated experience working with customers and with cross-functional groups
- Strong computer skills including Microsoft Office Suite
- Excellent people and project management skills
- The ability to be self-motivated and to handle multiple tasks and changing priorities
- Strong communication, organization and presentation skills
- Experience with QDR (quality deviation report) systems is preferred
- Implementation of the Supplier Quality Function related to medical segment
- Responsible for Supplier Qualification and supplier development, new parts approval execution and improvement, communication between supplier’s and customer’s relevant function
- Claims management requiring extensive contact with suppliers utilizing 8D methodology
- Taking advices in order to improve corporate processes
- Organization of escalation meetings with suppliers
- Supplier auditing
- Ensures that all part and supplier qualifications are performed in a timely manner to support business requirements
- Engages with internal stakeholders to ensure all requirements and priorities are fully understood
- Definition of supplier development measures and driving the implementation in cooperation with the cross-functional team
- 3-5 year relevant experience
- MS Office experience
- Continous improvement mindset
- Experience in medical segment is an advantage
- Thorough understanding of ISO 9001 standard, ISO 13485 is an advantage
- Experience as internal or supplier auditor is an advantage
- Successful demonstration of Key Responsibilities and Knowledge as presented above
- Perform supplier quality role in PRO Launch for new product introduction, work out Supplier Production Control Plans, Supplier Production Part Approval Documentation, Supplier Process Risk Assessment & Mitigation, Supplier Error Proofing Plans
- Minimum 7 years experiences in supplier quality management
- A strong mechanical background in working with Packaging, or Plastic Molding and Metal Stamping suppliers
- Bachelor's Degree or minimum 5 years of related experience in Quality Engineering. Experience and background in machining, circuit card assembly, special processes (welding, brazing, plating etc.)
- Must work well with others in a team and commodity buying structure and have experience in leading cross-functional teams in accomplishing goals
- Must possess effective communications skills, both oral and written for all levels of the organization
- Ability to multi-task in an environment of competing priorities. Provide alternate plans and options to project challenges
- Must conduct themselves in a professional, constructive, and cooperative manner with all levels of personnel while fulfilling job responsibilities
- Must be able to lead Suppliers to improve performance
- Must have computer skills including advanced proficiency with MS Word, Excel, Power Point and Access
- Must have ability to work independently and be self-directed to complete tasks
- Have industry experience with manufacturers of aerospace and defense industries
- Ensure compliance with all Mission Assurance related contractual requirements, division policies and procedures, while contributing to the projects’ process implementation and process effectiveness
- The successful candidate will demonstrate ability to perform: internal and external process audits, systems/software/hardware life cycle quality engineering activities, participation in the peer review of systems/software development and test, participating in stress testing for client and server software/hardware inspections, hardware/software configuration verification, maintenance and status of request for actions and corrective and preventive action databases, conduct independent risk assessments, perform risk management, review/inspect and sign off on deliverables, identify and implement process improvements, and maintain assurance of contract and policy requirements
- Demonstrate excellent decision making capabilities, problem solving ability, strong verbal and written communication skills, and the ability to work closely and effectively with project personnel
- Mechanical/Electrical Engineering Degree and 2+ Years’ experience
- Contract Manufacturing (CM) experience is a plus
- Knowledge of Print Wiring Board (PWB) and Circuit Card Assembly (CCA) specifications and processes is a plus
- Experience with Digital Product Definition Data Practices (ASME Y14.41-2012)
- SAP (MRP) experience
- Interface with ASL suppliers, engineering, operations, manufacturing, service/repair to implement effective supplier quality corrective actions (SCAR’s) and quality improvements minimizing cost of quality events
- Monitor, analyze and report monthly supplier quality performance (DPPM, FFOR, Consumption, and Yield). Collect and maintain supplier quality performance metrics
- Design and develop receiving inspection plans to ensure plans to ensure verification of purchased product is compliant to required material specifications
- Management of PPAP (Purchased Parts Approval Process) to ensure product/process V&V activities, first article inspection of components, parts or high-level assemblies meet requirements as defined by Invivo-PH
- Ensure supplier early involvement/input into product requirements and design specification and supplier participation in design reviews
- Plan, schedule and conduct supplier on-site audits (QMS, product, process, for-cause) to ensure defined audit scope and Q&R requirements are met
- Participate in the different nonconformance product reviews (MRB meetings) for disposition, defect documentation and RTV/RMA processing
- Drive structural quality and process improvements such as quality agreements, risk assessments, supplier classifications, sustainability agreements, and quality specifications in collaboration with commodity managers, Q&R and engineering
- Participate and support QMS management reviews for supplier quality key metrics
- Support all quality and applicable regulatory functions (ISO13485, FDA 21 CFR 820) to resolve supplier related complaints, recalls, DFOA’s, CAPA’s, and SCAR’s
- Ensure audit readiness for internal/external audits of purchasing and supplier quality controls
- Develop positive relationships with supplier account managers (SAM’s) and Commodity Manger in the process of supplier change assessments (SCA’s), new product introductions (NPI’s) and supplier transfers
- Knowledge of RF Coil system designs, specification and analysis
- Extensive knowledge of engineering and design principles related to Invivo coils products
- Knowledge of IPC manufacturing standards
- Ability to effectively utilize company provided software for engineering design, complaint tracking and document change management
- Electronic manufacturing background, preferably in a Medical Device Manufacturing environment
- The ability to provide timely and accurate reports of customer complaints and reported defects
- Working knowledge of appropriate global medical device regulations, requirements, and standards, such as 21 CFR Parts 803, 806, and 820, ISO13485, ISO14971, European Medical Device Directive (93/42/EEC), Canadian Medical Devices Regulation (SOR/98-282), Japanese MHLW Ordinance 169, and ISO 9001
- Bachelor’s degree in an engineering discipline and 3+ years of medical device experience or equivalent combination of education and experience
- ASQ – CQE, CQA, CSSBB or CSSGB preferred
- Lean – Six Sigma experience preferred
- Manage Supplier Quality related activities for purchased materials for electro-mechanical commodities such as printed circuit board assemblies (PCA’s), power supplies, cables, battery packs, plastics, sheet metal, machined parts, OEMs (displays, medical assemblies), labeling, etc
- Work with suppliers to ensure all necessary quality activities are rigorously addressed during initial product release and change such as: process mapping, process FMEA, process control plan, process validation (IQ, OQ, PQ), GR&R, MSA, line release, ramp monitoring, etc
- Ensure supplier management strategy aligns with quality goals. Focus on quality issue resolution via an 8-D based Supplier Corrective Action request process. Resolve quality issues via structured quality methods in order to ensure efficient and effective root cause analysis, and corrective / preventive actions that ensure there is no recurrence
- Experience:Minimum of 7 years industry experience in Quality or supplier quality engineering in manufacturing of electro-mechanical systems/products/solutions. Preferably more than 4 years’ experience in the medical device industry
- Competencies and skills: Demonstrated knowledge of manufacturing processes for commodities such as printed circuit board assemblies, power supplies, cables, custom battery packs, mechanical parts (plastics, machined, sheet metal), cables, etc. Experience with all aspects of supplier quality management: quality concepts/tools/methods (e.g. FMEA, DOE, IQ/OQ/PQ, MSA, GRR, 8D, etc.), quality issue resolution and quality monitoring measures. Knowledge of the Purchasing function and associated commodity, supply base, quality and data management considerations. Understanding of Procurement, Supplier Relationship Management, Material and Supplier Quality and Data Management areas. Experience in a regulated environment, medical preferred. Certified auditor for ISO System, ISO13485 is preferred. Knowledgeable in SAP Quality Management, Mini-Tab, Query tools such as Business Objects, web-based systems, and MS Excel (power user). CQE, six-sigma Black Belt or Green Belt is preferred. Fluent in English and Good command of Chinese Language skill(spoken and written) is a must
- Bachelor's degree in Science or Engineering discipline
- 2+ years of experience in the medical device industry or highly regulated industry
- 3+ years of Supplier Quality experience in the medical device industry
- Lean / Six Sigma training and working experience preferred
- Fundamental knowledge of ISO and FDA requirements for medical device industry
- Solid leadership skills to lead cross-functional teams to support business needs and resolve product-related or quality-related issues
- Good orgnizational and project management skills
- Computer skills (Microsoft Word, Excel, PowerPoint)
- Working knowledge in Statistical Tools (Design of Experiments, Measurement Systems Analysis, Process Capability and Statistical Process Control)
- Strong leadership skills to lead cross-functional team on problem solving or process/product improvement projects
- Strong communication and influential skills to lead improvement projects or problem solving efforts with external suppliers
- Certification in Quality Systems Lead Auditor preferred
- Develop and implement procedures for random audits on raw materials, work in process and finished goods to verify product specifications
- Determine critical characteristics and process specifications for various products
- Gather and analyze data to determine if existing processes and equipment have statistical process capability with respect to engineering standards
- Develop and execute various physical tests to validate product conformance to performance specifications
- Interface with engineering and manufacturing to perform root cause analysis of non-conformances and assist with corrective action
- Assist with disposition of non-conforming product
- Work and communicate with Suppliers on non-conforming product, new product development and quality system planning
- Support all New Product Launches (at a minimum: create PPAP documentation, create Test Plan, validate all process / product parameters)
- Participate in projects to reduce COF (specifically: Plant Scrap and Warranty Complaints)
- Minimum of 3 years experience in a plant/operations environment
- Supplier qualification and production product validation
- Technical coordination between suppliers and internal Siemens organizations to resolve supplied material Quality issues
- Implementation of containment, root cause analysis, and corrective action for supplier related issues
- Development of suppliers to reduce defect rates, and decrease cost of supplied materials
- Deploy the SSQM - Schneider Electric Quality Management System in Costa Mesa Facility
- Conduct quality system evaluations of new and existing suppliers
- Conduct material process and quality plan audits of existing suppliers as needed
- Develop key suppliers on Schneider Electric’s expectations, systems and performance objectives
- Respond and drive rapid resolution to emergency quality and delivery issues
- Bachelor of Science in Engineering (Mechanical, Electrical, Electronic or Industrial Engineer)
- Availability to travel, position requires 30% travel (domestic and/or international)
- Knowledge of manufacturing processes, FMEA, quality control plans
- Experience in qualification of purchased parts
- Competent in driving improvement through problem solving methodologies - such as 8Ds
- 2 or more years work experience in manufacturing areas such as: quality, manufacturing, design engineering or supply chain
- This position will report directly to the Supplier Quality Manager
- Coach/Train the supply base on Schneider Electric’s expectations, systems and performance objectives
- Respond and drive rapid resolution
SMT Supplier Quality Engineer Resume Examples & Samples
- Strong technical background in SMT/PCBA manufacturing and Quality management. Minimum 3-years’ experience working with electronic assemblies and/or components required
- Bachelor’s Degree in Engineering from an accredited college or university preferred. Electrical Engineering degree strongly preferred
- Familiar with soldering materials, PCBA process and electronics components, testing & acceptance criteria. Knowledge with or certificate with SMT, IPC- A600, IPC-A610, IPC-A620, J-STD-001 preferred
- Motivated by driving Continuous Improvement programs and application of Lessons Learned
- Strong understanding of statistical analysis and problem solving methods and tools. Ability to effectively use Six Sigma DMAIC process to define, root cause, and resolve issues
- Lead PPAP qualification activities associated with transition, supplier request and new parts
- Utilize standard Honeywell processes to audit and approve new suppliers associated with the assigned commodity areas
- Expand commodity knowledge to maintain expertise and be a local expert for Sourcing, Engineering, and Marketing teams
- Lead / Support efforts to fully realize cost savings opportunities
- Project Management - will be expected to identify and implement projects with a high impact to the business. As such, should possess proven track record of successful leadership of high impact projects
- Demonstrated capability in identifying Best Practices and leadership in successfully implementing these
- Must be willing to work in a results based, fast paced environment, with minimal supervision
- 3-5 years work experience and strong knowledge related to the manufacturing, design, and use of Mechanical components – Fasteners/hardware, springs, machining, stampings, die-castings. Knowledge of raw materials/metals/plastics/resins preferred as well
- Six Sigma Green Belt certification desired. Black Belt it’s a plus
- Manage supplier qualifications to ensure that assigned suppliers are capable of producing material, and/or components that will consistently meet GE Engineering drawing and specification requirements
- Perform robust Root Cause Analysis to solve quality issues and prevent recurrence
- Provide Sourcing Quality input to Engineering during product design reviews
- Conduct supplier on site visits per year as needed. Close all findings identified with supplier with focus on major findings and timeliness of corrective actions
- Strong background in interpretation of Engineering drawings/specifications, methodology, and manufacturing process planning/evaluation. Must understand GD&T and be able to lead technical design and manufacturing reviews with suppliers
- Black Belt certified or equivalent (demonstrated experience). Core competencies of a BB are a must for improving supplier statistical capability, evaluating readiness to serve, including capacity verification
- Ability and willingness to travel internationally. Travel >30%
- Monitor process capabilities at White-Rodgers’ Contract Manufacturer’s and ensure all Technical Specifications and requirements are met
- Conduct Supplier ESAC audits to support White-Rodgers Cost Reduction programs and Continual Improvement activities
- Monitor New Product Pilot, Pre-Production, and Production Runs (NPD PPR’s) at Contract Manufacturing facilities to ensure the Reliability of product prior to production
- Report to and liaison with White-Rodgers’ product teams regarding acceptability and sustainability of NPD PPR’s
- Thorough working knowledge of White-Rodgers’ products, performance specifications and applications
- Summarize and evaluate test results to determine conformance to requirements
- Alert manager and consult with product engineers with questionable product performance
- Participates in problem solving efforts with all functions in an effort to isolate root causes
- Communicates inter-and intra-departmental with Quality, Engineering, and Procurement to support process and product improvement initiatives
- Participate in Corrective Action Team(s) and assist in special projects
- Write procedures, test reports, and maintain technical documentation
- Knowledgeable use of JDE, ETQ, WRAPS, EPRF’s, ANSI Standards, and Team Center
- Proficient use of MS 365 Word, Excel, Power Point, Outlook and Access
- Good working knowledge of computers, data acquisition, and computer aided testing
- Organizational skills which include meeting schedules and deadlines
- Self-improvement through education, training, and experience
- Assist manager(s) in execution of long and short-range quality, test plan and reliability processes to meet objectives
- Moderate to high travel is required
- A BS or BA in related technical or science field
- Knowledge of White-Rodgers’ products, their purpose and how they function in the field, both stand alone or as part of a larger system
- Knowledge of White-Rodgers’ standards, reliability statements, data acquisition requirements/processes, and inspection/measurement techniques
- Leads supplierquality portion of MRB / non-conformance product issues using established systems
- Executes Quality tools that apply to the product and suppliers assigned. Quality Engineering tools such as: contract review, sampling plans, auditing principals, SPC, MSA, First Articles, FMEA, PFMEA, calibration systems, etc to understand and ultimately resolve issues in the supply base
- Solid understanding and implementationof the relevant product or customer specifications, flow down documents, procedures, engineering or process drawings and regulating agent body requirements that apply to the products and suppliers assigned
- Issues, monitors and maintains corrective action database
- Works effectively with suppliers to resolve problems using Root Cause Corrective Actions (RCCA) tools
- Proactively analyze supplier performance data to determine continuous improvement opportunities to improve supplier performance
- Utilizes available data to establish schedules and perform required audits of assigned suppliers
- Maintains accurate and current supplier quality records, such as supplier audits, certifications, corrective action responses, and database screens
- Consult and advisewith the Sourcing team to select and manage assigned suppliers
- Travel to assigned suppliers, as necessary (domestic and international)
- Leads/performs supplier business assessment activity
- Performs Design of Experiments (DOE) as needed
- Participates in supplier part family transitions and new product development activities
- Executes and manages established Quality plan for assigned suppliers, based upon
- Mentors less experienced SQE's and Supplier Quality Techs, as required
- Participate and lead CI teams for internal process development
- Leads, directs and manages multiple projects effectively
- Demonstrated ability to present information effectively, formally and informally
- Strong interpersonal skills and ability effectively work at all levels Team player
- Self-starting, minimal supervision required
- Strong analytical and critical thinking skills
- Strong facilitation skills
- Solid understanding of AS9100, ISO-9000/2000, QS-9000 and/or TS-16949
- Demonstrated knowledge and experience with Continuous Improvement Methodologies (6 Sigma, Lean Mfg. etc.)
- Demonstrated experience conducting supplier quality audits with effective follow up
- Greenbelt required; black belt preferred
- Experience with supplier development processes
- 7+ years quality engineering experience
- Executes quality portion of MRB / non-conformance product issues using established systems
- Applies demonstrated understanding of the relevant product or customer specifications, flow down documents, procedures, engineering or process drawings and regulating agent body requirements that apply to the products and suppliers assigned
- Analyze supplier performance data to determine continuous improvement opportunities to improve supplier performance
- Participate with the Sourcing team to select and manage assigned suppliers
- Work and lead multiple projects effectively to closure
- Executes established Quality plan for assigned suppliers, based upon
- May mentor less experienced SQE's and Supplier Quality Techs, as required
- Strong interpersonal skills and ability effectively work at all levels
- Knowledge and experience with Continuous Improvement Methodologies (6 Sigma, Lean Mfg. etc.)
- Solid understanding and previous experience conducting supplier quality audits
- Greenbelt training, preferred
- 4+ years quality engineering experience
- Hold an engineering/technical degree
- Have previous experience in production processes
- Be familiar with lean production methods and problem solving processes
- Have good command of the English language
Supplier Quality Engineer, Suzhou, HPS, PMT Resume Examples & Samples
- At least 3-5 years work experience. As a key member of the Strategic Sourcing, identify, select, develop and manage global suppliers to produce printed wired assemblies, raw circuit cards, electronic components, box build, full functional testing, and other raw-materials and finished goods. Assess supplier process, quality and capacity capabilities. In conjunction with purchasing personnel conduct external supplier audits. Drive problem resolution for supplier quality issues, including on-site supplier development. As an expert on printed wired card, complete assemblies with enclosure, and electronic components, work with Quality Assurance, suppliers and Engineering to adjudicate quality issues, recommend corrective actions and follow up on supplier corrective action reports
- Responsible for achieving business objectives: defect reduction, cost reduction, lead-time reduction, on-time delivery, and new supplier launches. Lead and support several concurrent projects and develop strong relationship within cross-functional teams including Purchasing, Manufacturing and Engineering
- Must be willing to work in a result based, fast paced environment with minimal supervision. Will interface regularly with all levels of personnel within Honeywell and suppliers globally, hence exposure to other cultures will be a plus
- Must be Bilingual with fluent English and native local language
- Working knowledge of QS, TS, and APQP standards and processes preferred
- Professional certification (CQE and CQA preferred) or willingness to obtain
- Must have demonstrated understanding of PPAP processes and implementation
- Very familiar with IPC standard, especially 610 Class III and II
- Bachelor and above, engineering or science preferred
- Familiar with Java, SQL coding preferred
- Self -managed, professional and mature
- Good English communication ability
- Assess effectiveness of supplier 8D responses and assure timely closure of VIN concerns
- Drive supplier corrective actions (root cause analysis, 8Ds, containment actions)
- Work closely with Customer Quality and insure that major customer complaints are resolved
- Apply verbal and written communications skills in periodic and special reports/presentations both internally and with customers
- Analyze data to detect quality problems and recommend corrective action
- Support corporate initiatives of CS1, CS2, and QIP
- Knowledge of Active Electronics, Diodes, Transistors, Zeners, Integrated Circuits, Microprocessors, Memory devices, Custom ICs, etc. and their manufacturing processes
- Providing Engineering expertise to new program launches (Requirements vs. Capability assessments, supplier development)
- Support supplier specific quality activities
- Apply statistical techniques in analysis of supplier performance indicators to improve supplier quality
- Facilitate communication between Suppliers, Marshall Quality, Engineering, Supplier Development Engineers
- Assist in the qualification of new suppliers (site visits and audits)
- Follow-up on implementation of corrective actions to insure effectiveness
- Root cause / corrective action
- Risk assessment
- Participate in Product Review Board meetings
- Continuous improvement initiatives
- Participate in FMEA, DV, PV and safe launch teams
- Implement and maintain quality systems
- Review specifications for new products to determine performance requirements in order to meet and/or exceed customer expectations
- Supplier qualification (PPAP approval, Revalidation approval)
- Comply with and support the health, safety, and environmental programs, policies and procedures
- Identify and routinely uses the most effective, cost efficient and best practices to execute processes and continually evaluates their effectiveness and appropriateness
- Evaluate and verify supplier process controls and supplier quality systems, analyze product failures, facilitate writing and/or approve results of corrective actions of suppliers
- Exercise judgment in planning, organizing, performing, coordinating, directing and/or applying engineering and scientific principles to the evaluation and solution of technical issues at suppliers
- Review and update procedures and practices relating to part quality, design, fit and function to improve Flextronics product quality and reliability
- Supervise APQP activities in the region
- Perform and/or support audits of critical suppliers regularly in order to ensure their compliance with ISO 9001 and/or ISO/TS 16949 requirements and other relevant quality standards. Responsible to coordinate audit activities with support of regional functions, when necessary
- Organize and lead quality workshops for suppliers to resolve and prevent specific quality issues. In-depth understanding of the supplier manufacturing processes when issues occurred
- Participate and coordinate multi-disciplinary teams including the automotive sites, suppliers and customer in understanding the magnitude of the issue and define together with the team corrective actions that are needed
- Implement and manage all developed automotive supplier management procedures for the selected accounts
- Conduct quality system and quality engineering training at supplier manufacturing facilities as required to achieve compliance and improvement
- Must have a thorough knowledge Automotive QMS System and input all Quality Audit Reports and 8Ds into Global Audit
- Prepare and report global supplier quality performance during Management Reviews, as well as establishing baseline for supplier monitoring and performances
- Work with Regional Quality Engineering Managers and Regional/Site Quality Managers to help automotive manufacturing sites improve the quality of supplied parts
- Minimum 10 years progressive experience in Quality Engineering / Quality Assurance especially supplier quality preferred
- Basic knowledge of Gas turbine, steam turbine or generator products desirable
- Supplier quality or supplier development experience required
- Minimum 5 years experience facilitating or participating in root cause investigations using KT / Apollo / 5Y / Fishbone or similar methods. Trouble shooting and problem solving skills required. Analytical skills required
- Knowledge of machining/welding/NDE preferred
- Basic knowledge of Geometric Dimensioning & Tolerancing (GD&T)
- Basic knowledge of SAP preferred
- Internal Auditor Certification or capability to obtain within 1 year
- Lean/6-Sigma Certification preferred or capability to obtain within 1 year
- ASQ certification preferred
- Practical understanding of Management Systems
- Demonstrates a good grasp of knowledge and principles of field of specialization and applies through successful completion of assignments. Successfully applies knowledge of fundamental concepts, practices, and procedures of particular area of specialization
- Typically 2-5 years of successful experience in related field and successful demonstration of Key Responsibilities and Knowledge as presented above. Advanced degree MAY be substituted for experience, where applicable
- Good interpersonal skills, ability to work well in teams, ability to make the right judgments and decisions, Excellent critical thinking and problem-solving ability
- Good analytical skills, time management skills, be self-motivated and self-directing and ability to proceed with minimal direction and information, good data mining skills and good computer skills, ability to self-learn, good networking skills
- Excellent conflict resolution skills and demonstrated experience in working with multi-disciplinary and multi-level teams
- Dedicated, flexible and highly motivated individual with exceptional communication and relationship building skills
- Perform direct and indirect supplier evaluations, including supplier audits and review of quality data. Implement supplier risk analysis and mitigation plans when appropriate. Maintain and monitor the Approved Supplier List (ASL) in compliance with procedures
- Work with design engineering to determine receiving inspection requirements of purchased components and finished product. Provide technical quality engineering support to receiving inspection
- Assist in complaint/field return investigations related to purchased product
- Lead or assist in internal Corrective Action Preventive Action (CAPA) activities
- Employ statistical techniques and rationale in decision-making activities driven by quality data that is statistical in nature (nonconformance trending, CAPA effectiveness, part qualification, process monitoring)
- Develop supplier’s knowledge and implementation of quality tools and techniques
- Escalate quality issues to management as appropriate
- Provide quality training to functional owners and process owners as business needs dictate. May be responsible for directing the work efforts of QA/RA Inspectors, Technicians, or Specialists
- 3+ years of Quality/Regulatory experience required
- B.S. in Engineering or other 4 year Bachelor’s Degree required
- Experience in a medical device company / industry required
- Experience in New Product Development/Design Controls required
- Experience with 510(k) preparation and submission desired
- CQA, CQE or RAC desired
- Work directly with suppliers to dramatically improve overall part quality and drive improvements to their quality systems
- Interface with supplier’s Engineering and Quality organizations to efficiently address rported problems impacting functionality, quality, and regulatory requirements of the project
- Drive corrective & preventive actions to preclude recurrence of identified issues
- Develop control plans that define the supplier’s processes, identify areas of risk, and institute quality tools and programs that focus on identification and prevention of quality defects
- Drive continuous improvement in supplier performance through utilization tools such as DOE, Six Sigma, DMAIC, FMEA, SPC, 5-Why and 8D Root Cause Analysis, and Lean
- Participate and assist in supplier failure analysis activities, drive opportunities for improvement, motivate supplier’s management to achieve agreed quality metrics
- Develop and drive department projects such as reducing the need for incoming inspections, vendor to stock improvement, electronic certificates of compliance and parallel audit expansion
- Ensure supplier report card process is in place and routine Supplier Business Reviews are scheduled and conducted
- Provide quality training to functional owners and process owners as business needs dictate
- Generate appropriate performance metrics and prioritize and drive resolution of issues
- Assess and develops Hill-Rom’s current and future supply base Develops and communicates expectations for quality performance, continuous improvement, quality systems, process controls infrastructure for high leverage/critical sustaining parts and new products sourced to contract manufacturers
- Measures and communicates supplier performance on key metrics and the corresponding continuous improvement plans
- Participates as an active member in the New Product development process supplier evaluation team and the sourcing core extended team
- Willingness and flexibility for business travel both domestically and abroad, when required, which may be upwards of 30%
- Bachelor of Science in Engineering or related technical field (Preferably Mechanical or Electrical)
- Five (5) to Ten (10) years of Manufacturing, Quality Assurance, and/or Engineering experience,
- Demonstrated strong analytical, problem solving, teaming and communication/interpersonal
- Computer competency in Word, Excel, Power point and statistical databases
- Practical experience in metrology, test, inspection and analysis techniques
- Experience in the medical device industry or automotive industry in development, as well as
- Can operate independently to drive projects to completion and have a “Get it Right the First Time”
- Ability to multi-task and successfully manage conflicting priorities and projects
- Preference for at least 3 years of experience in Supplier Quality
- Experience of deployment of Quality System (FDA 21 CFR Part 820, ISO13485, ISO9001), and process controls and continuous improvement methods
- Excellent approach to quality of work output and quality documentation
Senior Pcba Supplier Quality Engineer Resume Examples & Samples
- Establish and maintain management level relationship with our CM
- Assess CM technical capabilities in areas of process control, quality systems, traceability and continuous improvement
- Support cost reduction opportunities through process improvements, material changes and other optimizations and validate quality is maintained
- Support regular business and lead quality reviews with CM, representing Seagate Senior Management in these reviews
- Champions’ organizational values and objectives
- Deep industry knowledge of printed circuit boards assemblies, components and manufacturing processes
- Understands the corporate business plan and his/her role in supporting it
- Excellent communication skills in both English and local dialect(s)
- Apply knowledge of regulations and laws appropriately
- Advocate point of view when appropriate
- Analytical skills necessary to assess information and apply judgment in decision making
- Formal meeting organization and facilitation skills
- Can provide customer level Failure Analysis Reports
- Bachelor Degree qualified in Electrical Engineering
- Experience within the IT industry including server, storage and HPC with focus on supply chain within these markets
- Knowledge of Mechanical and Electro-Mechanical manufacturing processes as well as quality and measurement systems
- 4-7 years experience
Senior Metal Supplier Quality Engineer Resume Examples & Samples
- Assist Supplier Engineering in the Production Part Approval Process to qualify production parts at CM
- Relationship development and management
- Deep industry knowledge of sheet metal manufacturing for system canisters and chassis (L5) and manufacturing processes
- Ability to perform gap analysis with internal customers and supply base Knowledge of formalized project management theories and methodologies
- Intermediate level skill working with MS Office Suite of products including Word, Excel, PowerPoint and Google Apps, Minitab
- Apply skills of persuasion and the ability to create consensus
- Works ethically and with integrity. Maintains credibility by meeting commitments. Actively pursues opportunities for learning and self development both individually and amongst peers
- Support RMA activity including reviewing material disposition
- Bachelor Degree qualified in Electrical Engineering with 4 - 7 years of relevant of experience
- Knowledge of mechanical and Electro-Mechanical manufacturing processes as well as quality and measurement systems
- Sigma training
Senior Plastic Supplier Quality Engineer Resume Examples & Samples
- Establish and maintain management level relationship with our supply chain partners
- Manage and develop supplier technical performance
- Assess supplier technical capabilities in areas of process control, quality systems, traceability and continuous improvement
- Accountability for parts quality including quality incident resolution and supply security
- Assist Supplier Engineering in the Production Part Approval Process to qualify production parts in the Supply Chain
- Support regular business and lead quality reviews with strategic suppliers, representing Seagate Senior Management in these reviews
- Build collaborative relationships on multiple organizational levels, with managers, partners and peers from diverse backgrounds across functional lines in all geographies
- Drives continuous improvement programs across all areas of responsibility
- Shares best practices with partners and peer groups
- Champions organizational values and objectives
- Deep industry knowledge of plastic model injection supply chain and manufacturing processes
- Ability to read and interrupt design drawings, schematics and circuit diagrams
- Knowledge of WW supply chains and manufacturing processes to support the business
- Embodies effective verbal, written and interpersonal communication skills
- Ability to perform gap analysis with internal customers and supply base
- Ability to work with minimal day to day task direction in a multi geographic organization
- Knowledge of formalized project management theories and methodologies
- Uses effective change management techniques
- Quickly learns and assimilates new business processes, ideas and concepts to formulate conclusions and deliver results. Adopting best practices and processes for continuous improvement
- Works ethically and with integrity. Maintains credibility by meeting commitments
- Actively pursues opportunities for learning and self development both individually and amongst peers
- Knowledge of 8D principles
- Bachelor Degree qualified in Mechanical Engineering with 4 - 7 years of relevant experience
- Experience within the IT industry including server, storage and HPC with focus on supply chain within these markets will be an advantage
- Knowledge of mechanical and plastic model injection manufacturing processes as well as quality and measurement systems
- 6 Sigma training
- Responsible for supplied component quality, including supplier management for quality problems, product launches, and process improvements
- Work with core teams to troubleshoot, understand, transmit and improve production concerns created by supplied components
- Lead trouble-shooting activities
- On-site audit of suppliers as needed
- Support customer return investigation and technical report writing
- Support/lead meetings, tracking open issues to ensure completion and provide weekly update reports
- Support defect investigation and defect reduction
- Bachelors or Masters Degree in Electrical Engineering
- Prior engineering/quality experience in automotive manufacturing a plus
- Possess strong drive to lead the quality team and ensure projects are completed on time
- Strong communication skills to effectively communicate with cross-functional teams
- Ability to travel globally as required to investigate defect root cause and countermeasure, support equipment/line validation, customer/supplier/group company support, etc
- Possess skills to perform mechanical and electrical root cause analysis and report writing
- Ability to read and understand technical schematics and mechanical blueprints
- Ability to understand and develop test specifications for hardware and software
- Ability to prepare and present data in a scientific reporting format
- Possess a general working knowledge of automotive or industrial manufacturing (TS16949, AIAG, APQP, PPAP, PFMEA, Control Plan, and ISO/TS, MSA, AIAG Standards)
- Experience with Surface Mount Technology, RMA & circuit analysis a plus
- Knowledge of electronic wafer production process, electronic component final packaging, automated electrical testing, and destructive testing for investigation also a plus
- Ability to travel up to 50% (domestic and international)
- Three to five years’ OEM or Tier 1 experience in automotive interior, exterior, body, chassis, electrical or powertrain quality, manufacturing or engineering functions, including demonstrated experience and capability in any of the following areas
- Manufacturing, Process and or Tool Engineering
- Statistical Problem Solving (Red X, DFSS)
- At least 1 year of experience in quality, engineering, or manufacturing
- Familiar with geometric design and tolerance and gage design and function
- Demonstrated knowledge of probability, statistical quality control and design of experiments, lean concepts, statistical problem solving, and six sigma
- Knowledge of manufacturing and assembly plant processes, quality systems, procedures, facilities and equipment
- Able to manage multiple projects and lead diverse cross functional teams
- Manufacturing and/or process experience with assembly processes
- Knowledge of GM’s Supplier Quality standards, policies and procedures
- 5 years or more experience in sheet metal production, processing, or technical support to stamping and roll forming end users
- Understanding of Advanced High Strength Steel (AHSS) mechanical and chemical properties and their effect on forming, springback and part dimensional quality
- Fundamental understanding of steelmaking and aluminum casting with subsequent rolling of the sheet metal
- Three to five years’ experience in automotive sheet metal quality, manufacturing, die, metal assembly manufacturing or product engineering
- Knowledge of automotive quality systems and corrective action process such as GM GP-5
- Proficiency in Microsoft Office Word, Excel, and Powerpoint
- Ability to travel as necessary throughout North America
- Ten years of experience in problem solving of sheet metal forming and processing issues
- Formability analysis of sheet metal stampings and assemblies
- Five years’ OEM or Tier 1 experience in automotive body sheet metal stamping and/or metal assembly quality, manufacturing, die, body assembly manufacturing or product engineering
- Demonstrated experience and capability in any of the following areas
- Proficient in print reading and interpretation, part measurement, gage design and function. Experience in electrical systems is a plus
- Ability to travel up to 50% (daily commutable and overnight combined – Mostly planned in advance travel).Preferred Qualifications
- Previous experience in electrical components / system development is a plus
- Electrical / Technical degree (Electrical Engineering degree preferred)
- At least 2 years of experience in quality, engineering, or manufacturing related to the field
- Knowledge of how to bring a non-automotive supplier into volume production capability
- Knowledge of the GM / supplier software development process for moving from concept through production
- Demonstrated ability to investigate quality problems and apply technical judgment to develop possible solutions
- Strategic Agility – Sees ahead clearly. Can anticipate future consequences and trends accurately. Has broad knowledge and perspective
- Action Oriented – Enjoys working hard. Is action oriented and full of energy for the things he/she sees as challenging. Not fearful of acting with a minimum of planning. Seizes more opportunities than others
- Dealing with Ambiguity – Can effectively cope with change; can shift gears comfortably; can decide and act without having the total picture; isn't upset when things are up in the air; doesn't have to finish things before moving on; can comfortably handle risk and uncertainty
- Interpersonal Savvy – Relates well to all kinds of people – up, down and sideways, inside and outside the organization. Builds appropriate rapport. Builds constructive and effective relationships. Uses diplomacy and tact. Can defuse even high-tension situations comfortably
- Organizational Agility – Knowledgeable about how organizations work. Knows how to get things done through formal channels and the informal network
- Learning on the Fly-Learns quickly when facing new problems; a relentless and versatile learner; open to change; analyzes both successes and failures for clues to improvement; experiments and will try anything to find solutions; enjoys the challenge of unfamiliar tasks; quickly grasps the essence and the underlying structure of anything
- Conduct on site supplier assessments to evaluate supplier capabilities and identify improvement opportunities, provide supplier quality recommendation on the potential suppliers for GM global aftermarket product procurement programs
- Lead PPAP definition, review and approve PPAP to ensure flawless launch of GM aftermarket products
- Provide immediate containment and proper controls at the supplier and conduct root cause analysis for product quality issues, drive continuous quality improvement at the supplier site
- Support to develop some potential aftermarket suppliers to help the Aftermarket Product Center (APC) of GM achieve the best enterprise cost for the key aftermarket product programs
- Serves as a global SQE role for all GM Customer Care and Aftersales (CCA) units when involved suppliers are located in China
- 1) Supplier quality systems knowledge (APQP, PSA, PPAP, etc.) and the ability to audit the supplier
- 2) Knowledge of automotive parts, systems and suppliers, preferably in electrical products
- 1) Proficient English communication skills, in both writing and speaking
- 2) Problem solving skills
- 1) Bachelor or Master Degree in Engineering
- 2) Minimum 3 years of work experience, mainly in supplier quality
- Solicit supplier inputs into product design, considering design for manufacturability, cost, reliability, parts availability, and more
- With procurement, conduct technical interchange meetings with suppliers prior to start of production to ensure requirements are understood and can be met without limitation
- Perform process reviews, first article reviews, and witness testing at supplier facilities ensuring procured product meets drawings, specifications, processes and statement of work requirements
- Assist receiving inspection in resolving inspection and documentation issues
- Work with procurement, program management, program quality, engineering, manufacturing, inspection, and government representatives to resolve issues with discrepant supplier material
- Investigate trends and issue timely corrective action requests to suppliers to resolve discrepant material issues and determine root cause
- Minimum GPA of 3.2 or higher
- Ability to take direction
- Excellent communications/interpersonal skills
- Evaluation and selection of world class suppliers in safety, quality, delivery and cost
- Perform Comprehensive Supplier Evaluation Report (CSER) audits, capacity analysis and determine supplier core competencies to ensure work is placed properly
- Perform Quality Management System, Process and Product audits on suppliers
- Develop Suppliers in the areas of TS16949 compliance, Six Sigma methods, Value Stream mapping, standard work, 5S, Kanban and other Fortive Business System tools for preventative action, corrective action, and continuous improvement
- Responsible to act as a liaison between cross functional teams, and to review and approve PPAP’s from suppliers for submission to the Manufacturing Teams and Customers
- Prepare and submit supplier report cards, action plans and the Approved Supplier List as required
- Conduct in-depth review and follow-up on the implementation of supplier action plans for poor report card performance
- Lead corrective actions as required from supplier 8D’s or non-conformance reports
- Lead the implementation of the Supplier Quality Manual to the supply base
- Work with Value Stream Team (VST) Quality Engineers to develop standards and methods for inspection, testing and evaluation at JVS suppliers
- Work with suppliers to devise sampling procedures and develops forms and instructions for recording, evaluating and reporting quality and reliability data
- Prepare Operations review Supplier and Internal Quality KPI’s, countermeasures and annual action plans for supplier quality PPM, on-time delivery, late supplier 8D responses, etc
- Good understanding and working experience with mathematical concepts such as probability and statistical inference, Statistical Process Control, Design of Experiments and Six Sigma problem solving methods
- Ability to read and interpret documents such as blue prints, safety rules and TS16949 procedure manuals and standards and the ability to write routine reports and correspondence
- Ability to think logical and critically to measure the pros and cons and take the most appropriate decisions in a prompt manner
- Ability to perform quality audits on suppliers to assure products and services meet International Organization for Standards (ISO) and regulatory standards
- Ability to develop good rapport with the purchasing department, manufacturing and production departments to prepare products according to JVS’ needs
- Must be an active listener with good time management skills in order to work with suppliers and project management teams to define deliverables
- Must possess great organizational and communication skills and the ability to work cooperatively with management
- Ability to work with minimum supervision to meet customer’s requirements
- Must have complete knowledge of APQP documents like PPAP, FMEA, Measurement Systems Analysis (MSA), Control Plans and Quality and Environmental standards such as TS16949 and ISO 14001
- Ability to conduct training using FBS training materials, and the ability to speak effectively before groups of suppliers, customers or employees of organization
- 30% travel required, some international
- Minimum of a Bachelor's degree (B.S.) in Mechanical Engineering or a related field or equivalent experience (Chemical, Electrical or Industrial Engineering)
- 3-5 years related experience and/or training, or equivalent combination of education and experience
- ASQ Certified Quality Engineer (CQE) and Certified Quality Auditor (CQA) preferred
- BS/BA in Engineering (Mechanical, Industrial, Quality or related field of study preferred)
- Minimum 3 years’ experience in a manufacturing environment
- Strong understanding of statistical process control techniques; process capability assessment (Cpk, Ppk)
- Experience with reviewing, approving and creating improvement plans for product submission packages (PPAP, ISIR, FAI etc.)
- Ability to drive to true root cause and identify appropriate short and long-term countermeasures
- Strong people and communication skills, analytical skills, and a commitment to continuous improvement efforts also essential, along with the ability to coach, and lead individuals and teams
- Flexibility to work overtime, different shifts, travel on short notice required
- Ability to work without close supervision
- Understanding of Lean Manufacturing concepts and methods
- ASQ Certified Quality Engineer (CQE) preferred
- Implement Quality Engineering, Purchasing Controls and Supplier Quality processes related to the development, procurement and continuous improvement of manufacturing materials, components, software, sub-assemblies, contract manufactured finished devices/products
- Ensure compliance to regulatory requirements and/or procedures for regulated products/processes
- Ensure raw material and component specs and drawings are translated to supplier quality requirements, qualify suppliers, assess metrics of whether supplier products meet quality specifications, and audit suppliers critical to quality processes
- Ensure that validations are completed where specified, and control plans exist to ensure the sustained quality and compliance of supplied raw materials and components
- Ensure correction and prevention activities of suppliers are timely and effective
- Evaluate supplier defects, determine appropriate disposition actions, and initiate communication to supplier and internal customers
- Recognize repetitive failures, trends and issues that may require additional root cause and corrective action and/or may need containment if the defect is not an isolated event
- Coordinate closely with the assigned “Field Supplier Quality Engineer” for problem resolution and when additional action may be required at the supplier’s facility
- Lead investigations for “Factory Escapes” (defects identified after Receiving Inspection) to determine appropriate prevention methods are implemented
- Initiate action with Manufacturing Engineering, Design Engineering, Test Engineering, and/or FRACAS when defects are identified as “Can Not Duplicate” by the supplier. Identify trends and take preventative actions
- Implement Quality Flowdowns to suppliers via SAP coding in the Material Master, Quality Info Record and/or other methods
- Help develop new processes that reduce cycle time of supplied material defects
- Support Receiving Inspection for immediate problem resolution, complex or ambiguous technical interpretation, and/or Workmanship standards
- Provide feedback to the originator when Quality Notifications are missing, inadequate or incomplete. Help facilitate training opportunities where applicable
- Work with Design Engineering and Component Engineering to update drawings when necessary
- May develop Source Inspection plans and/or provide feedback about Receiving Inspection plans when changes may be required
- Maintain compliance with the physical work environment and material handling to be compliance with FOD, ESD, safety, etc
- This position requires a Bachelors degree in an Engineering discipline
- Proficiency in MS Office software applications
- Ability to interpret a drawing, SOW and other technical documentation, as well as ability to develop an associated inspection plan/compliance matrix
- Ability to learn AS9100, ISO:9001 Quality Systems; Supplier quality requirement flow down, FAI and FMEA
- Supplier APQP
- Visit new/resourced suppliers to ensure APQP progress/process integrity
- Serve as a roadblock remover to ensure APQP target dates are successfully met
- Proactively work with suppliers to minimize and/or eliminate launch issues
- Report Supplier APQP progress/problems to BW launch team
- Assure APQP milestones are completed
- Supplier PPAP Submissions
- Review and make disposition on Supplier PPAP submissions
- Assure PPAP timing remains on time and meets launch timing objectives
- Update/communicate PPAP timing to launch team members
- Responsible for ensuring all PPAP requirements are met and documentation is up to date and on file for components within assigned commodities
- Supplier Quality Training
- Conduct Supplier Quality Training at suppliers facilities to meet BorgWarner’s and/or customer’s specific quality expectations/requirements
- Host Supplier Quality Training sessions at BorgWarner’s manufacturing facilities
- Conduct supplier audits of Implemented Corrective Actions Plans
- Complete Quality Systems Assessment at Supplier’s facility
- Supplier Significant Characteristics Activity
- Coordinate identification via cross-functional Team approach and ensure supplier conformance to requirements
- Responsible for ensuring quarterly data is received from suppliers and entered into the database
- More than 3 years of Quality Engineering experience in the automotive industry
- Effective at defining problems, collecting data, establishing facts and drawing valid conclusions. Ability to interpret a variety of technical instructions in mathematical or diagram form and deal with abstract and/or concrete variables. Proficient at developing trip reports, general business correspondence, and procedure manuals. Effective presentation skills and ability to respond to questions from management and/or customers
- First point of contact to the supplier quality organization when a supplier non-conformance is written
- Support investigation and verification that defects are supplier responsibility
- Coordinate Hutchinson onsite defect containment actions, including hosting of suppliers performing the work at the plant
- Coordinate, through the Supplier Quality Engineer, containment actions at the supplier. Provide clean point information to the plant
- Host visiting suppliers for quality discussions
Related Job Titles
3 Supplier Quality Engineer Resume Examples and Templates for Your Successful 2024’s Job Search
Our Resumes are featured in

- • Developed and implemented supplier scorecards to measure and track performance metrics.
- • Identified areas of improvement in supplier manufacturing processes and facilitated process changes.
- • Collaborated with suppliers to resolve non-conformances in a timely manner to meet customer requirements.
- • Conducted process audits to identify opportunities for improvement and implemented corrective actions.
- • Collaborated with cross-functional teams to develop and implement quality control processes and procedures.
- • Worked closely with suppliers to resolve quality issues and improve overall supplier performance.
Modern Supplier Quality Engineer Resume Example
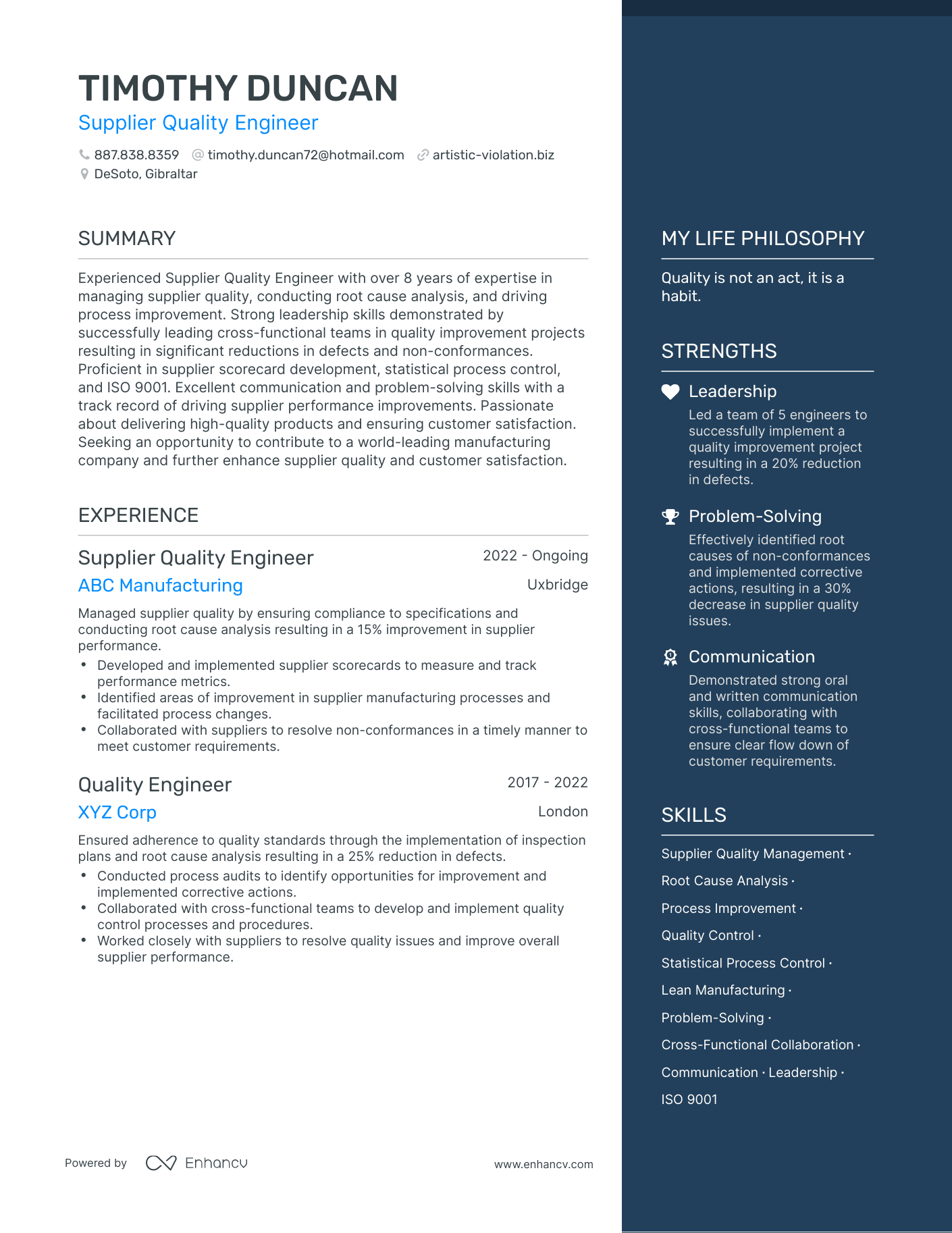
Creative Supplier Quality Engineer Resume Example
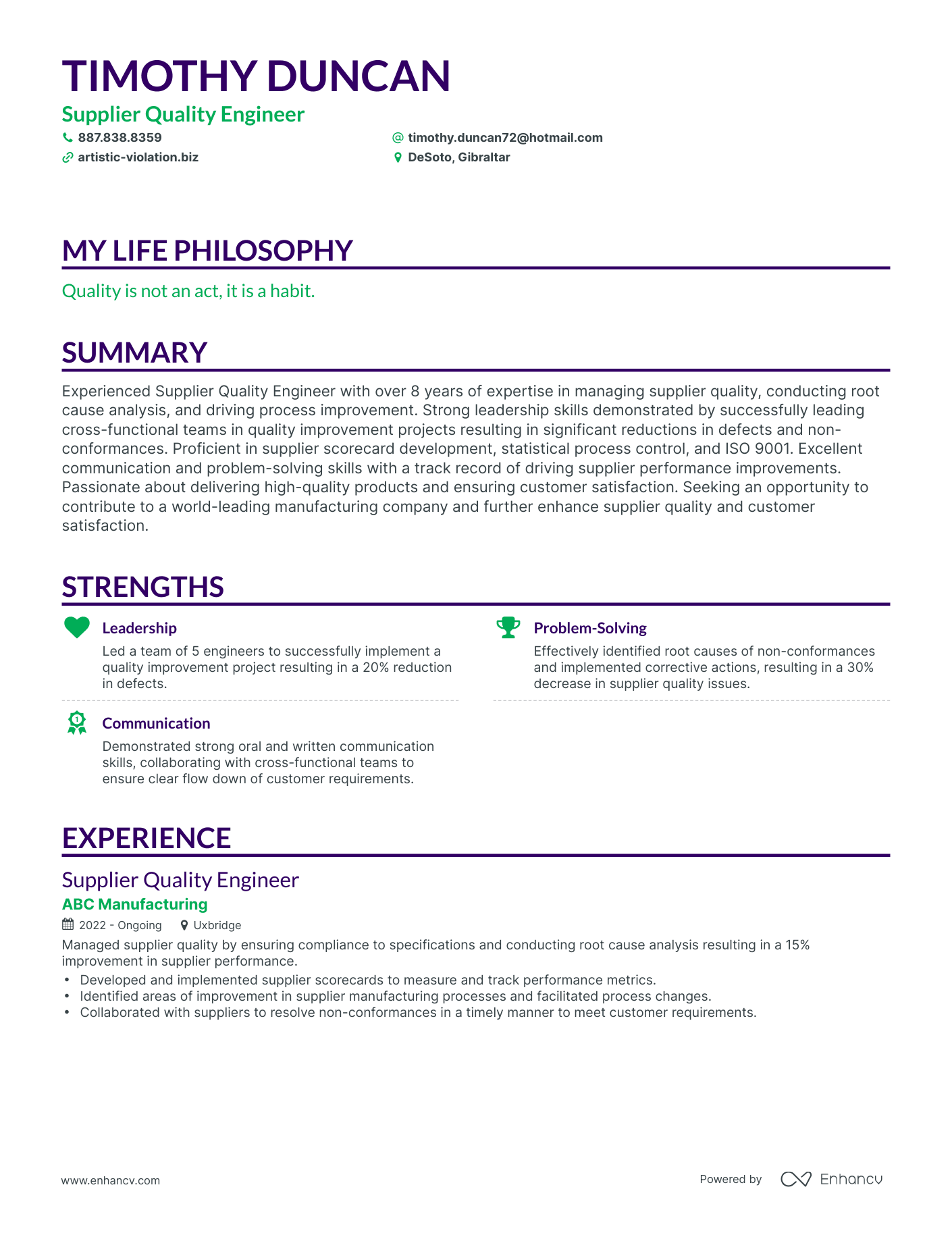
When it comes to creating a resume for a Supplier Quality Engineer job in 2024, there are a few important factors to keep in mind. The length, design, and format of your resume can all make a significant impact on how it is perceived by hiring managers. To ensure your resume stands out from the competition, follow these guidelines:
Resume Length:
While the length of your resume may vary depending on your experience and the job requirements, it's generally recommended to keep it between 1-2 pages. Be concise and focus on the most relevant information that highlights your qualifications for the position. Remember, hiring managers often have limited time, so make each word count.
Resume Design:
In 2024, the trend for resume design leans towards simplicity and elegance. Avoid flashy graphics or excessive colors that can distract from the content. Instead, opt for a clean and professional layout with clear headings and bullet points that are easy to read.
Resume Format:
The most common resume format is the reverse-chronological format, where you list your most recent experience first. This allows recruiters to quickly see your career progression. However, if you have extensive experience or are changing industries, a functional or combination format may be more suitable. Choose the format that highlights your strengths and aligns with the job requirements.
When writing a resume for a Supplier Quality Engineer position, there are several sections that you should include to showcase your abilities and qualifications. These sections are commonly expected by employers:
1. Contact Information:
- Phone number
- Email address (make sure it's professional)
- LinkedIn profile (optional but recommended)
2. Professional Summary:
This section provides a brief overview of your qualifications and highlights your key strengths as a Supplier Quality Engineer. Tailor your summary to match the job description and emphasize your relevant experience.
List your technical and soft skills that are relevant to the Supplier Quality Engineer role. Include skills such as quality management, risk assessment, statistical analysis, and problem-solving.
4. Work Experience:
Highlight your previous work experience in reverse-chronological order, focusing on your accomplishments, responsibilities, and impact. Use action verbs and quantify your achievements whenever possible to demonstrate your contributions.
5. Education:
Include your highest level of education, relevant certifications, and any additional training or coursework that showcases your expertise in Supplier Quality Engineering.
6. Projects or Achievements:
If applicable, include a section that highlights specific projects or achievements that demonstrate your ability to improve quality processes, reduce defects, or optimize supplier performance.
One highly effective way to structure the bullet points in your work experience section is by using the Context-Action-Result (CAR) framework. This framework provides a clear structure for explaining your experience in a concise and impactful manner. Here are a few examples:
- Context: Identified quality issues in the manufacturing process.
- Action: Collaborated with cross-functional teams to implement corrective actions and process improvements.
- Result: Reduced defects by 20% and improved overall product quality.
- Context: Led supplier audits to ensure compliance with quality standards.
- Action: Developed and implemented supplier scorecards to track performance metrics.
- Result: Improved supplier performance by 15% and reduced non-conformance issues.
As you craft your Supplier Quality Engineer resume, keep these key takeaways in mind:
- Keep your resume concise and focused on the most relevant information.
- Choose a clean and professional design that highlights your qualifications.
- Include sections such as contact information, professional summary, skills, work experience, education, and projects/achievements.
- Use the CAR framework to structure your bullet points and highlight your accomplishments.
With these guidelines and examples, you're well-equipped to create a compelling resume that showcases your expertise as a Supplier Quality Engineer. Good luck on your job search!
Top 7 Soft Skills for Supplier Quality Engineer Resume
- Analytical Thinking
- Attention to Detail
- Effective Communication
- Collaboration
- Time Management
Top 7 Hard Skills for Supplier Quality Engineer Resume
- Quality Engineering
- Statistical Process Control (SPC)
- Root Cause Analysis
- Failure Mode and Effects Analysis (FMEA)
- Corrective and Preventive Actions (CAPA)
- Supplier Auditing
- Process Improvement
Frequently Asked Questions
What is a supplier quality engineer (sqe).
A Supplier Quality Engineer (SQE) is a professional responsible for ensuring that suppliers meet quality standards in delivering materials, components, or services to a company. They assess supplier quality systems, conduct audits, and implement corrective actions.
What are the key skills required for a Supplier Quality Engineer?
Key skills for a Supplier Quality Engineer include knowledge of quality management systems, ability to perform supplier audits, expertise in statistical methods, strong problem-solving and analytical skills, excellent communication and negotiation abilities, and proficiency in project management.
What should I include in my Supplier Quality Engineer resume?
In your Supplier Quality Engineer resume, include information about your relevant work experience, highlighting achievements in supplier audits, process improvements, quality standards compliance, and cost reductions. Also, mention any certifications or training programs attended.
How do I format my Supplier Quality Engineer resume?
Format your Supplier Quality Engineer resume in a professional manner, with a clear and concise structure. Use a professional font, bullet points, and proper headings. Start with a summary or objective statement, followed by sections on work experience, education, skills, and certifications.
What are some common challenges faced by Supplier Quality Engineers?
Some common challenges faced by Supplier Quality Engineers include supplier non-compliance with quality standards, lack of clear communication with suppliers, managing supplier performance and improvement, resolving issues related to defective materials or components, and ensuring timely delivery.
Should I include any references in my Supplier Quality Engineer resume?
It is generally not necessary to include references in your resume unless explicitly requested by the employer. Instead, you can mention 'References available upon request.' This allows you to provide references when asked during the later stages of the hiring process.
For more inspiration, why not check out our free resource of job-focused resume examples?
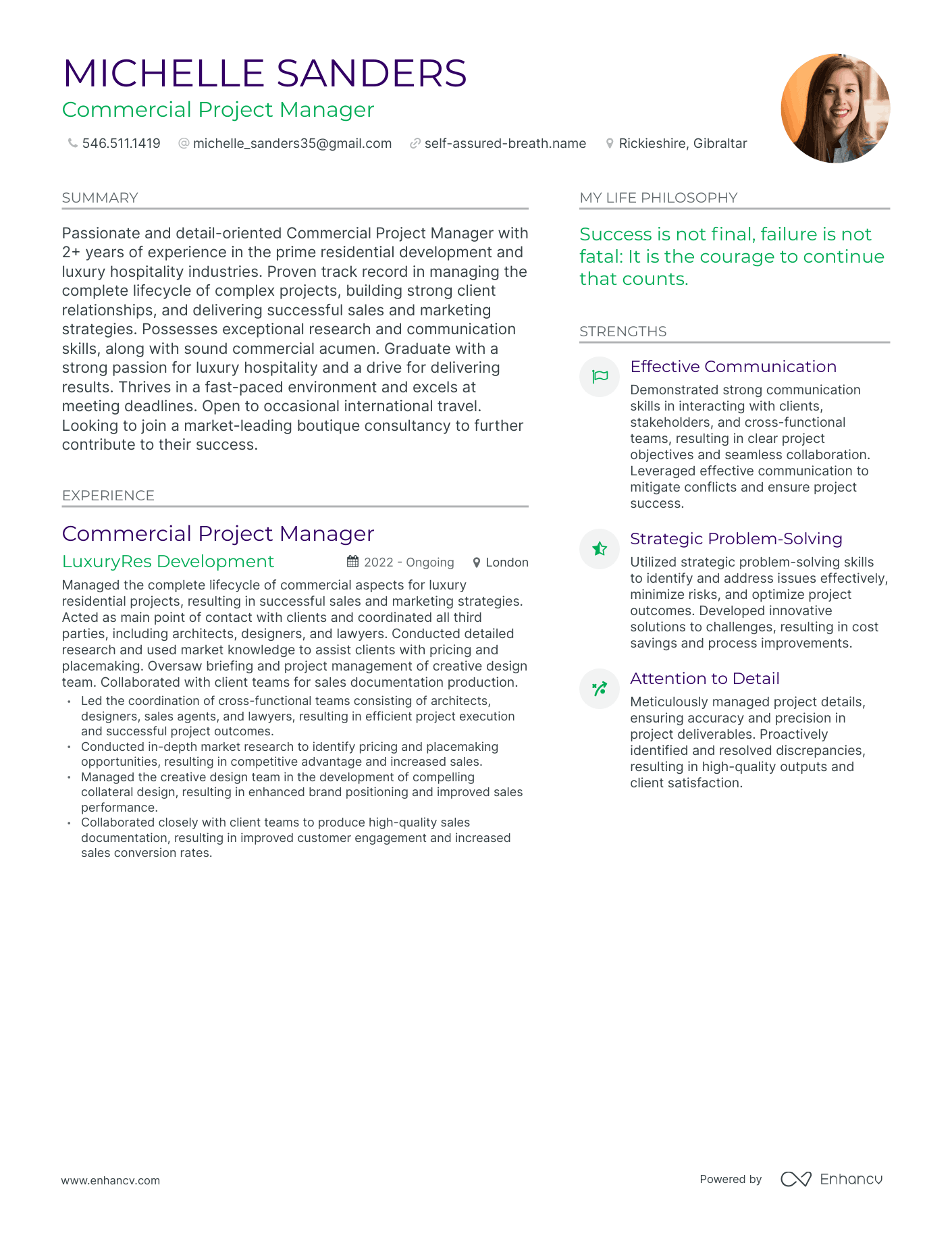
Commercial Project Manager
When it comes to applying for a commercial project manager position in 2024, it's crucial to have a well-crafted resume that highlights your skills and experiences. In this guide, we'll cover everything you need to know about formatting your resume, the essential sections to include, and the best way to showcase your experience using the Context-Action-Result framework. Formatting your resume correctly can make a significant difference in catching the attention of hiring managers. Here are a few things to keep in mind: Length: Aim to keep your resume to one or two pages. Cut out any unnecessary information to keep it concise and easy to read. Design: While it's essential to have an eye-catching design, ensure that it remains professional and easy to navigate. Use a clean and modern font, appropriate colors, and consistent formatting throughout. Format: Consider using a chronological format, highlighting your most recent and relevant experiences first. This format allows hiring managers to see your career progression at a glance. When crafting your commercial project manager resume, consider including the following sections: Contact Information: Provide your name, phone number, email address, and LinkedIn profile. Professional Summary: Write a concise overview of your experience, skills, and what you can bring to the role. Skills: Include a list of skills relevant to the commercial project manager position, such as project management, budgeting, and stakeholder communication. Experience: Detail your previous job roles, responsibilities, and accomplishments using the Context-Action-Result (CAR) framework. Education: List your educational qualifications, including degrees, certifications, and relevant courses. Optional Sections: Depending on your background and experiences, you may also include sections such as certifications, professional affiliations, or language proficiency. To effectively showcase your experience as a commercial project manager, use the CAR framework to structure your bullet points: Context: Start by providing the background and context of the project or situation you were involved in. Action: Describe the specific actions you took to address the situation or complete the project. Result: Highlight the outcomes or achievements resulting from your actions, quantifying them whenever possible. Here are a few examples of bullet points utilizing the CAR framework: Context: Led a cross-functional team of 15 members to deliver a high-stakes commercial construction project within a tight deadline. Action: Developed and implemented a comprehensive project plan, assigning tasks, monitoring progress, and ensuring adherence to budget and quality standards. Result: Successfully completed the project three weeks ahead of schedule, resulting in cost savings of $500,000 and receiving accolades from key stakeholders. Remember to tailor your bullet points to align with the specific requirements and responsibilities outlined in the job description. Creating an impressive commercial project manager resume requires careful attention to detail. Remember these key takeaways: Format your resume appropriately, keeping it concise, professional, and easy to navigate. Include essential sections such as contact information, professional summary, skills, experience, and education. Showcase your experience using the Context-Action-Result framework, highlighting your achievements and outcomes. By following these guidelines and crafting a targeted resume, you'll increase your chances of standing out as a strong candidate for a commercial project manager role in 2024.
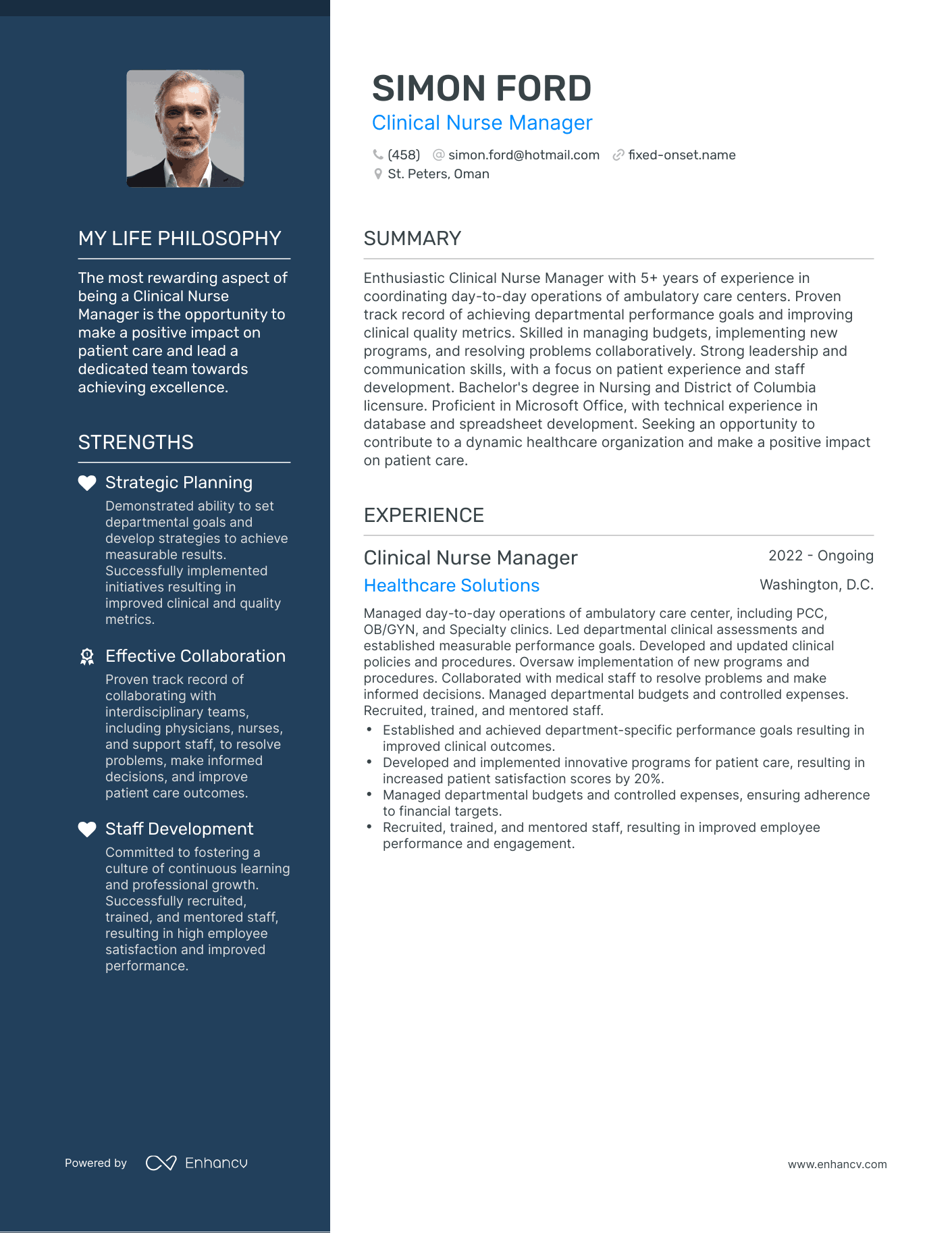
Clinical Nurse Manager
When creating a resume for a clinical nurse manager position in 2024, there are a few key formatting considerations to be aware of. First and foremost, keep the length of your resume to a maximum of two pages. With the increasing competition in the job market, recruiters prefer concise and targeted resumes that quickly highlight relevant skills and experiences. In terms of design, opt for a clean and modern look. Stick to a professional font, such as Arial or Calibri, and use a font size of 11 or 12 for easy readability. Utilize bold and italic formatting judiciously to draw attention to important points, but don't overdo it. Keep the overall layout simple and organized, using headings and subheadings to clearly delineate different sections of your resume. When crafting your clinical nurse manager resume, there are several sections that you should include to catch the recruiter's attention. Start with a compelling summary statement at the top, briefly highlighting your most relevant skills and experiences. This section serves as a snapshot of your capabilities and immediately grabs the reader's attention. Next, include a section for your professional experience. Use the Context-Action-Result (CAR) framework to succinctly describe your accomplishments and the impact you made in previous roles. For example, instead of simply stating "Managed a team of nurses," you could write "Implemented a streamlined scheduling system that increased efficiency by 20% and reduced overtime costs by 15%." Other important sections to consider include your education, certifications, and relevant skills. If you have specialized training or certifications related to clinical nursing management, be sure to highlight them in a separate section. Additionally, include a section for any additional relevant information, such as professional affiliations or volunteer experience. The CAR framework is an effective way to demonstrate your impact and results in previous clinical nurse manager roles. Here are a few examples of bullet points using this framework: Context: Managed a team of 20 nurses in a busy hospital setting. Action: Implemented a performance improvement plan to address staffing shortages and improve patient care. Result: Reduced nurse turnover by 30% and improved patient satisfaction scores by 15% within six months. Context: Led a cross-functional team in the implementation of a new electronic health record system. Action: Developed and delivered training programs to ensure smooth transition and adoption of the new system. Result: Decreased documentation errors by 20% and improved overall efficiency by reducing paper-based processes. Context: Implemented evidence-based practice protocols to improve patient outcomes in a critical care unit. Action: Collaborated with physicians and nurses to develop and implement standard protocols for common diagnoses. Result: Reduced mortality rates by 10% and decreased complications by 20% within the first year of implementation. Keep your resume to a maximum of two pages, using a clean and modern design. Include sections such as a compelling summary statement, professional experience using the CAR framework, education, certifications, and relevant skills. Highlight your impact and results using the CAR framework, focusing on specific accomplishments and outcomes. By following these tips and examples, you can create a standout clinical nurse manager resume that showcases your skills and experiences effectively. Remember to tailor your resume to each specific job application, emphasizing the qualifications that align with the position requirements. Good luck with your job search!
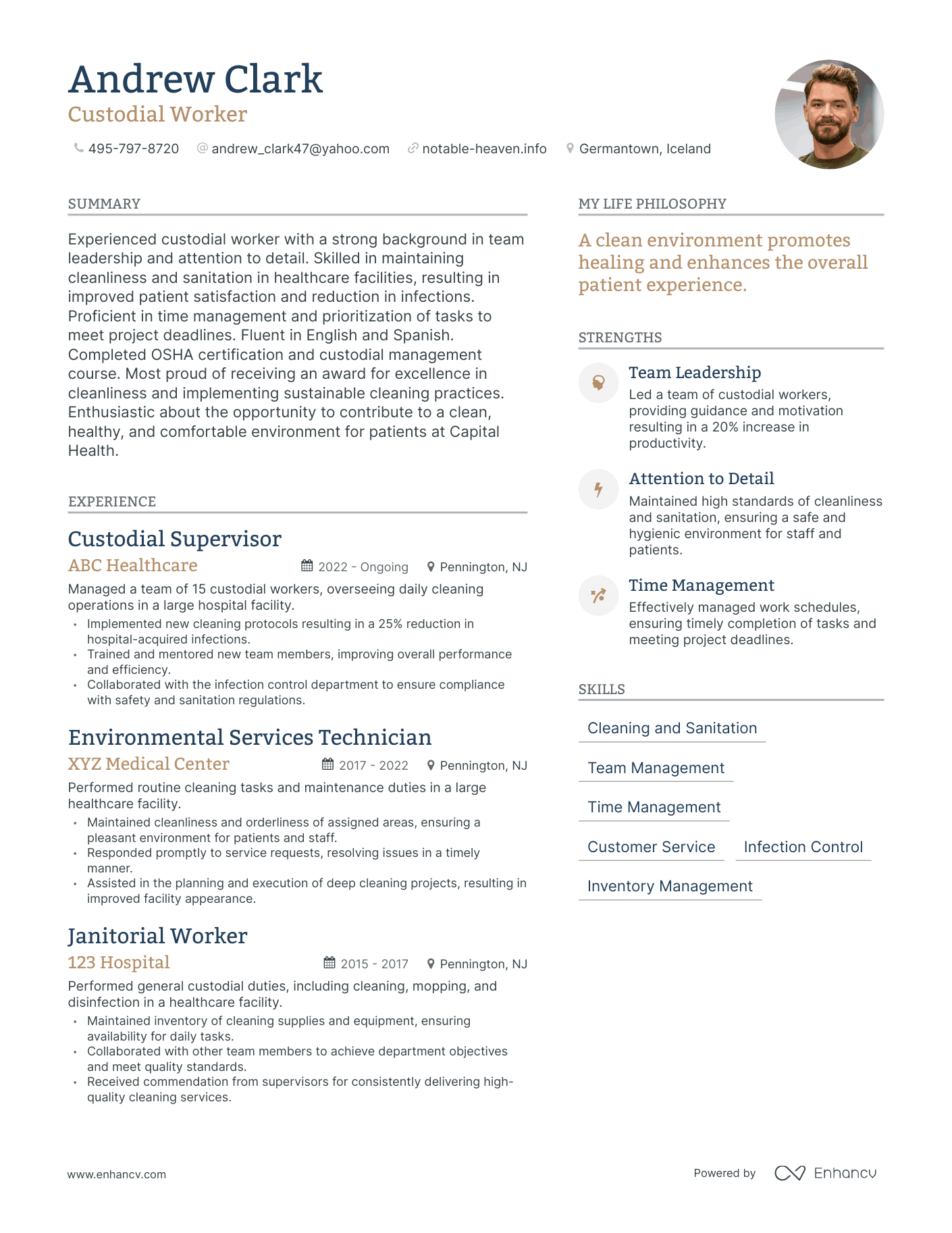
Custodial Worker
When it comes to creating a resume for a custodial worker in 2024, there are a few important things to keep in mind. The length of your resume should typically be one to two pages, depending on the amount of relevant experience you have. As for the design and format, it's best to keep it simple and professional. Here are some key formatting tips: Use a clean and easy-to-read font, such as Arial or Calibri. Set your font size between 10 and 12 points to ensure readability. Organize your resume into clear sections with headings and subheadings. Use bullet points to highlight your skills and accomplishments. Remember, the goal of your resume is to quickly and effectively communicate your qualifications to potential employers. By following these formatting guidelines, you'll make it easy for hiring managers to scan your resume and find the information they're looking for. When crafting your custodial worker resume, there are several sections that are essential to include: Summary or Objective Statement: This brief section should provide an overview of your skills and goals as a custodial worker. Work Experience: Highlight your relevant experience in custodial work, including job titles, dates of employment, and key responsibilities. Education and Certifications: Include any relevant education or certifications you have obtained, such as a high school diploma or OSHA certification. Skills: List any specific skills that are relevant to the custodial worker role, such as knowledge of cleaning chemicals, equipment operation, or safety protocols. Achievements: If you have any notable achievements in your previous roles, such as exceeding cleanliness standards or implementing cost-saving initiatives, be sure to highlight them. References: While not always necessary, it's a good idea to have a list of references available upon request. Optional sections that can still make an impact on your resume include: Professional Development: If you have attended any relevant training or workshops, you may want to include this section to demonstrate your commitment to continuous learning. Volunteer Experience: If you have volunteered in a custodial or cleaning capacity, this can be a valuable addition to showcase your dedication and experience. Additional Skills: If you have any transferable skills, such as excellent time management or attention to detail, add them here. When describing your experience as a custodial worker, using the Context-Action-Result (CAR) framework can help you effectively showcase your skills and accomplishments. This framework allows you to clearly communicate the situation or challenge you faced, the action you took, and the positive result or impact. Here are some example bullet points using the CAR framework: Context: Managed cleaning and maintenance for a large office building. Action: Developed and implemented a comprehensive cleaning schedule to ensure all areas were properly maintained. Result: Improved overall cleanliness and received positive feedback from building occupants. Context: Assisted with post-construction cleaning of a new commercial facility. Action: Coordinated with a team of custodial workers to efficiently clean and prepare the facility for occupancy. Result: Completed the project ahead of schedule, allowing the facility to open on time. Context: Managed custodial staff for a school district. Action: Implemented training programs and regular performance evaluations to ensure a high level of cleanliness and professionalism. Result: Achieved consistently positive reviews and maintained a clean and safe environment for students and staff. By following the CAR framework, you can provide concrete examples of your skills and accomplishments as a custodial worker, making your resume more compelling to potential employers. When formatting your custodial worker resume, keep it simple, clean, and easy to read. Include essential sections such as Summary/Objective, Work Experience, Education/Certifications, Skills, Achievements, and References. Consider adding optional sections such as Professional Development, Volunteer Experience, and Additional Skills to enhance your resume. Use the CAR framework to effectively describe your experience, focusing on the Context, Action, and Result of each situation. Remember to tailor your resume to each job application, highlighting the most relevant skills and experiences. By following these guidelines and customizing your resume for each application, you'll increase your chances of landing your dream custodial worker job in 2024.
3+ Supplier Quality Engineer Resume Examples and Templates
This page provides you with Supplier Quality Engineer resume samples to use to create your own resume with our easy-to-use resume builder . Below you'll find our how-to section that will guide you through each section of a Supplier Quality Engineer resume.
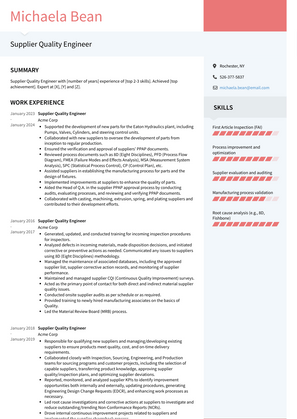
What do Hiring Managers look for in a Supplier Quality Engineer Resume
- Quality Assurance Knowledge : Proficiency in quality assurance principles, standards, and practices in manufacturing and supply chain management.
- Supplier Management Skills : Ability to assess, select, and manage suppliers, ensuring they meet quality requirements.
- Problem-Solving Abilities : Aptitude for identifying and addressing quality issues in supplier products and processes.
- Data Analysis : Skill in analyzing quality data, conducting root cause analysis, and implementing corrective and preventive actions.
- Communication Skills : Effective communication for collaborating with suppliers, cross-functional teams, and stakeholders to improve quality processes.
How to Write a Supplier Quality Engineer Resume?
To write a professional Supplier Quality Engineer resume, follow these steps:
- Select the right Supplier Quality Engineer resume template.
- Write a professional summary at the top explaining your Supplier Quality Engineer’s experience and achievements.
- Follow the STAR method while writing your Supplier Quality Engineer resume’s work experience. Show what you were responsible for and what you achieved as a Supplier Quality Engineer.
- List your top Supplier Quality Engineer skills in a separate skills section.
How to Write Your Supplier Quality Engineer Resume Header?
Write the perfect Supplier Quality Engineer resume header by:
- Adding your full name at the top of the header.
- Add a photo to your resume if you are applying for jobs outside of the US. For applying to jobs within the US, avoid adding photo to your resume header.
- Add your current Supplier Quality Engineering position to the header to show relevance.
- Add your current city, your phone number and a professional email address.
- Finally, add a link to your portfolio to the Supplier Quality Engineer resume header. If there’s no portfolio link to add, consider adding a link to your LinkedIn profile instead.
- Bad Supplier Quality Engineer Resume Example - Header Section
Joey 9 W. Wakehurst St. Mount Vernon, NY 10550 Marital Status: Married, email: [email protected]
- Good Supplier Quality Engineer Resume Example - Header Section
Joey Campos, Mount Vernon, NY, Phone number: +1-555-555-5555, Link: linkedin/in/johndoe
Make sure to add a professional looking email address while writing your resume header. Let’s assume your name is John Doe - here is a formula you can use to create email addresses:
- [email protected] - [email protected]
- [email protected] - [email protected]
- [email protected] - [email protected]
- [email protected] - [email protected]
- [email protected] - [email protected]
- [email protected] - [email protected]
For a Supplier Quality Engineer email, we recommend you either go with a custom domain name ( [email protected] ) or select a very reputed email provider (Gmail or Outlook).
How to Write a Professional Supplier Quality Engineer Resume Summary?
Use this template to write the best Supplier Quality Engineer resume summary: Supplier Quality Engineer with [number of years] experience of [top 2-3 skills]. Achieved [top achievement]. Expert at [X], [Y] and [Z].
How to Write a Supplier Quality Engineer Resume Experience Section?
Here’s how you can write a job winning Supplier Quality Engineer resume experience section:
- Write your Supplier Quality Engineer work experience in a reverse chronological order.
- Use bullets instead of paragraphs to explain your Supplier Quality Engineer work experience.
- While describing your work experience focus on highlighting what you did and the impact you made (you can use numbers to describe your success as a Supplier Quality Engineer).
- Use action verbs in your bullet points.
Supplier Quality Engineer Resume Example
Supplier Quality Engineer
- Conducted material inspection, including dimensional and metallurgical assessments.
- Generated layout inspection reports, including ISIR.
- Supported suppliers in reducing PPM (Parts Per Million) by emphasizing effective PFMEA (Process Failure Modes and Effects Analysis).
- Assisted the Head of Q.A in the supplier PPAP (Production Part Approval Process) approval by auditing and evaluating processes and verifying PPAP documents such as PFC (Part Submission Warrant), PFMEA, and control plans.
- Approved sampling plans and quality plans.
- Managed daily supplier rejection issues.
- Possessed working knowledge of Trimos, Profile Projector, Hardness Tester, and Spring Tester.
- Conducted customer return product analysis, facilitated PPAP approval, and conducted supplier audits and visits.
- Supported the development of new parts for the Eaton Hydraulics plant, including Pumps, Valves, Cylinders, and steering control units.
- Collaborated with new suppliers to oversee the development of parts from inception to regular production.
- Ensured the verification and approval of suppliers' PPAP documents.
- Reviewed process documents such as 8D (Eight Disciplines), PFD (Process Flow Diagram), FMEA (Failure Modes and Effects Analysis), MSA (Measurement System Analysis), SPC (Statistical Process Control), CP (Control Plan), etc.
- Assisted suppliers in establishing the manufacturing process for parts and the design of fixtures.
- Implemented improvements at suppliers to enhance the quality of parts.
- Aided the Head of Q.A. in the supplier PPAP approval process by conducting audits, evaluating processes, and reviewing and verifying PPAP documents.
- Collaborated with casting, machining, extrusion, spring, and plating suppliers and contributed to their development efforts.
- Oversaw supplier quality performance, focusing on resolving quality issues, verifying corrective actions, and ensuring timely supplier feedback and chargeback management.
- Strived to enhance overall supplier quality performance, particularly in terms of yield improvement and on-time solutions.
- Conducted audits of the production process, equipment, and manufacturing workflow at supplier facilities.
- Managed and reviewed Quality Plans, process flows, Work Instructions (WIs), FMEA (Failure Modes and Effects Analysis), and qualifications.
- Managed PPAP (Production Part Approval Process).
- Conducted process audits.
- Evaluated new suppliers.
- Managed non-compliance issues.
Supplier quality engineer Resume Example
Supplier quality engineer
- Conducted quality assessments of suppliers across different development stages: Selection audit, QPA, and leading activity.
- Spearheaded problem-solving and root cause analysis efforts with suppliers and customers to prevent the recurrence of non-conformances, ensuring the implementation of effective solutions.
- Expedited the resolution of technical issues with suppliers to ensure the uninterrupted supply of materials.
- Monitored, maintained, and updated the critical supplier audit system and schedule.
- Provided training to suppliers regarding standards and quality requirements.
- Collaborated with IQC (Incoming Quality Control) in evaluating and qualifying new supplier materials through a defined new product development process.
- Generated daily, weekly, and monthly reports, including tracking top suppliers and top issues.
- Conducted Supplier Quality System and Process audits and spearheaded Supplier Improvement and Development Programs.
- Identified underperforming suppliers, established performance improvement objectives, and managed progress plans in collaboration with commodity and program buyers to ensure the achievement of improvement goals.
- Acted as a liaison between Purchasing, Engineering, Manufacturing, and Suppliers to resolve supplier issues and offer technical support.
- Assessed cost reduction opportunities in partnership with Sourcing and Engineering.
- Analyzed data and generated reports on Supplier Performance to ensure suppliers maintained expected quality levels.
- Reviewed and implemented Supplier Change requests, Concessions, Deviations, and Engineering Change requests.
- Served as Subject Matter Expert (SME) for External Audits and as a lead auditor for Internal Audits.
- Led the identification and qualification of new suppliers in collaboration with Sourcing.
- Maintained the Approved Supplier List (ASL) database and regularly re-evaluated suppliers to ensure compliance with Regulatory, ISO standards, and global Medical device standards.
- Requested and evaluated Supplier Corrective and Preventive Actions, along with performing additional tasks as required.
- Responsible for qualifying new suppliers and managing/developing existing suppliers to ensure products meet quality, cost, and on-time delivery requirements.
- Collaborated closely with Inspection, Sourcing, Engineering, and Production teams for sourcing programs and customer projects, including the selection of capable suppliers, transferring product knowledge, approving supplier quality/inspection plans, and optimizing supplier deviations.
- Reported, monitored, and analyzed supplier KPIs to identify improvement opportunities both internally and externally, updating procedures, generating Engineering Design Change Requests (EDCR), and enhancing work processes as necessary.
- Led root cause investigations and corrective actions at suppliers to investigate and reduce outstanding/trending Non-Conformance Reports (NCRs).
- Drove internal continuous improvement projects related to suppliers and implemented the supplier chargeback process.
- Led critical process technical audit checklist projects (NDE, welding, coating, heat treating) and supported advanced shipping process projects, among others.
- Conducted detailed analysis of returned customer parts and leveraged findings to drive improvements through Corrective and Preventive Actions (CAPA).
- Actively participated in customer quality audits and promptly responded to audit findings.
- Generated trend analysis reports of non-conformances from both internal and external sources, communicating these reports to upper management.
- Prepared PPAP documents, including Control Plans, Flow Charts, Process Drawings, Part Submission Warrants (PSW), and Process Failure Modes and Effects Analysis (PFMEA).
- Assisted the Quality Manager in preparing, maintaining, and reviewing quality procedures to ensure compliance with customer and government requirements.
- Took part in ISO/TS audits and gained knowledge of the standards.
- Developed and implemented Layered Process Audits (LPA) within the organization.
- Served as a Supplier Quality Engineer, responsible for all Supplier Quality functions.
- Generated, updated, and conducted training for incoming inspection procedures for inspectors.
- Analyzed defects in incoming materials, made disposition decisions, and initiated corrective or preventive actions as needed. Communicated any issues to suppliers using 8D (Eight Disciplines) methodology.
- Managed the maintenance of associated databases, including the approved supplier list, supplier corrective action records, and monitoring of supplier performance.
- Maintained and managed supplier CQI (Continuous Quality Improvement) surveys.
- Acted as the primary point of contact for both direct and indirect material supplier quality issues.
- Conducted onsite supplier audits as per schedule or as required.
- Provided training to newly hired manufacturing associates on the basics of Quality.
- Led the Material Review Board (MRB) process.
Top Supplier Quality Engineer Resume Skills for 2023
- Supplier quality management
- Supplier evaluation and auditing
- Supplier performance metrics
- Supplier development and improvement
- Quality control and assurance
- Quality management systems (e.g., ISO 9001)
- Manufacturing process auditing
- Quality inspection and testing
- Root cause analysis (e.g., 8D, Fishbone)
- Corrective and preventive actions (CAPA)
- Statistical process control (SPC)
- Failure modes and effects analysis (FMEA)
- Lean manufacturing principles
- Six Sigma methodologies
- Process improvement and optimization
- Supply chain quality management
- First Article Inspection (FAI)
- Incoming inspection procedures
- Material inspection and testing
- Supplier qualification and onboarding
- Quality standards and specifications
- Quality data analysis and reporting
- Non-conformance management
- Risk assessment and mitigation
- Manufacturing process validation
- Quality audit reports and documentation
- Supplier performance scorecards
- Advanced quality planning (APQP)
- Supplier corrective action requests (SCAR)
- Root cause analysis tools (e.g., Pareto analysis)
- Design of experiments (DOE)
- Quality management software proficiency
- Auditing tools and techniques
- Statistical analysis software (e.g., Minitab)
- Supplier relationship management
- Quality process documentation
- Quality assurance testing methods
- Quality system certification (e.g., AS9100, TS 16949)
- Process capability analysis
- Control plan development
- Data analysis and interpretation
- Problem-solving abilities
- Time management and organization
- Adaptability and flexibility
- Decision-making skills
- Attention to detail
- Collaboration with cross-functional teams
- Presentation and communication skills
- Supplier quality agreements
How Long Should my Supplier Quality Engineer Resume be?
Your Supplier Quality Engineer resume length should be less than one or two pages maximum. Unless you have more than 25 years of experience, any resume that’s more than two pages would appear to be too long and risk getting rejected.
On an average, for Supplier Quality Engineer, we see most resumes have a length of 2. And, that’s why we advise you to keep the resume length appropriate to not get rejected.
How can I highlight my experience as a Supplier Quality Engineer on my resume?
Focus on your expertise in assessing and improving supplier quality, conducting audits, and ensuring that products meet company standards. Highlight your role in supplier selection, quality assessments, and problem resolution in collaboration with suppliers.
What are the key skills to feature on a Supplier Quality Engineer's resume?
Emphasize skills in quality control, supplier management, auditing, and root cause analysis. Highlight your ability to develop supplier quality programs, implement corrective actions, and ensure compliance with industry standards and regulations.
How do I demonstrate my ability to manage supplier quality on my resume?
Provide examples of how you’ve evaluated suppliers, conducted quality audits, and worked with suppliers to resolve quality issues. Highlight your role in improving supplier performance, reducing defect rates, and ensuring on-time delivery of high-quality products.
Should I include metrics on my Supplier Quality Engineer resume? If so, what kind?
Yes, include metrics such as reductions in supplier defects, improvements in supplier quality ratings, or cost savings achieved through supplier quality improvements. These metrics help quantify your impact on supplier performance and overall product quality.
How can I showcase my experience with quality audits on my resume?
Detail your role in conducting supplier quality audits, including reviewing processes, identifying non-conformities, and ensuring corrective actions are implemented. Highlight your experience in conducting on-site inspections and ensuring suppliers meet industry-specific quality standards.
What kind of achievements should I highlight as a Supplier Quality Engineer?
Highlight achievements such as improving supplier performance, reducing defect rates, or successfully implementing quality control measures. Mention any recognition you’ve received for your contributions to supplier development or continuous improvement initiatives.
How do I address a lack of experience in a specific area of supplier quality on my resume?
Emphasize your general quality control and engineering skills, as well as your ability to learn quickly and adapt to supplier-specific challenges. Highlight relevant training, certifications, or projects that demonstrate your readiness to manage supplier quality.
How important is collaboration for a Supplier Quality Engineer role?
Collaboration is essential for working with suppliers, engineers, and cross-functional teams to resolve quality issues. Highlight your experience in working closely with suppliers to improve processes, implement corrective actions, and meet quality expectations.
How do I demonstrate my ability to resolve supplier quality issues on my resume?
Mention specific examples where you identified quality problems, performed root cause analysis, and implemented corrective actions with suppliers. Highlight your role in ensuring that these issues were resolved and prevented from recurring.
Should I include certifications on my Supplier Quality Engineer resume?
Yes, include relevant certifications such as Certified Quality Engineer (CQE), Six Sigma, or ISO 9001 Lead Auditor. These certifications demonstrate your expertise in supplier quality management and your commitment to maintaining high standards in quality engineering.
What are the key skills to feature on a Supplier Quality Engineer's resume?
Copyright © 2024 Workstory Inc.
Select Your Language:

IMAGES
VIDEO
COMMENTS
A strong Supplier Quality Engineer resume will demonstrate your ability to inspect and analyze supplier processes, develop supplier quality metrics, and maintain relationships with suppliers. When writing your Supplier Quality Engineer resume, there are several key takeaways that should be included.
Here's what we see in standout supplier quality engineer resumes. Show Impact With Numbers: The best resumes show clear impacts with specific metrics like cost reduction by 15%, process efficiency up 25%, supplier defect rates down 10%, and on-time delivery improved to 95%.. Include Relevant Skills: Include skills on your resume that you have and are in the job description.
10 Supplier Quality Engineer Resume Examples & Guide for 2025. Supplier quality engineers focus on ensuring that the materials and components supplied meet the required quality standards and specifications. When crafting your resume, highlight your experience in quality control processes, your ability to conduct supplier audits, and your ...
Supplier Quality Engineer Resume Sample. Supplier Quality Engineers work with logistics, supply chain management, and manufacturing. They ensure that all products meet company, industry, and government standards and lack any defects. To advance in this field, it's important to show your strong technical and analytical skills through previous ...
Supplier Quality Engineer Specialist Resume Examples & Samples Evaluate and authorize manufacturing processes and packaging related to the CKD logistic process, according to the corporate guidelines Apply methods like DOE, 6 Sigma, CEP, etc. to analyze the root causes of complaints.
Example You can use the following example resume when creating your own: Julia Espesito [email protected] 990-455-0000 Professional summary: Driven supplier quality engineer with over six years of experience initiating quality control processes in purchasing programs with analysis of supplier agreement contracts. Successfully achieved 14% improvement to efficiency within supply chain ...
Creative Supplier Quality Engineer Resume Example. Use this example. When it comes to creating a resume for a Supplier Quality Engineer job in 2024, there are a few important factors to keep in mind. The length, design, and format of your resume can all make a significant impact on how it is perceived by hiring managers. To ensure your resume ...
Good Supplier Quality Engineer Resume Example - Header Section. Joey Campos, Mount Vernon, NY, Phone number: +1-555-555-5555, Link: linkedin/in/johndoe. Make sure to add a professional looking email address while writing your resume header. Let's assume your name is John Doe - here is a formula you can use to create email addresses:
Explore this Supplier Quality Engineer resume example, constructed with Wozber free resume builder. Discover how to seamlessly integrate your quality mastery with job specifics, making sure your career narrative is as flawless as the products you oversee! ... For example, "Supplier Quality Engineer with over 4 years of hands-on experience ...
Industrious Supplier Quality Engineer with over 22 years of successful work history in the supplier quality industry. Expert experience in purchasing programs analysis Supplier Quality Agreements and supplier performance improvement. Specialize in hand-held electronic device industry Supplier Corrective Action Requests and NCR system management.